— 8 min read
Construction Delivery Methods Head to Head: CMAR vs. Design-Build
Last Updated Aug 13, 2024
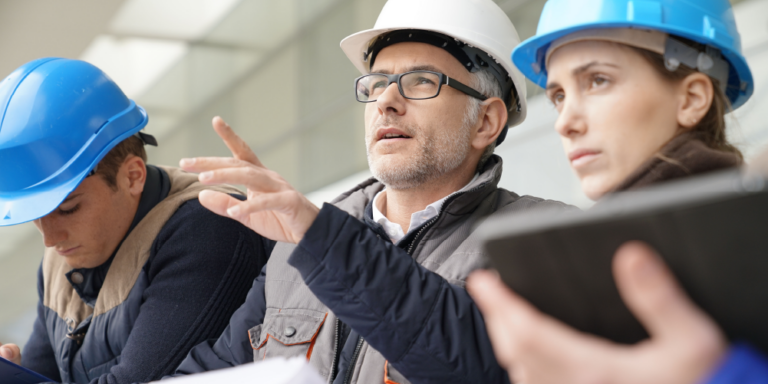
Project delivery methods dictate the roles and responsibilities of project stakeholders throughout the design and construction of a new build. Which method owners choose depends on many factors, including the owner’s skillset and comfort level with the building process, and the specifics of the project at hand.
Two popular project delivery structures, design-build and construction manager at risk, offer benefits and challenges to the stakeholders on a construction project, and there’s a number of factors owners must consider when selecting one for their projects.
Owners should evaluate their own skills, abilities, and willingness to be heavily involved, and the risks they’re okay with shouldering.
In this article, we'll examine the two popular methods, and help owners choose which might work for their next project.
Table of contents
Understanding Construction Manager at Risk (CMAR)
The CMAR method is sometimes referred to as CM/GC, because it effectively combines the construction manager and general contractor into a single role.
When using CMAR, the owner contracts a design firm to help begin the design process for a new project. Soon after the the design process begins, the owner brings in the construction manager to consult on the design plans. This early collaboration presents benefits for both the owner and construction manager.
The owner gets added expertise from an experienced pair of eyes. Together, the owner, designer, and construction manager can eliminate many design errors, optimize the project schedule, and balance the owner's wishes and desires with the desired budget and timeline.
Meanwhile, the contractor gets to spend time with the design to fully understand all of its elements, the site makeup, and other conditions that could impact construction.
Once the design is complete, the owner puts it out for bids. The CM who consulted on the project is not necessarily the one who wins the bid; however, additional time with the design (which could lead to a more competitive bid) and history with the owner does make it more likely that the consulting CM will go on to complete the build.
The owner and the CM then enter into a contract to build the project. The contract will often set out a guaranteed maximum price (GMP) for the owner, which takes much of the risk from the owner and places it onto the construction manager.
CMAR projects may be split into multiple phases, so construction can begin on one phase even before the design of the next phase is complete. In this way, CMAR can reduce project timelines compared with the traditional DBB method.
Stay updated on what’s happening in construction.
Subscribe to Blueprint, Procore’s free construction newsletter, to get content from industry experts delivered straight to your inbox.
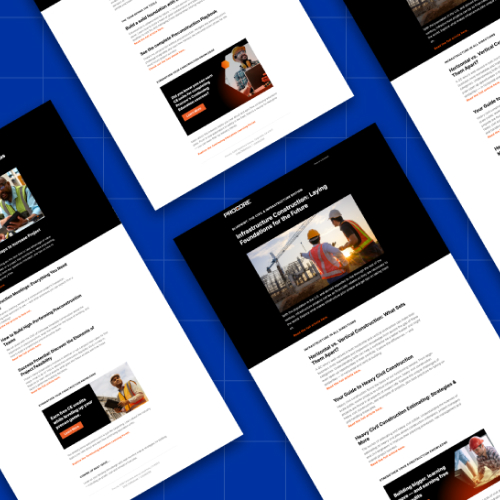
The Benefits of CMAR
While relatively new, CMAR has become quite popular for owners for a number of reasons. Below are some of the factors that make this project delivery structure a favorable choice.
Added input to construction design
CMAR allows contractors to get a concentrated early look at, and influence, over construction designs. The added expertise a CM brings to the design process can help avoid some challenges and change orders during construction, and even result in a better quality build.
Bidding advantages
CMAR allows contractors to get more time and in-depth knowledge of the design, which can inform a more specific and possibly more competitive bid. A better bid means more potential savings for the owner and better chances of winning the project for the contractor.
Cost certainty for the owner
Because construction managers provide a GMP to owners in the contract in the construction documents, owners may benefit from a lowered financial risk level if the project costs go over budget.
The Cons of CMAR
Contractors are pushing for wider use of the CMAR method because of the added input they get into design and the edge they get in bidding a project. However, there are also downsides the CM must consider when joining this type of project method.
Greater risk for the CM during construction
The construction manager on a CMAR project takes on a great deal of risk. The guaranteed price leaves the CM on the hook for any extra costs resulting from surprise site conditions, materials procurement delays, or regulatory changes that necessitate a late change in design.
Prolonged construction timeline
If the owner has split the project into multiple phases, CMAR may offer the CM the opportunity to overlap design and construction to save some time. But the sequential timeline CMAR projects follow can't compete with the time savings the DB method offers.
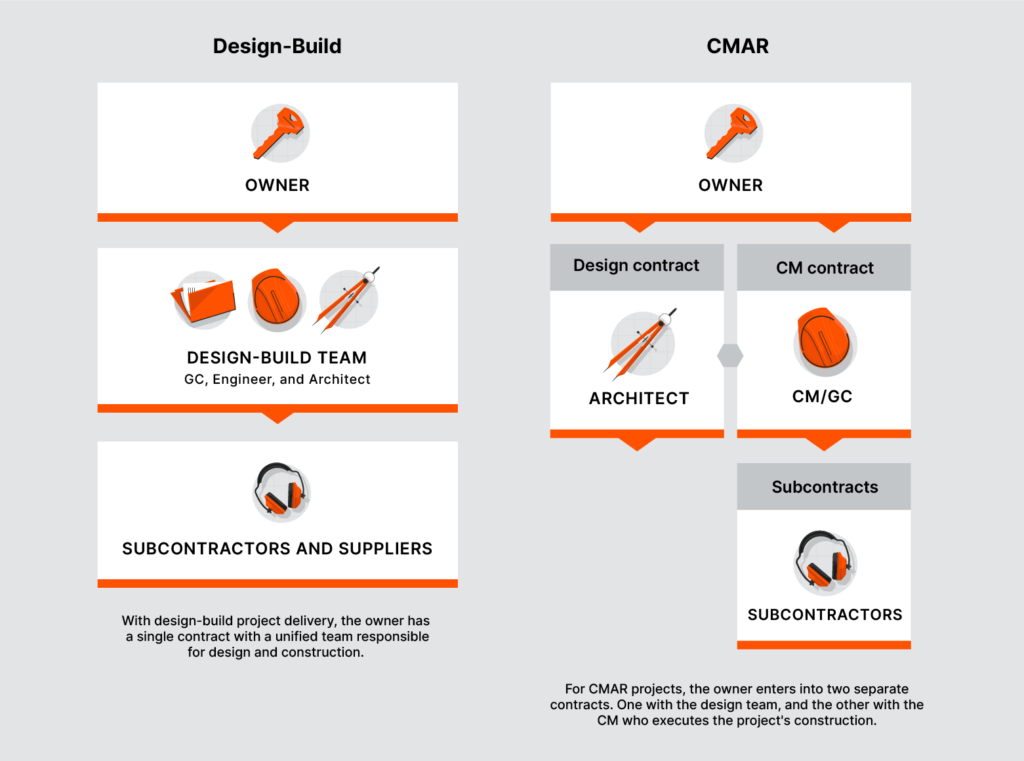
Understanding Design-Build
The design-build delivery method has been around for a long time, and thanks to its collaborative nature and ability to deliver projects with a highly compacted schedule it’s experiencing a resurgence in certain regions. Nearly half of all projects in the US are now delivered using the design-build delivery method.
An owner who chooses design-build will begin project conception, feasibility, and site selection in consultation with a design-build team. Once a project design and cost estimation has begun, the owner will issue a request for proposal (RFP), often only sending it out to select proposers.
With CMAR, the owner selects a design-build team based on both the project quote and the value that the design-build team can offer to the project.
The design-build firm the owner hires will then take over and complete the design process, and firm up the work's scope, schedule, and budget. Then, throughout the construction phase, the design-builder will handle all subcontracting, materials procurement, daily project management, and owner communications.
Design-build has two benefits for owners willing to loosen their grip on the project reins: it gives the owner a single point of contact, reducing the owner's administrative burden through project completion, and offers the potential for faster project completion.
The Benefits of DBB
Much like CMAR, design-build brings project stakeholders together earlier than other project methods. However, DBB organizes roles and responsibilities differently to offer unique features and downsides.
A compacted schedule
One of the best-celebrated features of design-build is its ability to deliver projects in a much shorter time frame compared with many other models. Because the design-build team is a single unit, it can begin construction on parts of the project even while design efforts for later phases are ongoing. Pulling double-duty can allow the DB team to shrink a project schedule from two decades to just five years.
Increased collaboration
The general contractor in charge of construction by the DB method is involved right from the beginning. The contractor can lend expertise and experience to the design process that could contribute to fewer problems during construction, and even a more efficient and cost-effective build overall.
Lower owner risk
Because the design-build team has the project right from the starting line, it accepts much of the risk for both the design and construction phases. Any extra costs fall to the design-builder, whether from rework due to design flaws, construction delays, or any other unexpected issue. The owner also has a single point of contact from whom to get project updates.
Disadvantages of Design-Build
The DB method can be a great option for owners looking to streamline and simplify the project process. Potential downsides have a lot to do with communication between project stakeholders.
Owners have less control
Owners who choose the DB method remain involved throughout the project but are no longer the conduit of information between other project stakeholders.
Further, owners have less transparency into individual project costs when they price out a combined DB team, compared with pricing design and construction individually.
Increased risk for the DB team
The other side of the coin is that DB substantially increases risk for the design-build team. The level of this risk depends on the level of cooperation and collaboration between designers and builders within the team.
The design-build team can be made up of the owner's selection of architect, engineer, and contractor, who will then become a unified design-build entity, or the owner may choose a single firm that chooses its own partnering members.
Regardless of the owner's selection process, the team bands together to become responsible for project delivery. If the firms are well-matched, the project experiences all the potential benefits of DB, but if collaboration is lacking and the construction team takes issue with the designs, those risks can become elevated.
Similarities between CMAR and Design-Build
The CMAR and DB project delivery methods have a few things in common:
- They both involve getting the contractor involved early in the design process
- That early involvement can improve design and reduce changes in design once construction has begun
- They may both involve some design and construction overlap, though DB has the best chance of significant schedule compression
The owner in a DB project must be comfortable handing over a project and releasing both risk and input over to the design-build team. Design-build excels at delivering complex builds with a reduced timeline. Completing the design on large and complicated projects can be a long and arduous process – DB allows construction to begin while designers hammer out later phases.
The CMAR construction delivery method will be a better fit for owners who wish for more control over a project's design. While owners often wonder whether CMAR will lead to overpriced bids because of the transferred risk to the CM, the broader and deeper knowledge the CM has of the project's design can actually lead to more precise bidding and lower costs.
In the end, the decision between CMAR and DB methods comes down to the owner's comfort level with managing a project, and the desired timeline for the project's completion.
this is part of the series
Project Delivery Methods
Was this article helpful?
Thank you for your submission.
100%
0%
You voted that this article was . Was this a mistake? If so, change your vote here.
Scroll less, learn more about construction.
Subscribe to The Blueprint, Procore’s construction newsletter, to get content from industry experts delivered straight to your inbox.
By clicking this button, you agree to our Privacy Notice and Terms of Service.
Categories:
Written by
Alex Six
13 articles
Alex Six is an Enterprise & Strategic Civil & Infrastructure Overlay Account Executive for Procore. Alex has a long background in the construction industry beginning with an internship with one of the biggest contractors in the world, and expanding across projects with teams as small as 4 people and as large as multi-billion dollar budgets with large teams and disciplines. His resume includes Caltrans highways & bridges, Metro light rail & underground, as well as airport runways and utilities.
View profileKristen Frisa
85 articles
Kristen Frisa is a contributing writer for Procore. She also contributes to a variety of industry publications as a freelance writer focused on finance and construction technology. Kristen holds a Bachelor of Arts in Philosophy and History from Western University, with a post-graduate certificate in journalism from Sheridan College. She lives in Ontario, Canada.
View profileExplore more helpful resources
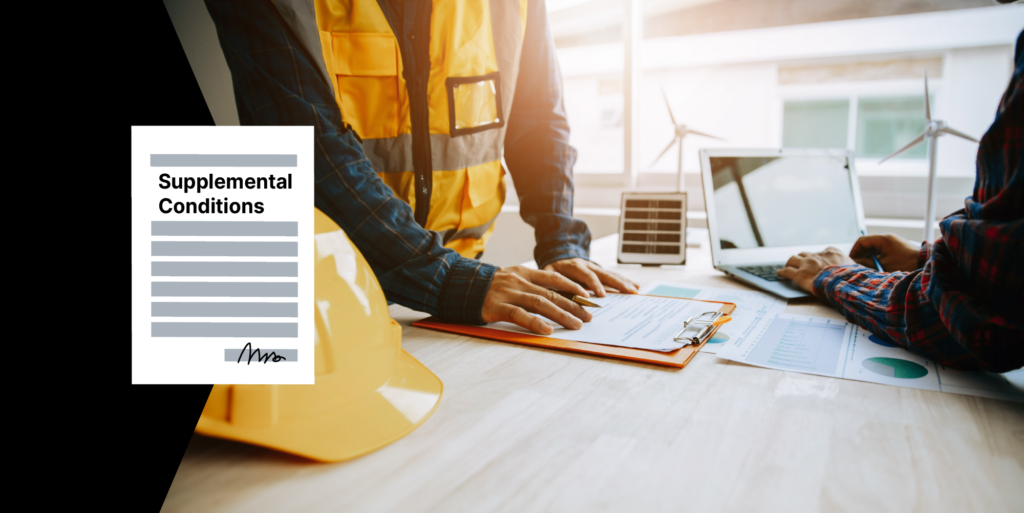
Understanding Supplementary Conditions on Construction Contracts
No two construction projects are exactly alike — and the same goes for construction contracts. Even when using a standard contract form, owners and contractors sometimes use supplementary conditions to...
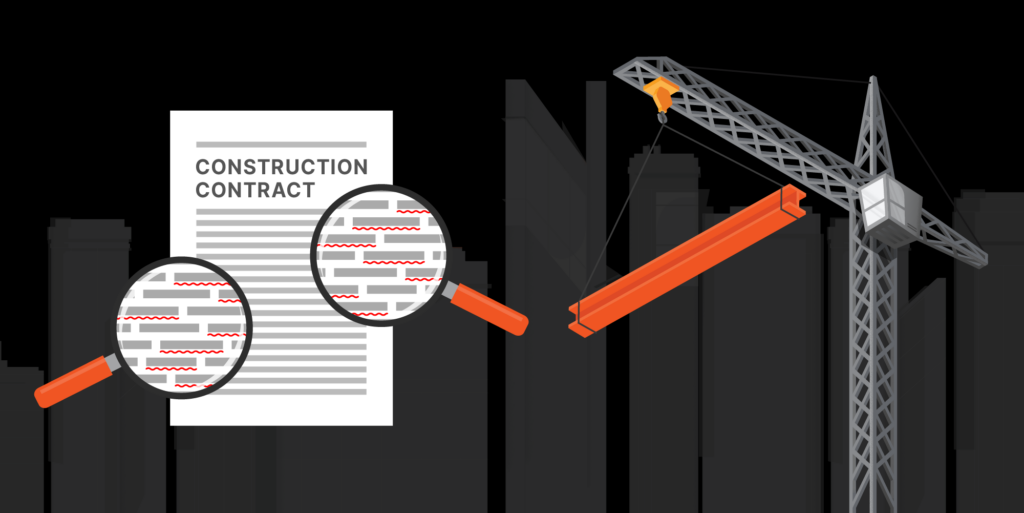
A Straightforward Guide to Construction Contract Review
Construction contracts are like the glue for the project team. They’re the ties that bind the working relationships and goals for the project, containing information about responsibilities, liabilities and processes...
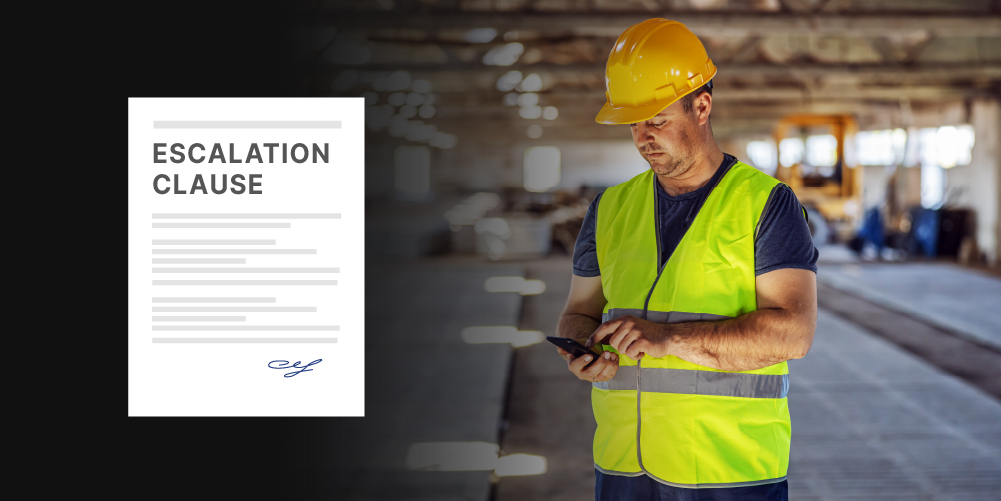
Escalation Clauses in Construction Contracts: When and How They Apply
In construction contracts, an escalation clause allows for the escalation of a certain price for labor or materials to be used in a construction project. This type of clause is most...
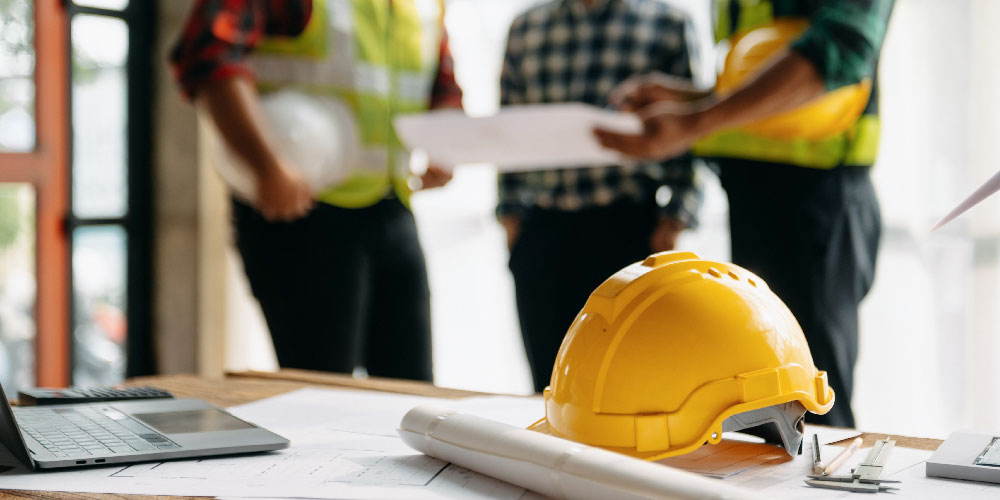
Scope Gap: Addressing Ambiguous Project Requirements
To turn contract documents into an actual building, every construction project requires stakeholders to complete certain items of work. Ideally, the scope of work outlines those items and clarifies who’s...
Free Tools
Calculators
Use our calculators to estimate the cost of construction materials for your next project.
Templates
Find a template to help you with your construction project tasks.
Material Price Tracker
Get the latest U.S. retail prices and view historical trends for common building materials.
Glossary
Explore key terms and phrases used in the industry.