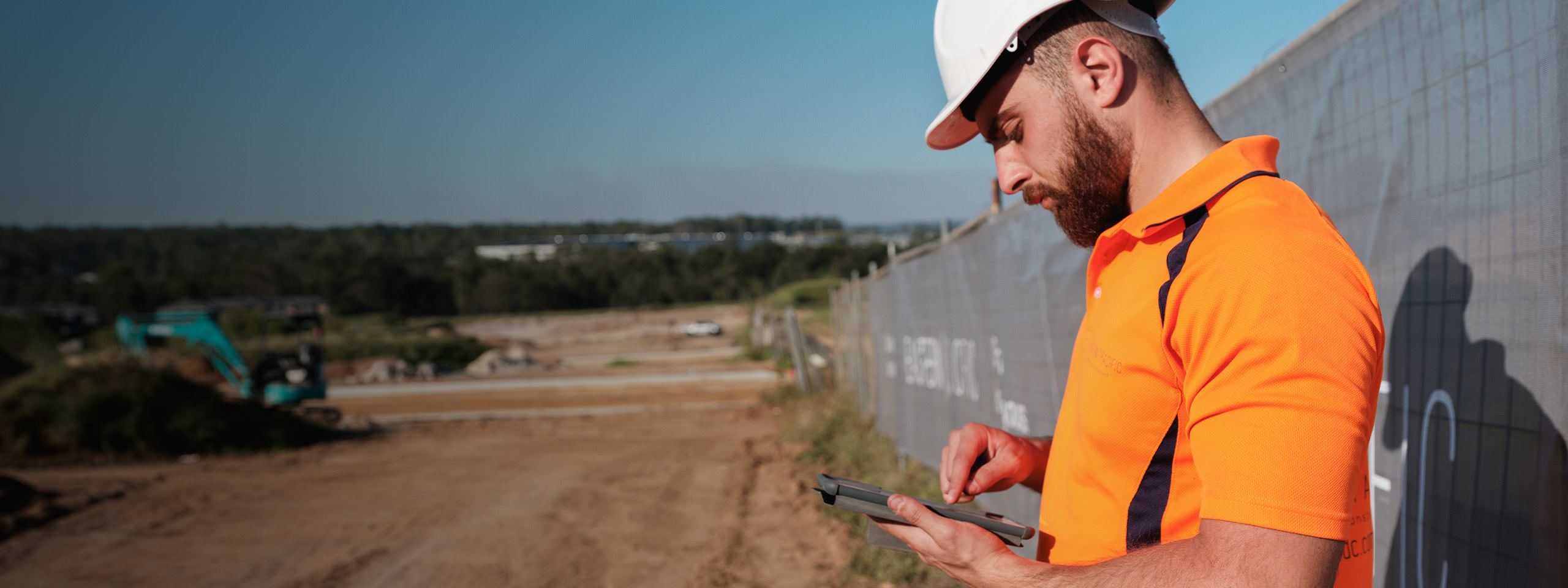
Article
Solve Technical Risk Management Problems Fast
Improve your construction projects in ANZ by learning to identify, assess, and manage technical risks effectively.
Want to learn more? We’re here to help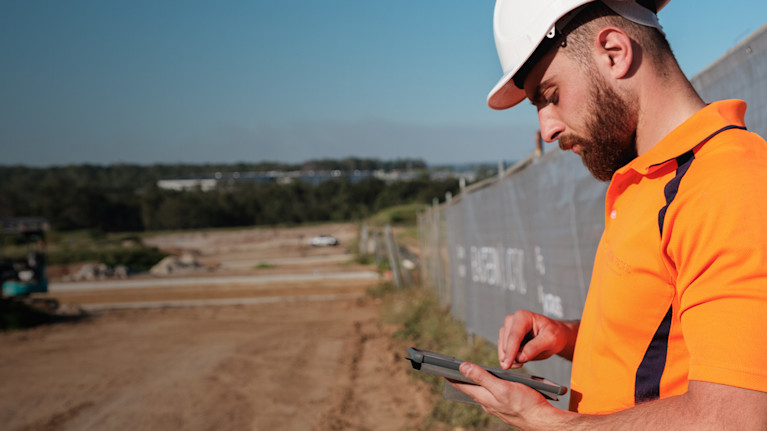
Risk surrounds head contractors and project managers at every step of the construction process—from the financial risks of payment disputes to the operational risks of documentation errors to the safety risks posed to on-site workers. With technical risks, the level of performance takes the impact.
Technical risk manifests in many ways—incomplete plans, fluid project scopes, or resource uncertainty. Each profoundly impacts project success, budgetary implications, health & safety concerns, as well as the performance requirement.
In 2023, construction companies in Australia and New Zealand are dealing with specific challenges, such as: New technologies like AI and Blockchain, with their technical requirements, unstable supply chains, both locally and globally, changing rules and regulations that impact risk level and shortage of workers across the industry
But there's a silver lining—proactive risk management.
Technical risk management as a strategic approach promotes safety and ensures higher-quality output and increased efficiency. By delving deep into the nuances of identifying, assessing, and continuously monitoring technical risks, construction firms can pivot to better project outcomes.
This article blog will shed light on these challenges and introduce the role of platforms like Procore in facilitating seamless risk mitigation. Dive in to arm your business with the knowledge and tools to fortify against looming technical risks.
Chapter 1
What are Technical Risks in Project Management?
In the realm of project management, the term "technical risks" refers to any factors that might hinder the successful completion of a project according to the customer's specifications. They’re more pervasive than other financial or operational risks because of technology's increasing role throughout the project lifecycle.
Technical risks are present across industries like aerospace, software, and construction, so it’s essential that you quickly identify and manage them.
For head contractors and project managers in construction, here are some common instances of technical risk:
Incorrect plans, designs, and documentation: A project built on flawed blueprints is like a house of cards. It can lead to wasted resources, extended timelines, and project failure. For instance, an incorrect design in construction could result in a structurally unsound building, posing severe health and safety threats.
Uncertainty surrounding resources and materials: Recent events have demonstrated the fragile nature of the construction materials supply chain and skilled labour markets. A sudden shortage of critical materials or key trades can cause costs to skyrocket, jeopardising project timelines and budgets in jeopardy.
Changes in project scope and requirements: Quick changes in project needs can come from new stakeholder requests or building laws changes. These changes can cause delays, increase costs, and create unexpected safety issues that teams must address.
In essence, project managers and head contractors must predict, recognise, and mitigate technical risks before they derail project success.
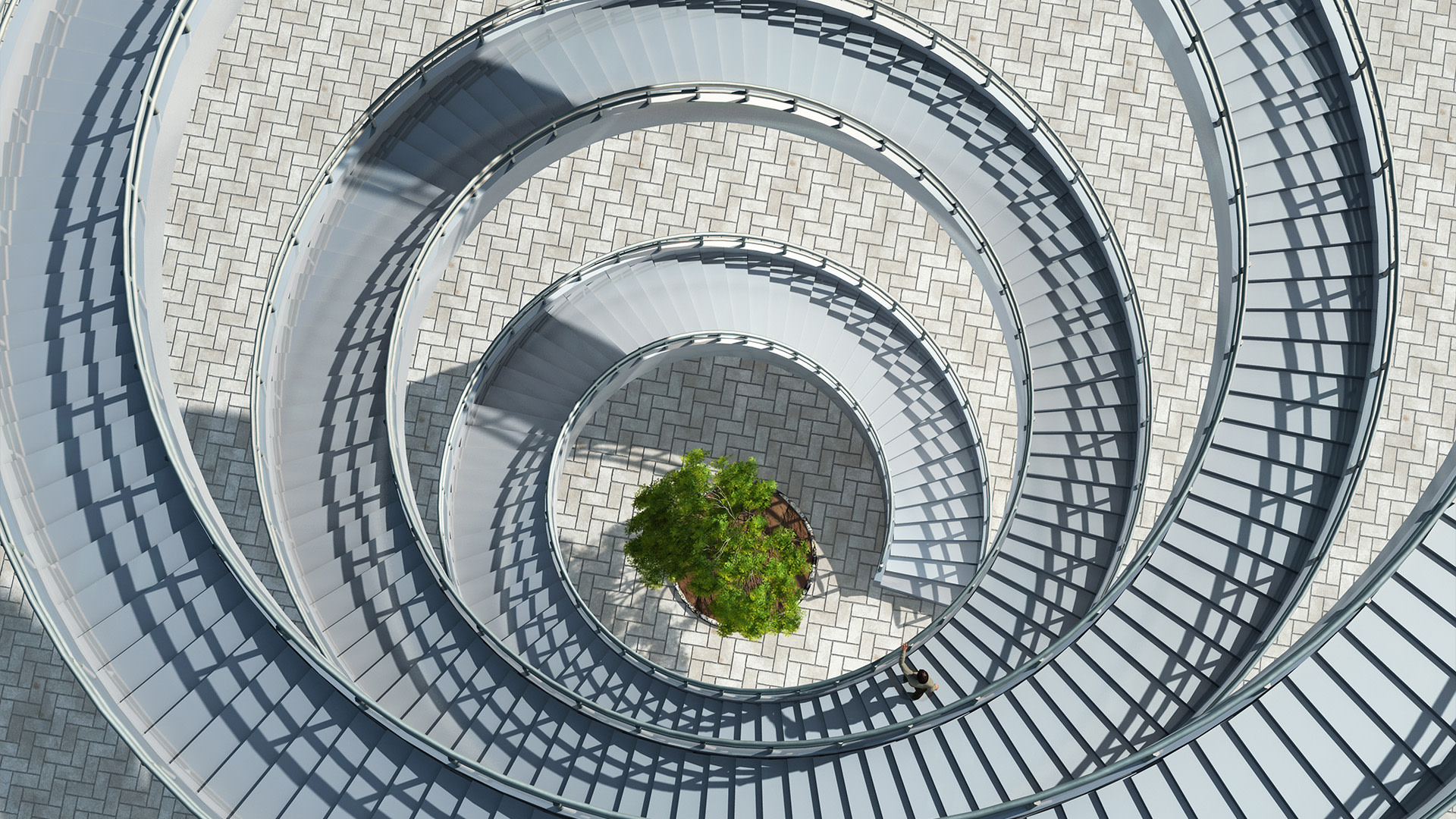
Chapter 2
Technical Risks to Construction Businesses in Australia and New Zealand
The construction industry in Australia and New Zealand (ANZ) is grappling with many technical risks that are reshaping the landscape. These challenges, ranging from emerging technologies to complex supply chains and changing regulations, have significant cost implications for regional businesses.
Emerging Technologies
ANZ construction firms handle vast amounts of data, encompassing materials pricing, labour efficiency, and tender win rates. The evolution of technology is enhancing the capability to gather, analyse, and utilise this data. However, the introduction of new technologies can be a double-edged sword. If not implemented correctly or ignored, they can pose significant risks:
AI and Machine Learning: Artificial intelligence will undoubtedly help the construction industry by arming builders with new insights. For instance, it can analyse injuries by project type or more efficiently select skilled labour from the talent pool during shortages. However, this technology is still rapidly developing and can lead to misinterpretations and flawed safety measures.
Internet of Things (IoT): IoT can help optimise the construction materials supply chain by providing unprecedented levels of logistics monitoring and building data analysis. Yet, with the proper digital infrastructure, it can be easier to make sense of this ocean of data cost-effectively.
Blockchain: Blockchain technology offers a secure ledger for contract storage, enhancing security through “smart contracts” that also promise to cut out legal middlemen. However, without proper understanding and application, this technology can lead to contractual disputes and soured relationships with partners and vendors.
Complex Supply Chains
Recent global events have left the global supply chain fragile, particularly for builders in Australia and New Zealand. The repercussions of the pandemic, global conflicts, labour shortages, and inflation are still evident in 2023.
For example, the war in Ukraine affects the supply of oil, gas, long steel, cement, and concrete. Meanwhile, COVID lockdowns in China disrupted the supply of construction steel and fixtures, increasing demand and price. The halt of aluminium precursor exports from Indonesia and the impact of climate change on key trade routes further complicate matters.
Experts at McKinsey predict major supply chain disruptions every three to four years, emphasising the need for businesses to assess their supply networks continually.
Changing Regulations
Federal and regional governments drive regulatory changes, creating both risks and opportunities. Head contractors in Australia and New Zealand must stay aware of these government amendments.
Just last year, the Australian government brought about amendments to the National Construction Code (NCC), including:
Stricter energy rating and efficiency standards for buildings.
Requirements for certain building classes to accommodate solar panels.
New Zealand also introduced several Building Code changes in 2022:
Revised standards for plumbing and drainage materials and systems.
Enhanced fire safety systems for residential buildings.
New emphasis on energy efficiency and waste minimisation.
Labour Shortages
The Master Builders of Australia identify labour shortages as the biggest challenge for the ANZ construction sector in 2023. The industry has a high demand for project managers and skilled tradespeople like bricklayers, plumbers, and roofers.
As both countries navigate a lack of talented labour, governments are working to develop new incentives to get more people into the industry. Still, this leaves project managers and head contractors in a pinch for the short term.
While the ANZ construction industry faces multifaceted challenges, understanding and navigating these technical risks is crucial. By taking a proactive approach to risk management, you can mitigate and harness these risks as opportunities for growth and innovation.
Chapter 3
Benefits of Proactive Technical Risk Management
In the dynamic world of business, proactive risk management stands out as a beacon of foresight and preparedness. Anticipating potential pitfalls and challenges is how PMs and head contractors can prevent costly mistakes and improve overall results. Such an approach benefits everyone, from frontline workers to top-tier executives.
Improved Safety
Risk management directly improves safety measures. The chance of accidents drops by giving project managers and head contractors the tools to spot health and injury risks. What's the outcome? A safer work environment makes employees happier and more productive. Better safety also reduces missed work and project delays, helping you stay on time and budget.
Higher Quality Work
Quality is the cornerstone of client satisfaction and referrals. Proactive risk management allows firms to detect errors and technical issues during preconstruction, ensuring they don't escalate into larger problems.
By analysing data from previous successes and failures, PMs and head contractors can glean insights that inform better real-time decision-making. This iterative learning process ensures that the end product delivered to clients is of the highest calibre, fostering trust and long-term relationships.
Increased Efficiency
Efficiency in operations directly impacts the bottom line. Actively managing technical risks, identifying potential threats and embracing innovative processes and tools that streamline operations. A prime example lies in the realm of data management. Companies that have honed their data management strategies to mitigate technical risks report significant cost savings. On average, such firms save an impressive 14% on project costs, showcasing the tangible financial benefits of being proactive.
In essence, proactive risk management is not just a protective measure; it's a strategic approach that drives safety, quality, and efficiency. Organisations that embed this philosophy into their DNA are better positioned to navigate challenges and seize opportunities in an ever-evolving business landscape.
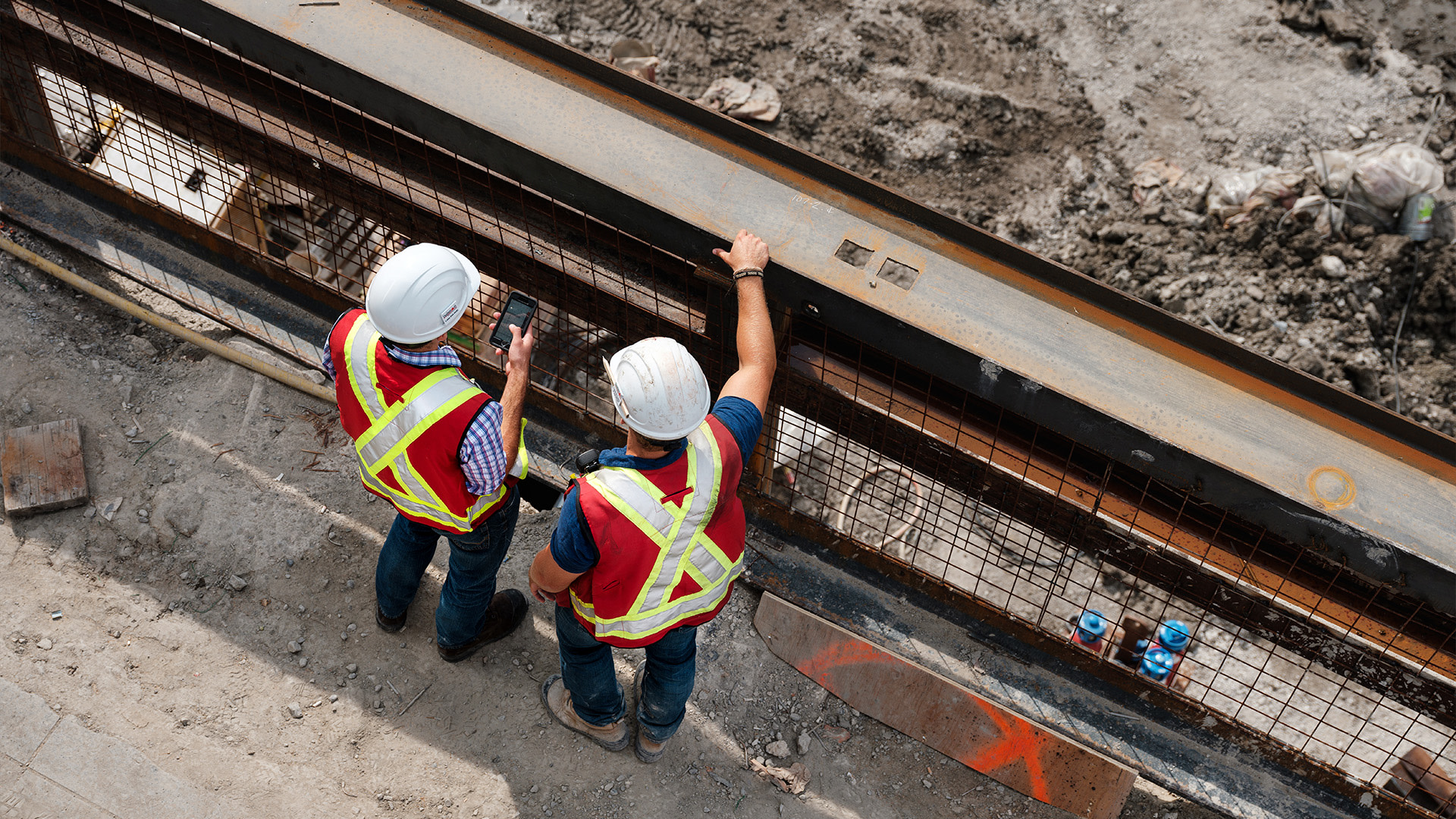
Chapter 4
A 4-Step Approach for Technical Risk Management in Construction
Technical risks can be as daunting as any other challenges. To navigate these successfully, construction firms adopt an approach similar to handling other risks. This involves a four-pronged risk management strategy: identifying, assessing, mitigating, and monitoring.
Identifying and Assessing Technical Risks
The cornerstone of risk management is the ability to pinpoint risk and evaluate its potential occurrence. NASA, a pioneer in risk management due to the high stakes of its projects, highlights three crucial components for proper risk identification:
1. Scenario: Identify any actual event that could adversely impact the project's performance. For instance, a design flaw could lead to structural instability.
2. Likelihood: Gauge each event's qualitative and quantitative probability. It typically ranges from 'highly' to 'low' likelihood but could be more granular depending on the project.
3. Consequence: Elaborate on the tangible impact these events could have on the project. Would it lead to minor delays or catastrophic failures?
During the preconstruction phase, head contractors and project managers must ensure that designs, estimates, and budgets are robust and free from potential pitfalls. An assessment matrix can be invaluable during this stage of the risk management process.
Implementing Effective Mitigation Strategies
Potential risks mark the starting point of technical risk management. The next step involves creating and implementing strategies and backup plans based on how likely these risks are to occur. This step requires careful data gathering and analysis.
It's good that construction firms already collect large volumes of data. The challenge now is to sort through it using the right tools. Adopting these tools means undergoing a digital transformation, integrating a construction management platform with existing resource planning and accounting tools.
Once you've set up the new technology, it becomes easier to establish procedures for monitoring risks throughout the project's life.
Monitoring Risk Throughout the Project Lifecycle
Risks aren’t static—they evolve as the project progresses. Successfully mitigating a risk at one stage doesn't guarantee it won't return, especially in areas like supply chain management and workforce planning. Regular monitoring is crucial.
Robust protocols and state-of-the-art tools can empower head contractors and project managers to detect risks. PMs and contractors can coordinate effective mitigation strategies when they detect low-probability or low-impact risks early.
By adopting best practices and leveraging the right tools, construction firms can safeguard their projects and enhance their overall efficiency and reputation in the industry.
Chapter 5
Mitigating Technical Risks with a Construction Management Platform
The construction industry is transforming in the digital age, and technology is pivotal in mitigating technical risks. Central to this transformation is the adoption of construction management platforms, like Procore, which offer features designed to reduce risk and streamline operations.
Here are some of the key tools Procore has to help you manage technical risks:
Construction Analytics:
Procore’s construction analytics software provides useful information on different aspects of a project—like how often Requests for Information (RFIs) get successfully resolved, the project's cash flow, and any safety incidents reported to OSHA. Using this information, project managers and contractors can make better decisions to help ensure the project is both safe and efficient.
Building Information Modeling (BIM):
One of the standout features of platforms like Procore is building information modelling. BIM revolutionises the construction process by providing all architects, engineers, and contractors with anytime access to 2D and 3D renderings of the job site.
These detailed visualisations offer a comprehensive view of the project, enabling workers to familiarise themselves with the site before setting foot on it. The result? Enhanced worker safety, as potential hazards can be identified and addressed beforehand, and improved job efficiency, as teams can plan their tasks with a clear understanding of the site layout.
A construction project's success depends on having access to the right skilled labour at the right time. With real-time access to workforce availability, project managers and head contractors can proactively identify potential labour shortages. This foresight allows them to address these gaps earlier, helping ensuring that projects remain on track with minimal delays due to workforce shortages.
Quality and Safety:
Two key pillars of any construction project are quality and safety. Procore’s site quality and safety management software help head contractors understand, predict, and enhance both aspects. By leveraging data and analytics, these platforms can identify potential site and worker safety risks, enabling firms to implement preventive measures.
It's important to note that while these platforms offer a robust defence against technical risks, construction firms that haven't equipped themselves with these tools are at a distinct disadvantage. Without the insights and foresight these platforms provide, builders are more susceptible to risks in terms of safety, quality, or project timelines.
Chapter 6
Opportunities for Technical Risk Management in the ANZ Construction Industry [2023]
Like many markets around the world, the construction industries in Australia and New Zealand face technical risks that threaten the safety of workers, the quality of buildings, and the overall success of projects. Over the past few years, the pandemic, global conflict, and demographic shifts have created some issues:
Implementing emerging technologies
Managing increasingly complex supply chains
Finding, hiring, and retaining skilled labour
These technical risks are far from the only challenges facing head contractors and project managers. To learn more about the state of construction in the ANZ and how construction management tools like Procore greatly improve project outcomes, download our How We Build Now 2023 report.