— 4 min read
Optimizing Material Logistics & Procurement: Insights from a Sports Facility Project
Last Updated Sep 18, 2024
Last Updated Sep 18, 2024
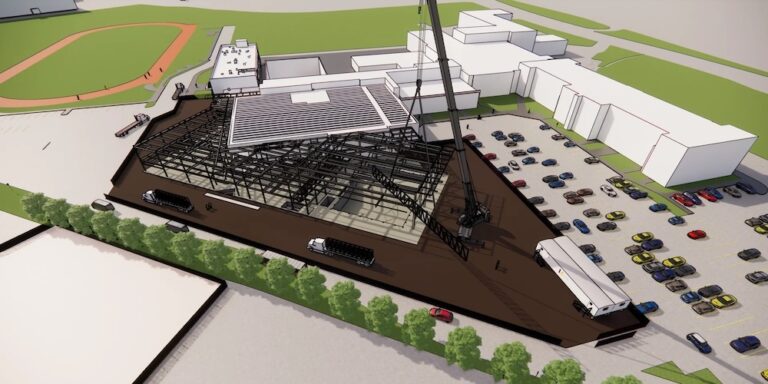
As an assistant project manager on the Cadigan Wellness Complex Project at Boston College High School, managing material procurement and logistics is one of my primary responsibilities.
In addition to the typical building materials you would expect on a steel-framed 42,000 square-foot facility — concrete, rebar, prefabricated structural steel, etc. — this project also includes an 8-lane, 25-meter Myrtha pool system which required shipment of panels from Italy.
Following lean construction methods requires tightly coordinated delivery of materials by project sequence to ensure that each trade partner has all of the required materials on-site when they are scheduled to begin. Working on an active school site creates an additional layer of complexity — it’s important that material delivery and storage doesn’t interfere with regular school traffic.
Here’s an overview of my workflow to procure and organize materials for the project.
Table of contents
Working Backwards to Prioritize Submittals
Early on in the project, my first step is creating and organizing submittals. I pull everything from the project specifications, generating all drafts submittals as “placeholders” for the materials we need on-site.
I always work backward from the schedule. I start with the required-on-jobsite date and calculate backward, considering the time necessary for submittal reviews, obtaining shop drawings and product data from trade partners, and the design team's review and approval process.
After that, I factor in material procurement lead time and fabrication times. Incorporating all these factors in Procore's submittal tool gives me a specific date to submit product data or shop drawings.
This information drives our schedule and procurement log. I use the procurement log as a communication tool by sharing it with the trade partners, whether it's for concrete rebar, steel shop drawings, or finishes. We coordinate these dates and ensure the materials arrive on-site when needed.
Sequencing Material Procurement
In construction, it's important to be as lean as possible. The Lean Construction project management method focuses on maximizing value by reducing waste. One way to eliminate waste is by minimizing on-site material storage; moving materials multiple times is inefficient. For instance, we don't want a yard full of materials that need to be moved around to make space for ongoing work.
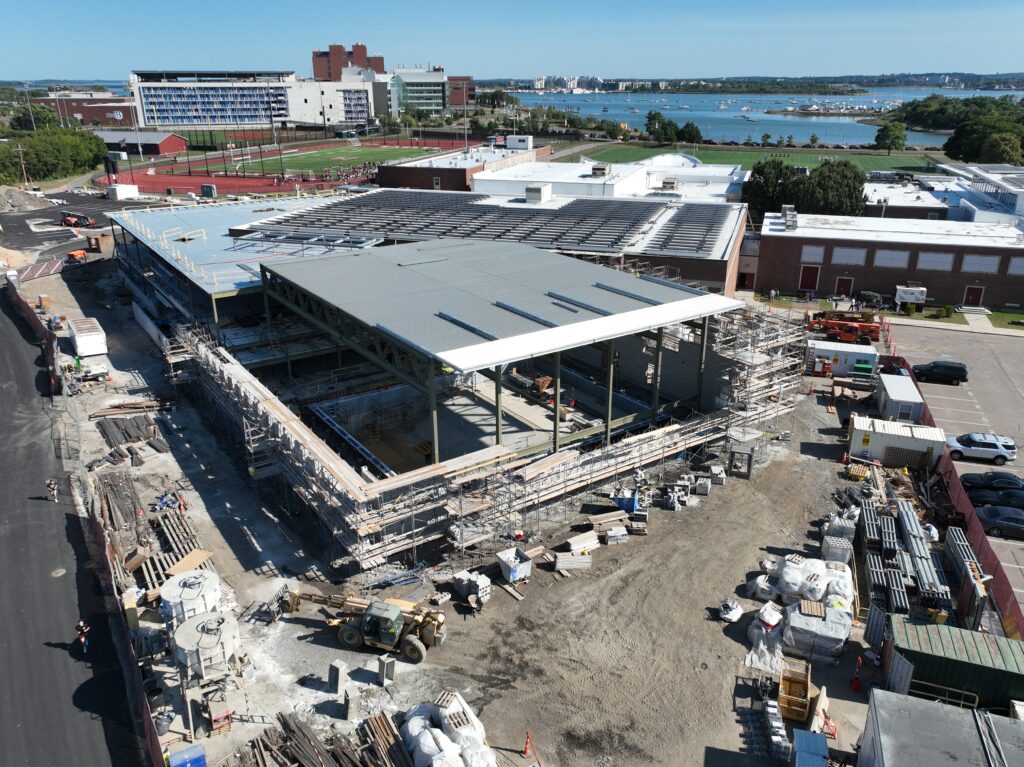
For our slab placements, rebar and steel beams are essential. The steel process, for example, is extensive. We broke our steel structure into 15 different sequences of shop drawings based on sections of the building. This started 8 months ago, and we are now seeing the material installed on-site.
Each steel sequence is shipped independently, ensuring precise coordination. The steel is fabricated in Canada, and the erector coordinates getting the material on-site on an as-needed basis. The erection process begins at the back of the building and moves forward, dictated by our logistics plan to address any safety concerns in advance. For example, we make sure other trades are clear of overhead work areas to ensure safety.
Managing Long Lead Times
One of the longest lead time items in this project was the Myrtha pool panels. Because the panels were prefabricated and shipped from Italy, advance planning and approvals were required. We tracked the shipping containers as they traveled via cargo ship through New York, providing regular updates to our client. Ensuring we complete any predecessor tasks before the panels arrive means we can install them immediately upon arrival.
Efficient Logistics & Site Management
Logistics planning includes organizing laydown yards for materials. For example, rebar for slab placements is stored close to the work area to minimize unnecessary movement. Weather-sensitive materials are stored appropriately to prevent damage.
Dealing with quality issues, especially with custom-fabricated items, involves conducting first-delivery inspections. We reference the approved submittals and shop drawings to confirm that the materials meet specifications. For steel, we look at applied coatings to ensure fireproofing compatibility requirements are met before installation.
Safety Coordination
For protection of high-value items like the Myrtha pool panels, fabricated in Italy, we plan for plywood coverings and build temporary structures like a dance floor scaffolding platform to serve as an elevated work platform for overhead work. This allows us to complete tasks above the pool without risk of damage.
Temporary structures such as fencing and access gates — to ensure public safety and site security — are carefully planned. They are installed and removed once the project is complete, restoring the site as needed. In addition, we are utilizing temporary barriers within the school’s gym as we demo openings to connect the new building into the existing gymnasium, allowing a majority of the space to be utilized by the school for assemblies and activities.
Coordinating with AHJs, like the local fire department, is another critical aspect. We provide them with a detailed NFPA 241 plan, ensuring they have all necessary access and information about on-site materials and hot works.
Explore data and trends for building materials prices.
Get the latest U.S. retail prices and view historical trends for common building materials.
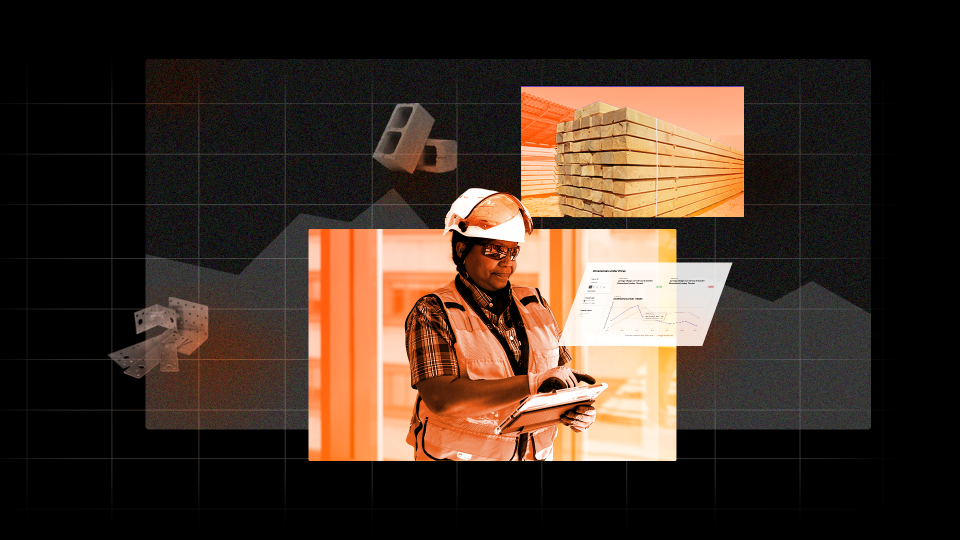
Keeping Information (and Materials) Flowing
Effective material procurement is a continuous process of coordination and planning. Keeping the flow of information constant between the office project management, field team, and trade partners ensures materials arrive on time, supporting the project's overall schedule. This approach avoids potential delays that could impact multiple trades, maintaining a lean, efficient and safe construction process.
Was this article helpful?
Thank you for your submission.
100%
0%
You voted that this article was . Was this a mistake? If so, change your vote here.
Scroll less, learn more about construction.
Subscribe to The Blueprint, Procore’s construction newsletter, to get content from industry experts delivered straight to your inbox.
By clicking this button, you agree to our Privacy Notice and Terms of Service.
Categories:
Tags:
Written by
Mark Venuto
Mark Venuto is a Senior Assistant Project Manager at Lee Kennedy, a Boston-based general contractor. Since 2018, he has demonstrated a strong aptitude for handling complex and high-impact projects in the construction management field, specializing in large-scale renovations, new construction, and mixed-use developments. At Lee Kennedy, Mark works primarily within the company’s large projects division, working across academic, commercial, and mixed-use sectors. His role involves overseeing project execution from inception through completion, ensuring adherence to quality standards, budget constraints, and project timelines. Mark holds a degree in Project Management from Wentworth Institute of Technology.
View profileExplore more helpful resources
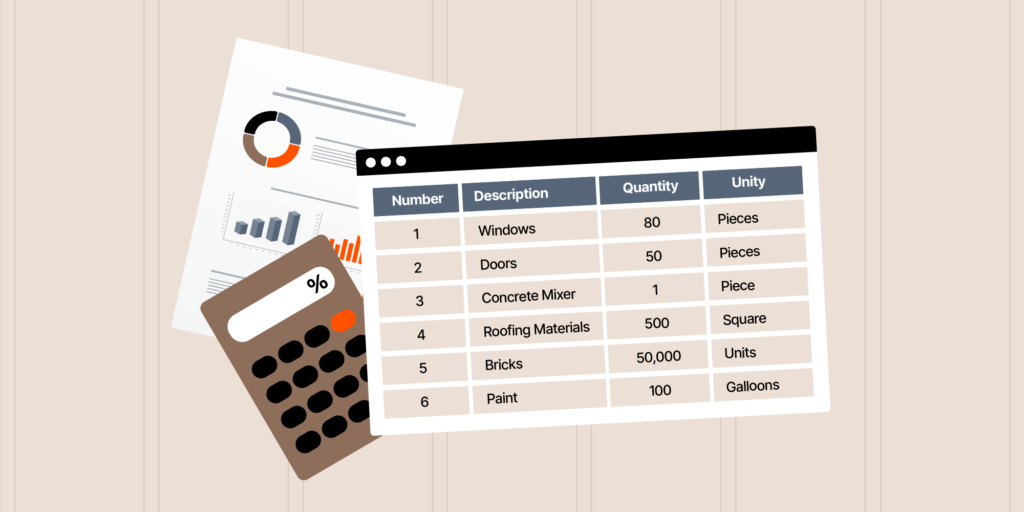
Key Benefits of a Construction Procurement Log (With Free Template)
By the time everything is purchased for a construction project, it represents not just a lot of money. It also represents a lot of energy from the teams involved. Getting...
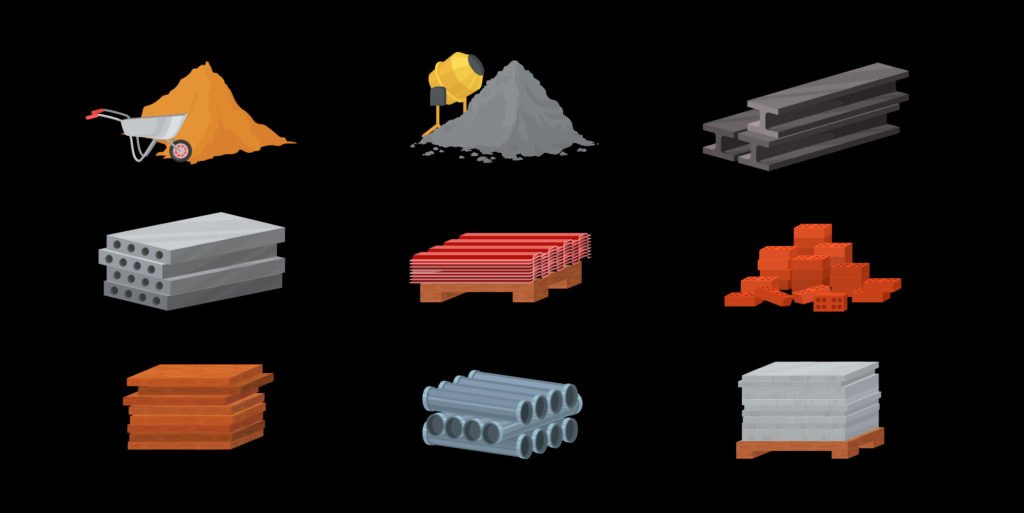
Material Management in Construction: A Project Manager’s Guide
Construction materials represent one of the key components for pulling off successful projects, and also one of the biggest expenses contractors face. Optimally managed materials procurement, storage and installation can...
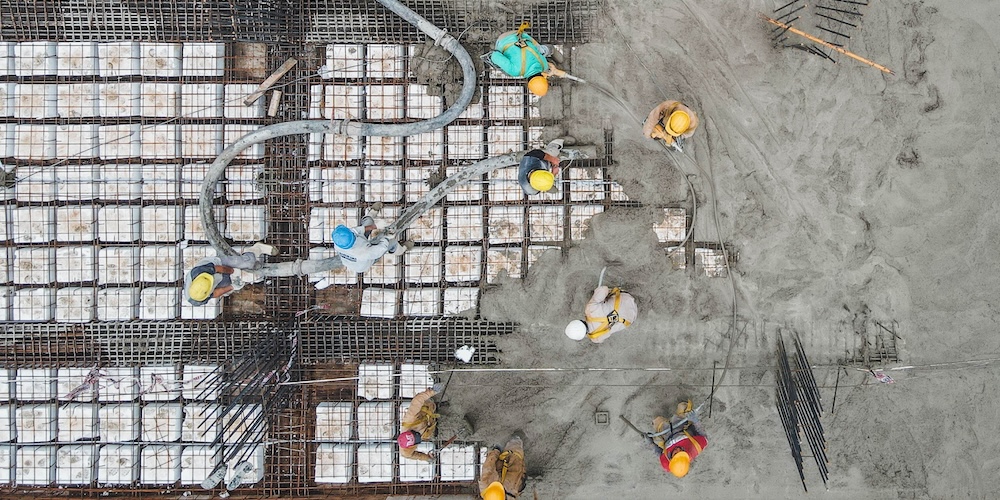
Mastering Construction Resource Management: Strategies for Success
Completing construction projects successfully requires the careful management of various resources: labor, materials, equipment, money, time and information. Since these resources are finite, allocating them wisely is crucial for minimizing...
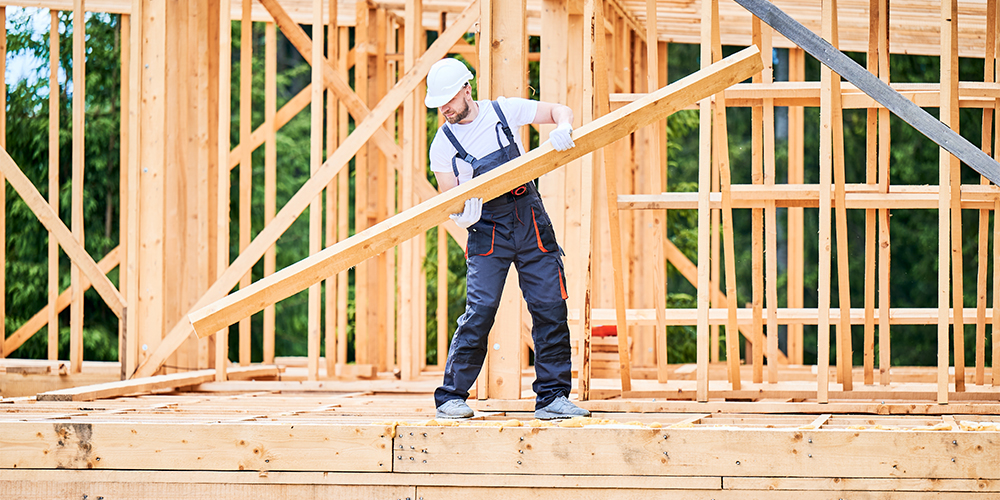
Wood Frame Construction: Techniques, Benefits & Challenges
Wood-framed structures can be found almost everywhere. If you are in North America, there’s a good chance you are in a wood-framed structure right now, as most single-family homes in...