— 8 min read
A Guide to Construction Commissioning
Last Updated Mar 13, 2025
Last Updated Mar 13, 2025
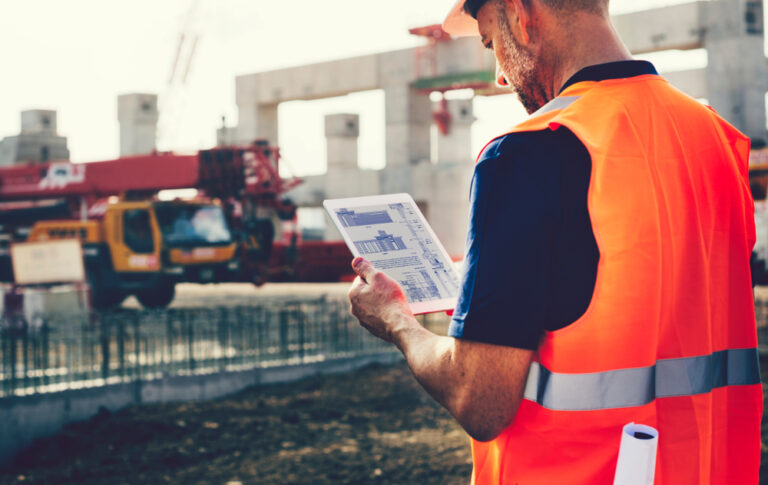
During project closeout, an owner wants to receive any documents, training and warranties needed to take over the management and maintenance of their building. But they also want assurance that the completed building meets their requirements and is functioning as designed.
In construction, commissioning is a quality assurance process to verify and document the performance of a building’s systems, equipment and components to ensure they meet design specifications, owner requirements and building regulations. Proper commissioning is part of delivering a high-quality project, investing in its long-term performance and ensuring it’s ready for comfortable and safe usage.
This article covers the benefits, best practices and the steps involved in commissioning.
Table of contents
The Basics of Construction Commissioning
Commissioning has generally become standard practice during project closeout, particularly on large buildings with complex systems. However, it is typically a requirement for owners who are submitting their building for green grants or certifications, such as LEED (Leadership in Energy and Environmental Design). These specialized programs often have specific requirements for system performance or for additional commissioning.
As a process, commissioning includes a series of tests, inspections and documentation to ensure a building’s systems are installed correctly, operating according to their design specifications and meeting the owner’s requirements for performance and efficiency.
Building systems that usually undergo commissioning include:
System | Commissioning Process |
---|---|
HVAC | Test all heating, ventilation and air conditioning units to confirm proper air flow and temperature regulation. |
Plumbing | Verify all water-related systems produce the appropriate levels of output, pressure and quality. |
Life Safety Systems | Verify functionality of fire alarms, sprinkler systems and emergency lighting. |
Commissioning generally assesses newly installed systems. Retro-commissioning or re-commissioning is the analysis of systems that are already installed and being used. These processes can help determine whether a system needs to be repaired or replaced.
Commissioning vs Start-up Reports
The phrase “commissioning,” is often used interchangeably with “start-up reports,” but they are technically different processes that often happen concurrently.
Start-up reports usually verify equipment and systems are able to be turned on and fulfill their most basic functions without necessarily focusing on performance, such as whether a drain line drains, pipes don’t leak or an A/C blows cold air. Commissioning reports, on the other hand, focus on system performance, such as verifying that a duct is receiving the right amount of air and at the correct temperature.
The Value of Commissioning
For owners, commissioning is an important step in ensuring they receive the building they paid for and that it meets their expectations. For contractors, commissioning can sometimes feel like an extra step and extra paperwork but it usually provides numerous benefits and helps identify and address potential issues.
For all stakeholders, commissioning usually offers many benefits, including:
- Quality assurance by ensuring work meets specified standards and requirements and verifying systems and equipment are energy-efficient and operating as designed.
- Reducing costs by ensuring systems are operating efficiently, which can help reduce energy and operational costs over the building’s lifetime.
- Risk mitigation by identifying issues before the building is occupied and while contractors have time to resolve them without disputes, callbacks or warranty claims.
- Ensuring compliance with relevant regulations, codes and standards, including certification requirements such as LEED.
- Establishing a baseline of performance, which can be used to assess future performance and determine the urgency of repairs or replacements.
- Reducing contractor liability by creating a record of the completed work to help settle or mitigate any future claims or disputes.
- Facilitating closeout, as commissioning reports and documents are often required parts of closeout documents.
The Commissioning Process
Some projects have specific equipment that might require special commissioning. For example, a medical facility might require a commissioning report for the medical gas system or a power plant might require testing for specialized cooling or fuel supply systems.
However, the process of commissioning is usually very similar for all projects and happens throughout the stages of construction.
Pre-design
The owner and the design team determine the systems and equipment needed to fulfill the building’s intended purpose. From there, they establish commissioning requirements for each system, including performance goals, sustainability targets and any specific documentation. These requirements can be based on a number of factors, including the needs of the building, local regulations and information from a manufacturer about how a piece of equipment should function.
Design
While designing the building, engineers and architects will include commissioning requirements as part of the project specifications and drawings. This will serve as a guide to the general contractor (GC) to know what systems need to be commissioned, what testing should be done and specific performance goals.
Construction
Subcontractors and trade teams reference the commissioning requirements to understand how equipment and materials should work and how they will be assessed. Members of the project or commissioning teams will conduct periodic inspections to check that the work is on track to meet project specifications.
Testing
Commissioning is typically scheduled shortly before the project is handed over to ensure all systems are installed before any commissioning takes place, which is usually important because many systems are intertwined. For example, the fire safety systems require plumbing and electricity. Commissioning before either of those systems have been installed could give incorrect results.
Issue Correction
Ideally, commissioning is simply a process of confirming things work as designed. However, when issues arise, they need to be addressed as promptly as possible. The GC might submit many Requests for Information (RFIs) or host meetings to determine the nature of the issue and its cause. If the problem is deemed to be a design issue, the design team will need to adjust the plans and rework will likely be required. If it was an issue in installation, the subcontractor will try to work quickly to fix it without delaying the closeout process.
Documentation
Commissioning documentation is often included with the closeout documents. These documents assure an owner that their equipment and systems work correctly, as well as providing them with a reference for future performance.
Re-commissioning
Some owners may continue commissioning even after the building is occupied. Periodic re-commissioning or retro-commissioning can help ensure systems continue to perform as intended. In some cases, a potential warranty claim might require re-commissioning to determine whether a defect has occurred.
Commissioning Best Practices
There are a few habits and mindsets that usually improve the likelihood of a successful commissioning process:
Integrate commissioning into project planning.
Commissioning should be included in the project management process, including factoring testing into the project schedule and budget. Many GCs try to align the commissioning process with the timing of the punch list, as issues can be included in the closeout workflow and the project team hasn’t demobilized. This timing also ensures all systems have been installed, which increases testing accuracy.
Establish clear roles and responsibilities.
The commissioning process involves many stakeholders, including the owners, the design team, the GC, subcontractors and the commissioning team. To further complicate things, some equipment is only part of a more complex building system.
For example, the fire damper system serves as a smoke block in the HVAC system in case of a fire. The commissioning of the fire damper system could feasibly fall to the three different commissioning agents — the one responsible for the life-saving systems, the one for the HVAC system, or one doing the electricity system.
To avoid this confusion, the commissioning scope should be clearly defined in the project specifications and in a subcontractor’s scope of work. The GC should identify when the process will require subcontractors to coordinate schedules and processes.
Communicate effectively.
Foster open and effective communication among all stakeholders. This can improve the commissioning process, as well as the process for resolving issues. Determining the cause of an issue might require a thorough investigation that involves numerous stakeholders.
Having systems of communication in place before a problem arises can help ensure they’re resolved promptly and effectively. Leveraging communication channels that are already in use — submittals, RFIs and punch lists — can help to streamline correspondence.
Free Class: Basics of Submittals
Master the basics of submittals with industry expert Janine Trinidad, and earn continuing education credits from AIA.

Keep documentation organized.
The commissioning process requires an immense amount of thorough documentation. It’s easy for this process to become chaotic, as subcontractors might prefer to use different formatting and include different information on their respective reports. GCs should work to establish clear systems of document management and convey their expectations. This might include providing a template for all commissioning documents or a sample report as a reference and prior to the start of testing.
The Future is Energy-Efficient
The construction industry has been putting an increased emphasis on sustainability and energy efficiency, which appears will only increase in the future. This likely means that commissioning will only become more common and more important, as it’s a crucial step in ensuring projects meet energy standards and qualify for green certifications. Embracing commissioning and being open to future innovations will allow owners, contractors and commissioning agents to make the process even more precise and impactful.
Was this article helpful?
Thank you for your submission.
80%
20%
You voted that this article was . Was this a mistake? If so, change your vote here.
Scroll less, learn more about construction.
Subscribe to The Blueprint, Procore’s construction newsletter, to get content from industry experts delivered straight to your inbox.
By clicking this button, you agree to our Privacy Notice and Terms of Service.
Categories:
Tags:
Written by
Janine Trinidad
21 articles
Janine Trinidad is a Construction Educational professional for Procore Technologies. In previous roles, Janine managed all phases of construction on hotel, mixed-use, and institutional projects in the San Francisco Bay area. She was responsible for negotiating contract budgets and change orders, managing RFIs and submittals, and overseeing quality control, among other duties. She is also a certified transformational coach with a focus on women-centered and trauma-informed methods. She is passionate about transforming the construction industry to be a healthier, more successful and welcoming place to work and believes technology and education are allies in doing so.
View profileJames Hamilton
70 articles
James Hamilton is a writer based in Brooklyn, New York with experience in television, documentaries, journalism, comedy, and podcasts. His work has been featured on VICE TV and on The Moth. James was a writer and narrator for the show, VICE News Tonight, where he won an Emmy Award and was nominated for a Peabody Award.
View profileExplore more helpful resources
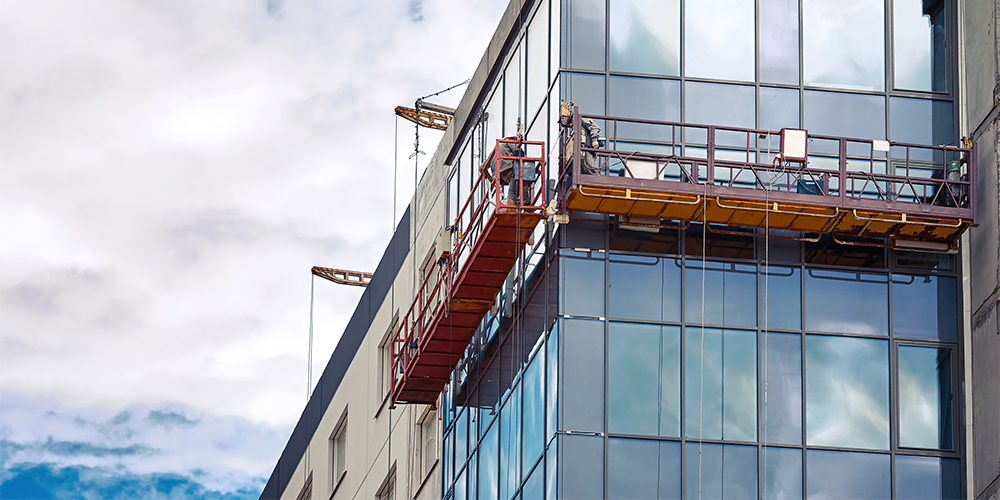
Preparing for Post-Construction: A Guide to the Final Phase of a Project
Large construction projects often take years to plan, more years to design, and even more years to build. From the groundbreak point of view, it’s often difficult to see the...
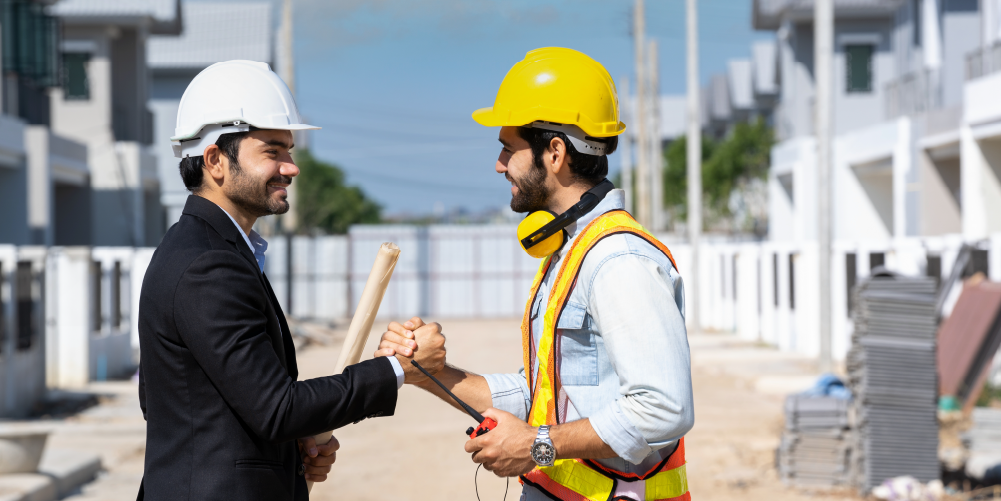
Construction Handover: Keys to an Efficient Process
After the months or years it takes to complete a construction project, the handover process begins. Project handover is the final part of the construction process, where a project, along...

Construction Closeout Documents: What’s Included & Why
Few parts of the building process can feel as stressful and as complicated as closeout: the multi-step, final phase of construction in which a project is prepared to be handed...

The Contractor’s Guide to Concrete Inspections
Concrete: It’s the key building block of nearly every structure’s foundation — and it’s the world’s most widely used building material. For most general contractors, understanding how to assess concrete...