— 6 min read
Trade Stacking: Preventing & Managing Trade Clashes
Last Updated Apr 2, 2025
Last Updated Apr 2, 2025
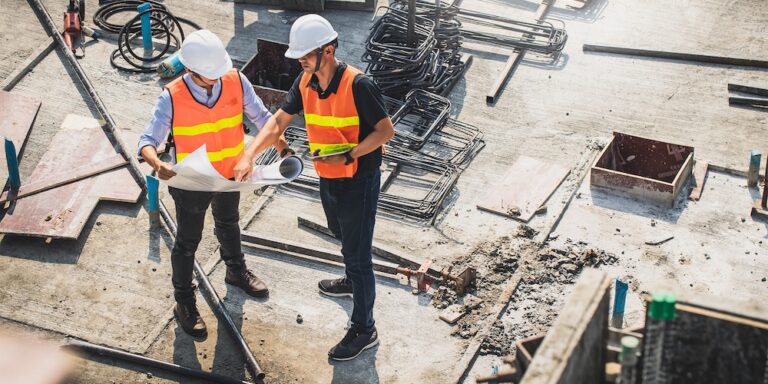
When construction projects fall behind schedule, adding more workers may seem like a logical solution. However, when multiple trades are forced to operate in the same confined space simultaneously, the result is often counterproductive. This phenomenon, known as trade stacking, leads to congestion, inefficiencies, safety hazards and quality issues that can seriously slow progress.
Effective construction management requires identifying the causes of trade stacking and implementing strategies to mitigate its risks while maintaining productivity. This article examines the causes and effects of trade stacking and how to manage communication and resources to avoid it and keep projects on track.
Table of contents
Causes of Trade Stacking
Trade stacking often arises due to a combination of poor planning, scheduling conflicts and unforeseen changes. Inadequate project planning and scheduling can lead to overlapping work, as multiple trades are assigned to the same area without proper sequencing.
Delays in preceding activities can further exacerbate trade stacking, as trades may be forced to work simultaneously to compensate for lost time. Additionally, insufficient workforce or resource allocation can create bottlenecks and force different teams to work in close quarters.
Miscommunication among trades and management also plays a significant role: Without clear coordination, workers may unknowingly schedule tasks that interfere with one another.
Notably, changes in project scope or design — especially last-minute modifications —can disrupt the original work schedule, forcing multiple trades into the same space at once.
Risks and Challenges of Trade Stacking
Despite the desire to accelerate project completion, trade stacking often has the opposite effect. Some potential negative impacts include lower productivity, issues with quality and even additional delays.
Reduced Productivity
Overcrowding creates distractions, inefficiencies and logistical challenges, making it difficult for workers to complete tasks efficiently.
When multiple trades compete for the same space, movement is restricted, tools and materials become harder to access, and workers are forced to navigate around one another. This slows down individual tasks and disrupts the overall workflow, leading to delays across the entire project.
Quality Issues
When trades are forced to work in limited space, workmanship may suffer. This leaves room for increased errors, expensive rework and even compromised structural integrity.
The lack of proper workspace can prevent workers from using their tools effectively, which can cause rushed installations and result in defects that require later corrections. This can be especially problematic in precision-dependent trades such as electrical wiring, plumbing or finishing work.
A Domino Effect of Project Delays
Poor coordination often results in workflow bottlenecks, leading to unexpected delays rather than improved speed. Instead of accelerating progress, excessive workers in one area create a chaotic environment where tasks take longer than planned. This congestion can lead to dependencies that push back other activities, delaying project milestones and increasing costs.
Safety Hazards
Overlapping trades increase the likelihood of workplace accidents, including trips, falls and collisions due to congested working environments. With multiple teams working in close proximity, the risk of dropping tools, improper material storage and miscommunication about active machinery operations grows. This doesn't just endanger workers: It can also lead to legal and financial liabilities for the project management team.
Strained Relationships
When schedules aren't managed effectively, tension can flare quickly. Plus, a strained and overloaded workforce working in tight quarters can worsen the problem and leave workers feeling fatigued. If project participants aren't in alignment and feeling stressed, the likelihood of even more disputes and delays increases.
Strategies to Avoid Trade Stacking
To prevent trade stacking, project managers can implement several key strategies.
Effective Project Planning and Scheduling
Effective planning requires a well-structured work sequence to ensure that only necessary trades are active in a given area at any time. Utilizing modern project management software helps create detailed schedules, track progress and make real-time adjustments as needed.
Implementing phased work schedules, where different trades operate in designated areas at different times, prevents congestion and enhances efficiency. Regular progress evaluations are also important for identifying potential schedule conflicts before they escalate, allowing for proactive adjustments to keep the project on track.
Enhanced Communication and Coordination
Communication is key in every aspect of construction, and it's essential for preventing scheduling conflicts and allowing for smooth project execution.
Regular meetings with stakeholders — including general contractors, subcontractors, and site managers — help align schedules and expectations. Establishing clear communication protocols, such as digital scheduling tools and on-site coordination meetings, makes sure all trades understand their work timelines and spatial limitations.
Visual planning tools like Gantt charts or digital whiteboards can also help enhance transparency and minimize conflicts. Encouraging open dialogue between trades allows teams to identify and resolve scheduling issues before they lead to significant delays.
Resource Management and Optimization
Effective resource management and optimization ensure that workforce and materials are allocated efficiently, preventing overcrowding and allowing trades to perform tasks without interference. Staggering work shifts or implementing rotating schedules helps distribute trades across different areas of the site, reducing congestion and improving productivity.
Regular site assessments are essential for evaluating resources and making necessary adjustments to prevent bottlenecks. Additionally, leveraging data analytics can provide valuable insights into resource utilization, enabling proactive decision-making to keep the project running smoothly.
Scheduling Flexibility and Contingency Planning
Scheduling flexibility and contingency planning are keys for maintaining project efficiency and preventing trade stacking.
Incorporating buffer time into the schedule allows for unexpected delays without forcing multiple trades into the same space. Developing contingency plans ensures that trades can be reallocated if conflicts arise, minimizing disruptions. Predictive analytics and real-time monitoring tools can help anticipate potential delays, allowing for proactive workflow adjustments.
Pro Tip
Focus on Flexibility
Maintaining a flexible workforce allows teams to adapt to shifting project needs without causing slowdowns, ensuring steady progress and driving on-time completion.
Implementing Lean Construction Principles
Implementing lean construction principles enhances efficiency by minimizing waste and optimizing workflow. Value stream mapping, also known as material and information flow mapping, helps identify inefficiencies and eliminate unnecessary steps in the construction process.
Just-in-time (JIT) delivery methods help materials arrive only when needed, reducing on-site clutter and potential obstructions. Pull planning techniques, which schedule tasks based on actual work progress rather than rigid timelines, create a more adaptive and responsive workflow.
Stay updated on what’s happening in construction.
Subscribe to Blueprint, Procore’s free construction newsletter, to get content from industry experts delivered straight to your inbox.
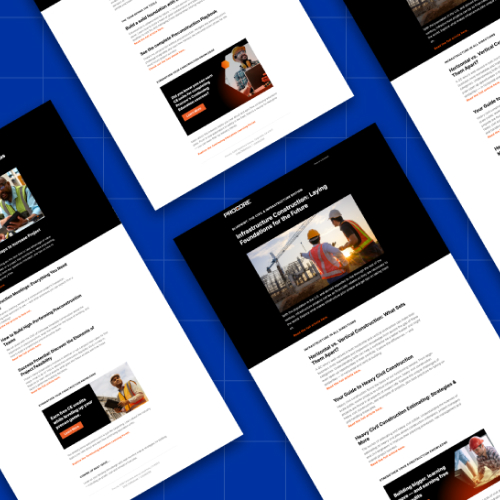
Prevent Trade Stacking With Proper Planning
Trade stacking is a common, yet avoidable, challenge in construction. Project managers can prevent overcrowding and workflow disruptions by implementing effective project planning, utilizing modern scheduling tools and promoting clear and constant communication among stakeholders.
Staggered work schedules, real-time progress tracking and proactive contingency planning help make sure trades operate efficiently without interfering with one another. Additionally, resource optimization and lean construction principles can help minimize congestion and maintain steady progress so that projects cross the finish line on time and within budget.
Was this article helpful?
Thank you for your submission.
0%
0%
You voted that this article was . Was this a mistake? If so, change your vote here.
Scroll less, learn more about construction.
Subscribe to The Blueprint, Procore’s construction newsletter, to get content from industry experts delivered straight to your inbox.
By clicking this button, you agree to our Privacy Notice and Terms of Service.
Categories:
Tags:
Written by
Caitlin Sweeney
Caitlin Sweeney is a freelance writer specializing in construction, design, and travel. Her writing has been featured in Building Design + Construction, The American Institute of Architects, ArchDaily, and AIA Contract Documents. Caitlin holds degrees in Public Relations and Psychology from Virginia Tech. In her spare time, she writes fiction, practices French and Russian, and travels as often as she can around the world. She lives in Virginia with her two pets, Pippin and Merry.
View profileExplore more helpful resources

Preconstruction Partnerships: How Safety Pros Can Collaborate with Estimating & Proposal Teams
Construction leaders and safety professionals are developing a strong understanding of how safety programs positively impact project outcomes. When safety is woven into every aspect of operations from pre-construction to...
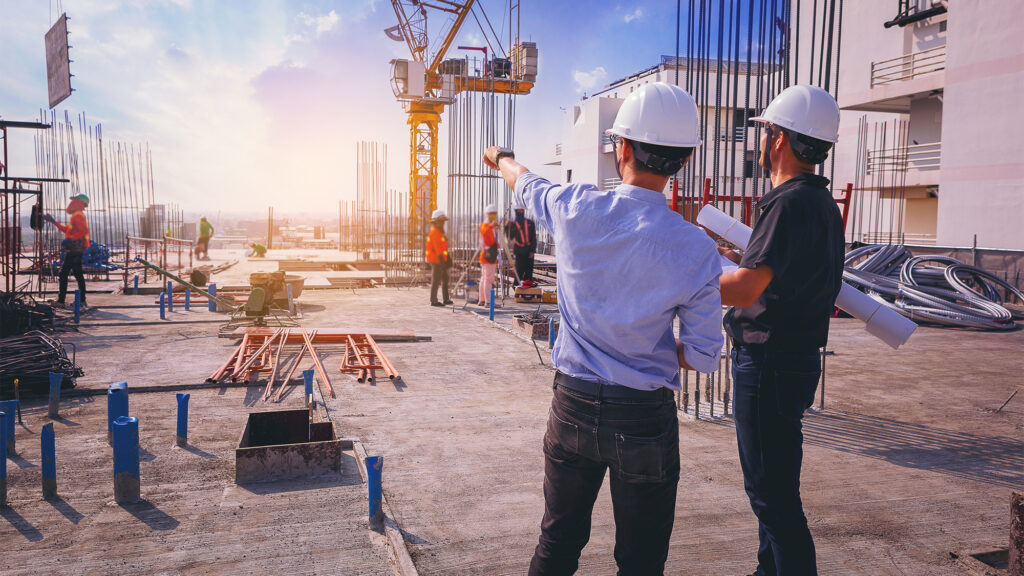
Construction Business Development: Tracking and Winning the Right Opportunities
Construction business development isn’t just a response to deadlines: It’s a long-term strategy rooted in focus, visibility and timing. Delays, funding gaps and market pressure have made it harder to...
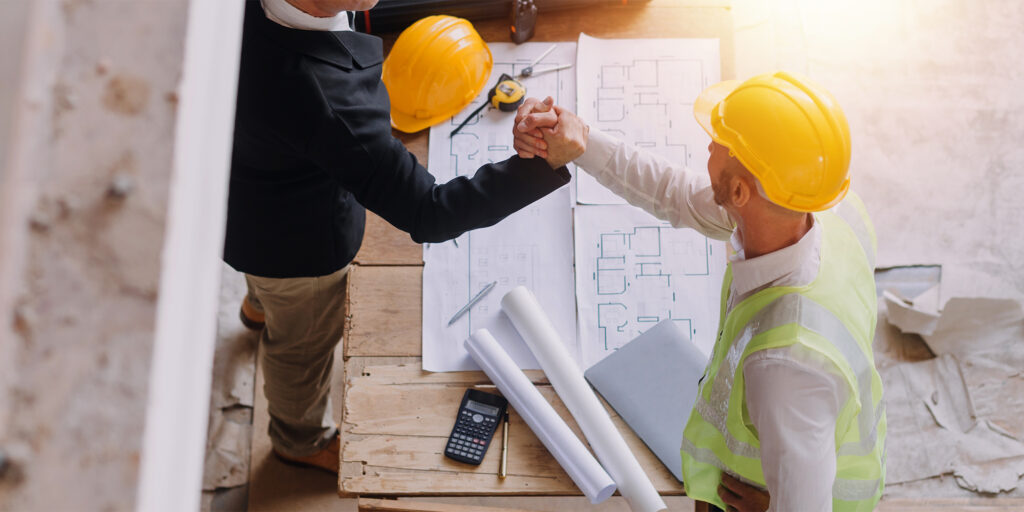
Qualifications-Based Selection: Prioritizing Expertise over Initial Cost
For large or complex construction projects, owners and public agencies often use qualifications-based selection (QBS) to prioritize experience and capability over merely selecting the lowest bid. QBS involves owners choosing...
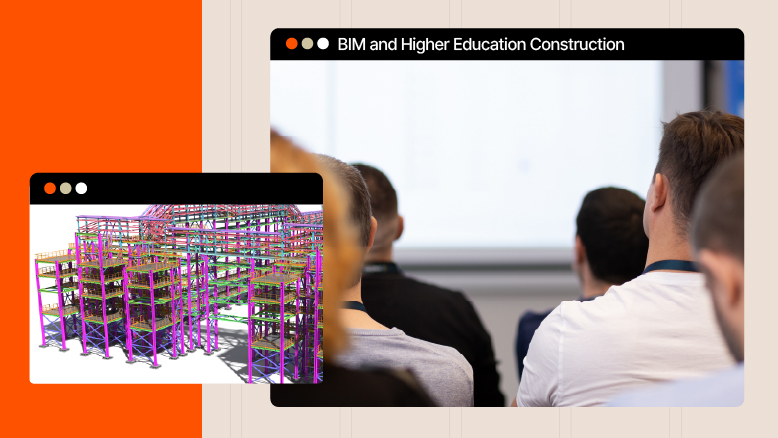
Using BIM in Higher Education Construction
As the construction industry changes, higher education institutions have started to implement building information modeling (BIM) at a rapid pace. If architecture, engineering and construction (AEC) companies want to work...