— 8 min read
Understanding the Bill of Quantities in Construction: An In-Depth Guide
Last Updated Feb 7, 2025
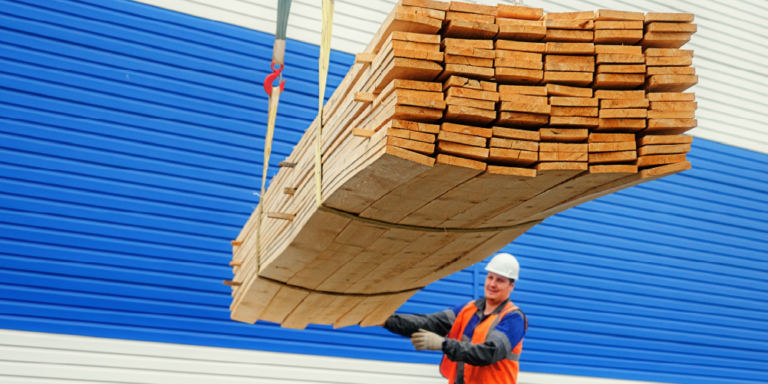
In construction, the bidding and tendering process requires detailed documentation to define the scope of work for a project. Both owners and contractors must make strategic decisions from pre-construction to project closeout, and a bill of quantities (BOQ) plays a critical role in standardising this process.
Table of contents
What is a Bill of Quantities?
A BOQ is a document that outlines the required labour, materials, and quantities for a project, ensuring that contractors are tendering for the same agreed-upon scope.
Typically, it’s created by the project owner, who compiles a standard list of items along with corresponding quantities as part of the tender. This list is then sent to multiple contractors, who provide pricing as part of their bid. By using the BOQ, owners can easily compare costs between contractors on a consistent set of items.
BOQs are most commonly used in construct-only proposals and are typically prepared after the project design is complete but before construction begins.
A BOQ should provide a clear and detailed outline for the contractor, specifying exactly what needs to be priced. This clarity ensures that contractors know precisely what is included in their scope of work, helping to avoid misunderstandings. Once the BOQ is priced and agreed upon, it becomes the basis for the contract—what's priced is what's locked in.
Will Carpenter
Senior Strategic Product Consultant, Procore
Procore
Bill of Quantities vs Bill of Materials
The difference between a bill of quantities (BOQ) and a bill of materials (BOM) is the scope they cover. A BOQ includes all project costs and labour, whereas a BOM focuses only on materials required for the job, listing the quantities and the cost of each.
Often, a BOM is created to support a BOQ and is used to obtain costs from a supplier. Suppliers will frequently also do their own takeoffs to verify quantities and check that all materials are accounted for. Once finalised and approved, the BOM serves as the basis for issuing purchase orders to the subcontractors and suppliers.
When would you use a BOM? A BOM is purely a material list and is commonly used with suppliers. For example, if you're sourcing only electrical equipment, you would give the electrician a BOM. However, if the electrician is responsible for both supplying the materials and doing the installation, a BOQ would be used to price both the materials and the fit out.
Why is a BOQ Important Throughout a Construction Project?
In the construction industry, success hinges on accuracy, cost-effectiveness, and clear communication. A BOQ is invaluable in ensuring that all stakeholders—from owners to subcontractors—are collaborating effectively, across the project’s lifecycle. Here are some of the benefits to using a BOQ:
Aligns Stakeholders on Costs and Scope
Serving as a reference point for head contractors, subcontractors, and owners, the BOQ acts as a single source of truth about project requirements and costs. This alignment improves communication and prevents misunderstanding, helping keep the project on time and within budget.
Standardises Tendering and Enables Fair Comparisons
During the tendering process, a BOQ ensures all contractors are bidding on the same scope of work. This way, it’s easier for owners to make a fair comparison and select the best option. This standardisation reduces the risk of inconsistency and provides greater transparency.
Provides Accurate Estimates and Budgeting
When it comes to construction estimating, the BOQ allows estimators to assign precise costs to each item, ensuring all materials and labour are accounted for. This level of detail helps prevent budget overruns and provides clarity to cost breakdowns.
How detailed and accurate your BOQ estimates are, can make a significant difference in your project not incurring inflated costs, which is a common issue in construction. While estimating tools and Excel can help give you an overview of labour, the most accurate estimates come from including data from past projects. Technology like construction management platforms can store this kind of historical data for future estimates.
Will Carpenter
Senior Strategic Product Consultant, Procore
Procore
Clarifies Contractual Obligations and Minimises Disputes
As a binding document, the BOQ protects the contractor and the owner. There is no room for misunderstanding or misquoting, accountability is clarified from the start, reducing the likelihood of disputes. In the event of disagreements, the BOQ serves as a reference to resolve issues quickly with greater accountability and less delay.
Contractually, the BOQ is what the job is locked in at. That's not to say that there aren't ways to make adjustments, variations can be used to adjust and claim additional work that may be needed beyond what was scoped in the BOQ. Variations will require separate negotiation and approval.
Will Carpenter
Senior Strategic Product Consultant, Procore
Procore
Supports Invoicing and Tracks Project Progress
Pro Tip
With modern construction management software, integrating a BOQ enables real-time monitoring of scope discrepancies, minimising human error and miscommunication. This added transparency helps keep projects on track and within budget, making sure that changes are visible and managed effectively.
As construction progresses, the BOQ serves as a schedule of rates, tracking completed work and monitoring the materials on-site. It helps identify any fluctuations or deviations from the original scope, providing a reliable basis for invoicing and timeline adjustments. This prevents scope gaps and protects stakeholders from inflated costs or delays. However, an inaccurately scoped BOQ can put all parties at risk, underscoring the importance of thorough checks before the project starts.
How to Prepare a Bill of Quantities
A BOQ is a collaborative document that has input from the entire construction team.
Pro Tip
A well-prepared, detailed BOQ should be created alongside a detailed set of drawings. When these documents complement each other, the owner can clearly see what is being priced. Contractors can then compare both documents, perform their calculations, and ensure they match. A BOQ is simply a line item—it cannot visually depict the project - in an ideal world, there would always be drawings too.
- Owner’s Input - The owner starts creation of the BOQ by outlining the mission and then the scope of work for the project.
- Design Development - Architects and engineers work together to turn the mission into drawings. The design is refined in increasing detail, ideally grouped by required subcontractors for easier pricing. This includes all requirements to complete the project, such as task descriptions, sizes, material volumes, and precise measurements.
- Collaboration with Contractors - The list is then shared with contractors, who can work with various suppliers, quantity surveyors, engineers, and subcontractors to prepare accurate pricing based on the BOQ and takeoffs.
- Addressing takeoffs and missed scope - Contractors will then often perform their own takeoff to verify quantities and identify discrepancies that the owner or design team may have missed. Missed scope occurs when an item is shown on the drawings but is missing from the BOQ. If discrepancies arise, they can submit a request for information (RFI) to the head contractor, who seeks a response from the owner.
Best Practice in BOQ Creation
To get the most value out of structuring your bill of quantities, it's important engage contractors as early as possible. I don't feel like that happens enough, and it's pretty evident in the industry - from the amount of incomplete and over budgeted work that happens - and that's really because the bill of quantities isn't being done properly.
Will Carpenter
Senior Strategic Product Consultant, Procore
Procore
Embrace early contractor involvement
Early Contractor Involvement (ECI) helps reduce missed scope and overlooked minor details for a more accurate bill of quantities. A much clearer definition of what needs to be done will yield much more accurate prices.
Include a lot of detail.
Don’t hold back on detail! A clear and detailed description of each item and task makes sure that all stakeholders are across exactly what is needed for a more accurate quote.
Invest in technology.
Using a single source of information for all stakeholders like construction management software minimises miscommunications between project stakeholders, which can lead to project delays and blown-out budgets.
Leverage past project data.
Capturing BOQ data from the start and end of a project provides insight into scope changes, helping identify missed requirements or underestimated costs. When stored in software systems, this data becomes actionable—teams can analyse discrepancies and refine future BOQs to prevent scope gaps from reoccurring. By pulling in historical data, contractors and estimators can ensure that future projects are better planned, minimising the risks of unexpected changes and improving overall project efficiency.
Work with experienced stakeholders.
Industry experience and expertise are a must when creating a BOQ. Working with people who have an inadequate knowledge and understanding of construction or have poor project management skills can lead to incorrectly forecasted scopes, many more variations and higher costs later on.
BOQs create transparency from tender to closeout.
A well-prepared bill of quantities sets up projects for success by providing a set estimated cost, timeline and project overview. It protects contractors, owners and suppliers by facilitating a document that everyone can reference. This supports transparent bidding and simplifies the tendering process. Using advanced construction management software, beyond Excel, can further enhance the accuracy and reliability of BOQs, providing invaluable data for future projects to benchmark against, and enabling more accurate pricing and identification of missed elements.
Categories:
Tags:
Written by
Will Carpenter
9 articles
Will is a Senior Strategic Product Consultant with a passion for utilising technology to enhance project workflows and efficiency in the construction industry. He plays a crucial role in assisting construction companies in maximising Procore's benefits.
With over a decade of experience in the construction industry, predominantly as a Civil Infrastructure Engineer, Will first used Procore as a customer himself, transforming his own daily operations. Captivated by its potential to elevate project and quality management, he made the decision to join Procore. His hands-on experience in construction, coupled with technical expertise, equips him to provide valuable insights and solutions for companies looking to optimise their workflows.
Explore more helpful resources
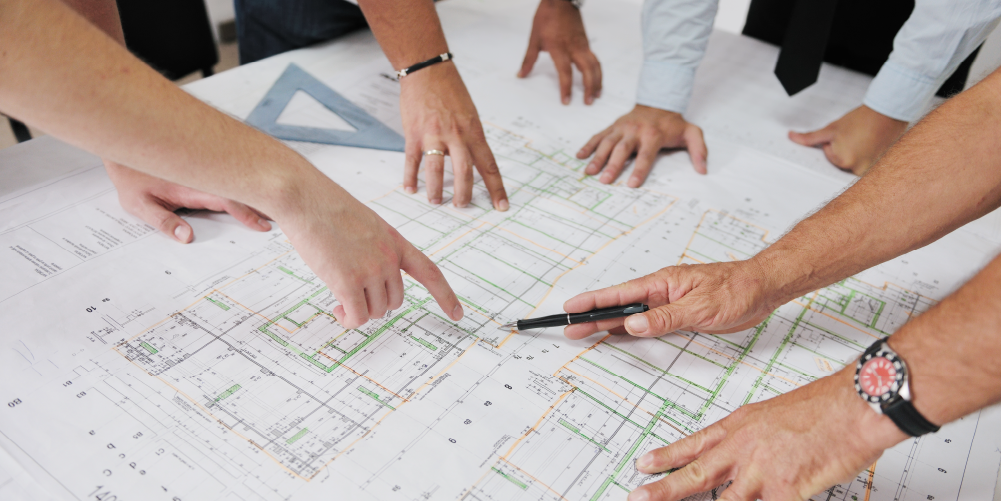
Streamlining Your Construction Workflow for Better Project Delivery
In commercial construction, effective coordination is not a luxury—it’s a requirement. As project scopes expand and regulatory oversight tightens, reliable workflows become the infrastructure that underpins successful delivery. Without structured...
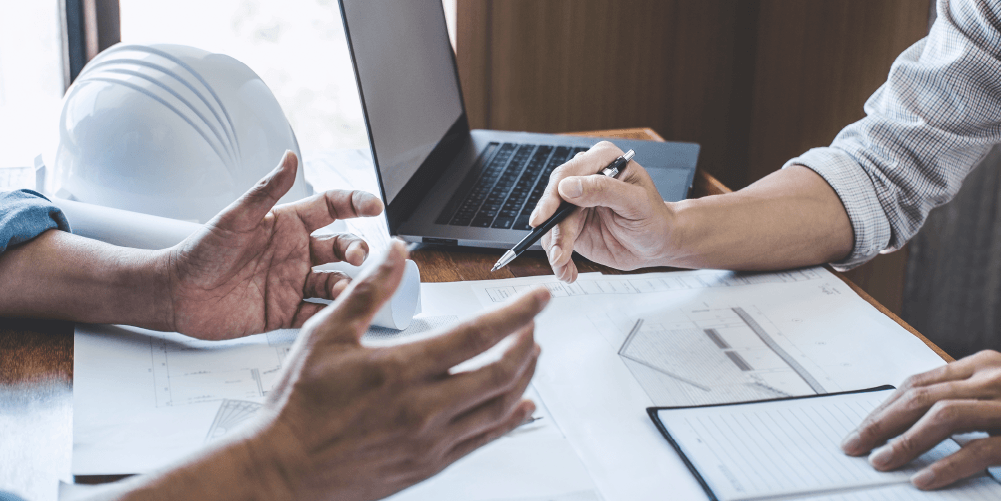
Construction Change Management: How to Minimise Risk and Maintain Control
Change is inevitable in commercial construction projects. Even with detailed planning, variations can arise from shifting client needs, site conditions, or sequencing challenges. These changes can lead to cost overruns,...
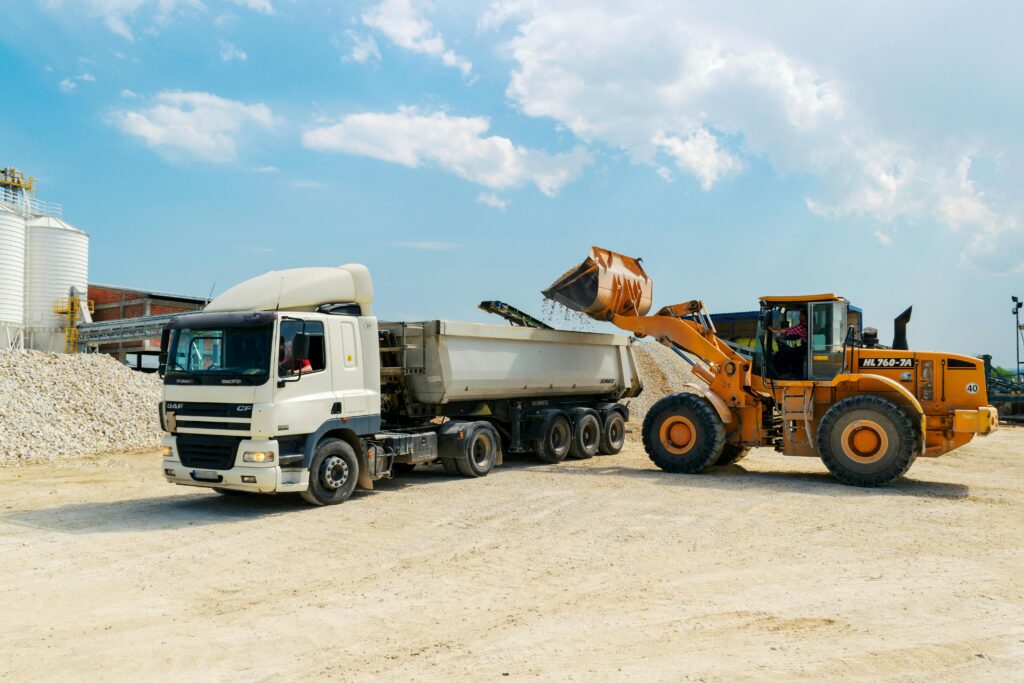
Construction Logistics 101: Planning, Coordination, and On-Site Efficiency
Strong logistics planning plays a critical role in delivering safe, efficient, and cost-controlled commercial builds—especially as projects grow more complex and client expectations rise. Well-planned logistics improves coordination and helps...
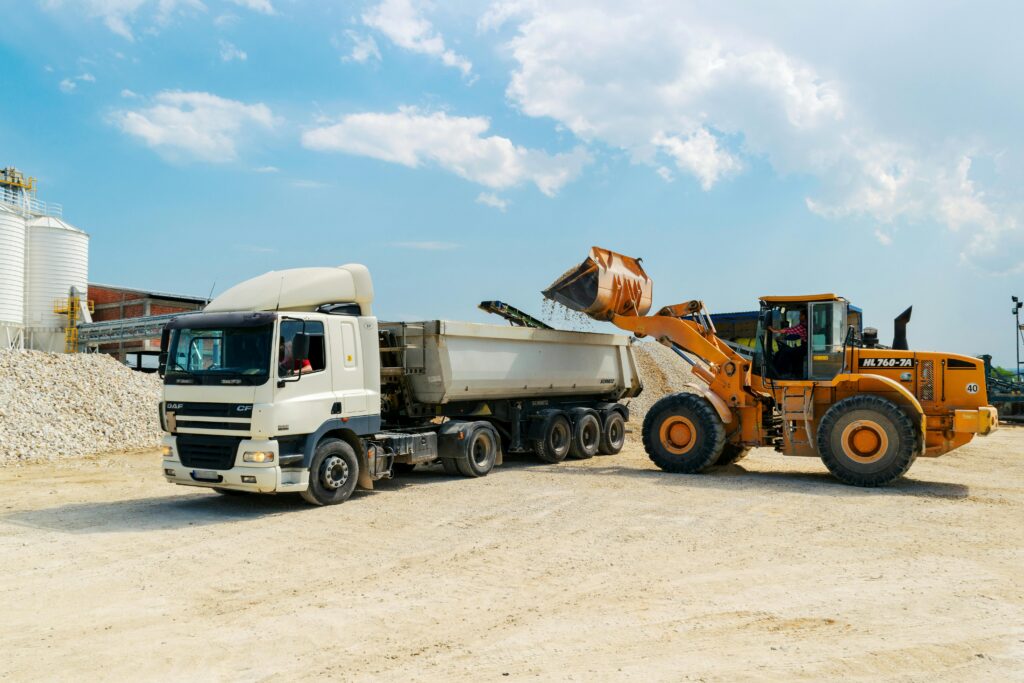
Construction Logistics 101: Planning, Coordination, and On-Site Efficiency
Strong logistics planning plays a critical role in delivering safe, efficient, and cost-controlled builds—especially as projects grow more complex and client expectations rise. Well-planned logistics improves coordination and helps teams...