— 10 min read
OSHA Standards for Construction vs. General Industry: Similarities & Differences
Last Updated Jun 14, 2024
Last Updated Jun 14, 2024
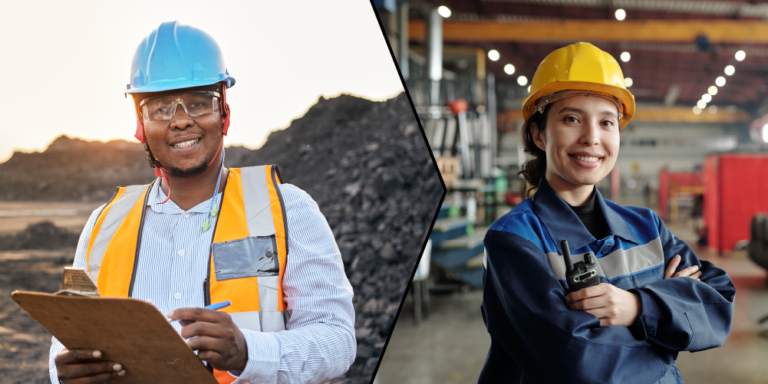
For more than 50 years, OSHA’s standards have outlined the necessary methods and precautions employers are obligated to take in order to safeguard their employees from potential hazards. Among its four distinct groups of standards, OSHA’s general industry and construction industry standards address various facets to keep employees safe in the workplace.
While general industry standards encompass a wide range of workplaces, construction standards specifically address these challenges and risks as they pertain to the construction industry. In this article, we’ll take a look at some shared standards across the two industries — and the clear distinctions that OSHA has set between them.
Table of contents
How OSHA standards were established
The Occupational Safety and Health Act (OSH Act) of 1970 was the first step in establishing a framework to ensure the safety and well-being of employees across industries. The OSH Act was enacted in response to the alarming rates of workplace injuries, illnesses, and fatalities that have historically impacted workers in the U.S. This act recognized the rights workers have to safe and healthful working conditions and sought to provide a comprehensive system of standards and regulations to enforce them.
Under the OSH Act, OSHA was granted the authority to develop and enforce standards covering a wide range of industries and address various aspects of workplace safety, including hazard communication, personal protective equipment, electrical safety, and handling of hazardous materials.
The creation and evolution of OSHA’s 29 CFR 1910 regulations apply to general industries and most worksites, but there are also standards that are specific to the construction, maritime, and agricultural sectors.
Because the scope of work in construction is vastly different from that of general industry, as construction sites often involve unique hazards and risks that require specific safety protocols, OSHA’s 29 CFR 1926 standards, target the construction industry, alterations and/or repair, including painting and decorating. These standards must be adhered to by anyone who is performing work in the construction industry sector.
8 OSHA common standards in construction vs. general industry
It’s important to know the differences between the general industry standards and construction-specific mandates, especially in regard to construction safety. This helps to make sure workers are taking the proper precautionary measures needed for their scope of work, because a one-size-fits-all approach when adhering to OSHA regulations across industries puts employees at increased risk for injury, or death.
Below are eight common workplace safety standards, including the variations OSHA depicts within the construction and general industries.
1. Fall protection
Both general industry and construction-specific standards address fall protection in the same manner: to prevent employees from falling off of overhead platforms, elevated work stations, or into holes in the floor and walls.
OSHA’s construction-specific fall protection standards, however, are generally for falls from elevated surfaces that are six or more feet above a lower level. This includes hoist areas, walking or working platforms, excavation edges, roofs, and other hazardous elevated surfaces or structures.
These standards also address types of scaffolds and include specific scaffold training, residential construction (1926.501(b)(13)), and steel erection (1926.501(b)(5)). It also adds in underground construction, fall protection from cranes and derricks, and provides requirements for training in fall protection.
OSHA’s fall protection standards for general industry addresses falls due to typical workplace hazards, such as ladders, stairways, and powered platforms like manlifts or vehicle-mounted platforms.
Standard 1910 Subpart R also includes guidelines for specialized industries such as telecommunications, electric power generation, transmission, and distribution.
Courses about construction.
For construction.
Unlock your career potential with our free educational courses on Health & Safety, Data in Construction, and more.
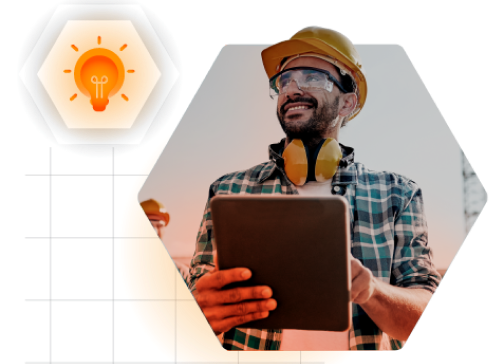
2. Personal protective equipment (PPE)
When considering personal protective equipment and its application, design, and equipment selections OSHA’s general industry and construction standards are similar.
But the construction industry standards have more in-depth criteria for PPE to help mitigate the increased hazards that workers are subject to on the job.
1926: Subpart E, for example, includes safety nets, requirements when working over or near water, and body protection such as hard hats, respiratory, eye and foot protection, and harnesses to keep workers protected when completing work in elevated spaces.
1926: Subpart P addresses requirements for protective systems when workers are performing excavations.
For more information on OSHA requirements for PPE, check out this Guide to PPE in Construction.
3. Confined spaces
There’s generally a clear distinction in standards between general industry and construction for confined spaces. In construction, confined spaces are large enough for employees to enter and perform assigned tasks, but are not designed for continual occupancy by workers because they present life-threatening hazards.
These areas such as manholes, crawl spaces, or HVAC ducts, provide limited entry and exit points for workers and pose risks for asphyxiation from low oxygen or exposure to toxic or flammable chemicals, being crushed or buried, or drowning.
OSHA provides detailed guidance on protecting construction workers who perform tasks in confined spaces, including requirements for a competent person to identify the type of confined space where work is to be completed. A competent person, according to OSHA, is capable of identifying hazards that pose dangers to workers and is authorized to implement measures to remove them.
A permit-required confined space (permit space) is a confined space that has one or more of the following characteristics:
- Contains or has the potential to contain a hazardous atmosphere
- Contains a material that has the potential for engulfing an entrant
- Has an internal configuration such that an entrant could be trapped or asphyxiated by inwardly converging walls or by a floor that slopes downward and tapers to a smaller cross-section
- Contains any other recognized serious safety or health hazard, such as unguarded machinery, exposed live wires, or heat stress
Guidelines for permit spaces are covered under OSHA’s general industry standards. Below are four key differences where the construction industry standard on confined space regulation is more stringent than what is required for general industry:
Mandated site evaluations: Construction industry standards require a competent person to evaluate the work site and identify confined spaces, including permit spaces (1926.1203(a)).
Best practices when multiple workers are onsite: There are specific details construction industry standards outline regarding coordinated activities when there are multiple employers at the worksite. These ensure additional hazards are not introduced into a confined space by workers performing tasks outside the space (1926.1203(h)).
Hazard monitoring: In construction, it’s important to watch for atmospheric (1926.1203(e)(2)(vi)) and engulfment hazards (1926.1204(e)(1)(iii)) continually as things can quickly change when working in small spaces, and exits and entry is restricted.
Handling permits: Allowing for the suspension of a permit, instead of cancellation (1926.1205(e)(2))
4. Illumination & lighting
OSHA's illumination standards also differ in focus between construction and the general industry. The illumination standard for construction, for example, focuses on the quantity and strategic placement of lighting.
Construction standard 1926.56 establishes minimum illumination requirements in foot candles for various working areas including offices, hallways, and exit ways. The foot-candle unit helps quantify the precise amount of illumination needed to maintain a safe and efficient working environment.
In addition, standard 1926.403 regulates the positioning of lighting outlets and switches. This ensures that outlets or switches are strategically placed so that employees changing bulbs or making repairs are not in harm’s way of moving machinery, live parts, or other potential hazards.
The general industry standard for illumination, on the other hand, emphasizes electrical safety, with regulations addressing electrical wiring installation, such as lighting.
This standard outlines the minimum criteria for wire size, grounding, and installation locations and procedures to ensure the proper and safe installation of lighting fixtures. Standard 1910.305, in particular, mandates that temporary lighting used during remodeling, maintenance, and repair of buildings should not exceed 600 volts. This aims to minimize potential electrical hazards and provide safer conditions for workers.
5. Stairways and ladders
For stairways and ladders, the construction industry's general regulations are more comprehensive and specific than those for the general industry.
Subpart X under the construction industry standard stipulates the use of a spiral staircase and double-cleated ladders for access or exits involving 25 or more employees, and also outlines extensive guidelines for all handrails, guardrails, and landings.
Additionally, Subpart X covers both portable and fixed ladder requirements, including the obligatory use of fall protection devices or lifelines when climbing heights that meet or exceed 24 feet. It also governs the specifications for cages and wells for fixed ladders, mounting specifications, and training and maintenance.
The general industry's standard aims to ensure accessibility and clear passageways, by requiring employers to provide stairways or ladders when there's a break in elevation of 19 inches (48 cm) or more and no other means of access are available.
When there's only one point of access between levels, it must be kept clear of obstructions to allow free passage by workers. Should free passage become limited, employers are required to furnish a second point of access and ensure that workers use it. This focus is more on ensuring that safe, unhindered passage is provided where necessary, which could help in minimizing accidents related to falls or tripping.
6. Fire extinguishers
While the requirements for fire extinguishers are relatively straightforward in addressing the placement, use, maintenance, and testing of portable fire extinguishers that are provided for employee use, there are still some distinct differences between construction and the general industry.
Construction standard 1926.150(c)(1)(vi), under fire protection and prevention, requires written plans, equipment, water supply, and training during course of construction. It also maintains these requirements post-construction/occupation for portable and fixed equipment and extinguishers, sprinklers, standpipes and hoses, alarm systems, and fire cutoffs.
For general industry, standard 1910.157 makes an exception on placement, use, and maintenance in cases when the employer has established and implemented a written fire safety plan requiring a total evacuation of the workplace upon alarm sounding. In these instances, employees would not use fire extinguishers and employer requirements fall under standards 1910.157(e) and 1910.157(f) for fire extinguisher inspections and hydrostatic testing.
7. Accident-prevention signs and tags
In general, signs and tags for the construction and general industry are similar according to OSHA. The construction industry, however, takes it a step further by including additional signage that addresses protection for employees completing road work.
Standard 1926 includes sign categories such as exit signs, directional signs, and traffic control signs and devices. Specifically, 1926.200 Traffic Control (g)(2) refers users to the Manual on Uniform Traffic Control Devices (MUTCD) for detailed instructions on maintaining safety for construction workers during road work.
Under the 1910.145 general standard, signs are categorized according to their use. These include danger, caution, safety instruction, slow moving vehicle emblems, and biohazard signs. Each of these contain a unique set of specifics, designs, colors, features, and required tags.
While both sets of standards aim to ensure worker safety through visual communication, the construction standards also encompass navigation and traffic control, reflecting the need for additional precautionary measures on construction sites.
8. Hazardous materials
Under 29 CFR 1910.1200, the Hazard Communication Standard (HCS) is a key OSHA regulation within the general industry standards that mandates comprehensive labeling, documentation, and training for hazardous materials. This standard ensures that employees are informed about the potential risks associated with the chemicals they handle.
For construction, 29 CFR 1926.1153, which focuses on crystalline silica exposure, addresses specific hazards prevalent in the construction industry.
These standards require employers to implement control measures to mitigate silica dust exposure, including the use of engineering controls, respiratory protection, and employee training.
Making a clear distinction with safety standards
Being familiar with the differences between OSHA’s general industry and construction industry standards allows employers and workers to implement the necessary safety measures tailored to their specific scope of work, reducing the risk of accidents, injuries, and illnesses. OSHA’s recognition of the unique hazards and risks present in the construction industry has paved the way for the creation and regulation of specific guidelines to mitigate these dangers for construction workers.
By adhering to OSHA standards, employers can foster a culture of safety and protect their workforce, ensuring a healthier and more secure work environment.
Was this article helpful?
Thank you for your submission.
100%
0%
You voted that this article was . Was this a mistake? If so, change your vote here.
Scroll less, learn more about construction.
Subscribe to The Blueprint, Procore’s construction newsletter, to get content from industry experts delivered straight to your inbox.
By clicking this button, you agree to our Privacy Notice and Terms of Service.
Categories:
Written by
Anthresia McWashington
19 articles
Anthresia McWashington is a Content Manager at Procore. She previously worked as an editor and reporter for Gulf Energy Information and Houston Media Group. She earned her BA in Communications and Journalism from the University of Houston. Anthresia loves track & field and practicing her French. She lives in Houston.
View profileAngelique Hamm
Angelique Hamm is a Strategic Product Consultant at Procore. Prior to joining the construction tech firm, Angelique spent three years working as a project engineer at Frymer Construction and Westport Construction. She also has a decade of experience in construction admin, preconstruction project management, and safety and risk management. Angelique is both OSHA 30 and CRIS certified.
View profileExplore more helpful resources
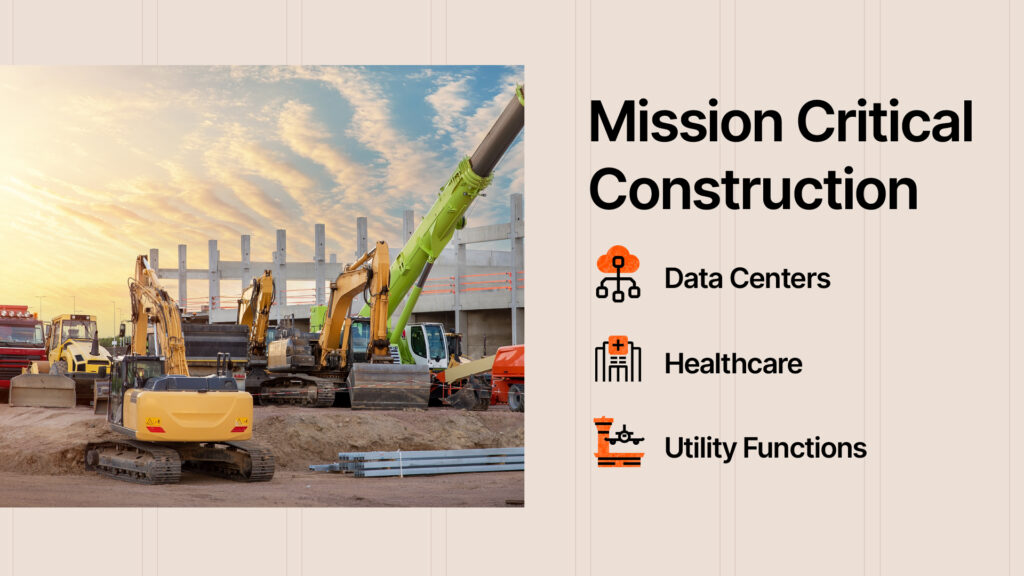
Mission Critical Construction: Strategies for Success
Mission critical construction involves building structures whose functions cannot afford to fail, as any disruptions can lead to significant consequences for society. Keeping data centers, hospitals, power plants and other...
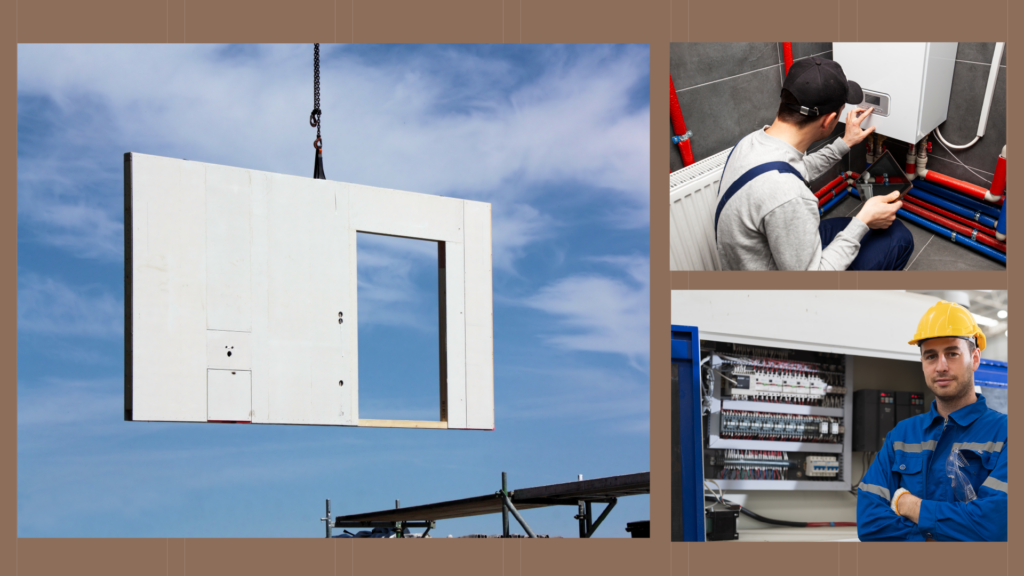
Modular Construction and MEP: A Collaborative Pairing
In an age of supply chain disruptions, workforce shortages, and rising material costs, off-site construction — including modular construction methods and prefabricated materials — is surfacing as a multipurpose solution....
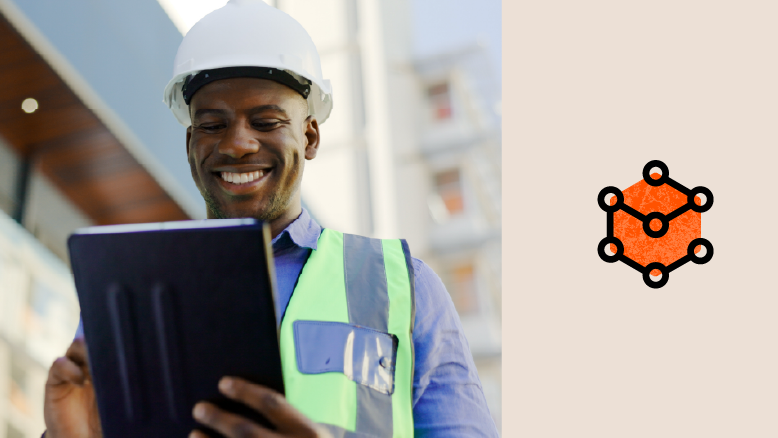
Connected Construction: Transforming the Industry Through Integration
Construction projects are becoming increasingly complex, so companies need to innovate to accurately and profitably complete these modern structures. Connected construction — using technology and data to improve communication, processes...
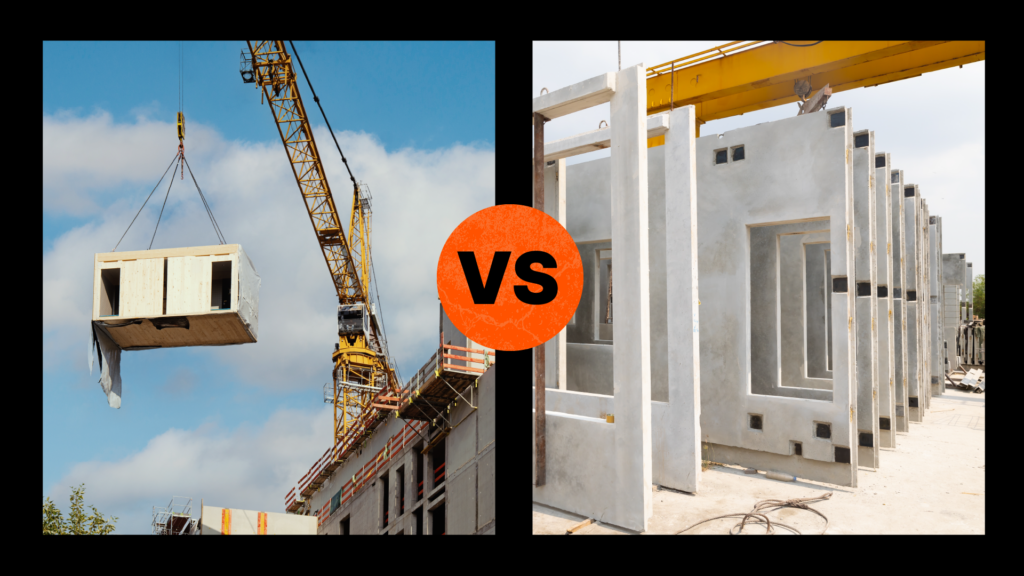
Off-Site Construction: Prefab vs. Modular
As the construction world becomes ever more competitive, deadlines get tighter and the margin for error gets slimmer, project owners around the world are always looking for an edge. Thanks...