— 6 min read
Improving Project Monitoring with Construction Quantity Tracking
Last Updated Apr 23, 2025
Last Updated Apr 23, 2025
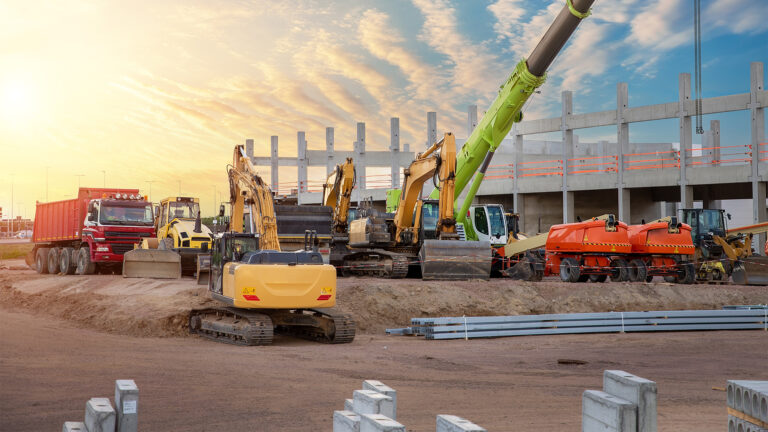
Once a construction project is underway, builders need to closely monitor the project's progress and make sure it's staying on schedule and within budget. Quantity tracking helps construction leaders manage resources effectively by giving them a true picture of how far a project has come.
This article defines quantity tracking in construction and discusses the tools and systems contractors can use to gain insights into their project progress.
Table of contents
What is quantity tracking in construction?
Quantity tracking is a measure of the progress on a construction project based on the amount of measurable units of production that have gone into the final installed project.
Quantity tracking looks at materials, labor and other resources that go into a construction project. Construction managers use these metrics to ensure that the project is on track and all the pieces and processes are accounted for, providing accountability and facilitating future planning.
For small and straightforward projects, a contractor’s quick assessment of the project’s completion may be enough — but for large and complex projects, getting the answer wrong can have significant consequences. Contractors need the right tools and systems to help them with accurate quantity tracking, allowing them to get a good sense of earned value.
Defining Construction Quantities
Quantity tracking only keeps tabs on activities and resources that provide a measurable difference to completing a project — those are the quantities being tracked. Examples of common construction quantities include square feet of installed tile flooring, volumes of concrete or weight, labor hours or length of rebar.
Quantities can be further broken down into those that are estimated and those that are installed. Estimated quantities are the projected amounts of materials and resources that were anticipated for a construction project and were used to create budgets.
Installed quantities are the actual amounts of materials and resources used during construction. The data collected on installed quantities provides a basis for assessing project progress, cost control and variance analysis.
Steps to Effective Quantity Tracking
Effective quantity tracking relies on several key components:
Gathering accurate data using tools and methods that ensure precision at every stage of the project
Establishing clear benchmarks to maintain consistency and accuracy, ensuring everyone measures quantities the same way
Keeping accurate records of the quantities used and what materials remain to maintain transparency and accountability
Ensuring all stakeholders, from on-site workers to project managers, are informed and involved in the process
The Benefits of Quantity Tracking in Construction
Quantity tracking helps contractors monitor their progress based on data instead of gut feelings, providing a true picture of earned value on the project and a metric that contractors may be able to use to course-correct when needed. There are a few key benefits to accurate quantity tracking.
Cost Control
Tracking the time and materials that go into completing a project can help pinpoint inefficiencies, allowing construction managers to minimize waste and reduce overall costs.
Resource Management
A firm grasp on project progress can help project managers allocate people and equipment effectively so that resources are in the place where they’re needed most. Effective resource management helps avoid delays and costly downtime.
Staying on Schedule
Tracking quantities in real-time is like keeping a finger on the pulse of the project: If conditions change, managers can recognize and react quickly to get activities back on schedule.
Quality Assurance
Tracking progress through quantities can help project managers detect deviations from the original plan that might lower project quality.
Common Challenges to Quantity Tracking
When done well, quantity tracking can give construction stakeholders the tools to manage more efficient and high-quality projects. However, there are some hurdles to using quantity tracking.
Data Accuracy
Managing project progress only helps with outcomes if the information the management team receives is true and timely. Delayed or incorrect data — which can happen when information gets sent back and forth between office staff and field teams, and finally makes it to a field supervisor — can hamper decision making and prove even more costly. The data used in quantity tracking has to be up to date and double-checked for accuracy.
Integration and Communication
Construction projects are complex and involve a lot of different processes. Teams and systems need to talk to one another so that decision makers have a full picture of the project to choose an effective path forward.
Rework or design changes can mess with quantity tracking, as can the use of disjointed spreadsheets. To use quantity tracking, teams need a consistent system that’s easy to update and share and integrates information from other systems.
Best Practices for Implementing Quantity Tracking
Set clear objectives and define the scope of tracking from the outset. A construction project team won’t track all installed quantities — it wouldn’t help that much and it would take way too long. Instead, pick the set of quantities that will help establish true project progress and, if delayed, would most impact all the work that comes after. Choose the metric that would best establish progress for each of those quantities.
Effective quantity tracking requires frequent upkeep and review. Establish systems for the collection of data in a central, accessible area and protocols for checking, verifying, and tracking all the data received.
Finally, encourage input from all levels of the team to improve processes and address any issues promptly.
The Role of Technology and Software in Quantity Tracking
Technology can help teams keep a tight grip on project progress by improving tracking, data quality and communication so that project teams have all the relevant information. Construction management software can automate data collection and reporting processes, which can reduce human error and help make sure project managers have up-to-date information at their fingertips.
The faster and more precise tracking can lead to quicker adjustments to plans as needed. Software also facilitates better communication across teams through centralized data platforms, so everyone is working from the same information, helping improve efficiency, reduce waste and helping to deliver better project outcomes.
AI and machine learning are transforming quantity tracking in construction with the amount of data they can assess at a rapid rate. These technologies analyze vast amounts of project data to identify patterns and trends that might be missed by humans. Further, AI can automate anomaly detection, alerting managers to potential discrepancies between estimated and actual quantities, allowing for proactive adjustments.
Stay updated on what’s happening in construction.
Subscribe to Blueprint, Procore’s free construction newsletter, to get content from industry experts delivered straight to your inbox.
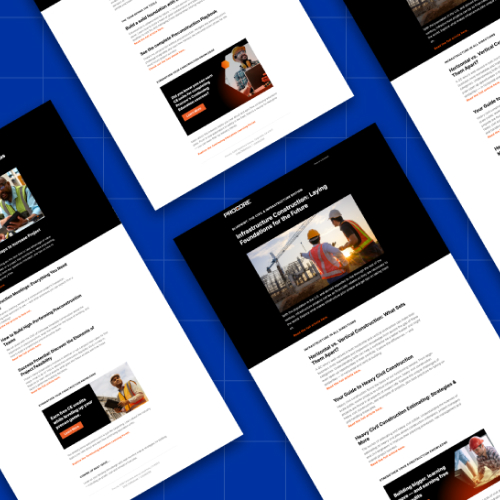
Is quantity tracking worth the effort?
Quantity tracking helps improve construction management by providing accurate and timely information on project progress to construction stakeholders. Improving quantity tracking processes can lead to more efficient and higher-quality construction outcomes.
Implementing quantity tracking software in construction projects can lead to substantial cost-saving benefits and a favorable return on investment (ROI). Accurate, real-time insights into material and labor use minimizes waste and prevents over-ordering.
Additionally, improved project management efficiency can result in fewer delays and lower labor expenses. The ability to quickly identify and address discrepancies in estimated versus installed quantities ensures tighter budget control and helps avoid costly project overruns. Over time, these efficiencies lead to significant savings and a strong ROI.
Was this article helpful?
Thank you for your submission.
0%
0%
You voted that this article was . Was this a mistake? If so, change your vote here.
Scroll less, learn more about construction.
Subscribe to The Blueprint, Procore’s construction newsletter, to get content from industry experts delivered straight to your inbox.
By clicking this button, you agree to our Privacy Notice and Terms of Service.
Categories:
Tags:
Written by
Kristen Frisa
70 articles
Kristen Frisa is a contributing writer for Procore. She also contributes to a variety of industry publications as a freelance writer focused on finance and construction technology. Kristen holds a Bachelor of Arts in Philosophy and History from Western University, with a post-graduate certificate in journalism from Sheridan College. She lives in Ontario, Canada.
View profileExplore more helpful resources
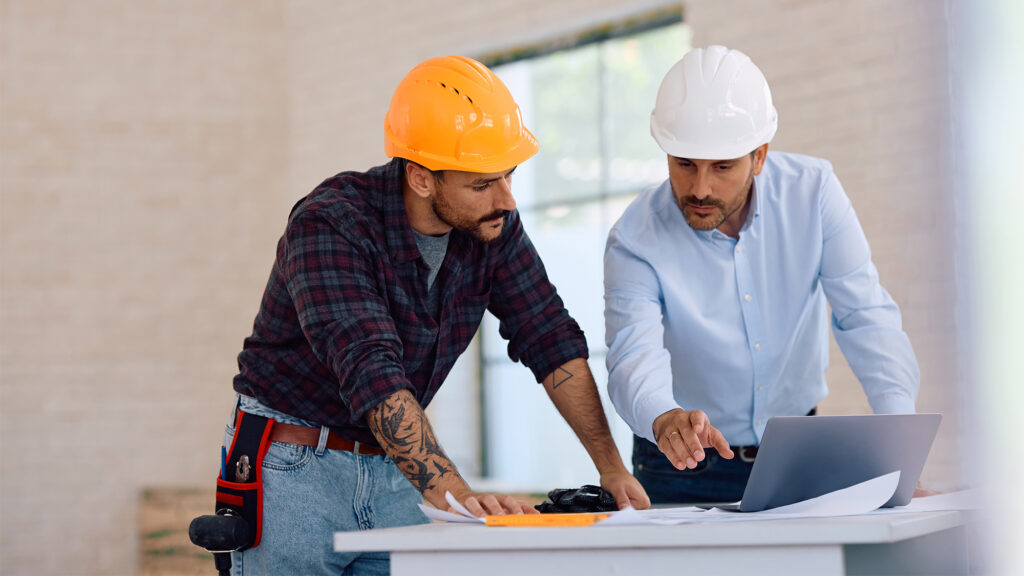
How to Understand and Use Architect’s Supplemental Instructions
Architect’s supplemental instructions, also known as ASI, offer a means of making small changes to the construction contract after it’s signed. The ASI is a document issued by the architect...
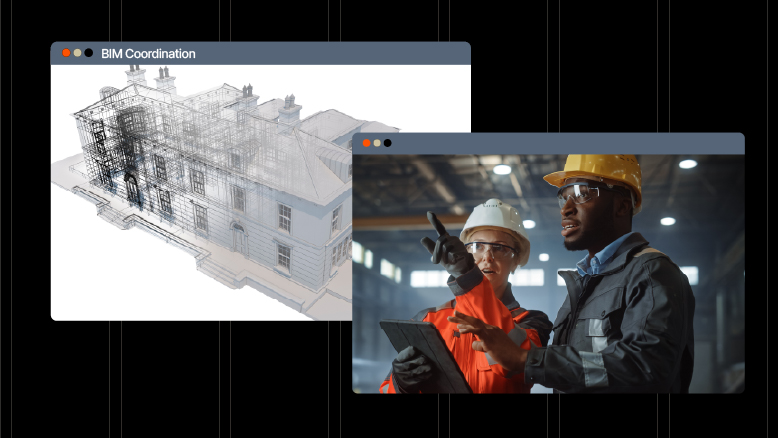
Streamlining Construction Projects with Effective BIM Coordination
The old saying goes: if you fail to plan, you plan to fail. Construction professionals know this better than nearly anyone. To take a project from a vision in an owner’s...
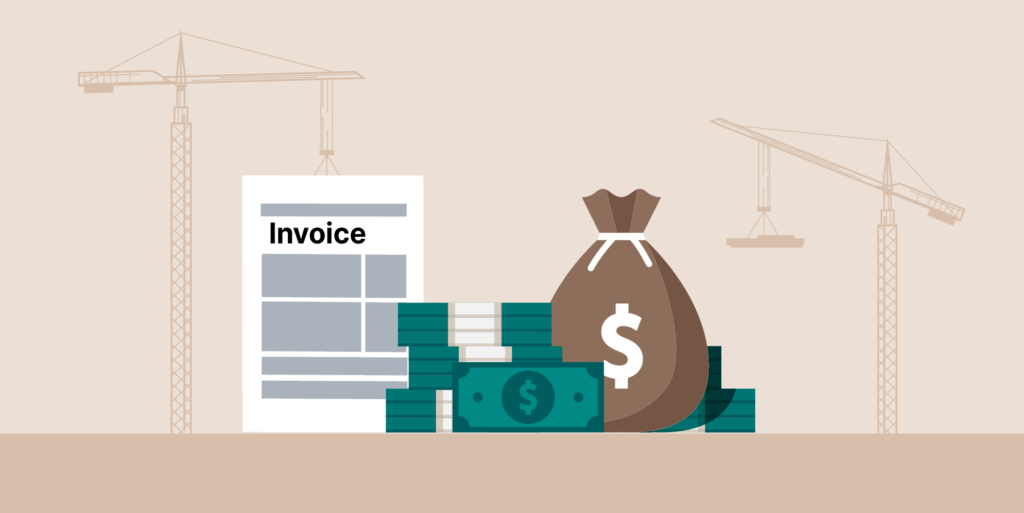
Construction Invoice Factoring: A Quick Guide
Construction companies need to maintain consistent cash flow. Projects can take years to complete, and delays and unforeseen events may keep expenses mounting. Adding to this load are typically high upfront...
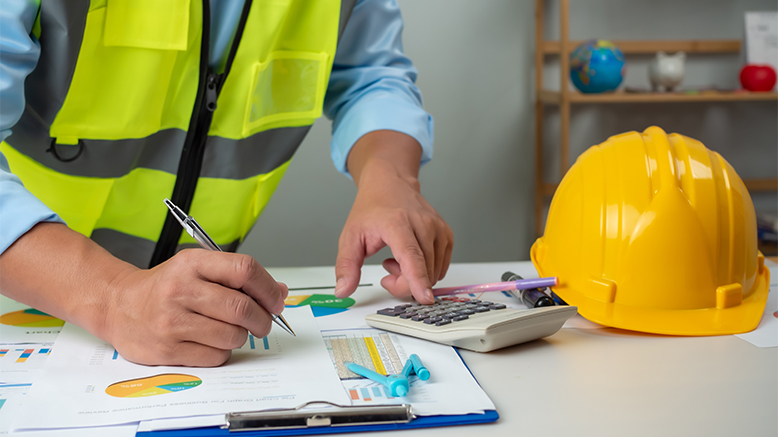
Understanding Subcontractor Bid Packages in Construction
Construction bid packages can have a cascading impact on the success of a construction project. The quality of a bid project may affect the quality of the bids, which in...