— 7 min read
Wood Frame Construction: Techniques, Benefits & Challenges
Last Updated Aug 9, 2024
Last Updated Aug 9, 2024
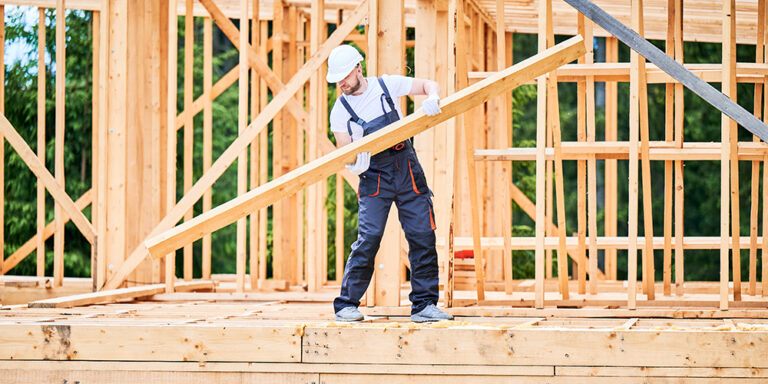
Wood-framed structures can be found almost everywhere. If you are in North America, there’s a good chance you are in a wood-framed structure right now, as most single-family homes in the U.S. and Canada are built that way.
Wood framing is a construction method that uses wood to create the framework of a building. The framing involves assembling a skeleton structure of vertical and horizontal wooden components that support the building's floors, walls and roof.
In this article, we’ll explore the basics of wood frame construction, including the advantages and disadvantages of using this popular framing material.
Table of contents
Wood Framing: Key Components
Wood framing is popular for both residential and light commercial construction because it’s generally priced lower than its framing counterparts, steel and concrete. It’s also versatile and easy to work with. Lumber can be cut, shaped and joined together with basic tools, making it great for both small and large projects. Wood is also a renewable resource when it comes from responsibly managed forests, making it a more sustainable choice.
Key components of framing include:
Studs
Vertical wood members used in walls
Joists
Horizontal wood members that support floors and ceilings
Rafters
Sloped wood members that support the roof structure
Sills
Horizontal and treated wood members that lay directly on the foundation, and provide a base for the wall framing
Headers
Horizontal wood members placed above door and window openings to support the weight from above
Plates
Horizontal wood members at the top and bottom of walls — the bottom is called the sole plate or bottom plate, and the top is called the top plate
Sheathing
Panels (often plywood or oriented strand board) attached to the exterior of the framing to provide structural stability and a base for exterior finishes
Treated Lumber vs. Untreated Lumber
Untreated lumber is best suited for interior and dry environments where natural appearance and ease of handling are preferred. Treated lumber, on the other hand, is chemically processed to resist environmental factors, making it ideal for outdoor and moisture-prone applications.
It is important to know when to use treated lumber instead of untreated lumber by knowing the specific environmental conditions and weather patterns in the area.
Untreated Lumber
Untreated lumber is more cost-effective and generally used in dry, enclosed spaces where exposure to moisture and pests is minimal. For interior applications, it is commonly used for framing interior walls, ceiling joists, roof rafters, interior partitions and non-load-bearing walls.
In above-grade construction, untreated lumber is used for floor joists, studs for interior walls, attic framing and interior support structures.
Treated Lumber
Treated lumber is commonly required in building codes for several specific applications to ensure durability and resistance to rot, moisture and pests. Treated lumber is generally more costly than untreated, and used for exterior walls, porch and deck framing, and structural posts and beams that are exposed to the elements.
Additionally, treated lumber is necessary for foundation posts or piers, retaining wall framing, and landscaping structures that touch the soil because it protects the wood from decay and insect infestations that are common in these situations.
Fire-retardant treated lumber is commonly used in commercial buildings where additional fire protection is necessary to meet building codes and safety standards.
Explore data and trends for building materials prices.
Get the latest U.S. retail prices and view historical trends for common building materials.
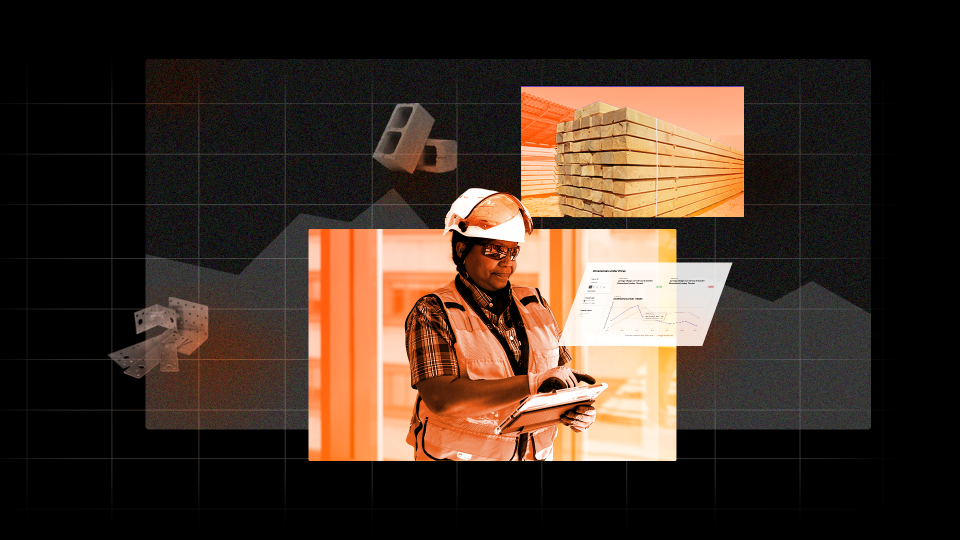
Challenges With Wood Framing
Even though lumber is one most popular materials for framing buildings, it does come with challenges that tradespeople and contractors should be mindful of.
Poor Lumber Quality
While managed forests make wood sustainable, lumber from younger trees, also referred to as “new-growth lumber,” tends to be less dense and lighter than older trees. The lower density level can lead to shrinkage when drying, and younger trees are often weaker than the mature wood cells found in older trees.
Moisture & Rot
Water management is an essential part of the framing process, especially with exterior walls. If moisture isn’t mitigated properly, the integrity of the wood is compromised, leading to rot that may cause structural damage down the line.
Older buildings with balloon-framed walls rarely see rot. With more openings and gaps in the wall, air circulation helps walls stay dry and the gaps allow water to escape. Additionally, treated lumber is ideal for areas where wood comes into contact with moisture. This includes wood in contact with concrete, such as sill plates, as well as framing in basements or crawl spaces. It's also essential in areas prone to flooding or high humidity to prevent rot and decay.
Termites
Preventing the onslaught of termite damage is important to the longevity of a building. As the pests feed and tunnel through the wood, the damage can be devastating to a structure leading to costly repairs. There are a few ways to minimize wood from pest infestations.
Installing Pest Control Systems
Pest control systems can be installed during new construction or remodeling to help prevent infestations. Some systems can be installed inside the walls.
Elevating Siding From the Ground
Ensure that the exterior siding sits several inches above the ground to make it harder for termites to build tunnels from the soil to the siding.
Using Termite Shields
Install termite shields, which are metal flashings that block termites from climbing further if they manage to build tunnels.
Waste Management
Worksites are often spattered with piles of scrap lumber. These unused materials are often due to excess inventory, poor organization, and a lack of communication between the crew. It often costs extra for storage and transportation of the lumber, or if left out, good lumber to warp and bow in the weather.
In order to cut down on this waste, many general contractors implement just-in-time (JIT) deliveries. JIT delivery involves scheduling and procuring materials to be delivered onsite as close to their installation in the build as possible.
While it takes careful planning and coordination with suppliers and subcontractors, JIT can help ensure timely delivery of materials and cuts down on wasted lumber and unnecessary costs. Keep in mind, the types of projects JIT is suitable for may vary, and JIT does require a well-coordinated supply chain.
In my time working in construction, the amount of waste on jobsites always stood out. When I worked as an estimator for a home builder, we meticulously calculated the exact quantities of materials needed for each project.
However, once the materials arrived on site, they often ended up in large, disorganized piles, with field workers using their own methods. This disconnect between the office and the field led to inefficiencies and significant amounts of scrap lumber.
To address this issue, we improved communication between estimators and field supervisors and implemented just-in-time ordering.
By ordering materials in smaller batches timed to arrive as needed, we reduced the amount of lumber sitting out in the weather, which could lead to warping and bowing, and minimized the risk of theft.
These changes helped cut down on waste, optimized the use of materials and ultimately improved the quality of our projects.
Ben Ashburn
Staff Trainer & Program Manager
Procore Technologies
Solutions and Innovations
As the construction industry evolves, innovative solutions are applied to traditional wood framing methods to address various challenges and enhance overall efficiency.
From the use of engineered lumber to prefabricated building techniques, these advancements are improving the structural integrity and sustainability of wood-framed structures, optimizing project timelines and reducing waste.
Engineered Lumber
Engineered lumber is a type of wood product that is manufactured by combining wood fibers, chips or shavings to create a composite material that is straighter, stronger and more consistent than traditional lumber. Unlike conventional lumber, which can suffer from warping and bowing due to the use of younger-growth trees, engineered lumber provides greater reliability and structural integrity. Engineered lumber is ideal for floor joists, roof rafters and when especially straight pieces are needed.
Prefabricated Buildings
Prefabricated buildings are structured in a controlled factory environment, often using engineered lumber, then assembled at the construction site.
Advantages of Prefabricated Buildings
- Prefabricated buildings are constructed more quickly due to simultaneous construction processes, where components are manufactured off-site while site preparation is ongoing.
- The controlled environment of factories where prefab components are made eliminates weather-related delays and reduces risks of material theft or damage.
- Efficiency and quality control are enhanced in a factory setting, leading to fewer errors, less waste, and faster on-site construction.
- Prefabrication requires reduced labor hours because of increased accuracy and speed in manufacturing, which speeds up the construction process.
Lumber: A Cornerstone of Construction
As a cornerstone of North American construction, wood framing is likely here to stay. Although it’s not without challenges, the versatility, reliability and cost-effectiveness of the method makes it a great choice for many residential and light commercial buildings.
Moreover, the sustainable management of forests ensures that wood remains a resource that the construction industry can depend on now and in the future.
Was this article helpful?
Thank you for your submission.
100%
0%
You voted that this article was . Was this a mistake? If so, change your vote here.
Scroll less, learn more about construction.
Subscribe to The Blueprint, Procore’s construction newsletter, to get content from industry experts delivered straight to your inbox.
By clicking this button, you agree to our Privacy Notice and Terms of Service.
Categories:
Tags:
Written by
Ben Ashburn
20 articles
Ben Ashburn is a Senior Construction Education Trainer at Procore. After a successful career as a construction estimator — working his way up from estimating manager to senior estimator — Ben has spent the most recent part of his career in construction sharing his skills with other as a construction educator. Ben has an extensive background in construction education: He has been an assistant professor in the Department of Construction Science at Texas A&M, and lectured about estimating, scheduling, management, and other related construction topics at Murray State University. He has been a construction training and learning development partner with Procore since 2019.
View profileMegan Duncan
Megan Duncan is an award-winning journalist based in Hannibal, Missouri. Her work has been featured on Muddy River News, Hannibal Courier-Post, The Whig, Hannibal Magazine, Q Magazine and Her View from Home. She has won two Best of Press Awards including first place from the Illinois Press Association for Localized National Story and third place from the Missouri Associated Press for best humor column. She holds a Bachelor of Arts in Communication from Quincy University.
View profileExplore more helpful resources
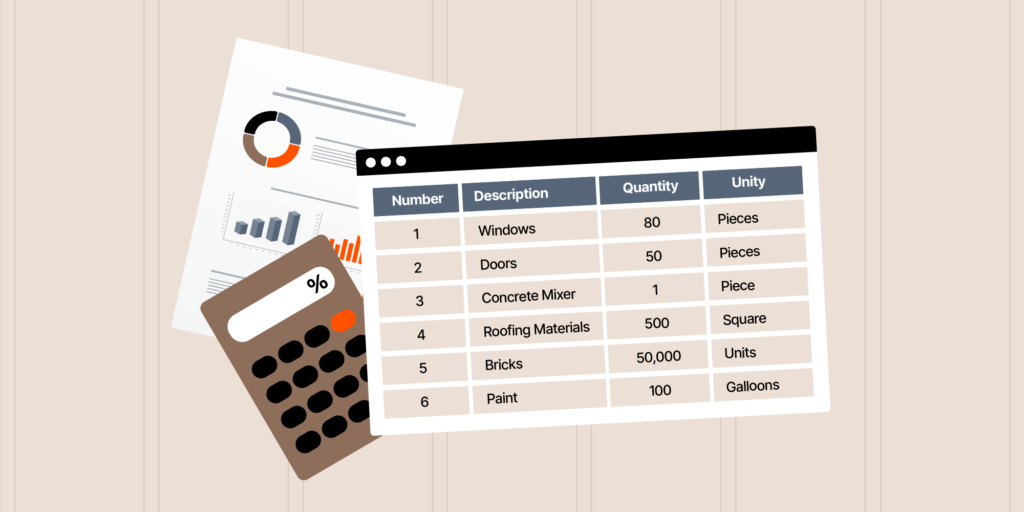
Key Benefits of a Construction Procurement Log (With Free Template)
By the time everything is purchased for a construction project, it represents not just a lot of money. It also represents a lot of energy from the teams involved. Getting...
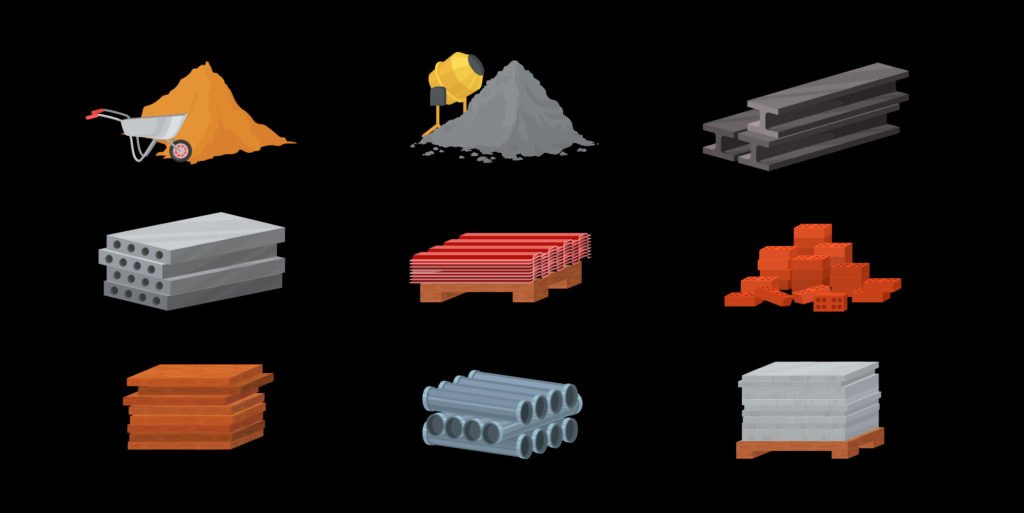
Material Management in Construction: A Project Manager’s Guide
Construction materials represent one of the key components for pulling off successful projects, and also one of the biggest expenses contractors face. Optimally managed materials procurement, storage and installation can...
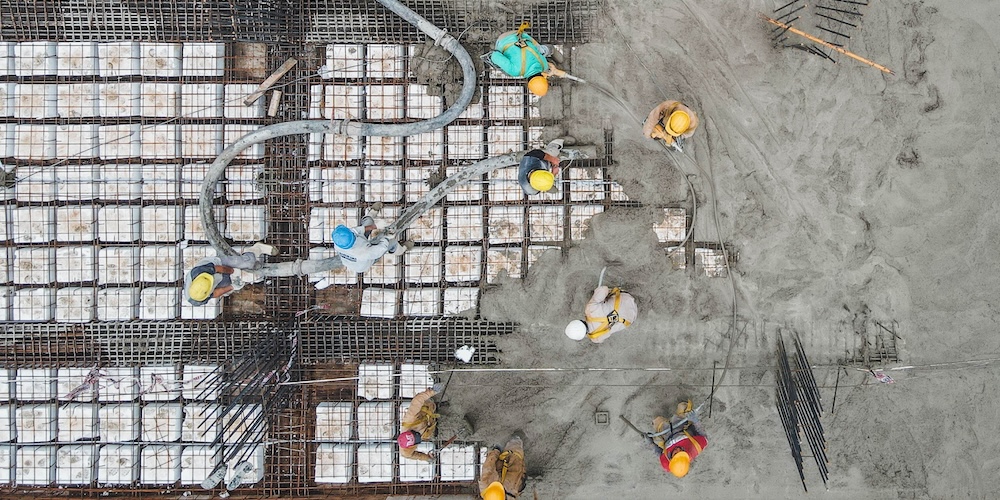
Mastering Construction Resource Management: Strategies for Success
Completing construction projects successfully requires the careful management of various resources: labor, materials, equipment, money, time and information. Since these resources are finite, allocating them wisely is crucial for minimizing...
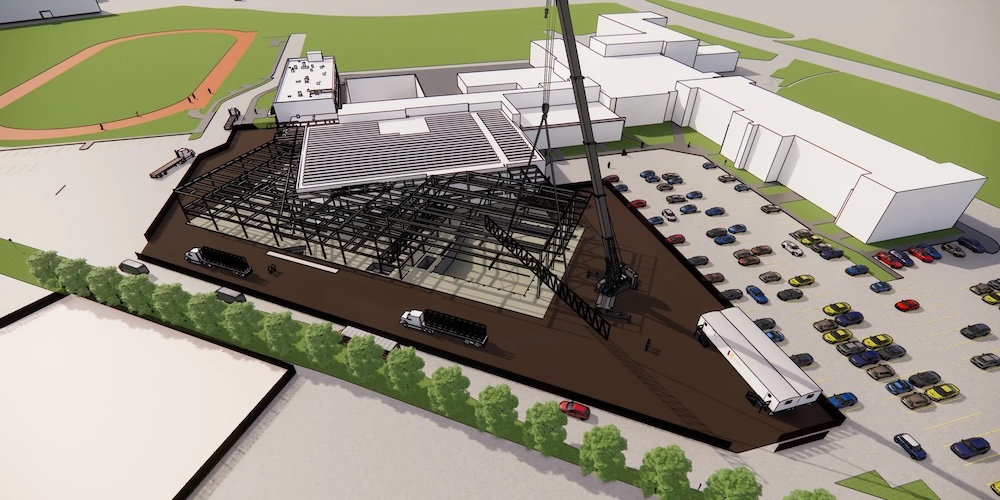
Optimizing Material Logistics & Procurement: Insights from a Sports Facility Project
As an assistant project manager on the Cadigan Wellness Complex Project at Boston College High School, managing material procurement and logistics is one of my primary responsibilities. In addition to...