— 10 min read
Skyscraper Construction: Reaching New Heights
Last Updated Aug 13, 2024
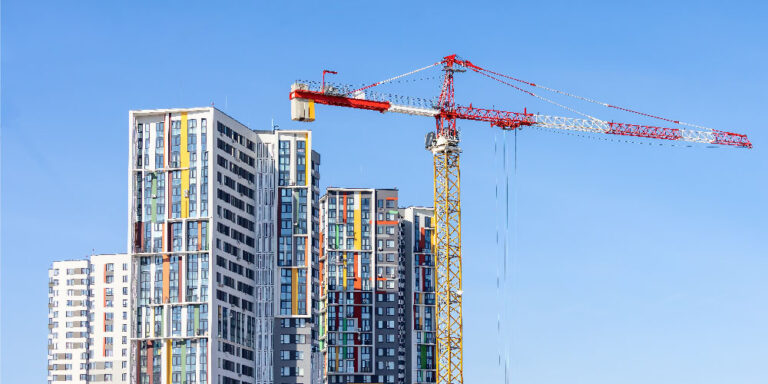
Since the first skyscraper was built in Chicago in the 1880s, most major cities have decorated their skylines with lines of these high-rise towers. The since-demolished Home Insurance Building’s construction broke the limits of what was thought possible at the time — and there's no sign of skyscraper construction slowing as populations continue to rise in urban areas, making the ability to construct them a unique but highly sought-after skillset for a general contractor (GC) or construction project team.
This article explores the challenges and unique components of skyscraper construction, including their meticulous preconstruction process, safety risks during the build and best practices for efficiently completing these modern marvels.
Table of contents
Planning for Skyscraper Construction
In many ways, skyscrapers are a clear-cut ideal of vertical construction — but they can be complicated to build and plan for.
There’s no set definition for skyscrapers, though the International Code Council defines a high-rise as any occupied building that scales more than 75 meters up into the air. Consensus on definitions for the minimum height of skyscrapers varies—some sources say there must be more than 100 meters, and others define these structures as taller than 150 meters.
Their sheer size makes the predevelopment phase of skyscrapers and high-rises complex and long, from costly site acquisition in densely packed areas to conducting a lengthy series of feasibility studies that make sure the built structure will be able to withstand wind and lightning, and that the soil beneath will be able to hold the massive building.
During preconstruction, a GC should expect many OAC meetings to work out pricing, especially since many of these buildings tend to be considered luxury spaces for offices or apartments, and designers or owners may want certain aesthetic features that are out of budget. There may be many rounds of pricing exercises to get to a consensus on moving forward with the build.
There may be special building permits for skyscrapers in the jurisdiction a GC is working in, so it's important to coordinate early and efficiently with authorities having jurisdiction (AHJs). Because the work will involve using a crane, the Occupational Safety and Health Administration (OSHA) will need to approve its use.
Less common but still important to consider is the role of the Federal Aviation Agency (FAA). If the building is in close proximity to an airport, it may need a special permit to intrude on the flying space above.
Another critical permit to obtain is a lane closure permit. Since these structures are often built in busy downtown centers, it can be a complicated process to close off roads for crane use or site deliveries. Failing to get approval for and properly schedule these closures can cause expensive delays to the project.
Challenges with Building Skyscrapers
Working at such heights has inherent risks, and the scale of a skyscraper can create obstacles to getting work done on time. The following suggests some of the many challenges a project may encounter as it enters the building phase.
Navigating Safety
Skyscrapers have historically been some of the deadliest projects to take part in, and falling hazards can mean death, but there are ways to minimize this risk and keep the entire team safe.
First, it’s important to establish a robust culture of safety from the start of the project. This means taking the time to demonstrate to foremen and crewmembers that it’s everyone’s job — not just safety engineer’s—to uphold safety standards. Make sure everyone knows they have stop-work authority, and that everyone is entitled to flag potential safety risks onsite.
Another big way to reduce safety risk is to keep the build indoors as much as possible. Strategically positioning cranes to reach every corner of the building, for example, is one method of keeping crews from having to work outside at great heights. Using prefabricated walls and roofing can also help keep installation short, reducing the amount of time a crew engages in high-risk work.
Per OSHA guidelines, guardrails and safety features are to be installed at each floor as the work progresses, but sometimes high-risk labor is unavoidable. Installing safety tie-ins at each level of the building can be helpful in making sure that any worker outside the building is safe from falling. Netting may also be useful in catching any falling equipment, so it doesn’t land on passersby below and cause an injury.
Finally, to fully prepare for risks, it’s important that the GC and other project leadership develop site safety plans that go above and beyond OSHA requirements, as ultimately it is their responsibility to keep their workers safe.
Scheduling and Coordination
High-rise buildings are massive, sometimes requiring even more intense workforce and material scheduling than other vertical construction projects.
Most material delivery will need to be just-in-time (JIT), though if budget allows and warehouse space is available nearby, it may be useful to rent for material storage, which can help house the large amounts of steel and prefabricated materials that will be needed.
It’s also important to schedule any road closures with the arrival of materials like concrete, or otherwise miss important deadlines for pouring it. Partnering with waste companies can sometimes off-load the responsibility of sorting and filtering garbage, and may also help with coordinating waste storage.
Since delays can ripple through a project, it’s critical to stay on top of workforce scheduling and monitoring, which can get complicated as the structure grows and crews are staggered across floors.
Hiring trusted, experienced foremen and workers can ease the risk of a potential slowdown, but project management teams must be skilled at scheduling their workforce to show up on time, and make sure their workers have all the materials and equipment available to successfully complete their tasks.
Structural and Geotechnical Issues
Feasibility studies play an important role in reducing risk of structural failure, but it’s still necessary to monitor this threat throughout the build, as it poses a danger to people not in both the building and its surrounding structures.
Skyscrapers are typically built by digging foundations deep into the earth, but placing a massive load of weight onto the wrong type of soil can destabilize the foundations of other buildings, which can result in lawsuits and catastrophes. It’s important to consider the structural integrity and age of these buildings as a project moves forward with its build.
Installing shoring walls is necessary to prevent collapse or structural failure and can manage the lateral loads in the ground to establish the excavation site. However, it will still be crucial to continue monitoring the impacts of the superstructure on the ground as the project moves forward.
Best Practices for Skyscraper Construction
As a massive example of vertical construction, building a skyscraper can have more intense issues than its shorter counterparts.
Keeping a few best practices in mind, however, may help a GC or project management team keep the work going smoothly, and get to handover as efficiently as possible.
Embrace and learn from failure.
There’s no surefire way to keep a project from going off the rails, and unintended obstacles are bound to show up on a large project such as a high-rise building. The best way to deal with a failed task or scheduling mishap is to embrace it with acceptance, working with the challenge to overcome it most smoothly.
While rework can pile up and become costly in terms of both time and money, doing something incorrectly can also often be the best way to learn how to do it correctly. Taking time to educate oneself or a crew on how to resolve an accidental problem can help foster a culture of learning and reduce the risk of these accidents happening in the future.
Communicate openly and directly.
Regular meetings for open, transparent communication are necessary for every phase of skyscraper construction, from OAC meetings to align expectations to toolbox talks and check-ins with onsite workers to address safety and work concerns.
Another part of communicating effectively is coordinating with the local community, which will be affected by both the build that will close roads and block walkways, and also by the future structure, which may add traffic, noise and even economic changes to the community. Holding monthly update meetings can mitigate disruptions and manage the expectations of people who may live or work around the high-rise.
Trust collaborators.
A sense of humility is required to build a skyscraper, even at the level of project management. Not every GC has the experience needed to work with such high amounts of concrete and materials, or the scheduling savvy to coordinate such a massive number of deliveries and workers.
Since it’s not always easy to find tradeworkers or other subcontractors with this background, either, it’s important to build a foundation of good teamwork by trusting crewmembers and foremen to do their jobs well, while monitoring their performances and giving feedback when it’s useful.
Bad teamwork can significantly derail a project, and failing to deliver the structure on time can have devastating consequences for a GC or construction company’s reputation—so it’s critical not to alienate collaborators during any phase of the process.
Stay connected.
It’s important to have systems that keep everyone informed of the work being done to properly manage a workforce across a tall, ever-growing high-rise building.
It’s hard to overstate the importance of keeping daily logs on any large-scale project, though some more traditional crews can be hesitant to adopt them. Having access to a record of what crews have gotten done — and what they still have yet to finish — is a critical part of monitoring the build, and is necessary to keep stakeholders updated on progress.
Using construction management software can be helpful in organizing these logs, as well as keeping up with the many other documents and logs that will be recorded throughout the project.
Software can also increase visibility on important information: For example, inputting punch lists and then pinning these items to a set of drawings can help a GC monitor what tasks still need to be done. Uploading photos of an area that needs work completed can save a contractor time in locating that place, and they can focus on assigning and scheduling this task.
Innovations in Skyscraper Construction
In the 20th century, taking on a skyscraper building project was a dangerous, expensive, behemoth project. While these towers still require significant workforce power and a lot of dedicated planning, some inventions and innovations have made the task more manageable for the skilled GC and leadership team.
One of the best ways skyscraper construction has innovated starts well before breaking ground. BIM technology has made it possible to plan and share the design of an entire building ahead of time.
Some firms have even started implementing both augmented reality (AR) and virtual reality (VR) with BIM to give designers and architects better visibility into the finished product long before it’s even started.
Another important innovation in skyscraper construction is the development of taller, more agile tower cranes that are built for operation in dense areas, and can increasingly lift heavier loads. It’s also possible, but expensive, to use an aerial crane for tall buildings.
Prefabricated materials have also represented an important development in the construction of high-rise buildings, as they present a durable, made-to-install alternative to building the skyscraper brick-by-brick.
In recent years, a lot of emphasis has been placed on making skyscrapers more energy efficient, with some designs utilizing natural light, ventilation, and even outdoor green spaces to reduce reliance on air conditioning systems.
For example, the Hearst Tower, which was completed in New York in 2006, has a steel frame that is 85% made up of recycled materials, and utilizes a water sculpture that also helps to maintain a cooler temperature within the building.
Going Higher: Skyscraper Construction of the Future
Skyscraper construction will likely continue to evolve, and it’s impossible to predict the heights these new structure will reach, or the technology that may be implemented in or outside their walls.
Ultimately, the future of skyscraper construction lies in the intersection of traditional best practices and cutting-edge innovations. For now, contractors can aim to master this blended approach to building these massive towers; those who do will be well-equipped to take on the challenges and opportunities of building the next generation of urban skylines.
Was this article helpful?
Thank you for your submission.
0%
0%
You voted that this article was . Was this a mistake? If so, change your vote here.
Scroll less, learn more about construction.
Subscribe to The Blueprint, Procore’s construction newsletter, to get content from industry experts delivered straight to your inbox.
By clicking this button, you agree to our Privacy Notice and Terms of Service.
Categories:
Tags:
Written by
Ezra Teshome
Ezra Teshome is a Senior Strategic Product Consultant for Procore Technologies. Their career in construction has empowered me to build my skills in managing teams and organizing construction labor, construction financial management (contracted budget changes, billing approval, bid leveling during precon, etc.), and project schedule management, including updating progress and expanding detailed activities for clients and subcontractors.
View profileTrey Strange
27 articles
Trey Strange is a Peabody and Emmy-Award winning writer and producer based in Brooklyn, NY. Throughout his career, Trey has worked for the Huffington Post, Houston Chronicle, Out Magazine, Brooklyn Eagle, CNBC, INTO, and New York Magazine's Bedford + Bowery. He received his Masters in Journalism and Middle East studies from New York University, and Bachelors in the same subjects from the University of Houston.
View profileExplore more helpful resources
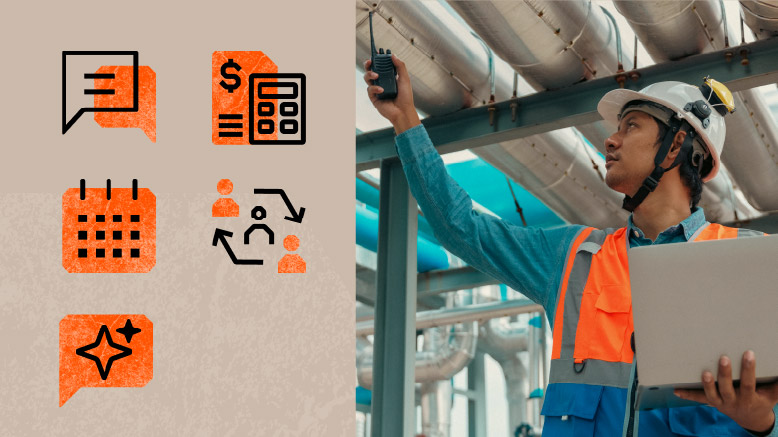
The Top 5 Skills of High-Performing MEP Professionals
Compared to standard MEP professionals, high-performing MEP pros don’t just get the job done. They also combine five key skills around technology, scheduling, finances, communications and flexibility into a proactive approach...
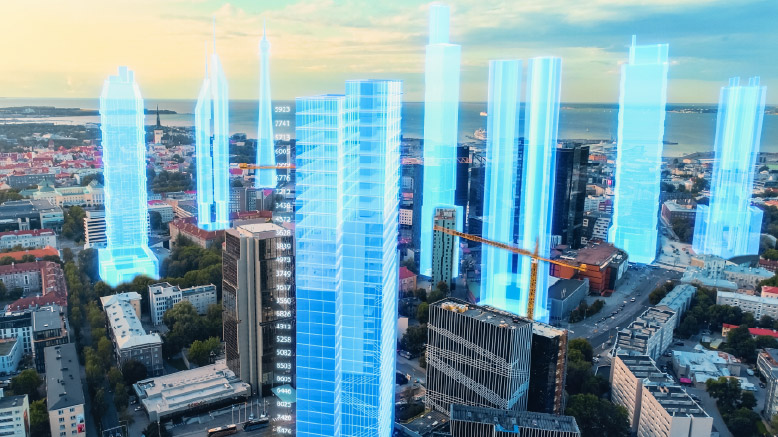
How AI is Reshaping Decision-Making and Project Resilience in Civil Construction
In construction, the ability to make informed, timely decisions is paramount. No longer is it sufficient to rely solely on historical data or reactive problem-solving. Enter artificial intelligence (AI), a...
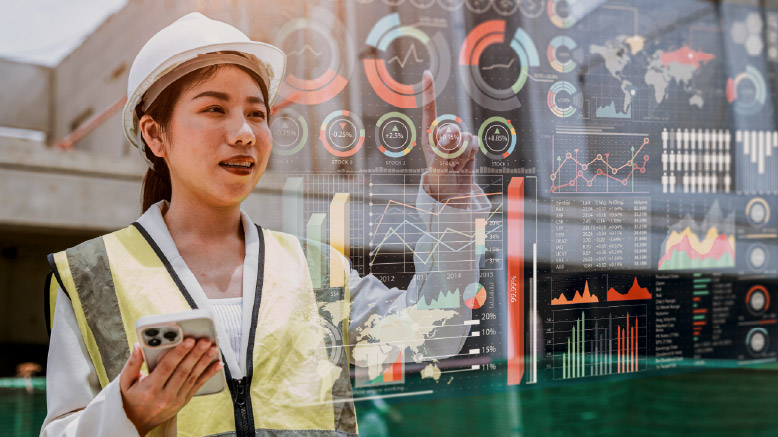
How AI is Redefining Efficiency & Safety in Civil Construction
As demand for new and modernized infrastructure surges, the civil construction industry faces an imperative to deliver projects with unprecedented speed, precision and safety. Emerging at the forefront of this...
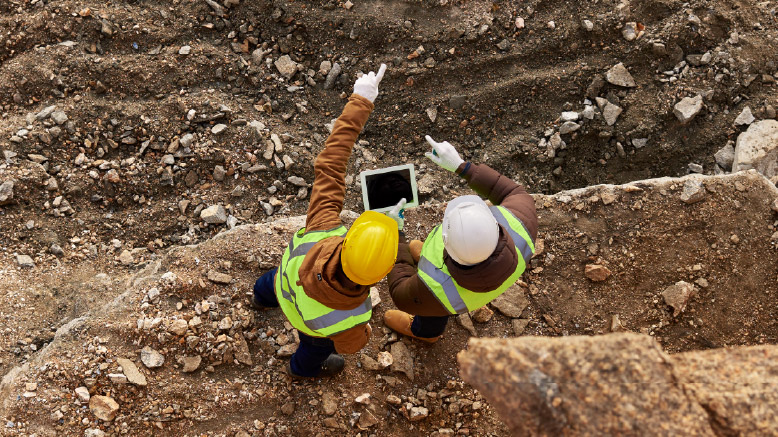
Building a Culture of True Tech Readiness in Civil Construction
While significant investments are pouring into revitalizing the nation’s infrastructure, the true capacity to capitalize on this opportunity hinges on more than just funding — it relies on a fundamental...
Free Tools
Calculators
Use our calculators to estimate the cost of construction materials for your next project.
Templates
Find a template to help you with your construction project tasks.
Material Price Tracker
Get the latest U.S. retail prices and view historical trends for common building materials.
Glossary
Explore key terms and phrases used in the industry.