— 6 min read
Oil Rig Construction: Building & Engineering in Extreme Conditions
Last Updated Jul 29, 2024
Last Updated Jul 29, 2024
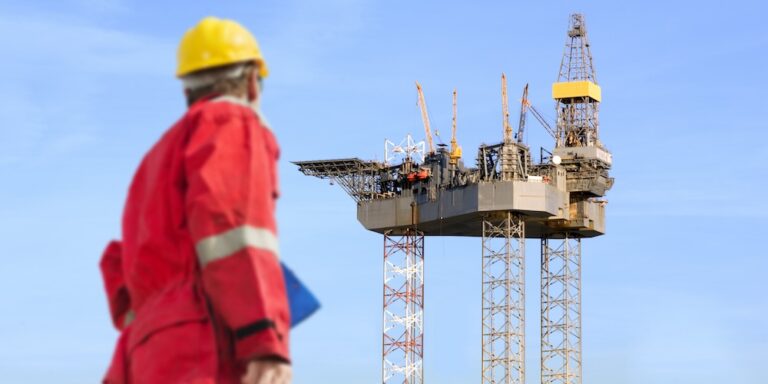
Every day, oil rigs around the world extract tens of millions of barrels of oil. Building oil rigs and platforms can be extremely dangerous and complex, and the finished product is often a feat of engineering excellence. In many ways, it’s construction at its most extreme.
Oil rigs and platforms are the structures used to extract oil from underground reserves. Their construction requires diligent planning, advanced engineering, creative innovation, extraordinarily precise execution and the ability to navigate harsh environments and conditions. Oil rigs are required to meet the current global demand for energy — and the environment, economies and geopolitics are all dependent on their effective and safe construction.
This article explores the basics, the process and the unique challenges of constructing oil rigs and platforms.
Table of contents
The Basics of Oil Rig Construction
Most oil rigs are one-of-a-kind, designed and built to withstand and maximize output in the specific conditions in which it’s located. Constructing oil rigs usually takes somewhere between 18 months to five years, depending on location, size and other factors, including geopolitics.
Onshore rigs extract oil from beneath the earth’s surface and account for a vast majority of the global oil output. Common onshore rigs and platforms include conventional rigs, used for drilling vertical wells, and horizontal rigs, made to drill horizontal wells or access unconventional resources like shale oil. Offshore rigs are less common and tend to be more complex, expensive and dangerous to build and operate.
The type of offshore rig is selected based on the water’s depth and conditions. For example, tension leg platforms (TLPs) are ideal for deep water up to 2,000 meters, while a fixed platform might be better in shallow water less than 500 meters. Other common offshore rigs include spar platforms, semi-submersible platforms, jack-up rigs and compliant tower platforms.
Most contracts to construct rigs and platforms are EPCs (Engineering, Procurement and Construction). EPC contractors are responsible for the entire project lifecycle, from engineering and design, to material procurement, construction, commissioning to project handover. All contractors who work in this field need to be extremely specialized, experienced and equipped to handle large-scale, high-stakes projects that involve many international stakeholders, including the private energy companies that own most of the world’s rigs.
The Phases of Oil Rig Construction
Constructing oil rigs usually includes a few important phases.
Planning
Planning begins with extensive feasibility studies, including geological surveys and environmental impact assessments. Offshore work must account for ocean currents and seabed conditions.
Just as the construction of oil rigs requires extreme precision, the design process is extremely detailed. Engineers often use advanced software and simulation models to ensure the rig’s functionality, safety and efficiency before work has ever begun. Most rigs are unique, and include custom components to withstand and maximize output in its specific location. Some components — such as piping, joints, hulls or topside modules — can be similar on different rigs and are more likely to be prefabricated.
Contractors working in oil rig construction often use advanced work packaging (AWP), a project management methodology used to improve productivity and predictability in large-scale projects. AWP breaks projects into smaller, manageable work packages that are planned and executed in a logical sequence.
The planning process itself can be broken into work packages, such as workface planning or engineering work, but having the rest of the project broken into packages, such as procurement or commissioning, can help with planning, scheduling and sequencing.
Fabrication
Fabrication involves the manufacturing of major components, such as the hull, topside modules and drilling machinery. Because most rigs are one-of-a-kind, components often need to be custom-made for each project. Many projects set up their own specialized yard in a convenient location to create components where they can then be transported to the jobsite.
Transportation
The components on oil rigs are usually massive, heavy and difficult to move. An important, and particularly challenging, part of planning and managing site logistics is ensuring components can be moved to the jobsite. For offshore rigs, heavy-lift vessels and specialized barges are often used to transport and install components.
Commissioning
Commissioning is the process of ensuring all systems and equipment are functional and meet safety standards. Extensive testing and certification are conducted when working with oil rigs, as the stakes of having something malfunction are extremely high, and can include loss of life or an environmental disaster.
Common Challenges in Oil Rig Construction
The goal when building oil rigs is almost always to minimize surprises and maximize predictability. That often comes with a few common challenges:
Safety
Oil rig construction can be extremely dangerous, and even more so when working offshore, where crew members have nowhere to evacuate in an emergency. Everyone working on the project usually undergoes extensive safety training, and contractors usually invest in high-quality fire and gas detection systems to help monitor and predict dangerous situations.
Safety also often includes plans for workers navigating the unfamiliar areas in which they’re living and working during the project. Some companies have workers and executives stay in secured premises, and risk management should account for everything from weather to more extreme dangers, such as kindnappings.
Authorities having jurisdiction (AHJ) around the world have wildly varying safety requirements and standards. Contractors often strive to maintain the rigor of their home country or set a standard within their company that meets or exceeds safety standards in most places they’ll be working.
The Extraordinary Costs of Delays
Project management and contingency planning needs to be extremely thorough and precise. A delay in finishing an oil rig can result in an extraordinary loss of money for the owner, often as high as hundreds of millions of dollars. Delays also create more opportunities for safety issues.
Geopolitical factors
Oil rig construction is uniquely subject to geopolitical factors, such as wars, protests, intra-country struggles, tariffs and sanctions. These things can impact accessing a jobsite, material procurement or transportation, timelines and safety. Large contractors often include teams that specialize in monitoring and managing political, economic and other factors that might impact the project.
Stay updated on what’s happening in construction.
Subscribe to Blueprint, Procore’s free construction newsletter, to get content from industry experts delivered straight to your inbox.
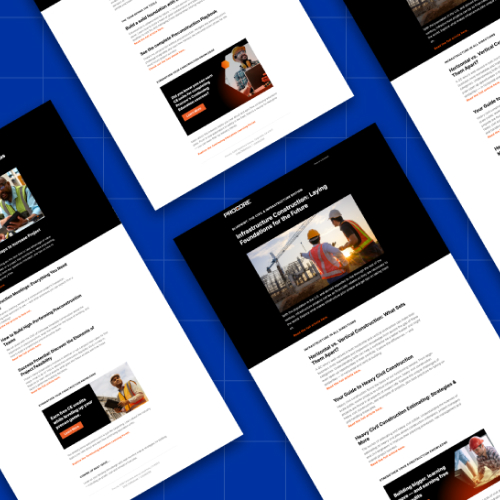
Oil Rigs: Innovation in Demanding Environments
Unlike some other areas of construction, oil rig construction has the means and the need to seek out, integrate and embrace new technologies. The sheer size of oil rig projects requires extensive communication, collaboration, and document management, which has made the use of project management software extremely important.
Even more dramatically, the industry embraced digital twins and IoT sensors long before many fields of construction, which has advanced contractors’ ability to monitor structures in real time and predict maintenance, reduce risk, and improve long-term outcomes. Oil rig construction is a powerful example of the ways innovation can both meet the needs of construction while also leading the way towards new horizons.
Was this article helpful?
Thank you for your submission.
100%
0%
You voted that this article was . Was this a mistake? If so, change your vote here.
Scroll less, learn more about construction.
Subscribe to The Blueprint, Procore’s construction newsletter, to get content from industry experts delivered straight to your inbox.
By clicking this button, you agree to our Privacy Notice and Terms of Service.
Categories:
Tags:
Written by
Sandra Benson
Sandra Benson is the Vice President of Industry Transformation at Procore Technologies. Sandra has an award-winning record of success in business process improvement utilizing technology for construction, engineering, real estate, and professional services firms. Sandra offers special expertise in creating operational strategies and business development, spearheading market expansion, and directing technology functions. Sandra brings over 30 years of experience in the Building and Building Technology industry holding a number of executive positions including Worldwide Head of Engineering, Construction and Real Estate at Amazon Web Services, CIO/VP at Kentz/SNC-Lavalin, Global Industry Director of E&C at J.D. Edwards/Oracle and at Hexagon PPM. She has worked with many global E&C, EPC, and real estate companies throughout her career. She is heavily involved in organizations that lead the way for technology advancement in the building industry and serves on the Board of Directors of the National Institute of Building Sciences as well as member of the Board of advisors for ViaTechnik. She is an advocate for women’s leadership. Sandra has been a featured speaker and author at many industry events. She was ConstrucTech Woman of the Year in 2014 and serves as a judge for this award.
View profileJames Hamilton
70 articles
James Hamilton is a writer based in Brooklyn, New York with experience in television, documentaries, journalism, comedy, and podcasts. His work has been featured on VICE TV and on The Moth. James was a writer and narrator for the show, VICE News Tonight, where he won an Emmy Award and was nominated for a Peabody Award.
View profileExplore more helpful resources
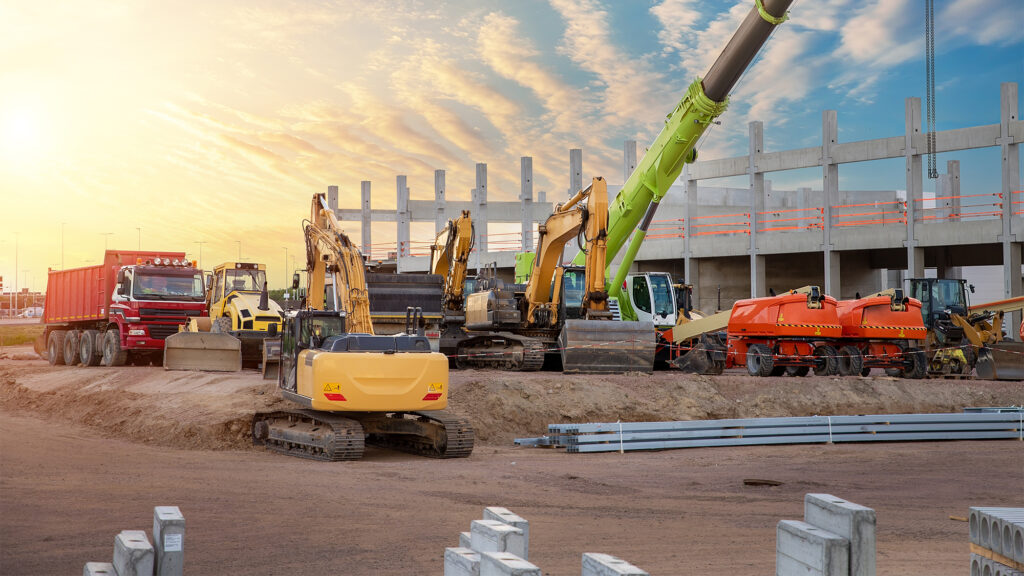
Improving Project Monitoring with Construction Quantity Tracking
Once a construction project is underway, builders need to closely monitor the project’s progress and make sure it’s staying on schedule and within budget. Quantity tracking helps construction leaders manage...
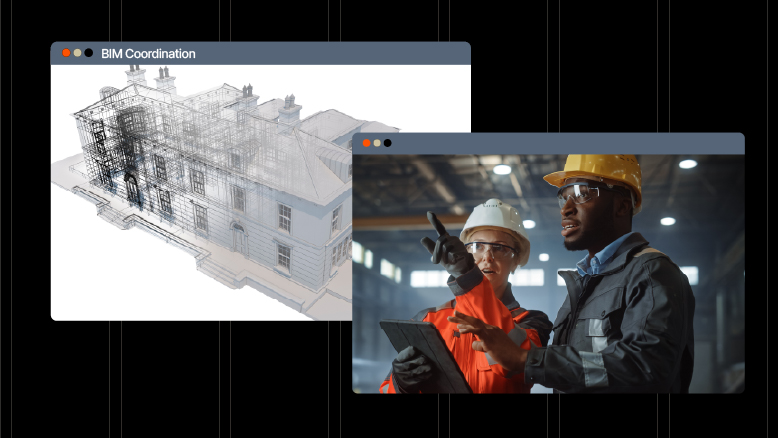
Streamlining Construction Projects with Effective BIM Coordination
The old saying goes: if you fail to plan, you plan to fail. Construction professionals know this better than nearly anyone. To take a project from a vision in an owner’s...
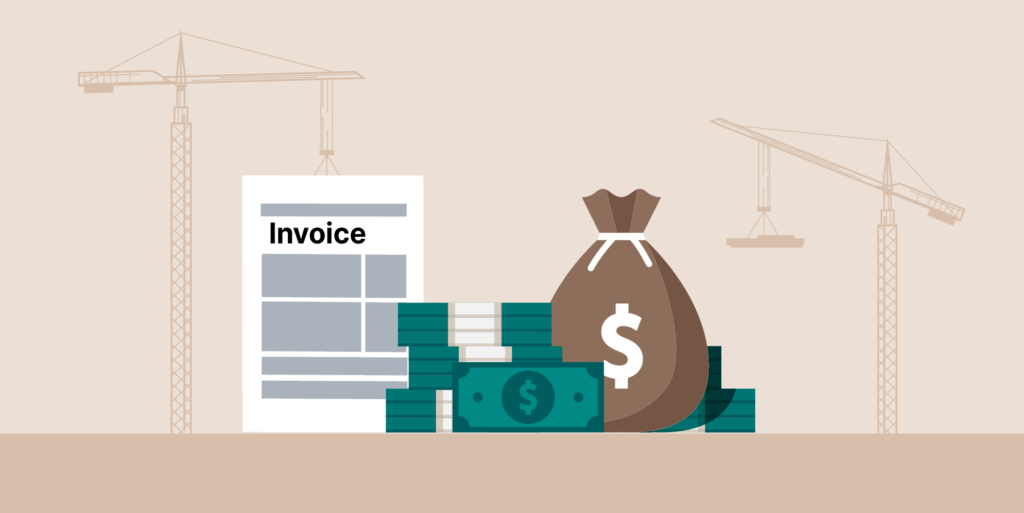
Construction Invoice Factoring: A Quick Guide
Construction companies need to maintain consistent cash flow. Projects can take years to complete, and delays and unforeseen events may keep expenses mounting. Adding to this load are typically high upfront...
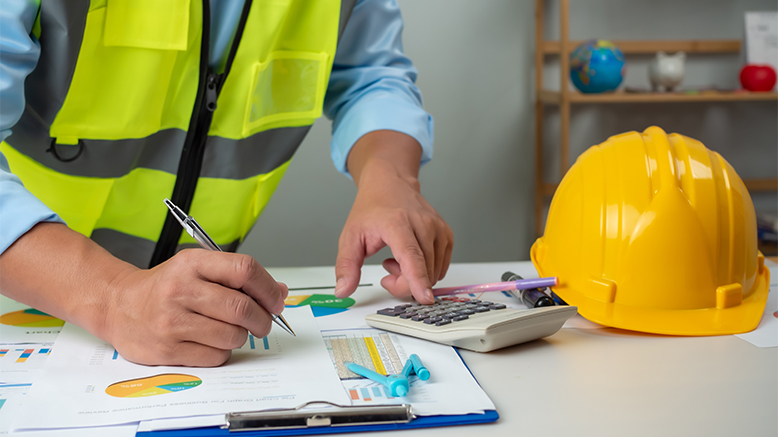
Understanding Subcontractor Bid Packages in Construction
Construction bid packages can have a cascading impact on the success of a construction project. The quality of a bid project may affect the quality of the bids, which in...