— 7 min read
The Role of the Procurement Management Plan in Construction
Last Updated Jun 6, 2024
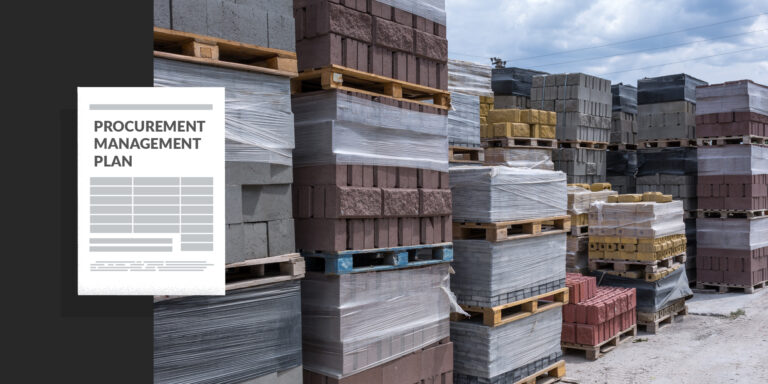
Procurement is a critical step in any construction project. It’s also a step that can go from relatively simple to completely unwieldy if not carefully managed and planned. Creating a formal procurement management plan can be extremely helpful on large projects, where multiple contractors can need infinite different resources throughout construction.
This article will explain procurement management plans, what to include and the benefits of having one on hand throughout a project.
Table of contents
What is a Procurement Management Plan?
A procurement management plan is a comprehensive document laying out in detail how materials will be purchased on a project. This includes who is going to be responsible for making purchase requests, what forms need to be used, and who is the buying agent that a project will work through. Procurement management plans include procurement schedules that are connected to submittal registers and workflows. Additionally, procurement management plans also help mitigate risks associated with long lead times.
Smaller jobs typically won’t have a formal procurement management plan as it’s easier for a small team to be nimble and purchase materials as needed. Once jobs scale up though, there is an increased amount of risk. Creating a procurement management plan and formalizing the purchase process helps mitigate some of that risk.
On the highest level, a procurement management plan lays out how all the materials on a project are purchased. Having a well-thought-out procurement management plan far in advance of the start of a project will prevent myriad headaches in the long run.
Procurement Strategy vs. Procurement Management
These two terms are so similar —both aspects of successful project management — that they may get confused. However, they cover two different aspects of procurement on job sites. Procurement strategy is the larger game plan for how materials will be acquired. This involves managing cash flow, order timing, and delivery timing, among other things.
Procurement management is the more tangible, nitty-gritty of procurement. Procurement management involves creating the documents and workflow needed to maintain order in your procurement plan. The two different areas work in tandem but cover slightly different areas of focus.
Understanding Procurement Management
It may seem like an obvious statement, but every single piece of material on a jobsite — from a nut and bolt to massive steel beams — needs to be purchased. Those purchases cannot simply happen without any planning or tracking. Budgets need to be maintained, and schedules need to be adhered to. Creating a plan allows for an increased understanding of cash flows, specifically how and when money needs to be spent.
The purchasing phase can be an overwhelming part of a project. Inventory needs to be purchased on a schedule that allows them to be delivered as close to the time they’re needed as possible – also known as just in time (JIT) delivery. Some materials can’t sit out in the sun, some can’t get rained on, the less time between their arrival on site and their use, the better.
Staggering purchases also ensures budgets won’t be blown quickly. There’s no need to buy roofing materials before the rest of a structure has been built. There’s no need to purchase plumbing before a foundation has been poured. Holding off on these purchases means fewer large lump-sum purchases. There is also a delicate balance between when to write up a purchase order (PO) versus when a buyer executes the order to their vendor.
Key Elements of a Procurement Management Plan
The procurement management plan dictates specifically how materials will be purchased. Under the plans, an engineer can’t simply swipe their credit card if they need a specific type of fastener or pipe. The procurement plan delineates the internal request process for purchases. The plan lays out what type of forms need to be filled out, as well as invoice forms and submittal registers. Preferred vendors and quantity, generally selected by the procurement specialist, will also be specified.
The procurement specialist identifies preferred vendors by comparing at least three quotes, determining the least expensive, and then checking with engineers to ensure the materials are still of good quality. The plan will also include waiver forms that can be used to allow purchases to be made from vendors outside the preferred list if deemed necessary.
The procurement management plan doesn’t necessarily dictate the budget of a project. However, the procurement professional or supply chain manager will be responsible for going out and looking for the best price possible. They will then confer with engineers and cost controllers to determine whether the quality of the product is adequate and the price feasible.
The biggest factor to consider while writing up early drafts of a procurement management plan is lead time. Materials need to be ordered with a long enough lead time to arrive on site at the correct time, without then being stored on-site for long periods of time. Lead times determine how hard crews need to sprint at the beginning of a project in order to get all the quotes in and built into their schedule.
The procurement management plan also delineates who gives final approval, typically the supply chain manager or procurement agent, and sends out the PO. When the materials are received, they are verified on site by the crews and cross-referenced with what was ordered. This can include a quality assurance and quality control (QAQC) step. Adding QAQC to a procurement management plan can be especially helpful if the project involves prefabricated materials because it provides clear guidelines on how each item will be cross-referenced with the plans drawn up by an engineering team. But QAQC can be used on anything, from prefabricated rooms to electrical cables, to ensure everything is delivered as expected.
Once everything is confirmed, the vendor will invoice the project, as laid out in the procurement management plan.
Benefits of Procurement Management Plans
Procurement management plans can seem like a tedious extra step to add to the beginning of a project. They have only become widely popular in the last several years, which means many teams still need to be convinced of their benefits. But taking a few extra days to walk through the different aspects of your procurement process and to make contingency plans can have huge benefits.
As previously mentioned, the biggest benefit of having a comprehensive procurement management plan is that you can mitigate risk. Procurement plans help minimize the likelihood of multiple teams purchasing the same materials. An example of this would be that multiple teams need to buy pipes. Without any kind of structured plan, different teams could be going to the same vendors to make the same kinds of purchases. Multiple POs can confuse vendors, increasing the chance that a job might be missed, or incorrectly paid off.
A procurement management plan also allows for better site management. Material delivery times can be better managed to ensure they arrive on site exactly when needed. This minimizes the amount of materials sitting around a job site for long periods of time. Too much material on-site prevents trucks from being able to maneuver easily and increases the likelihood of accidents.
Additionally, without a procurement management plan, the management of POs and invoicing typically falls to one person. They may have to wade through hundreds of emails to ensure everything is ordered properly. Given those circumstances, it’s easy to see how mistakes can be made. It’s far easier to spread the responsibility out and clearly delineate who needs to handle which task.
Procurement Management Plan: A Critical Step In Mitigating Risk
Solidifying clear workflows with regards to procurement, clarifying lines of communication and creating purchase plans can mitigate so many problems that can arise during construction projects. On large scale projects, procurement management plans are critical to ensure that efforts are not duplicated, purchases don’t fall through the cracks and that materials are on hand when needed. It can seem unnecessary to create a plan early on, but all members of a team will be grateful to have it throughout construction.
Was this article helpful?
Thank you for your submission.
50%
50%
You voted that this article was . Was this a mistake? If so, change your vote here.
Scroll less, learn more about construction.
Subscribe to The Blueprint, Procore’s construction newsletter, to get content from industry experts delivered straight to your inbox.
By clicking this button, you agree to our Privacy Notice and Terms of Service.
Categories:
Tags:
Written by
Makenna Ryan
Makenna Ryan is a Solutions Engineer at Procore. Prior to joining Procore, he spent seven years at McDermott International Inc. as a construction Manager and Senior Equipment Engineer. He also spent three years as a Project Engineer at Subsea7. Makenna received his B.S. in Mechanical Engineering and Technology from Texas Tech University. He is based in the Houston area.
View profileCait Bladt
13 articles
Cait Bladt is a multi-award winning freelance writer and producer. Her work has appeared at Vice, ABC News and Rolling Stone among others. She currently lives in Brooklyn with her cat Patricia.
View profileExplore more helpful resources
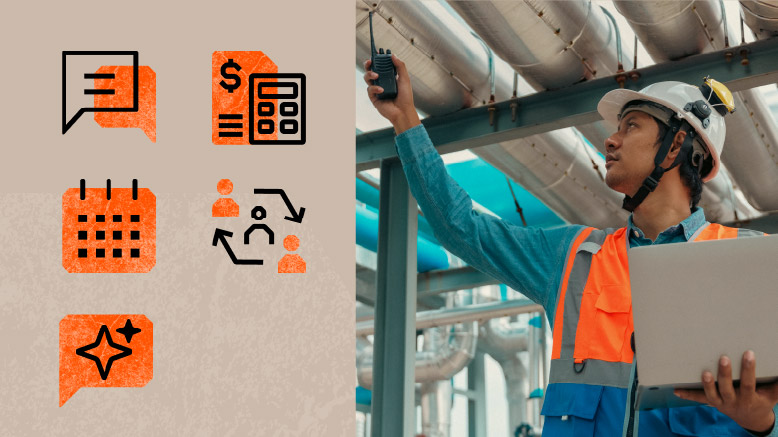
The Top 5 Skills of High-Performing MEP Professionals
Compared to standard MEP professionals, high-performing MEP pros don’t just get the job done. They also combine five key skills around technology, scheduling, finances, communications and flexibility into a proactive approach...
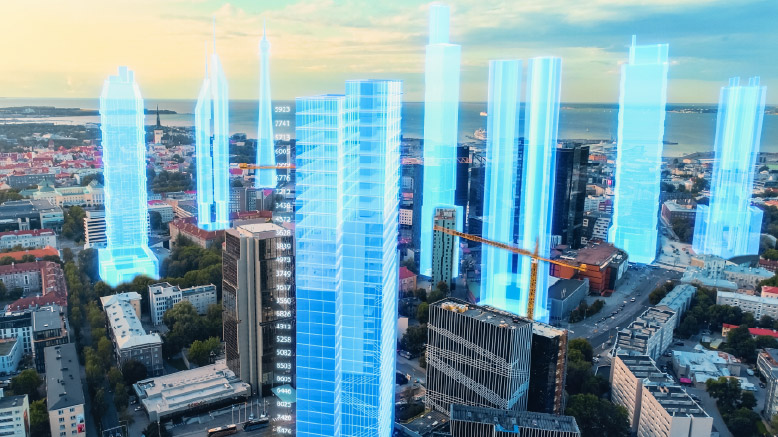
How AI is Reshaping Decision-Making and Project Resilience in Civil Construction
In construction, the ability to make informed, timely decisions is paramount. No longer is it sufficient to rely solely on historical data or reactive problem-solving. Enter artificial intelligence (AI), a...
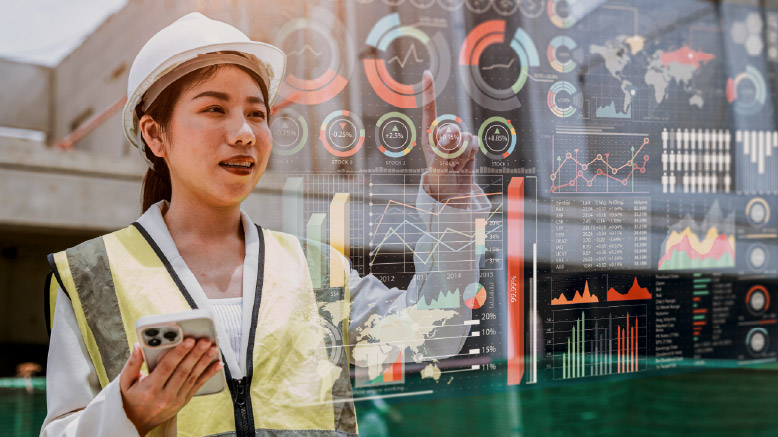
How AI is Redefining Efficiency & Safety in Civil Construction
As demand for new and modernized infrastructure surges, the civil construction industry faces an imperative to deliver projects with unprecedented speed, precision and safety. Emerging at the forefront of this...
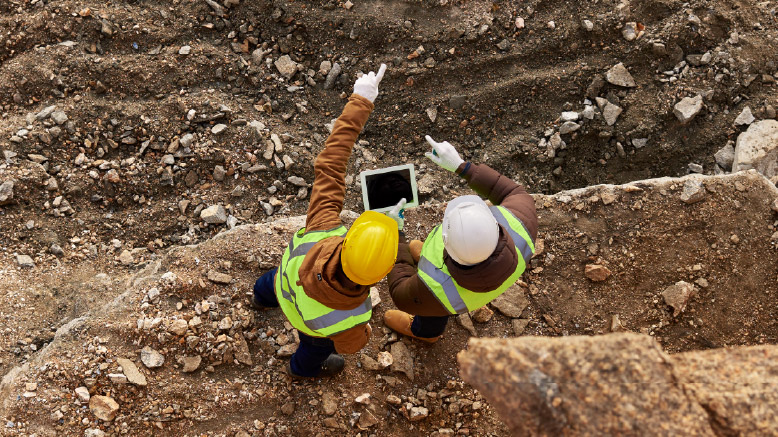
Building a Culture of True Tech Readiness in Civil Construction
While significant investments are pouring into revitalizing the nation’s infrastructure, the true capacity to capitalize on this opportunity hinges on more than just funding — it relies on a fundamental...
Free Tools
Calculators
Use our calculators to estimate the cost of construction materials for your next project.
Templates
Find a template to help you with your construction project tasks.
Material Price Tracker
Get the latest U.S. retail prices and view historical trends for common building materials.
Glossary
Explore key terms and phrases used in the industry.