— 11 min read
The Contractor’s Guide to Concrete Inspections
Last Updated Jun 6, 2024
Last Updated Jun 6, 2024
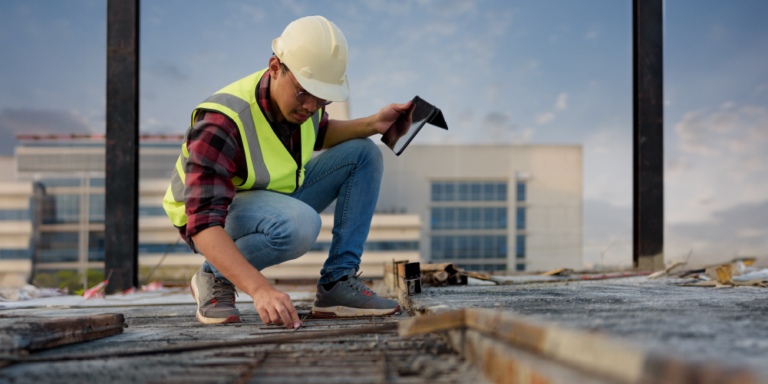
Concrete: It’s the key building block of nearly every structure’s foundation — and it’s the world's most widely used building material.
For most general contractors, understanding how to assess concrete safety, strength, and durability is crucial. One of the main ways that happens is through a concrete inspection.
Concrete inspections test that concrete on a project matches the specifications in the design plan and is going to be safe, strong, and durable over time. Passing the concrete inspection is required for most other parts of construction to commence, so delays can result in the project falling behind, money being lost, or the worksite becoming unsafe.
This article will explore the basics of concrete inspections, including how to prepare for them, what to look for and where they often go wrong.
Table of contents
The Basics of Concrete Inspections
Inspections are usually done by a third-party company that specializes in concrete. The inspector will be onsite for the duration of the pour to collect samples and oversee logistics, including monitoring formwork, verifying design specs, and problem-solving if the concrete doesn’t perform as expected. The general contractor is often responsible for hiring the inspector, though it can also be done by the owner or someone acting on their behalf.
When a building is being designed, concrete is selected based on a number of factors, including the building’s size, how it will be used, local building regulations, and environmental elements the concrete will have to endure. Different types of concrete have unique qualities, including flexibility and, most notably for inspections, strength.
Strength in concrete refers to how much pressure it can endure, which is measured in pounds per square inch (PSI). Each type has a PSI it is expected to be able to handle after a certain amount of curing time.
For example, concrete in a residential driveway is usually required to handle around 3,000 PSI, concrete in a footer would usually need to handle about 4,000 PSI, and concrete in a factory would usually need to clear about 5,000 PSI. Most of the time, a concrete inspection is a series of strength tests done on concrete over time, most commonly in a process called cylinder tests.
What Happens During a Concrete Inspection
Concrete inspections start when a concrete truck arrives on the job site. Samples from each truck are poured into cylinders, which are often made of single-use plastic for large projects that require many samples or, for smaller-scale projects, reusable steel or cast-iron. Most inspections require at least three cylinders from each truck.
These samples are tested to see how the concrete will handle the type of pressure it is expected to face and how much force is required to break it. Because concrete cures and strengthens as it dries, tests are usually done at a minimum of three different times after pouring.
Testing commonly occurs around day 7, 14, 28 or 56. The test on day 28 is often considered the defining test, as it gives a realistic idea of the concrete’s efficacy without delaying other parts of construction, while later tests may be done if design strengths aren’t met.
Other Types of Concrete Inspections
The phrase “concrete inspections” is most commonly and officially used to refer to the strength and performance assessments we’re talking about in this article. However, the phrase might be thrown around throughout the construction process to refer to a few more procedural practices that are similarly meant to ensure a building is safe and ready to use. Here are a few ways other ways the phrase “concrete inspection” can be used:
Engineering
Before pouring concrete, the design team or other structural engineers of record may come to the site to verify certain elements, such as reinforcement, formwork, or height.
Quality and Safety
It’s a good habit for contractors to conduct regular safety and quality control inspections before, during, and after concrete is poured.
For example, before the pour, it’s good to check things such as the placement and size or rebar, formwork, or the placement and size of sleeves and openings. During the pour, a contractor might check the mixture and moisture of concrete and ensure that curing is done correctly. After the pour, contractors should continue to monitor the appearance of concrete, looking for cracking, creeping, or slab curling. Some organizations, such as the International Association of Home Inspectors, will provide lists of things to visually check while working with concrete.
Closeout
By the time closeout rolls around, most of the concrete work should have been completed long ago and everyone should feel confident the building is structurally sound. However, concrete work can sometimes be included as a punch item. For example, if a flooring material that has been attached to the top of a concrete slab starts to bubble up, a contractor would be expected to check documentation or retest the adhesive properties of the concrete. At this late phase, issues are usually treated like one-off problems that need to be addressed before closeout can be complete.
How to Prepare for a Concrete Inspection
The time leading up to a concrete inspection can be stressful simply because of how many variables have to be considered. Here are a few things contractors should be doing to help improve the chances of passing an inspection:
Consider approvals & affidavits.
Before building, a contractor will often submit the list of materials and work plans they have developed based on the original building design. This is received by the building’s designers or engineers, who will usually respond with confirmation or any issues. This type of collaboration and clarification minimizes the risk of error and establishes communication in case something does go wrong.
Often, an engineer will be required to sign an affidavit stating that the structure, including the concrete, was built as it was designed. This affidavit can sometimes be required for parts of closeout, including obtaining a certificate of occupancy. For example, see this Designer’s Affidavit from the town of White Plains, New York.
Stick to local mandates and regulations.
Many towns, cities, and local building authorities will release guidelines and regulations on concrete. These can include important information such as when strength tests need to be done or the minimum weight a piece of concrete should be able to hold. Most municipalities will release these guidelines on their website. For example, see the guidelines for Concrete and Concrete Structures published by the City of Madison, Wisconsin.
Conduct pre-install meetings
A pre-install meeting should cover all critical information about the job and the inspection and should include anyone who might be at the pour or needs information about it. Who is in attendance depends on the project, but people commonly included would be the project manager, the foreman or superintendent and possibly the designer. Time should be allowed for people to raise concerns or ask questions.
Information covered might include the pour schedule, the scope of work, where concrete is and isn’t going, and verifying the type of material being used. Some pre-install meetings will include a specific checklist to ensure everyone is covered. Contractors can find sample checklists on the websites of specialist organizations.
For example, the Alabama Concrete Industries Association recommends that preconstruction meetings for concrete construction include:
- Copies of the specifications & drawings
- Project participants critical to the success of concrete construction
- Contractor’s construction schedule and operations
- Reports of the approved mix designs
- Phone numbers of personnel associated with the concrete construction
- Concrete production and transportation
- Ordering and scheduling
- Concrete testing and inspection requirements
- Reporting of findings of tests and the findings of inspections
- Procedures for testing and re-inspection of reported deficiencies
Review, confirm, & review
Pours happen quickly and often involve a lot of people and variables. Once they’re done, things are quite literally set in stone. Checking and double-checking is always a good idea:
- Review specifications and design documents before the pour and make sure information is easily accessible. We will share more on document management below.
- Confirm formwork, reinforcement, and other equipment/accessories are properly installed. One misplaced frame can lead to a blowout.
- Ask specialized contractors, such as mechanical, electrical, or plumbing, to check that plans, formwork, and placements of sleeves or openings reflect their needs.
Scheduling a Concrete Inspection
Picking the right time to pour is important for passing a concrete inspection and, more importantly, ensuring the work is done well.
Here are a few things to consider.
Weather
Because the water ratio in concrete is so important, some of the biggest considerations should be any weather that would alter the material's state, including rain or extreme temperatures. If heavy rain is expected during an outdoor pour, it is likely better to reschedule than to risk failing the inspection or, worse, the building being unsafe.
Sequencing
A master plan should include the sequence in which concrete work should be done. For example, new concrete poured against concrete that has already hardened can lead to cold joints, which can cause a weakened bond between the pours.
Coordinating with Other Trades
A master plan should account for trades, such as mechanical or electrical, that require a foundation, wall, or slab to be completed before beginning work.
Concrete Curing Times
Different concrete mixtures require different curing times and processes, including maintaining certain temperatures or covering concrete while it cures.
Availability of Required Personnel and Equipment
Have a list of people needed at the pour, including the inspector, to do the job. Accounting for the availability of these people, as well as equipment, can help to avoid work stoppages or delays.
Failing an Inspection
Failing a concrete inspection can make it very difficult to complete a project on time. The good news is that there are often ways to address issues with concrete before resorting to removal, which is likely the most expensive solution.
The general contractor is usually responsible for making sure a solution is found and implemented, even if the issue wasn’t caused by them. One of the first things a contractor can do after a failed inspection is confer with the engineer or designer about how to proceed. Possible solutions could be as simple as grouting, pouring more concrete and dowling it in, or adding additional reinforcement, such as Kevlar. Unfortunately, solutions to a failed concrete inspection are almost always very expensive. Suppliers understand the urgency of repair work and the cost of their products usually reflect that.
Overcoming Inspection Challenges
Working with concrete is hard. Any number of things can cause an error, from too much water to extreme temperatures to sitting in the truck for too long. However, many challenges with concrete inspection can be avoided with planning and a few of these factors:
Communication
It’s important builders and contractors know the plan and all specifics. This is especially true for large projects that involve many people and might take years to complete. Creating systems for documentation and document sharing can address many problems before they ever happen.
Avoid Being Lulled by Repetition
Pouring concrete can seem like it’s truck after truck, pouring the same concrete in the same place, sometimes for hours. One of the best ways to ensure concrete inspections are passed is being diligent: check the contents of every truck, double check structure before pouring, and over communicate.
Document Management for Concrete Inspections
There is no substitute for meticulous documentation, especially when it comes to quality assurance and legal purposes. This is true for most parts of construction, and especially true for concrete.
One of the biggest distinctions between documentation and good documentation is accessibility. Documents can’t help if they can’t be found. Accessible and shareable documentation helps with onboarding new people, verifying plans, and proving all work was done correctly.
The highest stakes reason for documenting everything is for legal purposes. If something goes wrong, a contractor wants to be able to prove they aren’t at fault. But good documentation goes a step further by helping to prevent problems in the first place. Providing information in an organized fashion before and during work is one of the highest impact ways to ensure quality workmanship, avoid delays or extra expenses, and catch issues before they ever become a legal question.
One of the best ways to ensure documentation is organized and accessible is using digital tools, like Procore’s Action Plans. These tools make sure documents are not only stored, but are available to everyone who needs them.
Stay updated on what’s happening in construction.
Subscribe to Blueprint, Procore’s free construction newsletter, to get content from industry experts delivered straight to your inbox.
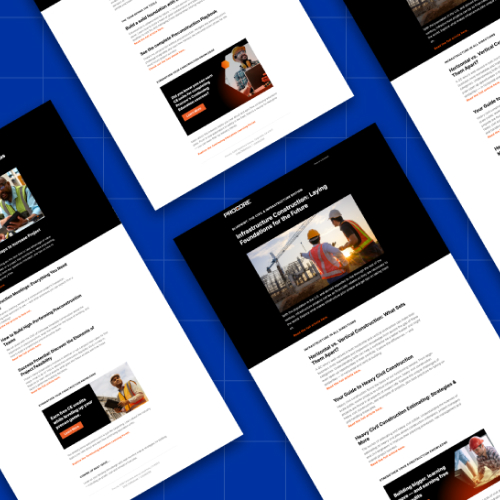
Things to Document
The simple rule is to document everything — but here is a short list of things especially important to document while working with concrete:
- Pour times
- Pour temperatures
- Crew details
- Test results and reports
- Plans and drawings
- Anything submitted to the designer for approval
- Photographs (before, during, and after the pour)
The Secret to Concrete Inspections
Concrete isn’t the most complex part of construction, but it does require some of the most precision. It can also be one of the highest-stakes parts of construction. Understanding how concrete inspections work can improve every part of the building process.
To learn more about some of the other elements and trades impacted by concrete, particularly in regards to closeout of a project, check out our articles on certificates of occupancy and final building inspections.
Was this article helpful?
Thank you for your submission.
100%
0%
You voted that this article was . Was this a mistake? If so, change your vote here.
Scroll less, learn more about construction.
Subscribe to The Blueprint, Procore’s construction newsletter, to get content from industry experts delivered straight to your inbox.
By clicking this button, you agree to our Privacy Notice and Terms of Service.
Categories:
Tags:
Written by
Dave Brown
Dave is a Senior Strategic Product Consultant for Procore, specializing in General Contractors. Previously, he worked for Consigli Construction Co in Boston and Washington, DC as a Project Engineer and Assistant Project Manager, responsible for a variety of activities including bidding and procurement, contracts, and cost control. Dave holds a Bachelor's Degree in Structural Civil Engineering from Bucknell University.
View profileJames Hamilton
70 articles
James Hamilton is a writer based in Brooklyn, New York with experience in television, documentaries, journalism, comedy, and podcasts. His work has been featured on VICE TV and on The Moth. James was a writer and narrator for the show, VICE News Tonight, where he won an Emmy Award and was nominated for a Peabody Award.
View profileExplore more helpful resources
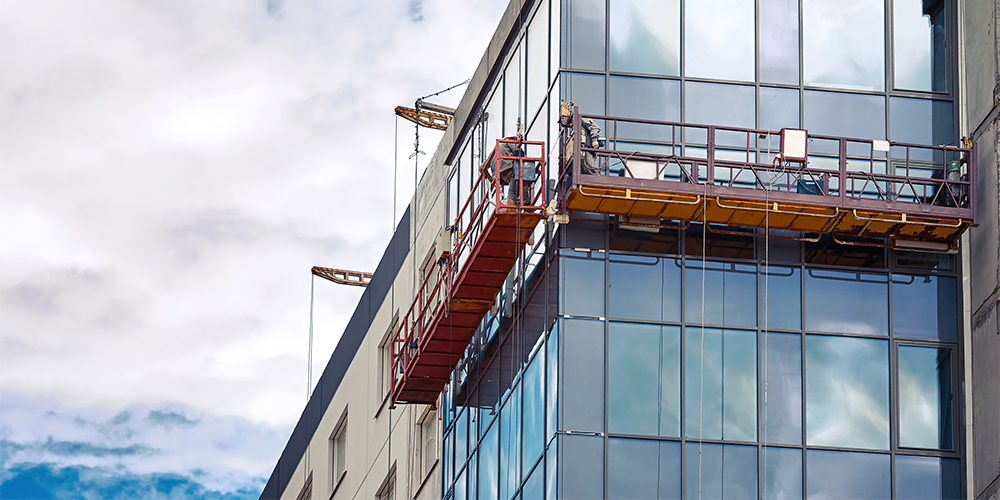
Preparing for Post-Construction: A Guide to the Final Phase of a Project
Large construction projects often take years to plan, more years to design, and even more years to build. From the groundbreak point of view, it’s often difficult to see the...

A Guide to Construction Commissioning
During project closeout, an owner wants to receive any documents, training and warranties needed to take over the management and maintenance of their building. But they also want assurance that...
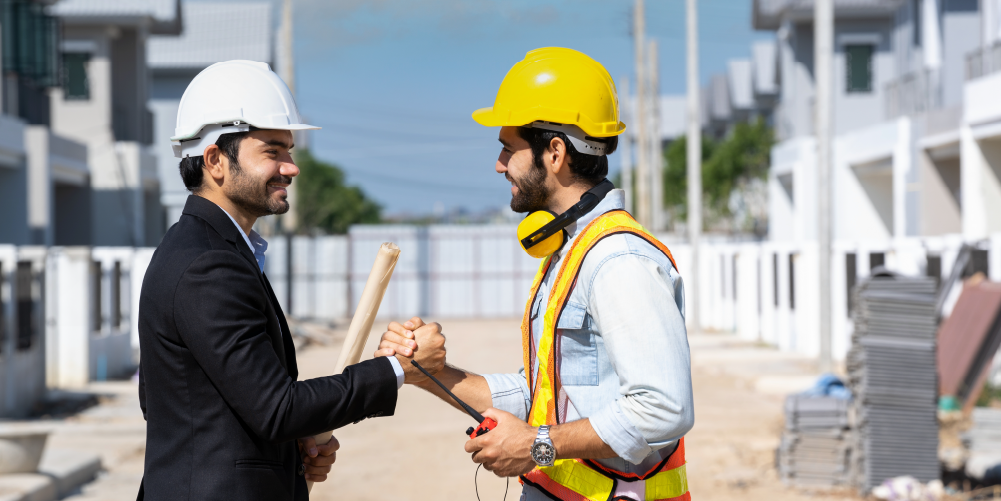
Construction Handover: Keys to an Efficient Process
After the months or years it takes to complete a construction project, the handover process begins. Project handover is the final part of the construction process, where a project, along...

Construction Closeout Documents: What’s Included & Why
Few parts of the building process can feel as stressful and as complicated as closeout: the multi-step, final phase of construction in which a project is prepared to be handed...