— 14 min read
The Ultimate Guide to Managing Commercial Construction Inspections
Last Updated Aug 20, 2024
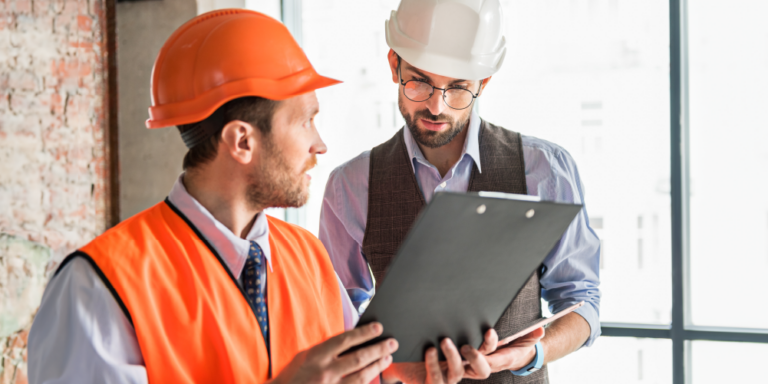
Commercial construction projects require ongoing inspections at almost every point of the building process, from checking the site before construction to the final inspection with a local building authority. Understanding how to conduct, manage, and make the most of these inspections is crucial to completing a project safely, on budget, and at a high level of quality.
Commercial construction inspections are the routine and formal checks of a commercial property during the building process to make sure it’s safe for use, up to code, and is being constructed properly. For contractors and owners alike, effective inspections throughout construction means the final inspection, and closeout in general, is more likely to go smoothly and have as few surprises as possible.
In this article, we will explore the various types of commercial construction inspections, how they fit into the construction process, and how to make the most of them.
Table of contents
Types of Commercial Inspections
Every piece of work that goes into commercial construction needs to be checked, sometimes more than once. “Commercial inspection” can refer to any time a quality check is done to a commercial construction project. Whether it’s a general contractor verifying drawings or a third-party specialist checking a roof after installation, the goal is make sure elements will be safe for use, a good investment for the owner, and completed with workmanship the contractor can stand by.
Below are common types of commercial construction inspections:
Pre-construction Inspections
Inspections begin before ever breaking ground. Before commercial construction, a series of checks should be done to ensure everything is ready and to minimize surprises that pop up during the build. This might include a general contractor and the design team inspecting conditions on the building site before construction or a specialist checking rebar, form work, and the vapor barrier before concrete is poured.
Routine Inspections
Throughout construction, a general constructor should complete informal inspections at least daily to monitor progress. This is generally to check that newly installed elements were put in correctly, follow building plans, and will ultimately pass more formal inspections later on. These inspections also look to catch problems as early as possible, when they’re easier to fix and haven’t been repeated in other parts of the build. Examples of common routine inspections include evaluating the first few installed windows, checking a newly completed section of roof after a storm, or simply walking the jobsite at the end of every day.
While these inspections are crucial for quality control, they can also help improve the construction process as a whole, by helping to do things such as identify potential schedule delays, prevent onsite accidents or injuries, and improve productivity.
GCs should keep checklists handy to help streamline the routine inspections process, and ensure nothing falls through the cracks. It’s important to have the correct types of checklists onsite, whether it’s a thorough “read-do” checklist that requires many steps to follow, or a “do-confirm” checklist with critical items GCs should remember to keep an eye on. These, along with daily logs, should be updated daily to keep the project flowing smoothly.
Rough Inspections
Rough, or rough-in, inspections are early checks to important systems, such as electrical, mechanical, plumbing, or fire safety. Usually, these happen when important elements of the system, such as an electrical box or water lines, have been installed but before walls have been put up and closed them in. Many municipalities require rough inspections to close work permits. This helps inspectors check elements before they are closed off and difficult to fix. Some places, like Florence, Oregon, provide a list of rough-in inspections with a description of when they should be conducted. Other places, like Nassau County in Florida, will provide a checklist of the things they will check at some rough inspections.
Post-construction Inspections
Most parts of a building should be inspected after they’ve been completed, but before the final inspection of the whole project. This helps make addressing issues more manageable and avoid the final inspection ending with a long list of problems.
These inspections are often done by a licensed inspector from a municipality. The same inspector who did the rough-in will often do the post-construction inspection, which gives them a more thorough understanding of the project’s progress and quality. For example, the fire marshal might be out every time before walls are closed in a building and then again to check the whole system when it’s completed.
Many places require post-construction inspections to close work permits. Which inspections are required depends on the building and where it’s located. Some places, such as Chesapeake, Virginia, provide a list of required inspections and when they should be done. Below are examples of common post-construction inspections:
- Roof
- Concrete
- Foundation and footing
- Mechanical
- Electrical
- Plumbing
- Framing
- Soil
- Insulation
- Steel
- Masonry
- Energy efficiency
- Walls
- HVAC
- Fire safety
Punch List Inspection
The general contractor and owner (or owner’s representative) will almost always do a walkthrough after construction to decide whether a building is substantially complete. These inspections ensure every part of the project is ready to be handed over to the owner and often focus on finishing details, such as painting, flooring, or countertops. The punch list consists of the items found in this walkthrough and is usually required to be completed and submitted with closeout documents.
Learn more about best practices to help simplify the punch process.
Final Inspection
The final inspection is conducted by a local zoning authority or building department to check that a building fully complies with codes and regulations for usage and safety. It can feel like one of the highest stakes parts of construction, as it’s usually the last step to obtaining a certificate of occupancy and is done after all work has been completed, permits have been closed, and other inspections have been conducted.
Inspections Before Purchasing a Commercial Building
Commercial properties are almost always thoroughly inspected before being purchased, whether the owner plans to use the building as soon as possible or renovate it to sell again. Usually, a third-party inspector will evaluate the building to assess its condition and determine the extent of required work. Sometimes, a manufacturer that issued a warranty for part of the building will send a representative to be part of these inspections.
Design Inspections
The design team might be called on throughout construction to inspect parts of the building. Specifically, architects might be asked to ensure elements comply with all building codes and engineers might be asked to ensure everything was installed properly. Some places, such as New York City, require members of the design team to conduct regular progress inspections.
Government Inspections
Typically, a municipality will want to check any part of a commercial building that might impact the safety of the people and the place they’ve been charged with looking after. This might include in-wall insulation inspections before sheetrock is hung, above ceiling checks of wiring, or in places like Houston, ensuring drainage and landscaping adheres to special floodplain regulations.
Most local building authorities have licensed inspectors they send to do required inspections. This often requires planning ahead to coordinate with the municipality or inspector and adds pressure to pass the inspection the first time. Contractors should factor these government inspections into their timeline and familiarize themselves with what inspections will cover in order to avoid surprises and potential delays.
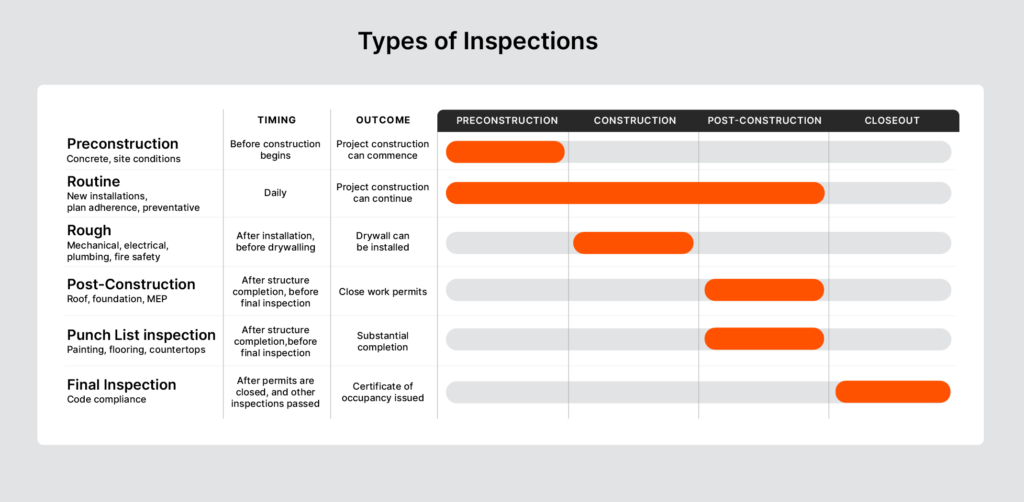
Conducting Commercial Construction Inspections
Different types of inspections are completed by various people throughout the process. For example, routine inspections are often done by a general contractor and the final walkthrough is often done by the GC and the owner or owner’s rep.
However, most inspections require some type of third party to give a specialized and impartial evaluation. This could be the municipality on required inspections or someone hired by the contractor to check everything is satisfactory and identify issues to be fixed. A common example happens with concrete inspections, which usually involve a general contractor hiring a third-party to be onsite during the pour and to conduct break tests.
Items and Systems Reviewed During Inspections
The focus of an inspection depends on who’s doing it and its purpose. In most cases, the items and systems to be reviewed are clear, such as looking at the air conditioner during an HVAC inspection or electrical boxes during the electrical inspection. However, cumulative inspections, such as post-construction or the final, focus on all parts of the project.
Here are things commonly looked at during a full commercial construction inspection:
- Final construction matches approved plans and compiles with building codes
- Structural components, including walls, floors, roof, or other parts of the building’s envelope, are complete, sealed from water, and, when applicable, can be opened
- Electrical, plumbing, and HVAC are working and installed properly
- Fire safety systems are working and can be tested
- The building meets all accessibility standards and laws, as outlined by the ADA
- Exterior features, such as parking, drainage, and landscaping, match approved plans and meet building codes
- Handrails and guardrails for stairs are in place and at the correct height
- Required exits are in place and unhindered
- All signage is in place and visible
Responsibilities During Inspection
General Contractors
General contractors usually view all parts of construction as their responsibility, and inspections are no different. GCs should conduct most routine inspections themselves. They also usually schedule inspections with third-parties, which requires a thorough command of a project’s timeline. They often follow along with an inspector to answer questions and get a better understanding of any issues.
GCs are usually in charge of collecting and providing all necessary documentation. Commonly, they should have an organized photo album with pictures of all elements throughout the project, especially those that have been enclosed by a roof or wall. If an inspector has a question about a particular system, the GC will want to quickly have an answer and proof of proper installation.
Owners
Throughout the inspection process, owners and owner’s representatives are concerned with making sure the project will ultimately be able to fulfill its intended use. They usually focus on making sure elements look good and function properly.
For most privately owned commercial buildings, an owner or their rep will periodically visit a jobsite to verify construction is being done according to plan and their expectations. For punch list inspections, an owner or their rep is an important part of evaluating the project and compiling a list of anything that still needs to be done. In some cases, such as commercial buildings owned by the federal government, owner’s reps or engineers are usually required to be part of all inspections.
Sellers and Buyers
Commercial buildings are often undergoing renovation to be prepared to be sold. In these cases, owners or prospective owners are usually invested in ensuring that work is done correctly and won’t result in unexpected expenses later on. They will often hire third-parties to conduct inspections on their behalf to make sure work is done properly, on budget, and on time.
Architects and Engineers
The extent of a design team’s role in inspections is generally stipulated in their contracts. Much of their work is done long before post-construction or final inspections. However, they are often called on throughout the project to inspect parts of the building on behalf of the owner or, in some places, because design teams are required to do so by local municipalities. Architects will generally be asked to check that construction complies with building codes and meets accessibility regulations. Engineers will often be asked to ensure elements were installed properly and will work as intended.
Preparing for a Commercial Inspection
Most work to prepare for an inspection is done long before the inspection takes place, particularly when preparing for post-construction and final inspections. However, there are some things that usually make all inspections more effective and impactful:
- Documentation: Having all necessary documents on-hand can greatly improve any inspection. This might include building plans, proof of passing previous inspections, work permits, or reports such as a concrete break test or a start-up on a drainage system.
- Pictures: Have an organized photo album of all parts of the build. This helps a GC’s ability to answer any questions that arise, especially about things that might be enclosed by a wall or roof. Photos can save time and confusion that might result in having to undo or redo any work.
- Conduct routine inspections: Checking a project on a daily, or multiple times a day, basis will ensure issues are caught early, are easier to fix, and don’t involve an inspector making numerous trips to a jobsite to ensure problems were addressed.
- Plan ahead: Have a detailed outline of the milestones needed to be hit throughout construction. This can help ensure inspections happen at the right time and don’t hold up other parts of the project.
Commercial Inspections vs. Residential Inspections
Inspections should generally be approached with the same level of diligence and urgency, regardless of whether it’s a towering office building or a small family home. In all inspections, lives and resources are on the line, and detecting potential problems can have major implications for a project’s safety, timeline, and budget.
While owners, contractors, and inspectors should approach all inspections with a similar mindset, the listed requirements for a commercial structure might be more rigorous or lengthy than those for a residential building. Similarly, commercial buildings are more likely to have specialized systems, which might require specialized inspections such as a medical gas inspection in a hospital. City government websites, like Pittsburgh’s, provide lists of required inspections for different types of buildings and can show how many more inspections might be required for a commercial building than for a residential one.
For both types of buildings, obtaining a certificate of occupancy usually requires a final inspection by a municipality. However, with residential inspections, architects and engineers are often less involved, or potentially not involved at all. Their involvement is rarely required for residential inspections, as residential buildings are more likely to be duplicates of a structure that’s already been successfully built and requires less adjustments.
Post Inspection Next Steps
Receiving Inspection Report Results
Return times on reports generally depend on the municipality doing the inspection, though most come back between 24 to 48 hours. Most inspectors and municipalities understand the intense timelines which contractors and their teams are facing and the potential costs of a delay, so they are usually prompt in getting results back.
Understanding the Inspection Report
Municipalities and inspectors understand contractors are balancing an immense number of variables and time considerations. They will usually make inspection reports easy to understand. The report will, when it applies, state if an inspection was passed or failed, and usually have a straightforward list of issues to be addressed.
However, when possible, GCs should usually try to join the inspector during the inspection and take notes. This can help GCs get a jumpstart on addressing problems and GCs can provide inspectors with information such as area names, door numbers, or room numbers that make for more detailed and easier to understand reports.
Stay updated on what’s happening in construction.
Subscribe to Blueprint, Procore’s free construction newsletter, to get content from industry experts delivered straight to your inbox.
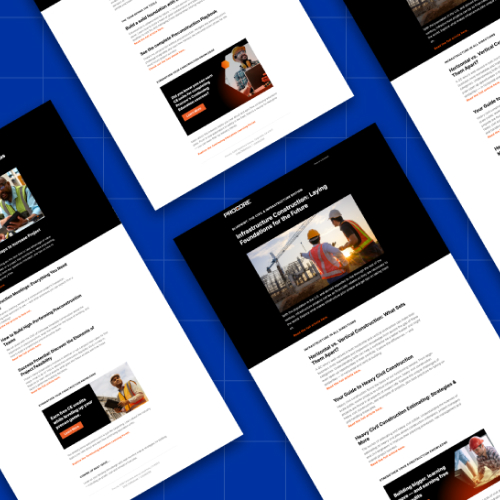
Pass vs. Fail: What Happens Next?
If an inspection is passed, what happens next is pretty simple: proceed to the next stage of construction, whether that’s the next part of building or applying for a certificate of occupancy.
What happens after failing depends on the issue found and the timeline needed to fix it. If the final inspection finds the building is not safe to occupy, the inspector might simply say the building isn’t ready and instruct the contractor to call them back when it is. Generally, this type of result shouldn’t be a surprise to the GC and it’s generally best practice to only schedule inspections when it’s likely a building will pass.
In some cases, a temporary certificate of occupancy (TCO) can be obtained, which will allow the building to begin being used while certain, non-life threatening issues are addressed. TCOs usually last for about 30 days, at which time the inspector will usually return to check all issues have been resolved. If the building’s problems aren’t addressed, some inspectors will close the building altogether.
Improving Closeout Through Commercial Construction Inspections
Conducting and managing effective commercial construction inspections can mean issues are caught as early as possible, are easier to fix, and aren’t repeated throughout building. This improves the chances that the final parts of construction, specifically closeout and the final inspection, are less likely to have surprises, are easier to manage, and feel more like a formality on the path to owners being able to receive a return on their investment and contractors being able to fully turn their focus towards the next project.
Was this article helpful?
Thank you for your submission.
100%
0%
You voted that this article was . Was this a mistake? If so, change your vote here.
Scroll less, learn more about construction.
Subscribe to The Blueprint, Procore’s construction newsletter, to get content from industry experts delivered straight to your inbox.
By clicking this button, you agree to our Privacy Notice and Terms of Service.
Categories:
Written by
Ryan Nash
Ryan Nash is a Field Team Leader at RNGD, delivering safe, efficient, and quality commercial construction projects in greater Nashville. Since he joined the company as Superintendent, he has successfully delivered multiple $100M+ projects on schedule and within budget. Throughout his 10+ years in the industry, he has developed a cost-saving mindset, expertise in navigating complex challenges, and commitment to a safety-first construction site. Ryan holds a Bachelor of Science degree in construction management from Southeast Missouri State University. He lives in Nashville.
View profileJames Hamilton
70 articles
James Hamilton is a writer based in Brooklyn, New York with experience in television, documentaries, journalism, comedy, and podcasts. His work has been featured on VICE TV and on The Moth. James was a writer and narrator for the show, VICE News Tonight, where he won an Emmy Award and was nominated for a Peabody Award.
View profileReviewed by
Dave Brown
Dave is a Senior Strategic Product Consultant for Procore, specializing in General Contractors. Previously, he worked for Consigli Construction Co in Boston and Washington, DC as a Project Engineer and Assistant Project Manager, responsible for a variety of activities including bidding and procurement, contracts, and cost control. Dave holds a Bachelor's Degree in Structural Civil Engineering from Bucknell University.
View profileExplore more helpful resources
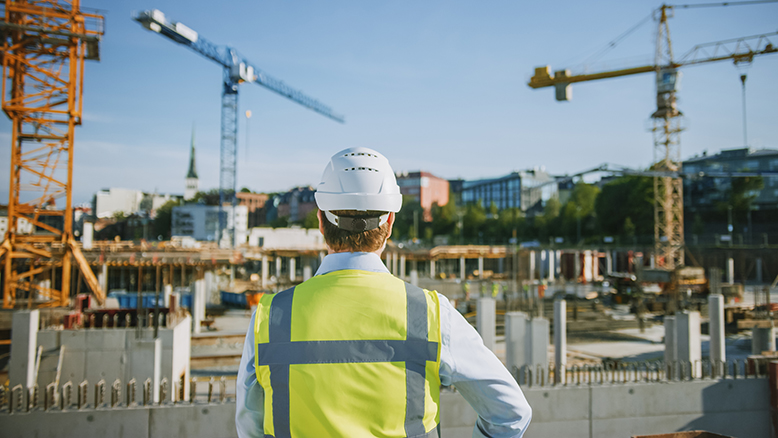
Commercial Construction Management: Mastering the Basics
Commercial construction management is no small feat: Commercial projects tend to be large and complex, and unlike residential construction, which involves repeatable tasks, can involve industry-specific and technical aspects. Commercial...
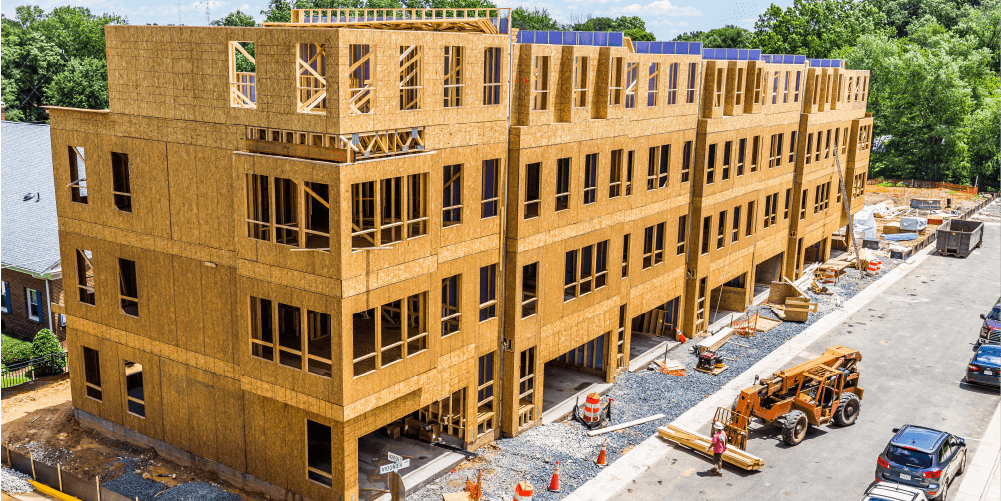
6 Types of Construction Projects: Key Differences for Owners & Contractors
Construction projects are often categorized based on their scale, the types of structures being built, and the purpose of the project (also called “end use” or “land use”). Broadly, there...

How BIM Software Supports Construction Teams in the Field
Gaps between project design and field execution can cost a lot of money. Architects can create beautiful designs, but if the foreperson and trade crews don’t have access to the...
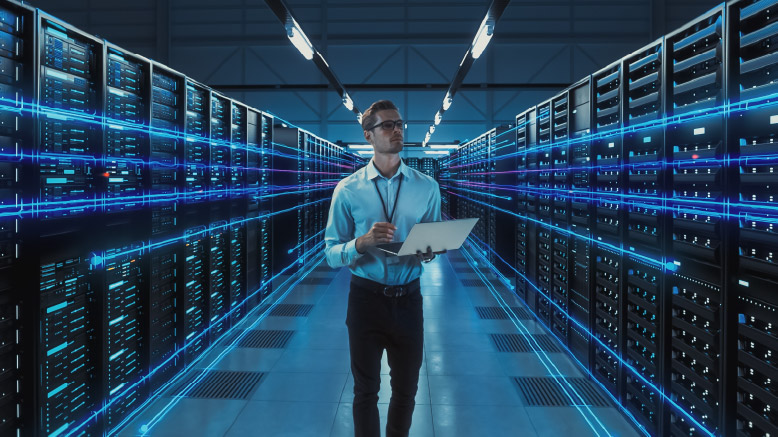
Mission Critical: Delivering on the Demand for Data Centers
Unprecedented growth in the data center market has created enormous pressure on industry stakeholders to keep pace. The need to quickly build hyperscale data centers to support modern applications demands...
Free Tools
Calculators
Use our calculators to estimate the cost of construction materials for your next project.
Templates
Find a template to help you with your construction project tasks.
Material Price Tracker
Get the latest U.S. retail prices and view historical trends for common building materials.
Glossary
Explore key terms and phrases used in the industry.