— 13 min read
The Ultimate Guide to Building Information Modeling (BIM)
Last Updated May 30, 2025
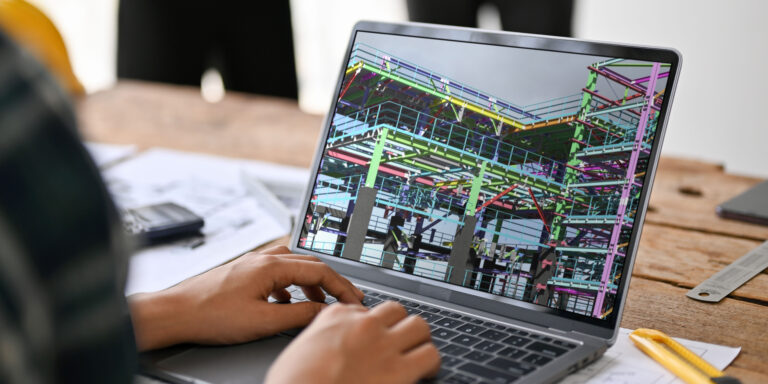
Construction is one of the last industries to adopt new technologies. Still, as novel solutions become available — and as their benefits are proven — construction professionals get increasingly open to digitizing their process.
Building information modeling (BIM) is a prime example. Moving from 2D drawings to a 3D visualization of the project delivers a broad range of wins, from automated constructability checks to smoother coordination.
BIM has seen steadily increasing adoption across architects, engineers, construction professionals and project owners. It’s important, then, for industry stakeholders to understand what this technology is and how it works.
Table of contents
What is BIM?
Building information modeling is an umbrella term that encompasses both the 3D model and all of the data and processes attached to it. In other words, it’s more than just a 3D plan. Users can attach additional data — from scheduling to costing to sustainability factors — to better drive the project toward its desired outcomes.
Construction stakeholders have taken note of BIM's benefits: The United Kingdom now mandates BIM for all of its public sector projects and some domestic entities, from healthcare to higher education institutions, require BIM, too. Take the U.S. General Services Administration and Harvard as examples.
Through building information modeling, stakeholders use digital models to design, construct and operate buildings better. BIM allows more accurate and more useful visualization of the project than 2D drawings. Just as importantly (if not more so), BIM allows users to apply metadata and aggregate information within the model so that all stakeholders can collaborate there and refer to a single source of truth.
From CAD to BIM
BIM is technically a process but one that leverages a specific object: a digital model. To understand BIM processes, working up to that model helps.
BIM contrasts with computer-aided design (CAD). By leveraging technology, CAD has helped the construction industry move faster and with more accuracy in creating drawings. CAD is almost always used to create in two dimensions, though.
With BIM, users move from 2D to 3D visualization of the project. But BIM is more than just the 3D model. It also overlays data and processes. As a result, the umbrella term of “building information modeling” encompasses the entire process of creating and maintaining the digital 3D representation of the project in question.
BIM, then, is technically a verb, not a noun. That said, across the architecture, engineering and construction (AEC) industry, BIM is commonly used to refer to the model (i.e., used as a noun). And while a “BIM model” — that is, a building information modeling model — might seem redundant, it's a common industry vernacular.
The Anatomy of a BIM File
While BIM is a verb, BIM files are nouns — i.e., objects.
BIM files are the digital 3D models that AEC professionals and owners use to create and maintain the building. The BIM file contains millions of lines of code. It might be captured as an Industry Foundation Classes (.ifc) or a DWG file, but many BIM software providers have their own proprietary BIM file formats.
Data interoperability plays a role here. For the model the design team makes to be useful to the general contractor (GC), for example, the model file might need to move from one software to another. Beyond that, the project might leverage a federated model, or a multi-disciplinary model that integrates different areas modeled by different stakeholders. The GC might create a federated model using models from their mechanical, electrical and plumbing (MEP) contractors. Currently, data interoperability serves as a challenge in BIM processes.
Even with that challenge in play, BIM models provide a data-rich resource stakeholders can use to learn about the project. However the model is created, the resulting BIM file is composed of a series of layers, with each layer composed of objects. Each object is clickable. When the BIM file is enriched with data, clicking an object will pull up the aggregated information. Clicking on a pipe, for example, would tell the user about all of the specifications of that pipe.
Dimensions of BIM
Since BIM extends beyond just the 3D model, it leaves room for additional data and processes. These add more information to drive specific project outcomes.
Today, stakeholders can add the following dimensions to the model:
- 4D BIM for scheduling
- 5D BIM for cost estimating
- 6D BIM for sustainability
- 7D BIM for facility management
Some organizations take BIM even further, up to 10 dimensions. As the AEC industry catches up in its BIM maturity journey, though, the four dimensions above capture what most companies are doing.
BIM in the Preconstruction Phase
With a virtual 3D model, designers, engineers, construction professionals and the owner’s team get a way to explore the structure before a single shovelful of earth is moved. As a result, the model allows for analysis, improvement and planning optimization during preconstruction. This means making changes when they’re significantly more cost-effective than in the built environment.
Specifically, BIM can be useful during preconstruction to deliver the following results.
Speed in Authoring and Design Iteration
BIM has the potential to deliver major efficiency gains in arriving at the drawings needed for any project. Instead of having to draw a plan view, then an elevation view, then an isometric view and so on, designers “draw” the building once in creating the model. They can then slice the model to create the required drawings.
BIM continues to deliver productivity improvements as the design evolves, too. If a door needs to be moved, for example, the designer could need to go back and make adjustments in each individual drawing. But if they have a model, they can move that door once there. Every resulting drawing automatically updates.
This persistence between different views and slices saves a lot of time in drafting, making it a highly efficient tool for preconstruction. At the same time, BIM eliminates the possibility of human error in individual drawings as updates need to be made.
Project Analysis and Optimization
BIM allows engineers to virtually test the design to make sure it will be structurally sound and align with the owner’s goals. Structural load analysis is a type of BIM-supported engineering analysis, for example.
If the owner wants to develop an environmentally friendly structure, teams can overlay energy modeling on the BIM file. This allows designers and engineers to optimize the structure for operational efficiency upon completion.
If the owner is trying to achieve a certain sustainability certification for the building — like Leadership in Energy and Environmental Design (LEED) or Building Research Establishment Environmental Assessment Method (BREEAM) certification — the model can be used to build in adherence with the required standards.
As the design process moves forward and that model aggregates more data, it helps to finesse everything from the proper integration of mechanical systems to the desired placement of design features.
Clash Detection
Fully visualizing the project during preconstruction makes it possible to perform clash detection.
This is the practice of reviewing the model to make sure that no solids intersect or come too close to one another to be functional. It’s a spatial coordination effort that gets particularly useful in congested areas like ceilings and corridors. Because everything is modeled in three dimensions, it gets easier to see where clashes occur. Better yet, most BIM software solutions can perform automated clash detection.
Clash detection is a valuable constructability check that can prevent rework.
Project Coordination
BIM makes it possible to streamline the planning on any construction project. Depending on the dimension(s) of BIM the team deploys, it can help with:
- Scheduling (4D BIM): Overlaying the axis of time on the model arrives at 4D BIM. This allows for the visualization and simulation of the project over time. As a result, teams can more easily determine where milestones should be set, how to sequence work and even how to schedule material deliveries and usage of laydown yards.
- Cost estimating (5D BIM): BIM software can deliver automated material quantifications. As a result, stakeholders can more accurately — and more easily — estimate the total cost of the build. It can also make it easier to estimate the time required to complete installation, helping better budget for labor.
- Enhanced sustainability (6D BIM): Because it allows for more accurate design and better planning, BIM helps to eliminate waste on the project, particularly waste from rework.
If the BIM model is data-rich and accurate, it can be used to automate 3D construction takeoffs. With this kind of material takeoff, the modeling software quickly generates information about the type and quantity of materials needed for the project based on the data in the model. By some estimates, using BIM for construction takeoffs makes them 35 times faster.
Build a Strong Foundation with our Preconstruction Course
With 20+ years of experience, Ben Ashburn teaches you how to streamline planning, bidding, and procurement for better outcomes.
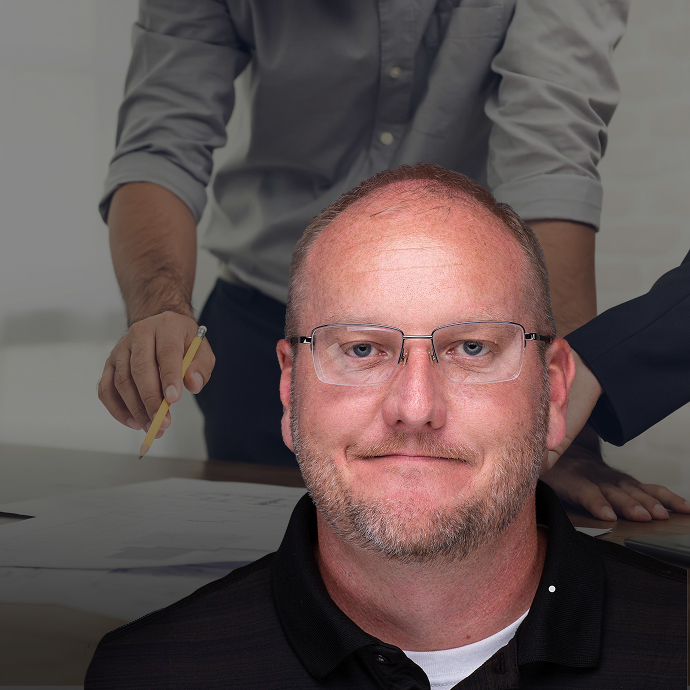
BIM During Construction
Using a 3D model in the field can be highly useful to the team there. Some teams deploy the model via tablets, while others set up kiosks with desktop computers or even print off slices from the model and tape them to the wall. In any iteration, the model serves as a valuable tool for contractors in the following ways.
Guiding and Validating Installation
The model should provide the necessary information to answer the majority of questions that arise. Workers on the jobsite gain the ability to click on any object and instantly access all the aggregated information about it. If a team is unsure where a pipe needs to be installed, for example, the model can tell them the precise location, avoiding wasted time and resources.
Then, the model becomes a valuable validation tool for performed work. It can be used to confirm that installation was either completed in line with the project’s plan or that something needs correction. Continually using the model in this way means that any issues get caught early before the problem can escalate. It also serves as a meaningful quality control measure.
Because it allows teams to validate what has been installed on an ongoing basis, BIM supports enhanced scheduling, supply chain and cost management. Comparing what’s happening in the field to the model illuminates any areas that need adjustment, minimizing unwelcome surprises as the project progresses.
Integrating BIM With Other Field Technologies
BIM can be even more useful when deployed alongside tools like lidar, robotic total stations and reality capture drones. With tools that allow for analysis of what has been planned and what’s being installed onsite, stakeholders can confirm that the work being done aligns with what was coordinated in the model.
Beyond that, BIM can make it possible to have skilled labor performed by unskilled personnel. When augmented reality (AR) overlays the model with the built environment, it tells that worker precisely what to do where. Sophisticated BIM-AR technology can even provide step-by-step instructions.
Improving Jobsite Safety
Because BIM enables stronger, smarter project management, it can help to create safer, more predictable jobs. The data shows that a good share of jobsite injuries happen during rework. In many cases, rework comes from incomplete design or poor communication of the design to the installers in the field. BIM helps to reduce the likelihood of both.
Prefabrication
Prefabricating systems, components and even entire rooms can deliver a range of benefits for the project. It allows work to be completed in a safe, controlled environment. Workers can have a clean, dedicated space to do their job, where other contractors and materials aren’t a concern and all the resources they need are readily available. This makes it possible to create high-quality components faster.
It’s key, though, for prefabricated components to fit precisely once they’re brought to the jobsite for installation. With BIM, the entire structure has already been coordinated to the necessary level of detail.
BIM in Post-Construction
While BIM’s usefulness after a project is completed is still evolving, most owners currently use the model in two primary ways: maintenance and improvement.
Facilities Maintenance
When owners have a model they can access for the lifespan of the building, they gain a wealth of information about their structure. They can click on any object in the model to access all of the aggregated data about it.
Clicking on a malfunctioning mechanical system would tell the owner what power source it uses, for example. Similarly, clicking on a window would pull up the precise model should it need to be replaced. When maintenance is required, owners no longer have to search through close-out documentation to find the required details about the building’s features.
Even less sophisticated models can be useful from a facilities maintenance perspective. The model can allow maintenance personnel to identify the location of access panels, for example.
Some owners have even advanced to the point where internet of things (IoT) sensors throughout the building tie to the model, alerting them of maintenance requirements.
As owners increasingly deploy facilities maintenance technologies, the model becomes more and more useful. Providing the owner with the model at closeout gives them a wealth of data they can plug into their building maintenance system (BMS) or computerized maintenance management system (CMMS).
Some owners today even deploy digital twins, or virtual replicas of the built environment. With metadata attached to the virtual twin, this allows for better maintenance, operational efficiency and sustainability.
Renovations, Retrofits and Capital Improvement Projects
The as-built drawings handed over to the owner at closeout have a reputation for being poor when it comes to accuracy. A model that was updated throughout the construction project can be particularly useful here, then.
By leveraging that model to determine the starting point for renovations, retrofits and capital improvement projects, owners can minimize the likelihood of requests for information (RFIs) and change orders.
The Current and Future State of BIM in Construction
Adopting BIM alone doesn’t necessarily increase productivity, safety or anything else. Teams need to be trained to properly deploy building information modeling processes. In other words, they need to learn how to design and build virtually in the same way they needed to learn to design on paper or build in the field.
Today, the data seems to show that as more AEC professionals get increasingly familiar with BIM — and as they learn the skills required to build virtually — productivity gains are starting to be realized.
With artificial intelligence (AI) on the scene, models should become increasingly useful and easy to use, too. For example, deploying AI for 4D BIM may better optimize scheduling and do so in an automated way, making life easier for the team coordinating the project.
Similarly, evolving technologies like AR and reality capture introduce new ways to deploy BIM. The use cases for building information modeling will likely increase significantly over the next decade and beyond.
Today, the construction industry is in its early stages of BIM adoption. As more teams integrate building information modeling — and their personnel develop skills in using these processes — the resulting models should drive safer, more predictable projects that create buildings faster with less rework and less waste.
Was this article helpful?
Thank you for your submission.
96%
4%
You voted that this article was . Was this a mistake? If so, change your vote here.
Scroll less, learn more about construction.
Subscribe to The Blueprint, Procore’s construction newsletter, to get content from industry experts delivered straight to your inbox.
By clicking this button, you agree to our Privacy Notice and Terms of Service.
Categories:
Tags:
Written by
Dave McCool
Dave McCool is a Director of Product at Procore and author on BIM and construction tech. He holds a master’s degree in engineering, DBIA, and LEED accreditation, but has realized that his BS in psychology is much more useful in the construction industry than any of the other credentials. Dave has a background of over 9 years of BIM management and coordination experience at McCarthy Building Companies and Brasfield and Gorrie, and is the co-author of BIM and Construction Management: Proven Tools, Methods, and Workflows — a complete integration guide for implementing BIM in construction. He has lectured at multiple university and industry events, and has held chair positions for both AIA and NBIMS committees. He is also a co-founder of Virtual Builders. Originally from Alabama, he now lives in Los Angeles, where he enjoys the sunny weather, trying to surf, and playing music on the weekends.
View profileDJ Phipps
12 articles
DJ Phipps has spent over two decades working in the building and design industry. He's dedicated to using technology to make work easier and more efficient, with a focus on project management and improving systems. DJ now plays a key role at Procore as a Senior Principal Strategic Product Consultant.
View profileKacie Goff
66 articles
Kacie Goff is a construction writer who grew up in a construction family — her dad owned a concrete company. Over the last decade, she’s blended that experience with her writing expertise to create content for the Construction Progress Coalition, Newsweek, CNET, and others. She founded and runs her own agency, Jot Content, from her home in Ventura, California.
View profileExplore more helpful resources
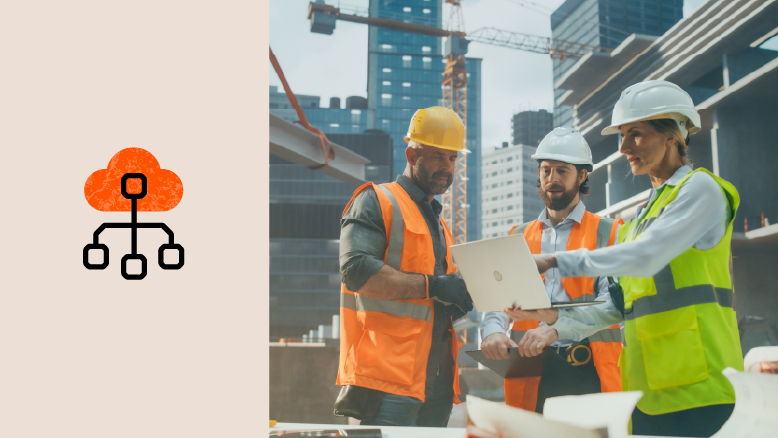
Guide to the Common Data Environment (CDE) & BIM
BIM isn’t just a 3D model. As its full name — building information modeling — suggests, BIM encompasses processes, too. It’s a wide-ranging digital effort designed to drive wins on the...
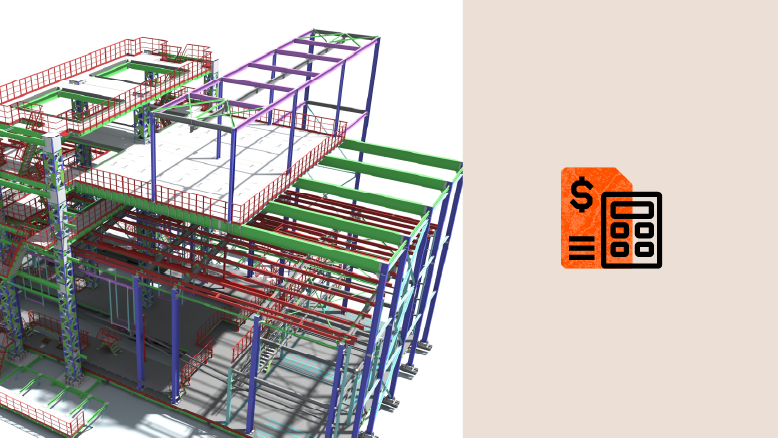
BIM for Construction Cost Control & Budget Management
As the construction industry advances in its digital transformation journey, building information modeling (BIM) is becoming increasingly common. Teams and individuals who push back against using the 3D model and...
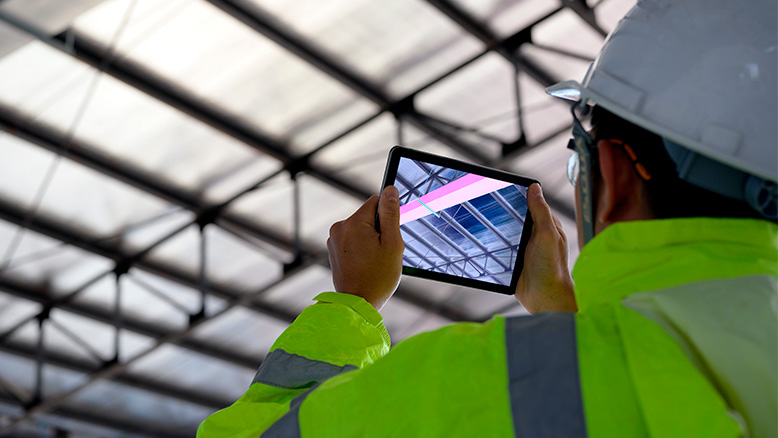
How to Use Tech to Keep Construction Clash-free
Construction professionals are leveraging technology to make clash detection work smarter, not harder. With cloud-based platforms and sophisticated software, they are not only spotting clashes —they’re averting and resolving them...
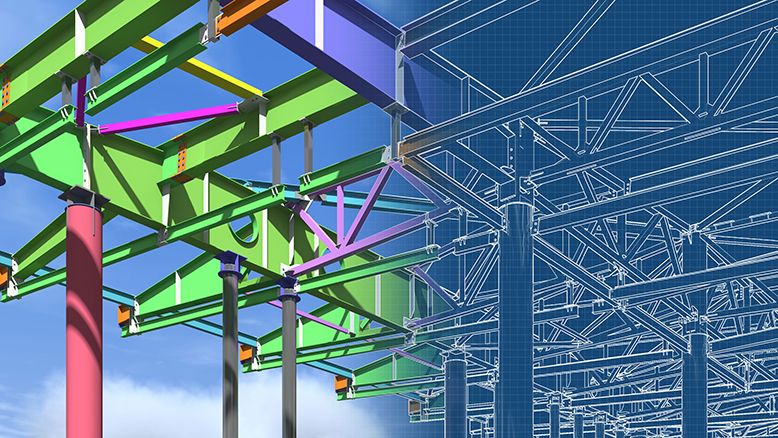
BIM’s Role in Risk Mitigation: Strategies for Success
Building information modeling (BIM), has been touted as a way to deliver a broad range of wins on any construction project. It supports stronger planning and smoother collaboration. It provides...
Free Tools
Calculators
Use our calculators to estimate the cost of construction materials for your next project.
Templates
Find a template to help you with your construction project tasks.
Material Price Tracker
Get the latest U.S. retail prices and view historical trends for common building materials.
Glossary
Explore key terms and phrases used in the industry.