— 8 min read
Subway Construction: Building a Unique Underground World
Last Updated Apr 29, 2024
Last Updated Apr 29, 2024
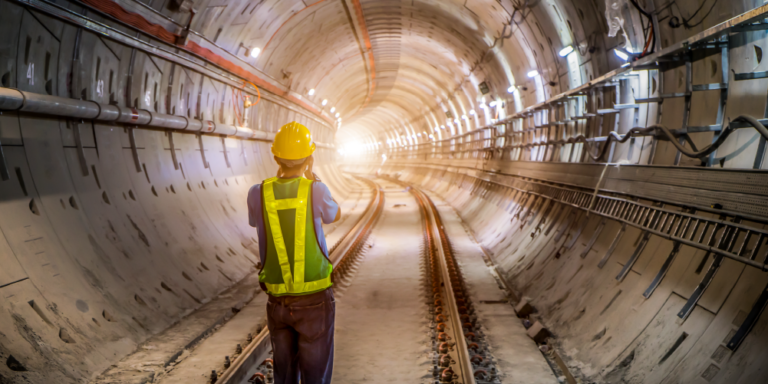
Most major cities in the world serve the public with large transportation systems, whether they’re above-ground light rails or trains bulleting through underground tunnels. As more people move to urban areas, subway systems will likely have to be updated — or even built outright in some places — which means they can be a lucrative area of business for a skilled general contractor (GC).
But subways are complex, sprawling, subterranean systems, and performing construction work on them can be a daunting task. In particular, the nature of subways gives them unique challenges in terms of cost, workforce, safety and ability to complete the job.
This article explores the process of subway construction work, the specialized and costly equipment necessary to do the job and the unique safety and jobsite considerations of working below street — and sometimes sea — level.
Table of contents
Stages of subway construction
Working on an existing subway system — extending a track or building a new line, for example — can mean that the worksite is miles long and costs millions of dollars. Many aspects of subway construction mirror the phases of project management in other types of construction, but in general, the challenges at each step tend to be as large and complicated as the jobsites themselves.
The following lists some of the challenges a GC could come up against in the different stages of construction.
Planning and Design
Subway projects tend to be billion-dollar, drawn-out affairs. Since they’re typically funded by governments and through public-private partnerships, the process before even securing the bid can be years, even decades, long.
For example, the most recent phase of the NYC Second Ave Subway project secured 3.4 billion from the Federal Transit Administration and began soliciting bids in 2023, but the Metropolitan Transit Authority (MTA), which operates the subway system, has been working on the master plan for that design since the early 2000s.
Preconstruction
Getting ready to start the build requires obtaining permits from relevant authorities having jurisdictions (AHJs), hiring a competent workforce, creating safety and material delivery plans and meeting with stakeholders.
However, the sheer number of stakeholders involved in a subway project can be overwhelming. In addition to regulation from the Department of Transportation, often the local operating authority — the MTA in New York City, for example — has a heavy hand not just in preconstruction meetings but also in their own approval processes.
They may employ their own environmental engineers, project managers and specialists to work with the contractor’s own team and approve the details of each preconstruction decision.
This structure, although designed to maintain quality and oversight on projects using taxpayer funds, can feel slow and unwieldy to a contractor not used to getting so much external approval.
Since the worksite is so big, the GC should plan to hire a large workforce. They’ll need standard tradespersons — like electricians, mechanics and plumbers — but they’ll also need to work with the local tunneling and dirt excavation trade, like the Sandhogs in New York City. It’s also a good idea to work with local fire rescue teams to generate an evacuation plan in case of emergency, and to train crewmembers on the procedure regularly.
Finally, since subways tend to be under streets, the GC must work with the city to determine what lanes or streets will need to be closed, and for how long.
Construction
Before even starting on the actual subway tunnel, the GC and crew must build a launch box. The launch box is a designated area used for assembling and launching specialized equipment — in this case, the tunnel-boring machine (TBM). It also includes facilities for maintenance, storage of materials, and logistical support, and will remain after the build is complete.
Expert Insight: Working with a Tunnel-Boring Machine (TBM)
A Tunnel Boring Machine (TBM) is a specialized piece of equipment that few GCs get a chance to use. One of their particularities is that they’re generally custom-made to order for a specific project, and are bought, not rented. They often need to be ordered years in advance, which is part of what makes the planning phase of these projects so long. They can cost up to $150 million.
The TBM cuts into the soil and rock using a massive rotating head. On its backside, a series of conveyor belts pull excavated material to the surface, leaving behind a relatively finished tunnel. As it moves, a crew of about a dozen workers places anchor bolts. At the same time, concrete is pumped from the surface level to the site, and the machine lays slabs as it moves, which the rails and tracks will be placed onto.
A TBM is a relatively new invention, and the method more traditionally used to excavate tunnels is called cut and cover. This method involves digging a trench, building out the interior of the tunnel to serve a subway or train, and then backfilling the trench with soil—effectively covering it, so that the surface can go back to normal.
In general, a TBM is faster than using cut and cover methods, and it’s less disruptive to the surrounding environment since only the space for the launch box needs to be dug out.
To make a launch box, workers blast and drill into the street and lower it into the hole. An important part of this process is utility relocation. Water mains, electrical lines, phone cables and gas pipes may all need to be re-routed during this phase.
Once the relocations are finished, actual tunnel excavation begins, starting from the launch box. The TBM is assembled and deployed, carving out the tunnel according to the project's specifications.
While building a tunnel requires a lot of earthwork, a subway system is a unique feat of electrical and mechanical engineering. Other aspects of construction include laying tracks, installing switches, signals, cars and rails — including the third rail, the live conductor that moves the train.
Above ground, ventilation buildings will have to be installed at regular intervals for both the safety of future passengers and crewmembers.
Materials — concrete, bars for both the tunnels and tracks, for example — are likely to arrive as just-in-time deliveries, and because of the huge amounts needed, a GC may need to source from several companies. These materials — as well as any other equipment — will need to be dropped down into the tunnel with a crane.
Managing waste during the construction phase can also present challenges. A system will need to be rigged to lift debris out of the tunnels as needed, and be sorted into a dumpster nearby. Since subways tend to be in large metropolitan cities, space for waste could be limited, and the nearest landfill could be far away.
Project Closeout
When subway construction is near complete, it enters the commissioning phase, during which the transit authority conducts the final checks and approvals. This phase also involves meticulous inspections to ensure that all signals, switches and installations are functioning correctly. Finally, it will include test runs with rail cars to ensure that the system is ready for public use.
Typically, the opening of the subway will involve an inaugural train ride, which signifies the end of years-long planning and construction efforts.
Additional Challenges of Subway Construction
It’s hard to overstate the safety risks of asking a crew of hundreds to tunnel underground. Site superintendents should always know how many people are inside the tunnel at any given time, which may require additional documentation and logging processes that some crewmembers aren’t used to.
Jobsite security
In addition to safety, security measures might be needed to protect the integrity of the tunnels once they are built. Security cameras might be useful at every tunnel access point, and security officers may need to be stationed. Measures like these aren’t just about keeping out potential trespassers; they’re about ensuring that every worker knows they’re operating in a safe, secure environment.
Working underground
Working underground also requires air and dust monitoring, and may require extra PPE like respirators to keep workers from being exposed to harmful pollutants.
But some subways don’t just run underground — they also run underwater. Dewatering pumps operate constantly in areas with high groundwater levels or where tunnels are below the water table. These pumps are designed to remove excess water from the excavation site, keeping the work area dry, and they will remain in place after construction ends to maintain the system.
The Bottom Line on Subway Construction
There’s a reason that the New York Subway System began construction in 1900 and wasn’t truly close to the bustling apparatus we know today until the F line opened in 1989: Subways are long projects, built and renovated in many stages — and are never truly finished.
Since they’re ever-growing and ever-needed, subways are also an incredible source of profit for the adept contractor. Though building a subway line is a challenging feat of literal earth-shaking proportions, this work is also necessary to the function of society, and a monumental gift to a city’s current and future residents.
Was this article helpful?
Thank you for your submission.
0%
0%
You voted that this article was . Was this a mistake? If so, change your vote here.
Scroll less, learn more about construction.
Subscribe to The Blueprint, Procore’s construction newsletter, to get content from industry experts delivered straight to your inbox.
By clicking this button, you agree to our Privacy Notice and Terms of Service.
Categories:
Tags:
Written by
Jacob Kunken
21 articles
Jake Kunken currently works as Solutions Engineer for Procore's Heavy Civil division. He brings 14 years of experience working in various construction roles in New York and Colorado, including laborer, assistant carpenter, carpenter, assistant superintendent, superintendent, construction manager, safety manager, and project manager. Jake also spent time in EHS as an environmental engineer for Skanska. He’s worked on more than 40 commercial projects from ground-up, to heavy civil, hospital work, and tenant improvement. Jake studied Ecological Technology Design at the University of Maryland.
View profileTrey Strange
26 articles
Trey Strange is a Peabody and Emmy-Award winning writer and producer based in Brooklyn, NY. Throughout his career, Trey has worked for the Huffington Post, Houston Chronicle, Out Magazine, Brooklyn Eagle, CNBC, INTO, and New York Magazine's Bedford + Bowery. He received his Masters in Journalism and Middle East studies from New York University, and Bachelors in the same subjects from the University of Houston.
View profileExplore more helpful resources
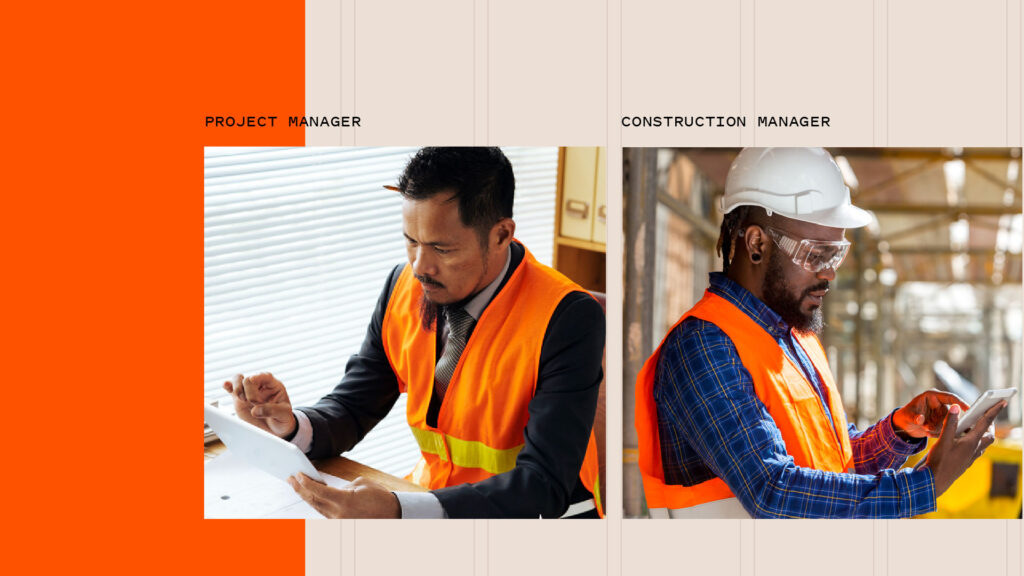
Construction Manager vs. Project Manager: Comparing Leadership Roles
Skillful oversight of construction projects allows companies to deliver to owners on time and within budget. Construction managers (CMs) and project managers (PMs) provide the necessary supervision to keep projects...
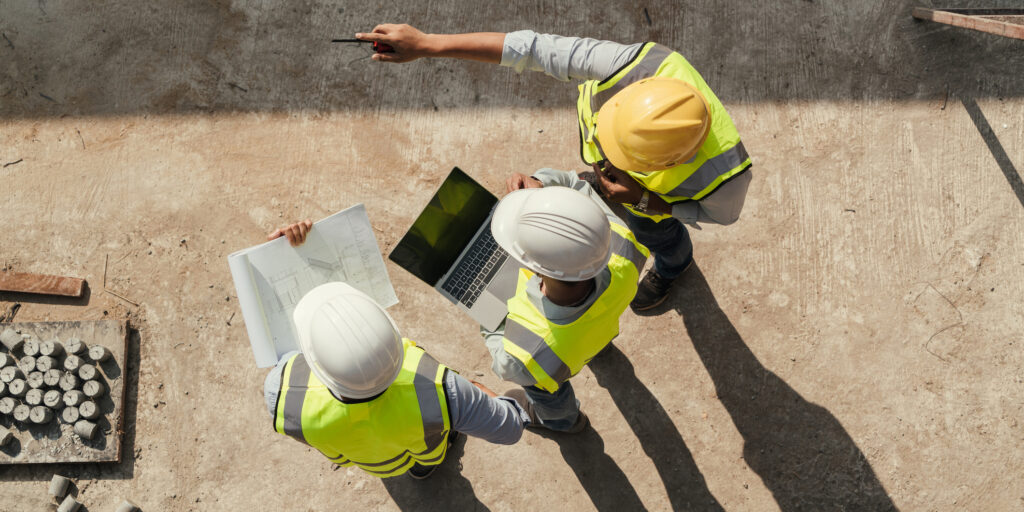
Holistic Construction Project Oversight: Aligning Relationships & Processes
All parts of a construction project are connected. A delayed approval for a change order can impact a project’s timeline, required overtime and, ultimately, the budget. Communication with an owner...
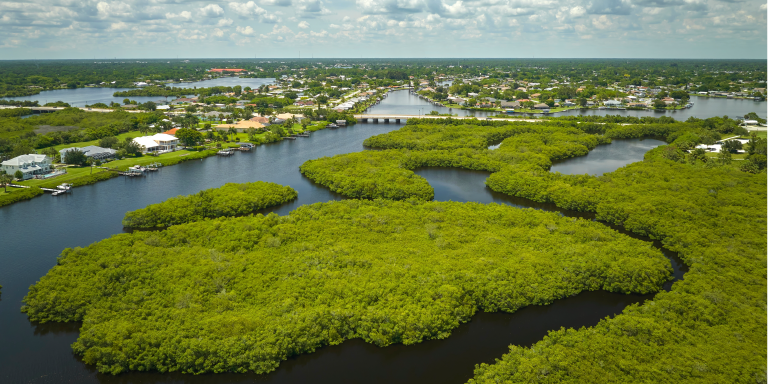
Navigating the Challenges of Industrial Construction in Wetland Areas
Industrial construction in Florida presents unique challenges and opportunities for construction companies, especially because over 31% of the state is wetlands. As the demand for logistics and distribution facilities grows,...
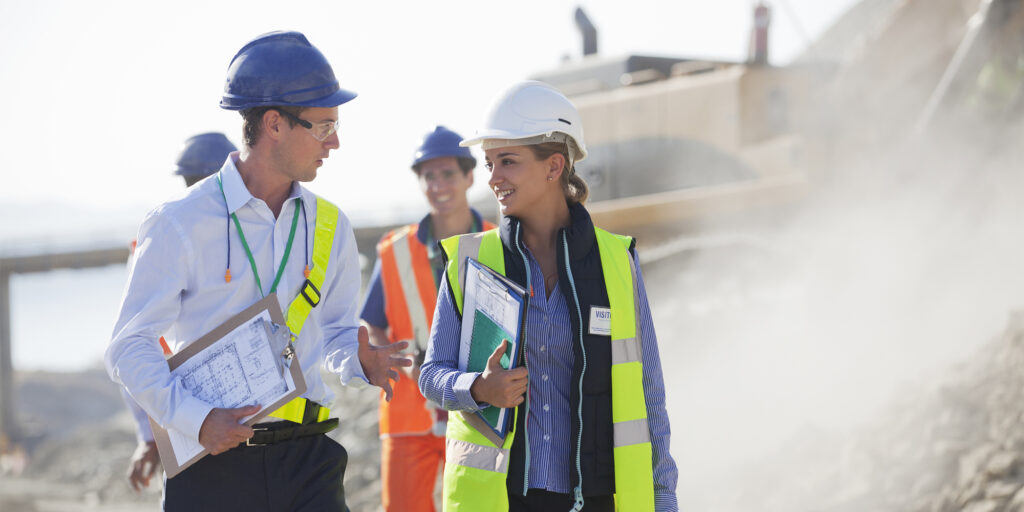
Building Together: How Integrated Project Delivery Creates Shared Value
As technology and innovative processes continue to evolve the construction industry, the need for openness and collaboration among teams and stakeholders has increased significantly. Traditional project delivery methods, such as...