— 20 min read
The Preconstruction Phase: A Deep Dive into the Precon Process
Last Updated Mar 13, 2025
Last Updated Mar 13, 2025

Preconstruction is a strategic phase of a construction project that bridges the gap between the initial plans drawn up in the predevelopment stage and the physical activities associated with on-site construction. This phase refines initial project ideas into concrete plans that balance cost efficiency and quality while identifying and mitigating potential risks.
The essence of preconstruction is to transform broad strokes into fine details. This phase encompasses a wide range of activities, from design development and contractor selection to risk analysis and project scheduling. You might find project managers collaborating closely with architects to fine-tune designs, cost estimators developing detailed budgets, or construction managers identifying potential safety hazards and devising robust mitigation plans.
Below, we’ll examine why project owners and contractors focus so heavily on a thorough preconstruction process when aiming for a successful construction phase.
Table of contents
Importance of Preconstruction
Preconstruction is the foundation that takes a construction project from idea to physical reality. During the preconstruction phase of a project, owners, construction project managers, architects, engineers, and other stakeholders tackle important questions, including:
- Have we fully refined the design to account for all practicalities of construction?
- Which contractor is most suitable for our specific project requirements?
- How do we efficiently organize resources and mobilize for construction?
- How can we best anticipate and mitigate potential risks, both in terms of safety and cost?
- What are the realistic timelines for each phase of construction?
- Have we obtained all necessary permits and licenses for our project?
Addressing these questions enables the project team to avoid roadblocks and ensure that the project gets off to a smooth start.
The work that happens during the preconstruction phase sets the stage for the project’s later successes — or failures. Projects with shaky budgets, poor risk mitigation tactics, shoddy site assessments, and negligent designs break ground all the time — but they rarely make it through the construction phase unscathed.
Change orders, budget or financing problems, differing site conditions, and many other issues are virtually guaranteed to arise. The most successful developers and construction professionals know that projects live and die according to preconstruction management.
The Preconstruction Team
Before preconstruction begins, the owner or developer will assemble the team that will work together to complete all of the activities necessary to prepare for the project. The actual professionals and companies involved will depend greatly on the type of construction project and its size and scope.
Owner or Developer
The owner or developer sets the project objectives, budget, and other criteria. Developers who work on many projects or have a construction division of their company may assign a project manager or owner’s rep to manage the preconstruction process.
Design Team
The design team is responsible for designing every detail of the project.
- Architects or designers prepare preliminary designs, drawings, and specifications. They work closely with the owner to develop a vision for the project.
- Civil Engineers provide site analysis, including assessments of the land, drainage, traffic patterns, and other site-specific factors.
- Structural Engineers work alongside architects to ensure the design is structurally sound, providing expertise on foundations, structural systems, and materials.
- Mechanical, Electrical, and Plumbing (MEP) Engineers provide design and input for the building's critical systems.
General Contractor/Construction Manager
Often, owners will hire a general contractor or construction manager (GC or CM) to the team to provide input on constructability, budget estimates, scheduling and potential construction methods.
Specialty contractors (like plumbing, electrical, HVAC) might also be consulted during the preconstruction phase to provide insights on specific elements of the project, especially if there are unique or challenging components.
For simplicity, we use the term “GC” or “general contractor” throughout this article when describing activities that a construction manager may perform.
This is by no means an exhaustive list. Many other players may be involved, including legal counsel, environmental consultants, government representatives, and more. A savvy owner will identify the knowledge gaps or needs as they build the preconstruction team to ensure they hire professionals with the right experience and skill sets for the job.
Build a Strong Foundation with our Preconstruction Course
With 20+ years of experience, Ben Ashburn teaches you how to streamline planning, bidding, and procurement for better outcomes.
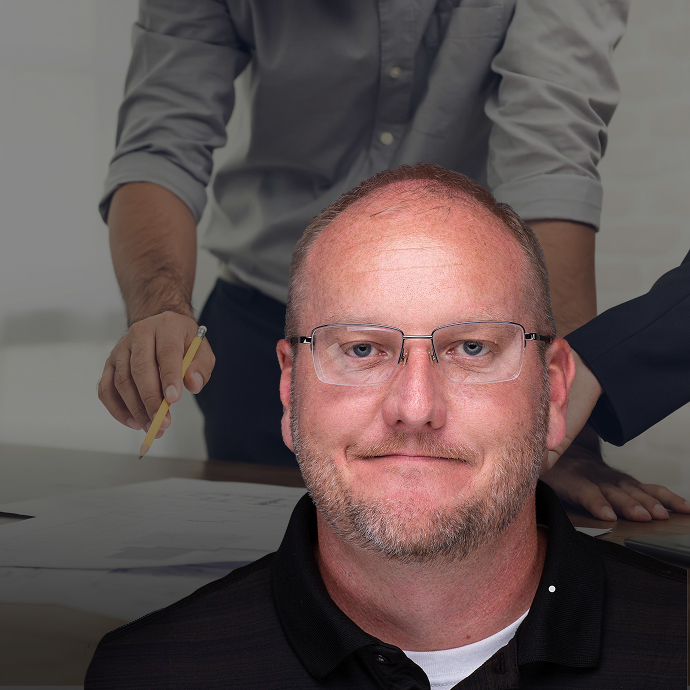
Key Activities in Preconstruction
During preconstruction, the project owner assembles the project team that will produce with architects, engineers, contractors, and other construction professionals to take a project from conception to construction. Before preconstruction begins, a project owner will have already completed key predevelopment tasks like feasibility studies, site assessment, land acquisition, financing, and preliminary design.
At that point, the focus shifts to further developing the design, selecting contractors, accounting for risk, and mobilizing for construction. To kick off this phase of a project, the owner or project manager often holds a preconstruction meeting with the key stakeholders to establish roles and responsibilities and clarify expectations.
Activity | Definition | Key Challenges |
Design Development | Architects and engineers refine project designs into detailed construction drawings and project specifications. | Balancing aesthetics and functionality with budgetary and regulatory constraints. |
Contractor Bidding and Selection | Project owners solicit construction bids, assess contractors’ qualifications, and establish a contractual relationship. | Ensuring an ethical bidding process, choosing the most competent contractor, and negotiating favorable terms. |
Risk Analysis and Mitigation | GC identifies potential project risks, assess cost implications, and plan for safety measures. | Anticipating unforeseen events, controlling costs, and upholding safety standards. |
Project Schedule and Timeline | GC devises a detailed project plan with timeframes for each construction phase or activity. | Predicting accurate timelines, scheduling interdependent tasks, and managing possible delays. |
Permitting | GCs and project owners secure all necessary construction permits, licenses, and regulatory clearances. | Navigating through complex regulatory environments and meeting all compliance requirements. |
Construction Mobilization | GC or CM organizes on-site setup, ensures workforce readiness, and arranges for equipment and materials needed. | Coordinating site setup, workforce scheduling, and timely delivery of materials and equipment. |
We’ll take a look at each of these major preconstruction activities below.
Design Development
Design development is the process of refining the preliminary concept into a collection of project specifications and drawings that detail the design, materials, methods, and standards required for construction. This process involves the collaboration of architects, engineers, interior designers, and potentially contractors with certain project delivery methods, like design-build (DB). Design development finds a balance between creative vision and technical or financial feasibility through several stages: architectural design, engineering design, interior design, and design review.
Activity | Description |
Architectural Design | The design team, led by the architect, develops comprehensive architectural plans outlining the project’s look, functionality, and structure. |
Engineering Design | The engineering team creates structural, mechanical, electrical, and plumbing designs, ensuring the building will be sound, efficient, and in compliance with codes. |
Interior Design | The interior design team plans the indoor spaces, considering aesthetics, functionality, and occupant needs. |
Design Review and Revisions | The design is reviewed and refined, taking into account feedback from various stakeholders, ensuring the design meets all project requirements. |
The architectural design phase involves creating schematic drawings that visually depict the project’s concept, layout, and structure. The design team then expands upon these schematics to develop detailed construction drawings. These documents provide in-depth information about the design and are essential in guiding the subsequent construction process.
Next, the engineering design process ensues. Specialists in structural, mechanical, electrical, and plumbing engineering ensure the building’s robustness, efficiency, and regulatory compliance. A key aspect of this phase is creating project specifications, which detail materials, standards, and methods for the project’s construction.
Interior design is an integral component of the design development phase as it pertains to crafting functional, aesthetically pleasing indoor environments. Here, the focus is on the eventual occupant’s experience, comfort, and productivity within the space.
Design Review
Throughout the design development phase, an iterative process of design review and revisions unfolds. Stakeholders, including the project owner, potential tenants, regulatory authorities, and community representatives, can provide valuable input, leading to design enhancements. This process is instrumental in achieving a design that aligns with the project’s budget, constraints, local regulations, and objectives.
Contractors can also engage in design review as a design-assist contractor. This gives the architect and project owner valuable input, such as the constructibility of the design, installation, and cost estimating.
Many projects use value engineering during the design development phase. Value engineers use a methodical review process to identify and remove unnecessary costs while ensuring the design meets the desired quality and functionality. Budgetary constraints inform and shape the design process from the beginning, ensuring the final design is economically viable without compromising on value.
Another increasingly common aspect of modern design development is the creation of a Building Information Modeling (BIM) model. BIM is a 3D model-based process that gives architecture, engineering, and construction (AEC) professionals the tools to efficiently plan, design, construct, and manage buildings and infrastructure.
A BIM provides a digital representation of the building’s physical and functional characteristics, enabling teams to anticipate and address potential issues before construction begins. BIM is a potent tool that enhances visualization, improves collaboration, and promotes better decision-making throughout the construction process.
At the culmination of the design development phase, the project team will have a comprehensive design, constrained and honed by budget considerations, regulatory compliance, and stakeholder feedback. With a solid design in place, the project owner is ready to select contractors, moving closer to the construction process.
Contractor Selection
After finalizing the project’s design, a project owner will seek to find a qualified general contractor to build the design. Typically, this involves using some combination of a Request for Qualifications (RFQ), a Request for Proposals (RFP), or an Invitation to Bid (ITB).
For contractors, this phase requires an understanding of the project (typically a short amount of time) to provide detailed cost estimation, and the development of a competitive bid.
Learn more: The difference between RFPs, RFQs, and RFIs
Activity | Description |
Issuing and Responding to RFQs or RFPs | The project owner issues an RFQ, and contractors respond with their qualifications or a detailed proposal, demonstrating their capability to deliver the project. |
Selective or Negotiated Bidding | The owner may invite select contractors or negotiate with a preferred contractor to submit bids for the project. |
Cost Estimation | Contractors analyze the project’s scope, labor, materials, and overheads to provide a comprehensive cost estimate. |
Bid Preparation | Contractors create detailed bids outlining their proposed approach, cost, and timeline for the project. |
Bid Evaluation and Leveling | The owner evaluates bids, considering factors such as cost, contractor experience, proposed schedule, and approach. Bids are “leveled” to ensure accurate comparison. |
Contract Negotiation | The owner and the selected contractor negotiate terms and conditions of the contract. |
The construction bidding process often begins with the owner issuing an RFQ or an RFP, soliciting contractors to demonstrate their ability to carry out the project based on their past performance, expertise, and financial stability. Contractors must have a deep understanding of the project’s requirements and express their qualifications — often related to a specific proposal, record of past successful projects, safety record, and financial stability.
Depending on the type of project, the goals of the owner, and existing relationships with contractors, the owner can choose from several different types of bidding. While open bidding is typically required on public projects of a certain size, owners on private commercial projects often prefer selective or negotiated bidding. This allows them to approach contractors they trust or negotiate directly with a preferred contractor, often ensuring a higher quality of work. As a contractor, being on the shortlist for selective bidding often indicates a strong reputation and trust in the industry.
Cost estimation is an essential part of a contractor’s process of writing a bid. Contractors analyze the scope of the project, the labor required, the cost of materials, equipment, overhead, contingency, and profit margin to arrive at an accurate cost estimate. A well-crafted cost estimate can demonstrate a contractor’s understanding of the project and their ability to deliver it within the owner’s budget.
Once the cost estimate is complete, the contractor creates a bid that outlines their proposed approach, cost, and timeline for the project. It should detail how they plan to execute the project, their estimated costs, and when they expect to complete the project.
During bid evaluation and leveling, the owner scrutinizes the bids to select the best contractor for the project. They compare bids on various factors, such as cost, experience, proposed schedule, and proposed approach — though price tends to be the definitive factor. Leveling the bids ensures a fair comparison by normalizing for differences in how contractors might have interpreted the project scope.
Finally, the project owner awards the contract to a specific contract and contract negotiation occurs. This involves finalizing the contract’s terms and conditions, such as payment terms, project timeline, and scope of work. It’s a chance for both parties to align their expectations and agree on how the project will proceed.
Risk Analysis and Mitigation
Risk analysis and mitigation help the project team anticipate potential issues, assess their impact, and develop plans to mitigate negative effects on the project. The general contractor or construction manager typically performs these activities to plan for cost control, site-specific safety measures, and quality control.
Activity | Description |
Risk Identification and Assessment | The team systematically identifies potential risks and evaluates their possible impact on the project’s objectives. |
Cost Control Planning | A strategy is developed to monitor and control the budget, preventing cost overruns and ensuring financial performance aligns with the project’s goals. |
Site-specific Safety Planning | The team prepares a safety plan tailored to the specific conditions and risks of the construction site, aiming to prevent accidents and ensure regulatory compliance. |
Quality Control Planning | A quality control plan is created to maintain the project’s standards, prevent defects, and ensure the final deliverables meet the project’s objectives and the owner’s expectations. |
Risk Response Planning | The team prepares responses to many kinds of potential risks, which could include avoiding, transferring, mitigating, or accepting risks. |
Risk analysis starts with risk identification and assessment. This involves a systematic process to detect potential risks that could impact the project and evaluate their likelihood and possible impact. This comprehensive risk review covers everything from budget and schedule risks to design, legal, regulatory, safety, and environmental risks.
Next, cost control planning involves developing strategies to monitor and control costs throughout the project. This goes beyond merely tracking expenses — it encompasses forecasting, variance analysis, and change control to keep the project within budget and prevent cost overruns. By controlling costs effectively, the project team can ensure that the project’s financial performance aligns with the budget — and maintains profitability for all parties.
Site-specific safety planning is the process of developing a safety plan that takes into account the unique conditions and potential hazards of the construction site. This safety plan is designed to prevent accidents, ensure the wellbeing of workers, and meet regulatory requirements. It includes protocols for proper use of safety equipment, handling hazardous materials, emergency response, and training.
Quality control planning involves the creation of a plan to maintain quality standards throughout the project. It aims to prevent defects, reduce rework and ensure that the final project deliverables align with the project’s objectives and the owner’s expectations. This might involve setting quality targets, defining inspection and testing procedures, and establishing a process for handling defects and changes.
Finally, risk response planning involves preparing strategies to deal with identified risks. The team might choose to avoid, transfer, mitigate, or accept risks, depending on their potential impact and the project’s risk tolerance. This response planning helps ensure the team is prepared to proactively address risks and maintain control over the project’s outcomes.
Project Scheduling
The GC produces a detailed project schedule that lays out the timeline of all tasks necessary to complete the project, taking into consideration dependencies (i.e. tasks that must be finished before others), the resources required, and potential risks.
The schedule serves as the project’s roadmap, guiding all involved parties throughout the project’s lifecycle.
Activity | Description |
Developing Work Breakdown Structure (WBS) | The team defines the project’s scope into manageable tasks, providing a foundation for detailed scheduling and resource allocation. |
Selecting Scheduling Methodology | A project scheduling methodology, like Critical Path Method (CPM) or Program Evaluation and Review Technique (PERT), is selected based on the project’s needs. |
Identifying the Critical Path | The sequence of project activities with the longest duration is determined, highlighting tasks that can’t be delayed without affecting the project turnover date. |
Resource Allocation Planning | Resources such as labor, materials, and equipment are assigned to each task, ensuring their availability aligns with the project schedule. |
Risk Assessment in Scheduling | Potential scheduling risks are identified and assessed, allowing for contingency planning in the schedule. |
Visualizing Construction Schedules | The team develops visual representations of the schedule, such as Gantt charts or network diagrams, to clearly communicate the project timeline and dependencies. |
A well-planned project schedule begins with the development of a Work Breakdown Structure (WBS). This process breaks down the project’s scope into manageable tasks, providing a clear foundation for scheduling and resource allocation. Each activity is then linked with the necessary resources and dependencies to form a cohesive project timeline.
Identifying the critical path involves outlining the sequence of dependent tasks that takes the longest time to complete. As these tasks directly impact the project’s finish date, any delay on the critical path will inevitably delay the whole project. Understanding the critical path allows project managers to focus on managing these crucial tasks effectively.
Resource allocation planning is the process of assigning resources — such as labor, materials, and equipment — to each task in the schedule. This ensures that the necessary resources are available when needed, preventing schedule delays due to resource shortages.
Risk assessment in scheduling involves identifying and evaluating potential risks that could impact the project schedule. This could include unforeseen delays, changes in scope, or resource availability issues. Risk assessment helps the team develop contingency plans and buffer times in the schedule, allowing for more accurate and realistic project timelines.
The team can visualize the project schedule using tools like Gantt charts or network diagrams. These visualizations provide a clear picture of the project timeline, task dependencies, and progress, making it easier for all stakeholders to understand the project’s status and expectations.
Finally, the project team chooses an appropriate scheduling methodology. Methods like the Critical Path Method (CPM) or Program Evaluation and Review Technique (PERT) provide structured frameworks for creating and managing the project schedule.
Permitting
Obtaining proper permits ensures the project complies with all relevant regulations and codes. This process involves acquiring necessary permissions and clearances from local, regional, and sometimes national regulatory bodies.
Though the beginning of the permitting process typically begins in the predevelopment phase, it extends through the preconstruction period and can even continue into the construction phase.
Activity | Description |
Pre-application Meetings | Engage with relevant government bodies and authorities to understand permitting requirements and processes. |
Application Preparation and Submission | Develop detailed plans and documents for permit applications, and submit them to the appropriate bodies. |
Plan Review | Regulatory bodies review the submitted plans, identify issues, and request revisions if necessary. |
Permit Issuance | Once all requirements are met, authorities issue the necessary permits for the project to proceed. |
During pre-application meetings, the project team meets with permitting authorities to discuss the project and understand the specific requirements for permit applications. These meetings help set expectations and lay the groundwork for a smoother permitting process. This is a step where any potential roadblocks can be identified and mitigated early on.
Following these meetings, the project team prepares the necessary documentation for permit application submission. These documents often include detailed project plans, environmental impact assessments, and other required information that varies depending on the specifics of the project and the jurisdiction in which it’s located.
Once the application is submitted, the relevant authority conducts a plan review. During this stage, the submitted plans are scrutinized for compliance with local codes, regulations, and any specific requirements for the project. Any identified issues are communicated back to the project team, who will then revise the plans accordingly. In some cases, community input is required during the review stage, since a project may affect neighboring structures or communities.
The final step is permit issuance. After all the requirements are fulfilled, the necessary permits are issued, giving the green light for construction to begin. It’s important to note that permits often come with conditions and requirements that must be adhered to throughout the construction process. Non-compliance can result in penalties or even the revocation of permits, halting construction.
Construction Mobilization
Construction mobilization marks the transition from preconstruction to the physical start of work on site. This process involves preparing the construction site, assembling the construction team, arranging necessary equipment and materials, setting up site facilities, and ensuring proper safety measures are in place.
Learn more about managing construction mobilization costs
Activity | Description |
Site Preparation | Prepare the site for construction by clearing, grading, setting boundaries, and implementing necessary erosion and sediment control measures. |
Team Mobilization | Assemble the on-site construction team, including key personnel like the project manager, site supervisor, and safety manager. |
Equipment and Materials | Arrange necessary construction equipment and materials on site. |
Site Facilities Setup | Set up site offices, temporary utilities, staging areas, worker facilities, and safety installations. |
Safety Measures | Implement necessary safety measures including safety signage, fencing, safety equipment, and fire department connection. |
Site preparation is the first step in mobilization. This typically involves clearing the site, removing any existing structures, grading the site for drainage, setting site boundaries, preparing access for equipment and materials, and implementing necessary erosion and sediment control measures. This process prepares the ground for the upcoming construction activities and helps to minimize potential site-related risks.
Next, team mobilization takes place. Key members of the construction team, such as the project manager, site supervisor, safety manager, and various trade personnel, are assembled on site. These individuals are instrumental in coordinating and managing construction activities and ensuring a safe and efficient work environment.
In tandem with team mobilization, the project sees the arrival of equipment and materials. The necessary construction machinery and equipment are brought to site, and arrangements for material delivery are coordinated to align with the construction schedule. Proper planning here ensures that work can proceed without unnecessary delays.
Site facilities setup involves establishing temporary facilities needed to support construction activities. This can include site offices, storage areas, worker facilities like restrooms and break areas, and any necessary safety installations.
Lastly, the team will put in place necessary safety measures and procedures to protect workers and the public. This includes safety signage, fencing to secure the construction site, and the provision of personal protective equipment (PPE) for the workers. A site-specific safety plan is implemented, which outlines procedures for safe work practices, emergency response, and ongoing safety training.
The Preconstruction Playbook
Learn to navigate challenges, understand root causes, and harness technology for smoother project execution. Revolutionize your approach and unlock your team's potential.
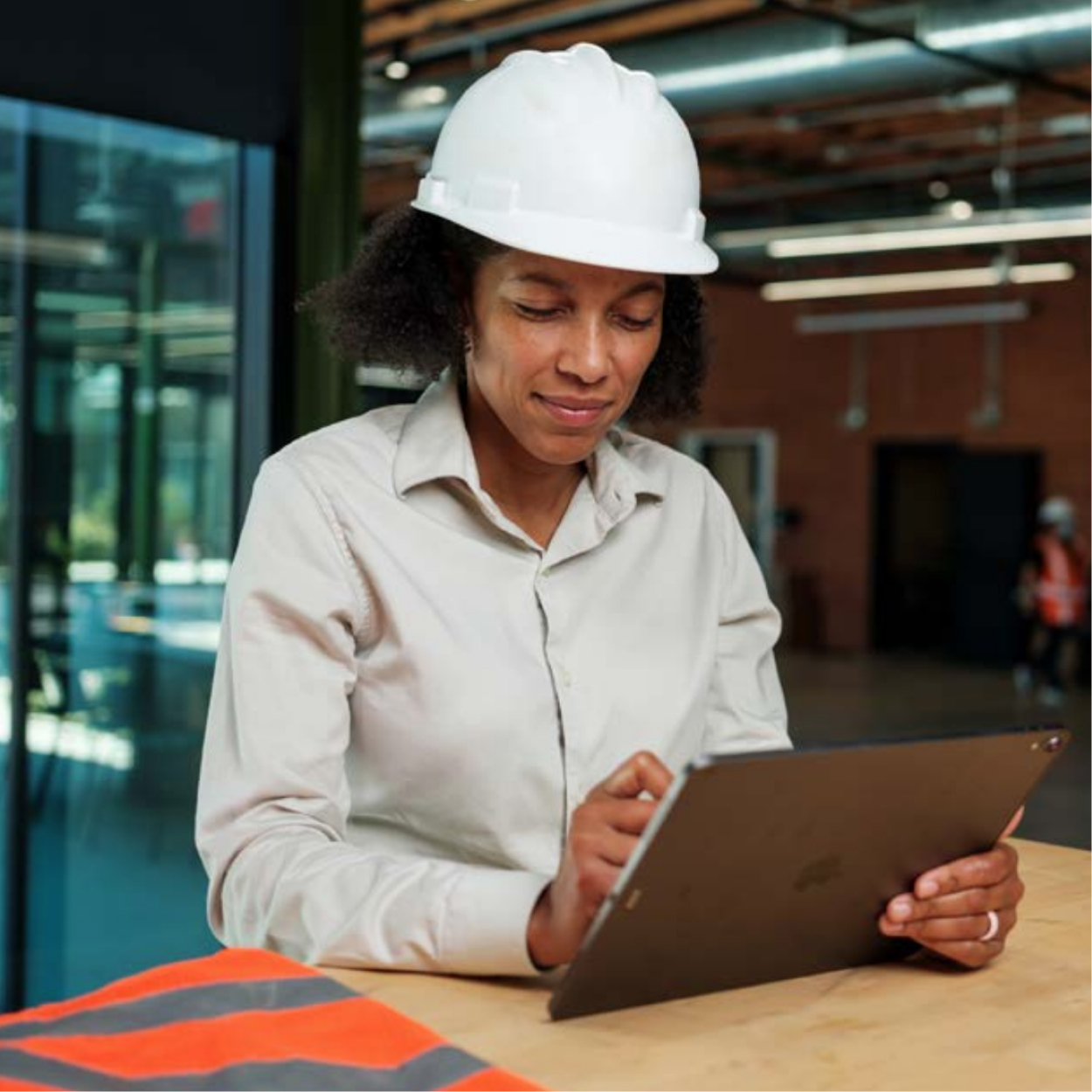
Transitioning Seamlessly From Preconstruction to Construction
The preconstruction phase is a critical juncture to lay the groundwork for successful project completion. Elements like design development, contractor selection, risk analysis, project scheduling, permitting, and construction mobilization require careful planning, rigorous analysis, and thoughtful decision-making.
But what happens when all the meticulous preconstruction planning meets the on-site reality of construction?
In the best case, project owners and contractors rely on a single source of truth that carries relevant information from preconstruction – budgets, schedules, specifications, etc. – right into the construction phase. Construction project management software creates a single repository for all project data, giving stakeholders access to critical details from the office or the field, mitigating the risk of miscommunication or data loss. During and after construction, owners and contractors can easily compare preconstruction plans to actual performance on the jobsite, enabling more accurate predictions and outcomes for future projects.
With this information at their fingertips, project teams can stay on track, maintaining timelines and budgets while delivering the quality specified in the project plans.
Was this article helpful?
Thank you for your submission.
100%
0%
You voted that this article was . Was this a mistake? If so, change your vote here.
Scroll less, learn more about construction.
Subscribe to The Blueprint, Procore’s construction newsletter, to get content from industry experts delivered straight to your inbox.
By clicking this button, you agree to our Privacy Notice and Terms of Service.
Categories:
Tags:
Written by
Janine Trinidad
21 articles
Janine Trinidad is a Construction Educational professional for Procore Technologies. In previous roles, Janine managed all phases of construction on hotel, mixed-use, and institutional projects in the San Francisco Bay area. She was responsible for negotiating contract budgets and change orders, managing RFIs and submittals, and overseeing quality control, among other duties. She is also a certified transformational coach with a focus on women-centered and trauma-informed methods. She is passionate about transforming the construction industry to be a healthier, more successful and welcoming place to work and believes technology and education are allies in doing so.
View profileDaniel Gray
28 articles
Daniel is an educator and writer with a speciality in construction. He has been writing construction content for Procore since 2022, and previously served as a Procore Content Manager before continuing to pursue an education career as an Assistant Headmaster for Valor Education in Austin. Daniel's experience writing for construction — as well as several clients under an agency — has broadened his knowledge and expertise across multiple subjects.
View profileExplore more helpful resources
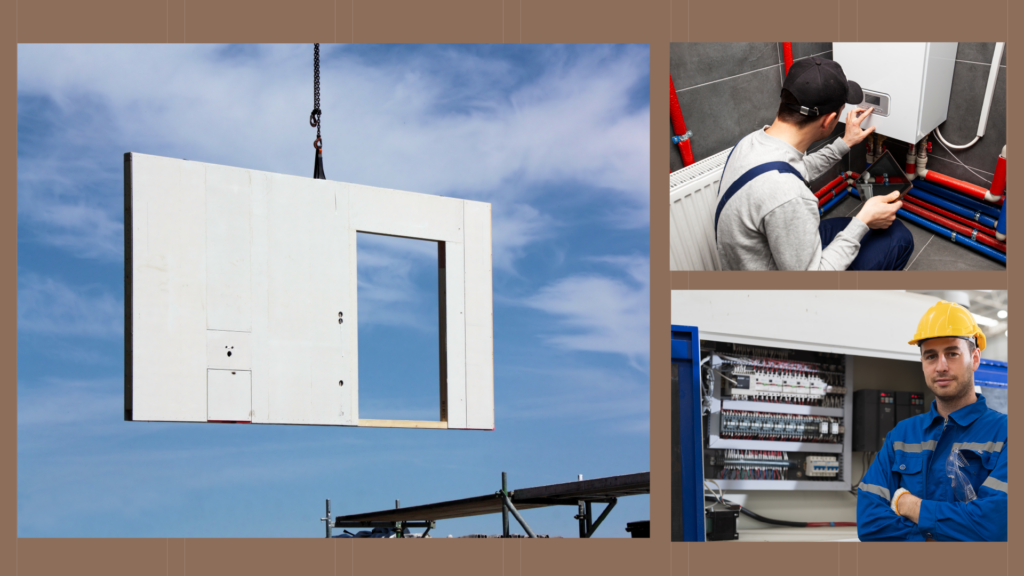
Modular Construction and MEP: A Collaborative Pairing
In an age of supply chain disruptions, workforce shortages, and rising material costs, off-site construction — including modular construction methods and prefabricated materials — is surfacing as a multipurpose solution....
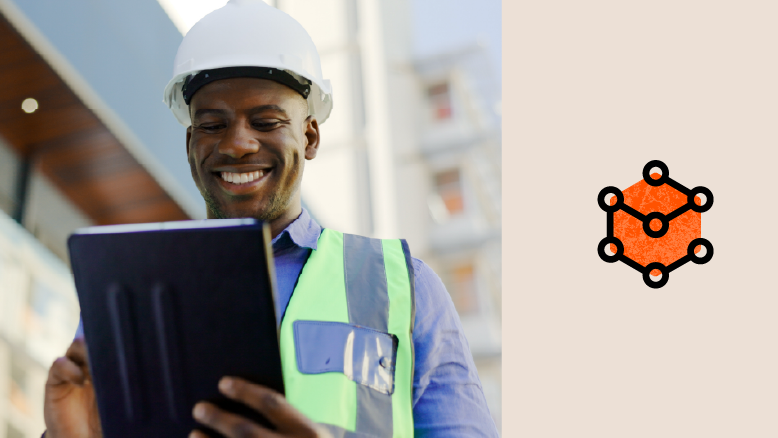
Connected Construction: Transforming the Industry Through Integration
Construction projects are becoming increasingly complex, so companies need to innovate to accurately and profitably complete these modern structures. Connected construction — using technology and data to improve communication, processes...
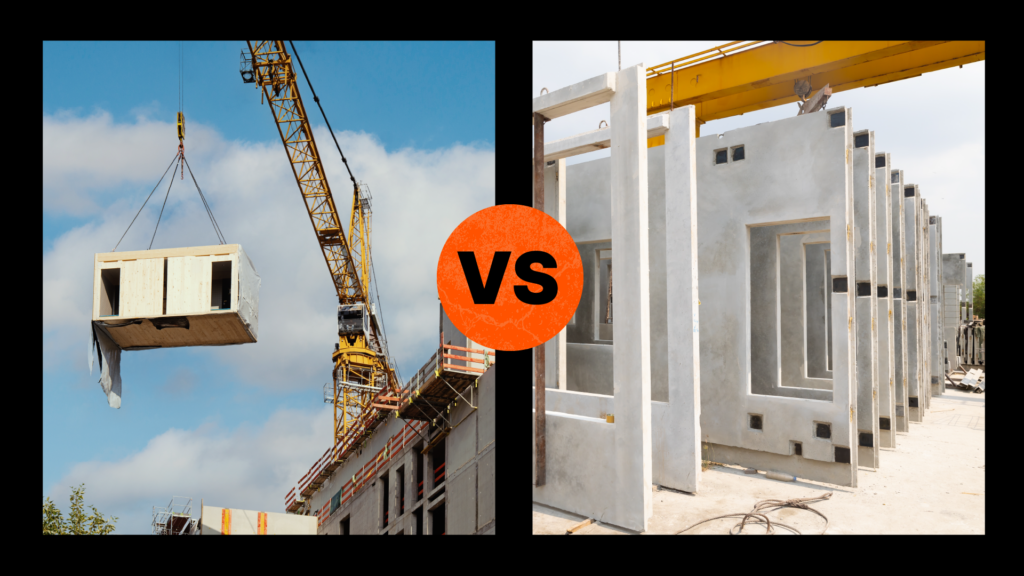
Off-Site Construction: Prefab vs. Modular
As the construction world becomes ever more competitive, deadlines get tighter and the margin for error gets slimmer, project owners around the world are always looking for an edge. Thanks...
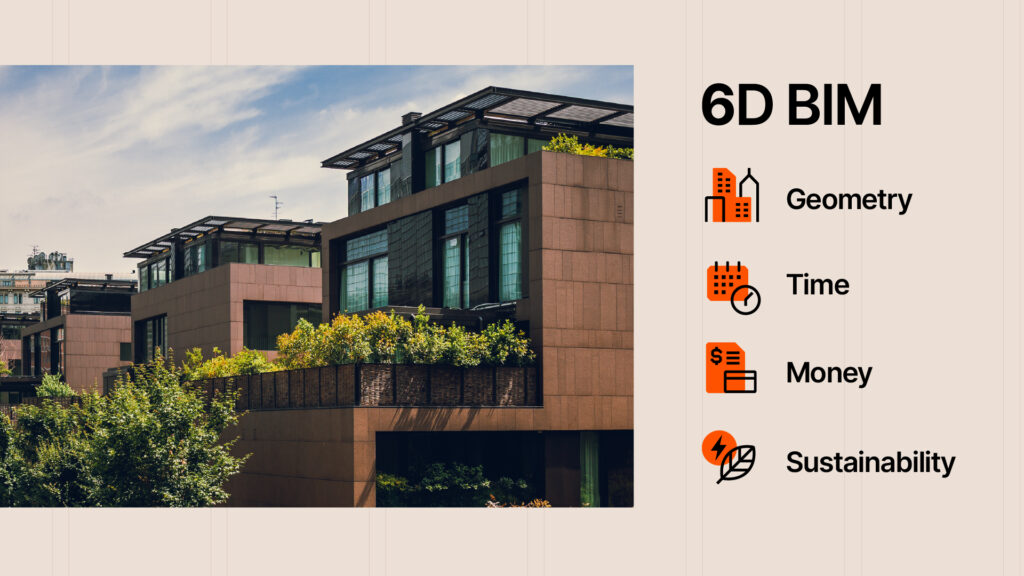
The Role of BIM in Sustainable Construction
Building information modeling (BIM) is transforming the architecture, engineering, and construction (AEC) industry. With this kind of sophisticated modeling, the industry has shifted from designing in 2D to 3D. This helps...