— 8 min read
A Guide to Construction Procurement in Australia
Last Updated Jun 13, 2025
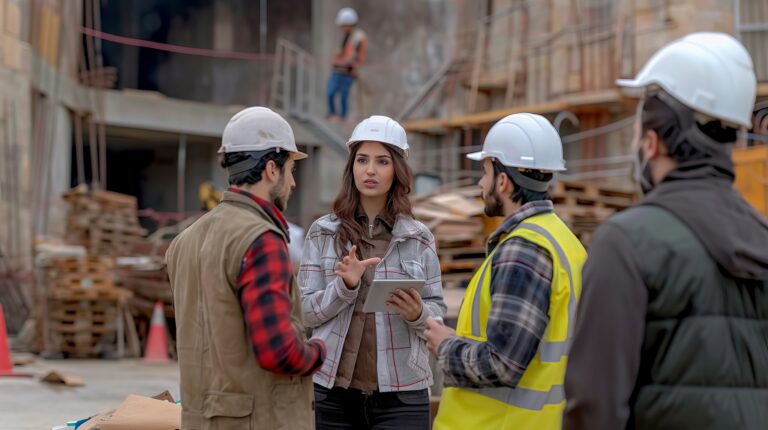
Construction projects almost always have a lot of moving parts. There are specialised materials to order (many of which need to be customised), suppliers to negotiate with, contractors to manage and a schedule to adhere to.
In this article, we walk through the steps in the construction procurement process, providing an overview of the responsibilities and common challenges during each phase.
Table of contents
What is Construction Procurement?
Construction procurement is the process of acquiring goods, services, and works for construction projects. It involves selecting contractors, suppliers, materials and consultants to deliver a project on time, within budget, and to required standards.
Procurement is a critical element of project management. It ensures all resources are available when they’re needed and that delivery aligns with project goals, budget constraints, and timelines.
Without a robust procurement strategy, even well-planned projects are more likely to face significant disruptions and financial setbacks.
Procurement vs Purchasing: The Difference in Construction
Procurement and purchasing are often used interchangeably, but they serve distinct functions within a construction project.
Purchasing refers specifically to the act of buying the materials or services needed—placing orders, managing financial transactions, and ensuring the right products are delivered on time. But this is just one step in the procurement process, which also includes things such as logistics, approval, and strategy.
An effective procurement strategy ensures that purchasing decisions are made at the right time and under the right conditions, preventing—or at least minimising— delays and cost overruns.
Who is Responsible for Procurement?
Usually, responsibility for procurement will depend on the size of the organisation and complexity of the development.
On larger infrastructure projects there will almost always be a dedicated procurement team with specialised positions (e.g. procurement managers, supply chain coordinators, and purchasing officers).
On smaller projects, procurement is typically less formal, with duties shared among several roles. Site engineers, project managers, site managers, and even foremen often take on procurement responsibilities.
On residential projects, procurement is even simpler being organised but the owner or foreman.
What are the Different Construction Procurement Methods?
There are various construction procurement methods organisations use depending on the project's size, complexity, and the number of stakeholders involved. Each of the common procurement methods has its own strengths and weaknesses, meaning that it suits a particular style of project.
The design-bid-build method provides clarity and control over the design, but it can lead to longer project timelines. It works best on major projects where the client wants full control over the design before involving the contractor. Meanwhile, because the design and construct method allows for greater efficiency and potentially faster project delivery, it’s commonly used in commercial building projects where integrated project delivery is a priority. Finally, the construct only method is commonly used in Australian commercial and civil construction projects.
Will Carpenter
Senior Strategic Product Consultant, Procore
Procore
Design-Bid-Build
This method is typically used for larger projects, such as government infrastructure or large-scale private developments.
The design phase is completed first, either by the owner’s in-house team or an independent consultant. The project is then put out to tender, and a contractor selected.
Design and Construct
In this method, a single contractor is chosen before the project begins and is responsible for both design and construction. This approach is often chosen for projects that require fast-tracking or when the owner wants to streamline the procurement process.
Construct Only
This is incorporated in the design-bid-build method. In construct only, the owner completes the design plans separately, often with a consultant, before tendering the project as ‘construct only’.
There is a clear delineation between the design and build phases. The contractor delivers the project to predefined design specifications, managing all construction activities and subcontractors as required.
Construction Procurement Management Process
Pro Tip
For larger projects, such as high-rises, adopt strict procedures, assign dedicated project teams, and closely monitor lead times.
Careful planning and sequencing are essential—For example, coordinating the delivery of hundreds of tonnes of steel over months, requires precise timing to avoid delays and maximise efficiency. Treat every step in the procurement process as critical to staying on track, controlling costs, and ensuring the project’s success.
The construction procurement process is essential to project management, though its steps vary with project size and complexity.
In the early stages, procurement focuses on estimating costs, preparing tenders, and gathering data for planning and pricing. Long lead-time items and procurement schedules are arranged at this time. As the project moves into construction, the project team takes over procurement, finalising and tracking items to ensure smooth delivery.
Steps in the Procurement Process
There are generally some key steps most procurement processes go through.
1. Identify requirements.
The design team creates detailed specifications, outlining the materials and services needed. This is crucial for accurate budgeting and planning.
2. Prepare estimates and tenders.
Contractors prepare estimates and submit bids, including bill of quantities, based on project specifications. For larger projects, this involves getting quotes from multiple suppliers and subcontractors.
3. Award contracts.
The client reviews the bids, selects the contractors, and formalises contracts. For complex projects, the procurement team may begin ordering long lead-time items well before construction begins. From this point, the responsibility of procurement typically lands on the hands of a project team who are responsible to finalise and track procured items for the remainder of the project.
4. Order materials.
Contractors confirm lead times with suppliers and issue purchase orders. For smaller projects, this may be as simple as getting three quotes and placing an order.
5. Approve materials.
The client and relevant authorities inspect and approve all materials, making sure they meet required standards.
6. Manage delivery and coordination.
Procurement managers track the delivery of materials, making sure they arrive on site as scheduled. This involves coordinating with suppliers and arranging logistics to avoid delays and site congestion.
7. Inspect quality and compliance.
Materials are inspected for quality and compliance. Any issues are addressed before approval and installation.
Solving Procurement Challenges
Construction procurement can come with its fair share of challenges. If not managed effectively, these can lead to delays, budget overruns, and disruptions. By identifying these risks and developing contingency plans, teams can respond swiftly to unforeseen challenges, safeguarding project timelines and budgets.
Engaging stakeholders from the earliest stages of procurement ensures that everyone is aligned on project goals, timelines, and risks. When all key players are involved early, it reduces miscommunication and provides the flexibility needed to manage design changes or supply chain issues efficiently. Proactive planning allows us to identify potential disruptions upfront, so we can respond quickly and avoid delays or budget blowouts.
Will Carpenter
Senior Strategic Product Consultant, Procore
Procore
Challenge | Solution |
Ambiguous specifications: Vague instructions can lead to significant issues. When designers or owners provide vague instructions like “build as per standard” without detailing exact requirements. | Leverage historical data and use Requests for Information (RFIs) to clarify ambiguous details. Procurement management software also allows for effective communication and documentation of clarifications. |
Submittal delays: Approval delays for shop drawings and materials can hinder progress. In commercial projects, fine details such as specific fabrications and finishes need thorough approvals before materials can be ordered. | Delays can be avoided by establishing strict timelines for submittal reviews and approvals, and tracking these with project management software. |
Budget overruns: Hidden costs often stem from inaccurate initial estimates. This is common when estimators lack accurate market data or don’t consider material lead times. | Re-tendering key packages during the project can help secure more favourable terms and manage costs effectively. |
Supply chain disruption: The COVID-19 pandemic has highlighted vulnerabilities in supply chains. Shortages in materials like steel and concrete can severely impact project timelines. | Anticipate potential delays by diversifying suppliers and proactively analysing lead times. |
Payment delays: In Australia, most construction works on a 30-day payment cycle, but exceptions exist for specialised items, like concrete or steel. | Ensure suppliers are pre-approved and align procurement activities with expected cash flows to avoid bottlenecks. |
Schedule changes or delays: Projects often face unexpected delays. | Maintain a detailed and regularly updated procurement schedule that integrates with the overall construction timeline to facilitate smooth operations. |
Design changes: Projects often encounter unforeseen changes to designs as projects progress. | Build flexibility into designs to accommodate changes without necessitating new material orders, and ensure prompt communication of any alterations. |
Damage to stored materials: On larger or longer builds, materials may need to be stored for some time. | Implement proper storage protocols and conduct routine checks to ensure materials remain in good condition. |
Standardisation, preparation and technology can improve the procurement process.
In conclusion, effective construction procurement is essential for ensuring projects are completed on time, within budget, and to the required quality. With so many moving parts, from material lead times to contract management, a well-planned procurement strategy helps align stakeholders, manage risks, and streamline processes. Early collaboration fosters clearer communication, minimising delays and budget overruns. Leveraging standardisation, preparation, and integrated technology, enhances visibility across procurement activities, ensuring smoother operations.
By anticipating challenges and implementing proactive solutions, teams can safeguard project timelines and avoid costly disruptions. Ultimately, strong procurement management is key to driving successful project delivery in Australia’s dynamic construction industry.
See what’s coming in construction over the next decade.
Download the Future State of Construction Report for insights, trends, and innovations shaping the industry over the next 8–10 years.
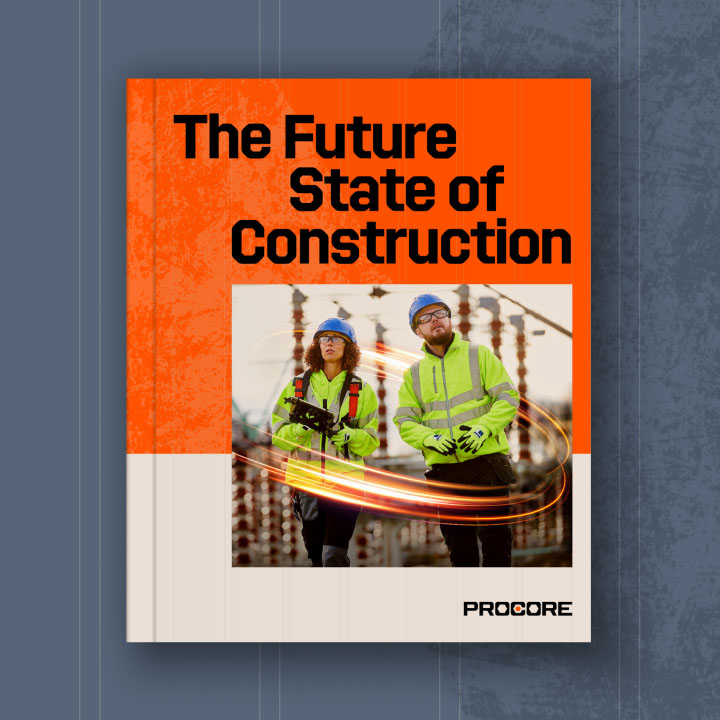
Categories:
Tags:
Written by
Will Carpenter
9 articles
Will is a Senior Strategic Product Consultant with a passion for utilising technology to enhance project workflows and efficiency in the construction industry. He plays a crucial role in assisting construction companies in maximising Procore's benefits.
With over a decade of experience in the construction industry, predominantly as a Civil Infrastructure Engineer, Will first used Procore as a customer himself, transforming his own daily operations. Captivated by its potential to elevate project and quality management, he made the decision to join Procore. His hands-on experience in construction, coupled with technical expertise, equips him to provide valuable insights and solutions for companies looking to optimise their workflows.
Explore more helpful resources
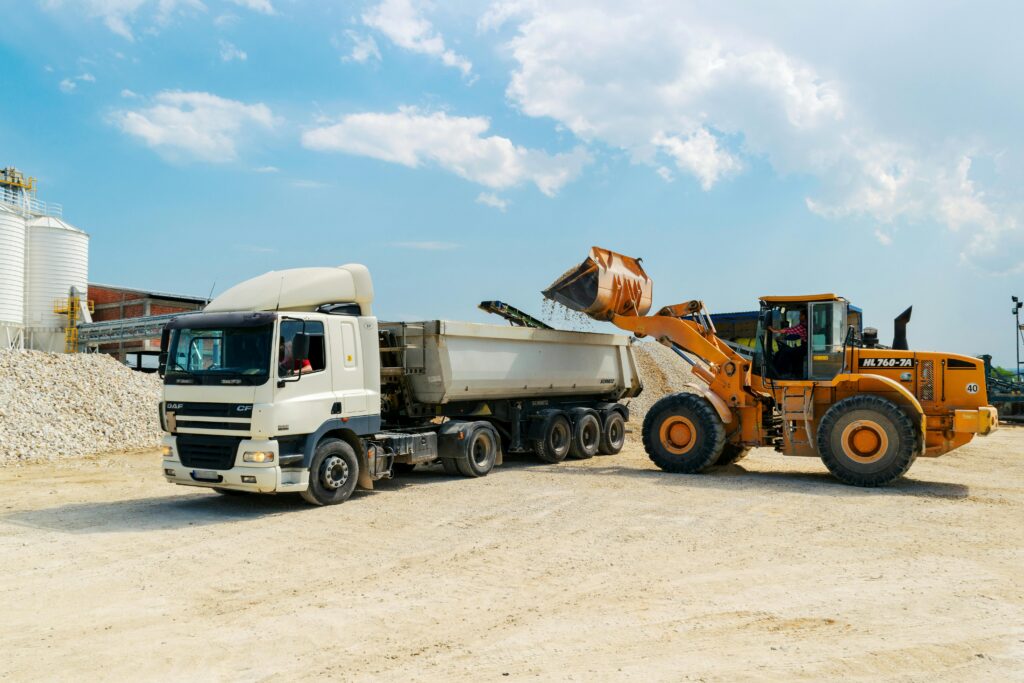
Construction Logistics 101: Planning, Coordination, and On-Site Efficiency
Strong logistics planning plays a critical role in delivering safe, efficient, and cost-controlled builds—especially as projects grow more complex and client expectations rise. Well-planned logistics improves coordination and helps teams...
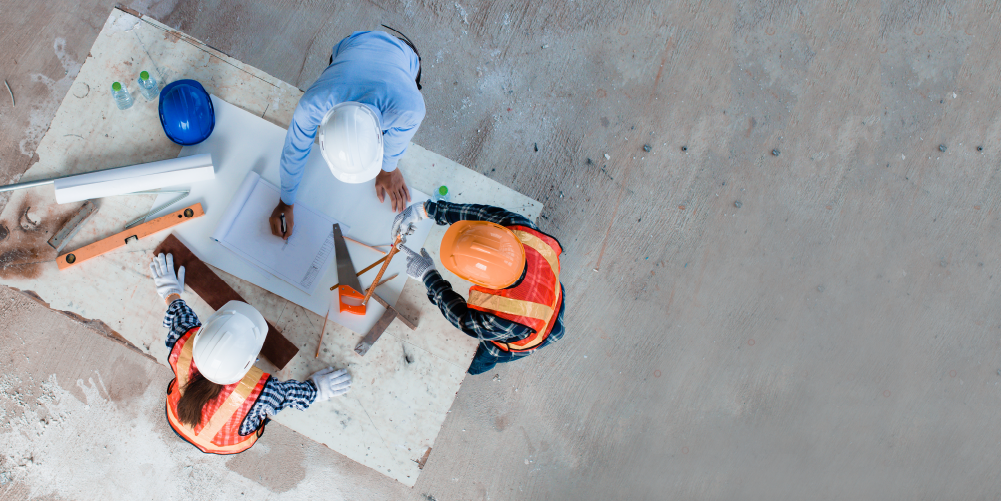
Understanding Construction Milestones: What They Are and Why They Matter
Construction milestones help drive timely, cost-effective project delivery in commercial builds. They bring structure to complex construction programs, support accountability, and enable better planning and coordination across teams. When milestones...
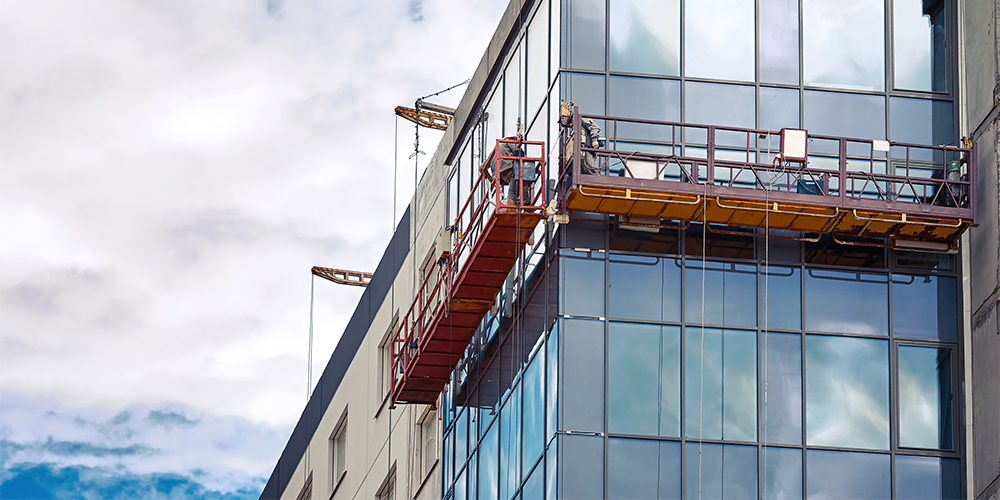
What Happens Post Construction? A Guide to Final Stages and Handover
Construction work may be finished, but the project is not complete. The post-construction phase is a critical transition period where compliance, client satisfaction, and long-term outcomes are either secured or...
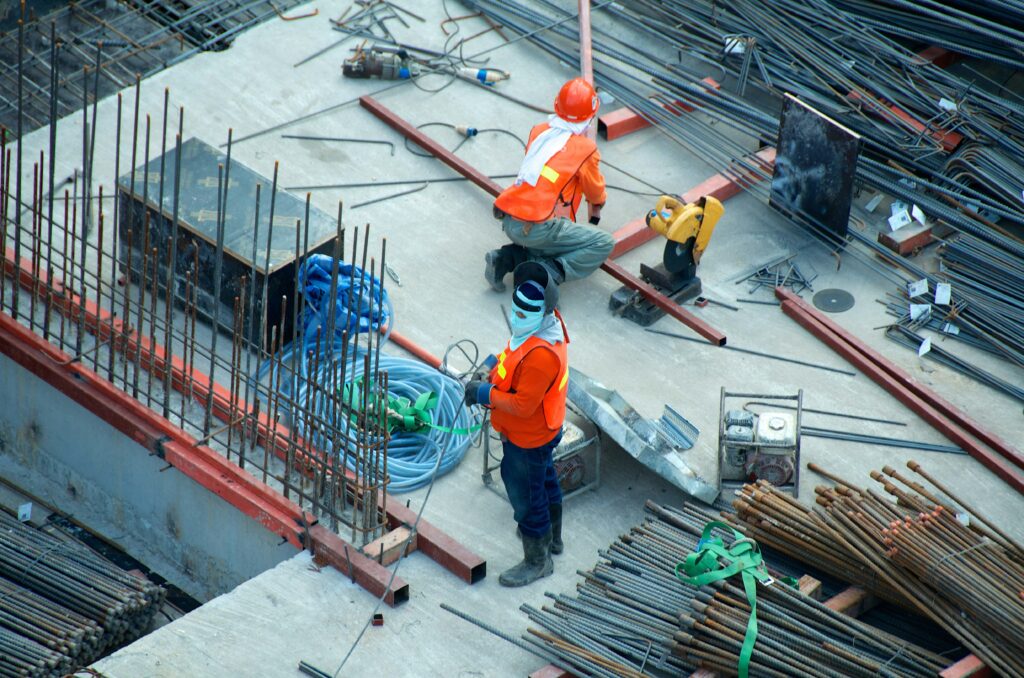
Mastering Subcontractor Management: Tips for Smoother, More Profitable Projects
Subcontractor management directly impacts project quality, timelines, and profitability. Strategic oversight reduces risk and keeps work running on schedule while maintaining budget control. This article explores the essential components of...