— 9 min read
A Guide to Resource Breakdown Structures in Construction
Last Updated Feb 28, 2025
Last Updated Feb 28, 2025
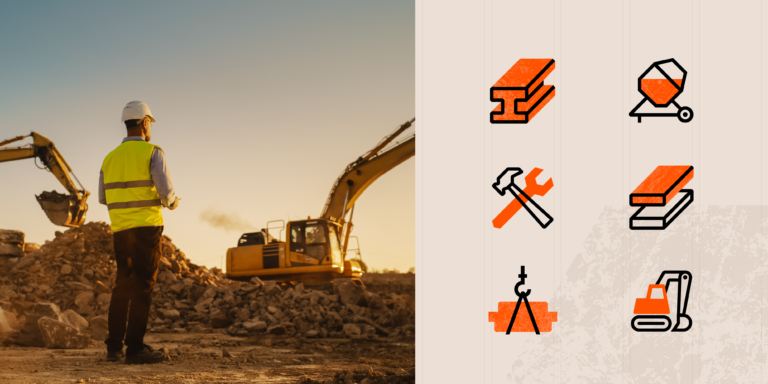
Construction project planning must account for many interlocking materials, people, machines and tasks to complete a build. Keeping a project on budget and schedule requires carefully managing those resources so the right people and materials are available when and where they are needed. A resource breakdown structure (RBS) is a project management tool that systematically lists all the resources needed for the project in a hierarchy to plan and track resource availability and use.
Allocating and tracking resources minimizes waste and helps project managers see an overview to manage construction resources proficiently. These include items like human resources, equipment and materials, as well as less concrete items like time and permits. Along with a work breakdown structure (WBS), the RBS helps project managers match resources to tasks, schedule construction more accurately and adeptly move resources as project needs change.
This article will define resource breakdown structures and describe the benefits of using an RBS. In addition, it will delineate the difference between a WBS and an RBS and outline the steps and best practices for creating an RBS.
Table of contents
What is a Resource Breakdown Structure (RBS)?
Project managers are charged with compiling an RBS during the preconstruction phase, coordinating needed talent, tools and supplies — plus any other less-tangible resources like time and space. Other team members contribute knowledge to the RBS, assisting the PM in accurately apportioning resources to each task.
The RBS divides the larger project into smaller tasks so everything required for a discreet work segment can be made ready when the time comes to perform the work. Allocating the proper personnel involves understanding the skills needed for each task, and listing the amounts of material required helps in resource planning so that supplies are available to workers when it’s time to begin a specific task. In addition, the task will be assigned a specified or estimated time to complete, the area the work will happen within and may require a permit or particular software or technology resources.
The purpose of the RBS is to help distribute resources wisely to accomplish project objectives. A construction RBS maps the relationships between resources, clarifying which depend on each other for optimal use. For instance, during mechanical, electrical, and plumbing (MEP) installation, materials such as conduits and pipes require scissor lifts and excavators to complete the work segment. The RBS also makes apparent the relationships between the timeline, storage space constraints and the need for material availability.
RBS Styles
Depending on the project management methodology, PMs can organize the RBS to suit the project and align it with other planning documents. Often, the RBS will be in a tree or hierarchy chart listing categories and itemizing individual resources within. A Gantt chart can add time for tasks to the RBS. Using the critical path method for scheduling helps create the hierarchy of resource importance to match functions that will impact the project schedule.
Using construction project management software eases creating the RBS and linking the list to other project documents.
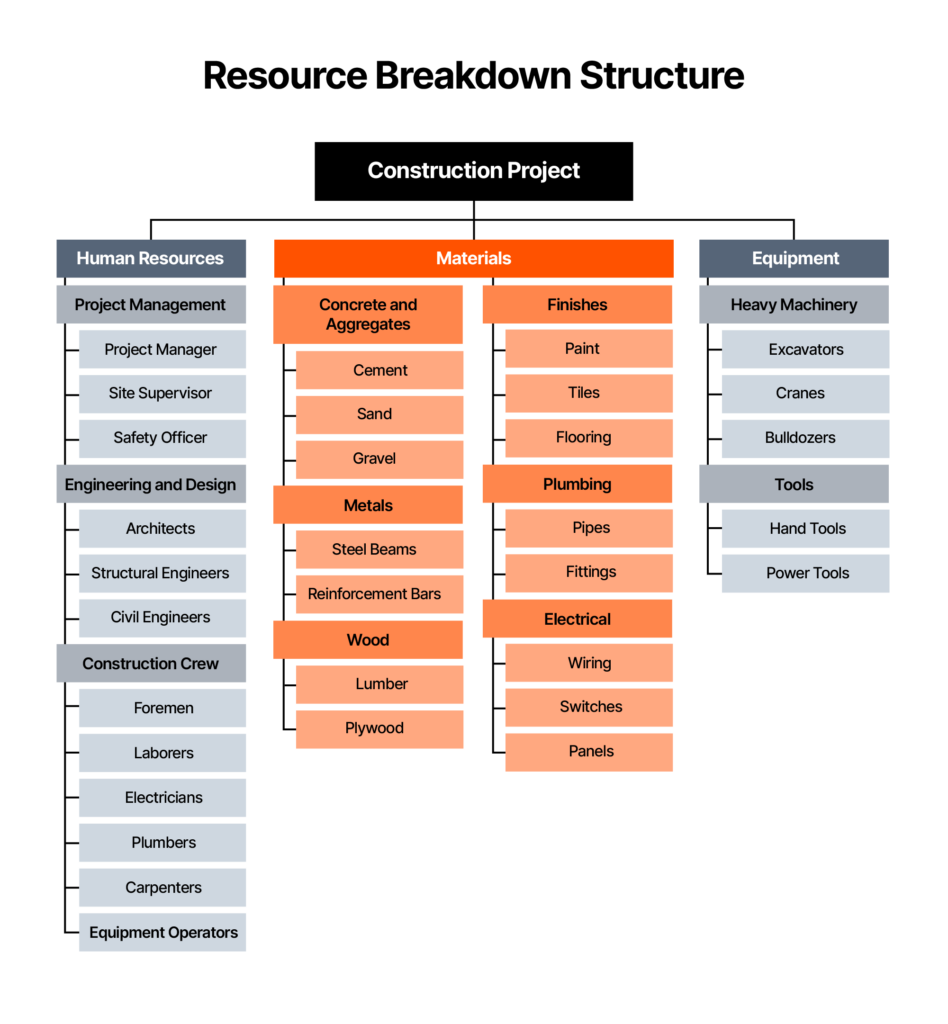
Work Breakdown Structure vs Resource Breakdown Structure
The work breakdown structure (WBS) details the tasks involved in completing a project, while the RBS itemizes the resources needed for each task. Together, the two breakdowns help managers accurately plan and execute schedules using the materials and equipment allocated to each task.
Having a WBS and RBS at hand allows PMs to quickly shift resources and change scheduled tasks as on-the-ground conditions and change orders necessitate reallocating workers and equipment.
Benefits of a Resource Breakdown Structure in Construction
An RBS offers a framework to visualize all needed project resources and structure the acquisition or distribution of resources to meet the project’s goals. Here are some of the main benefits of using an RBS.
Optimize Resource Usage
Managers can see all available and needed resources and adjust their distribution to the most urgent tasks — precursors to other parts of the project — to keep the schedule flow as smooth as possible and optimize time use. Teams can align construction sequencing with budgets and resource availability.
Accurately Schedule Workers
The RBS allows managers to assign skilled workers to priority tasks to better utilize the workforce to accomplish tasks efficiently and competently. Distributing employees to use their time and skillsets best minimizes downtime. Balancing the workload among personnel and within the timeline helps avoid overtaxing individuals, thus decreasing burnout.
Minimize Waste
Seeing all the variables in one place allows for more accurate ordering of materials and supplies, minimizing waste from overpurchasing. Labor resources can be optimized by seeing where to assign workers to keep the work flowing, not overburden any workers and avoid worker downtime.
Identify Resource Shortfalls
If specific equipment is unavailable in the company fleet, managers can consider renting or purchasing the right equipment for the project. If the needed skills are not available in sufficient quantities to accomplish the project, the company can consider upskilling current workers or hiring the right talent. If materials such as steel and bar joists have extended lead times, making them unavailable for scheduled tasks, managers can consider shifting the schedule or changing suppliers.
Mitigate risks
By identifying dependencies and possible bottlenecks in the workflow in the planning phase, PMs can map out how to move resources to reduce potential delays and scheduling conflicts. Scheduling workers so tasks are not rushed minimizes the risk of safety incidents or poor quality of work. Mapping when materials and tools are needed allows more accurate planning so that work can begin on schedule, decreasing the risk of wasted labor or delays.
Track Project Budget
The RBS helps correctly estimate the project's budget and cash flow needs in the planning phase. During construction, the RBS assists in tracking expenditures and adjusting the budget as changes occur in the project. The project’s cost breakdown schedule (CBS) is the primary tool for financial controls, but the cost details in the RBS help identify the detailed expenditures to enable adjustments to help meet budget goals.
Communicate Resource Visibility
Team members can use the RBS to visualize and communicate about resource constraints and collaborate to resolve issues and make necessary changes. Soliciting feedback from project team members can help refine the RBS to reflect time and material needs for different trades and assist in communicating needs and progress during the project.
Creating an Effective Construction RBS
The steps to creating an RBS are as follows.
Determine the Project Scope
Identify the project goals, deliverables, tasks and requirements to plan resource needs.
List Resources Required
Collaborate with project team members to determine the resources needed for the project, including labor, equipment, physical spaces, materials, supplies and time.
Categorize Resources
Divide needed resources into categories by type of resource (i.e., Human, material and equipment) or construction phase (i.e., design, preconstruction and construction)
Develop Framework
Organize the resources into a hierarchy with larger categories broken into subcategories, adding attributes like availability and time requirements
Allocate Resources to Tasks
Match resources to each task or work package in the WBS, providing details like skill requirements, quantities and schedule.
Validate and Review
Check completeness and review with the team to confirm consistency and accuracy.
Resource Categories and Characteristics
The RBS categories are usually organized by type, breaking resources into human, machinery/equipment, materials, supplies, facilities, financial, technological and any other resource category desired. It is also possible to structure the RBS by resource function, phase of construction, deliverable section of the project or by department for larger construction companies.
Here are resource type categories typically used in construction:
- Human resources (including skill levels)
- Heavy equipment and tools
- Materials and supplies
- Physical space and facilities
- Time and scheduling
- Cash flow and budget allocations
- Technology and software
- Information and communication
Modern construction teams need tablets and smartphones on-site to take advantage of software integrations that provide information for work tasks and specifications. Different technology tools may be required for surveying the site or design and engineering processes. Information as a resource is a category often overlooked, but teams need the correct information at the right time to implement the tasks and build to the specifications.
Tracking resource attributes, such as required skill level, cost per unit or availability windows, can help allocate resources and track direct costs and time. For instance, if a rental crane is needed for multiple tasks, the RBS can help schedule the tasks within a defined time window to minimize rental costs.
Explore data and trends for building materials prices.
Get the latest U.S. retail prices and view historical trends for common building materials.
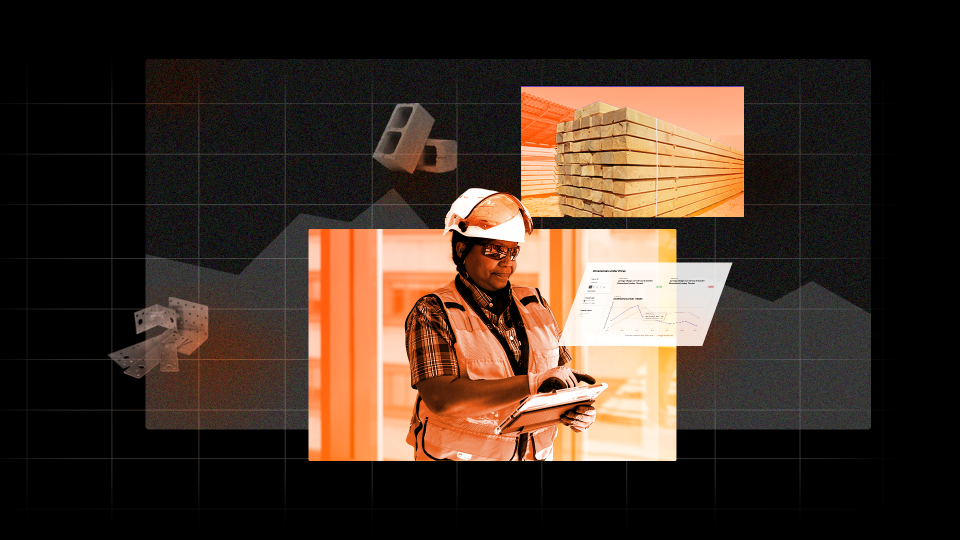
Resource Breakdown Structure Best Practices
To maximize the benefits and overcome the challenges of implementing an RBS, here are some best practices.
Align the RBS with Project Objectives
Start from the project objectives and make sure the RBS resource needs are associated with the goals, priorities and deliverables of the project.
Involve Stakeholders
Subcontractor leads, owner representatives and key in-house managers need to participate in creating and validating the RBS. Team members' expert input determines the accuracy of scheduling and resource allocation.
Establish Naming Conventions
Within the RBS, consistency in the names of resources and characteristics helps the team track resources, solve problems when conflicts arise, and avoid confusion and mistakes in interpreting the document. Consistent cost coding allows accurate budget oversight and
Integrate the RBS with Other PM Documents
The relationships between the RBS, WBS and CBS allow changes in one to be tracked into the other documents. Work blocks may change schedules and require reallotting equipment to different tasks, and changing material needs can impact cost tracking. The documents are interrelated and help different management teams to communicate.
Implement Construction Management Software
Project management platforms are invaluable in keeping the RBS updated and allowing stakeholders access to needed information. Training for team members can enable companies to fully use the RBS and bolster collaboration for successful project outcomes.
Continuously Monitor and Optimize
The RBS is a living document that can help address issues during planning and construction. Utilize the RBS to assist in quickly identifying where changes in the scope or problems on site require resource reallocation. The RBS can help control costs and optimize resource use to boost the company’s bottom line.
Use Visuals to Enhance Understanding
To help stakeholders understand and interpret the RBS, use color-coded charts to make resource planning visual in meetings and reports. Different chart formats can help individuals appreciate resource constraints and evaluate resource use. Construction software tools provide many reporting and dashboard options for tracking resources.
Using the RBS to Successfully Deliver Construction Projects
Incorporating an RBS into construction project planning enhances efficiency and effectiveness. By providing a detailed overview of all necessary resources, the RBS allows project managers to allocate resources knowledgeably, optimize schedules and reduce waste. The RBS can identify potential shortfalls, mitigate risks and boost clear communication among stakeholders.
The RBS, when integrated with other project management documents such as the WBS, offers a comprehensive framework to support dynamic resource management. Using an RBS helps companies optimize resource use for successful project delivery.
Was this article helpful?
Thank you for your submission.
0%
0%
You voted that this article was . Was this a mistake? If so, change your vote here.
Scroll less, learn more about construction.
Subscribe to The Blueprint, Procore’s construction newsletter, to get content from industry experts delivered straight to your inbox.
By clicking this button, you agree to our Privacy Notice and Terms of Service.
Categories:
Tags:
Written by
Julia Tell
45 articles
Julia Tell is a freelance writer covering education, construction, healthcare, and digital transformation. She holds a Ph.D. in Media & Communications and has written for publications including Business Insider, GoodRx, and EdSurge, as well as nonprofits, international businesses, and educational institutions.
View profileExplore more helpful resources
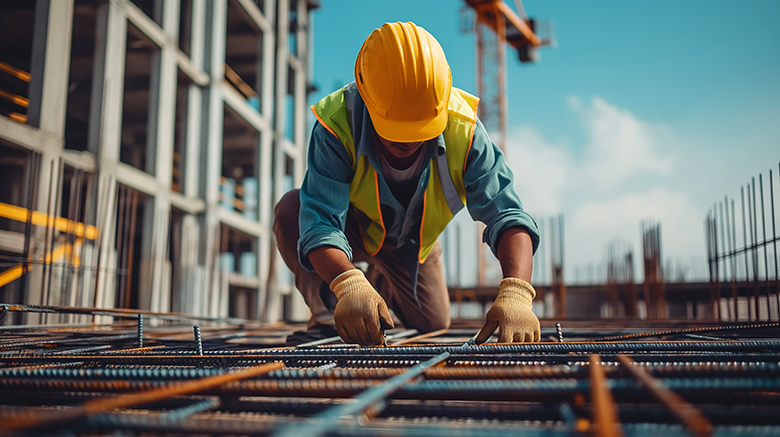
Mitigating the Impact of Tariffs in Construction
The construction industry faces constant financial uncertainty, and the 2025 escalation of global tariffsmandated by executive order drew attention to their potential impacts. While no crystal ball can tell exactly when...
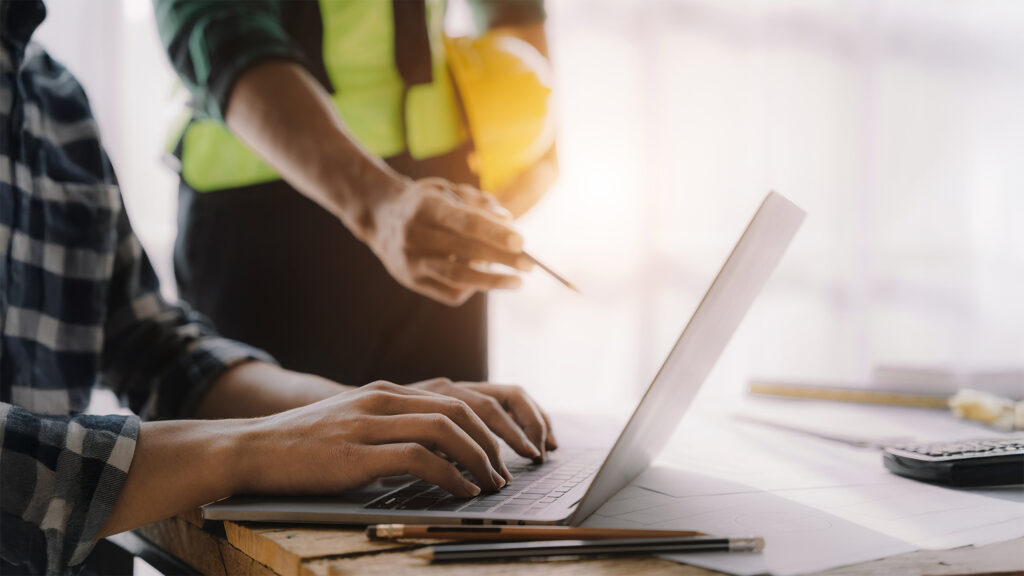
Using Construction Benchmarking for Better Project Outcomes
Successful construction teams consistently work toward getting better at what they do — producing better quality projects, reducing waste and delivering work on time and on budget. Construction benchmarking provides...
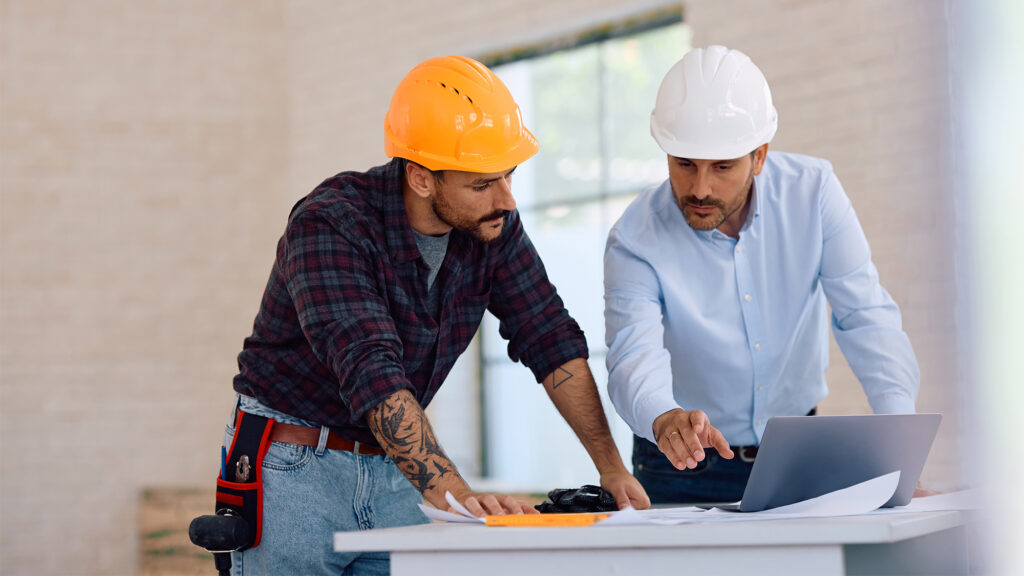
How to Understand and Use Architect’s Supplemental Instructions
Architect’s supplemental instructions, also known as ASI, offer a means of making small changes to the construction contract after it’s signed. The ASI is a document issued by the architect...
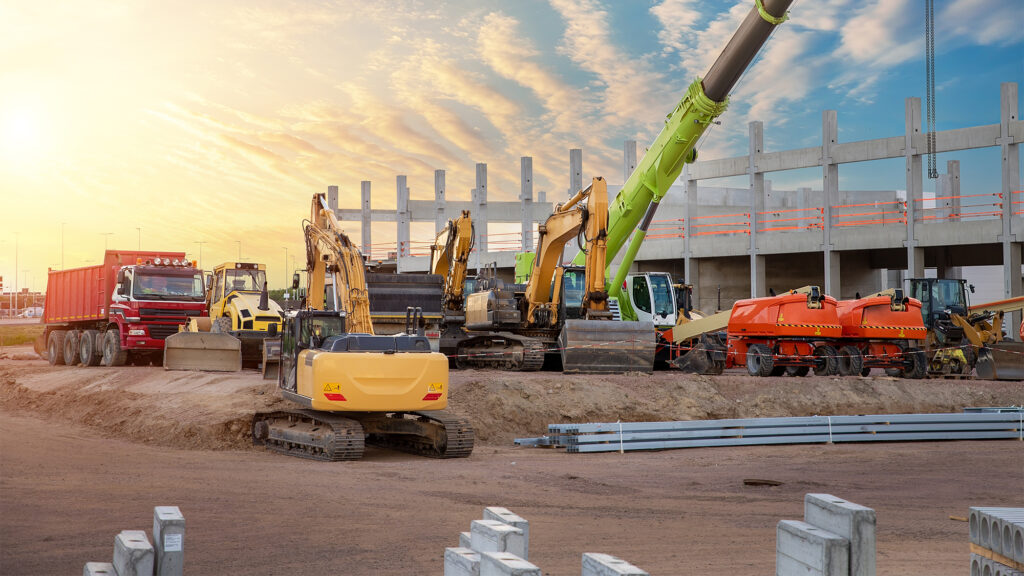
Improving Project Monitoring with Construction Quantity Tracking
Once a construction project is underway, builders need to closely monitor the project’s progress and make sure it’s staying on schedule and within budget. Quantity tracking helps construction leaders manage...