— 9 min read
Effective Construction Progress Tracking: Tools and Techniques
Last Updated Aug 29, 2024
Last Updated Aug 29, 2024
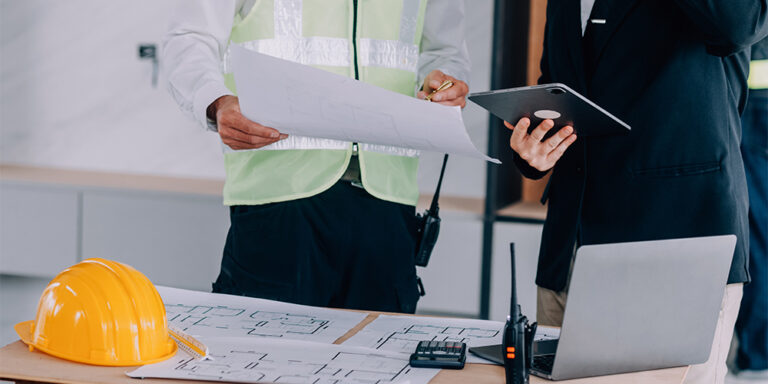
General contractors (GC) must work to get projects across the finish line before the deadline, or else they can face massive penalties. However, the best GCs know that simply completing the job is only one element of their role, and not being able to effectively track their progress and share that information with stakeholders is an easy way to lose trust and rapport with clients.
When one fails to track their progress, it becomes very hard to prove that they’re doing what the owner hired them to do. This is where progress tracking comes in. Progress tracking refers to the ability to assess a construction project's level of completion and distribute this information to relevant project stakeholders.
This article explores practical steps for approaching progress tracking, including how to use technology to its fullest analytical capacities and strategies for getting a project back on track when it is delayed.
One of the biggest challenges in tracking progress is how many hands the information has to go through to update. There are people in the field hanging drywall and someone in a back office looking at it on a different scale, waiting for that update. The time it takes and the number of people involved in getting the information to those who need it is probably the biggest challenge, especially on large projects.
Dave Brown
Senior Strategic Product Consultant, General Contractors
Procore
Table of contents
Practical Steps for Effective Progress Monitoring
Following a handful of basic, practical steps can help a GC monitor the progress of most any project.
Set clear milestones and objectives.
Communication is key at every level of construction work, and effective progress tracking begins with setting clear objectives. One way this can look is taking the time to inform team members what their key performance indicators (KPIs) are, so they know how to do a good job.
As the project moves along, make sure to keep team members informed on how they’re meeting or exceeding their KPIs.
Making those KPIs visible is essential. You can have the percent complete up on a board, but many folks make building plans very visual. They'll have big posters showing the layout and color-code them to represent different phases. Progress can be shown by color-coding a plan with thousands of dots, representing completed foundations. Making that open and visible helps spot problems early.
Dave Brown
Senior Strategic Product Consultant, General Contractors
Procore
Regularly update progress data.
When a project begins, the GC and owner or rep agree to a timeline, but how and when the work actually unfolds can be different from the projected schedule.
In real-time during the build — especially as obstacles and rework occur — a GC must continually align their idea of the project schedule with the reality on the worksite. It can be a difficult balancing act, especially acknowledging that rushing can push workers toward safety hazards.
As the schedule evolves, make sure to update crew members and clients alike, as managing everyone’s expectations of the process is a critical soft skill in keeping them motivated.
Unify different types of data.
The long-upheld iron triangle of project management is made of three simple corners: schedule, budget and resources.
Tracking these three areas requires relying on both quantitative and qualitative data. On the qualitative side, a GC may find timekeeping and financial tracking programs, budgets for individual contractors with the projected amount of hours they will be needed on the project, contracts with vendors and software that helps calculate the percent-complete of a project or individual building within a project.
The qualitative side, however, can be just as important for being able to communicate the reality on the worksite to stakeholders.
Examples of qualitative data include photo documentation, accurate reports and daily logs, and sometimes email or text communications. These are necessary complements to quantitative data—for example, a photo may contradict that an install has been completed correctly, and a daily log or email may be useful in understanding why a particular part of an installation was performed the way it was.
Contractors should rely on a system of progress tracking that can unify both qualitative and quantitative data — for example, a software management program that can link documents and plans to annotations, photos and other important reference materials.
Both qualitative and quantitative data have their own problems, especially if you're not using a unified system to help tell the story of what’s going on at the worksite.
If you can't look at a photo and understand what the photo was of, because it hasn't been attached to a manpower entry or linked into the budget and a scheduled task, it becomes really hard to connect those corners of the iron triangle that govern most projects.
Dave Brown
Senior Strategic Product Consultant, General Contractors
Procore
Using Technology for Data Collection and Reporting
Some projects might be particularly hard to track—for example, some heavy civil construction involves massive, sprawling worksites that could go on for miles.
Harnessing the power of advanced technology can be incredibly useful for a GC to keep tabs on the most unwieldy projects. Making use of cameras, drones, artificial intelligence and robotics can help a GC get information in real time and then analyze that information to make informed decisions.
Continuous Monitoring With 360 Cameras
The camera has been an incredible invention for the construction industry, especially since many innovations have turned it into a tool for real-time analysis.
360-degree cameras can be mounted on hard hats, allowing continuous, real-time photo documentation as workers move around the site. This creates a seamless way to capture visual data without disrupting daily activities.
Drones, on the other hand, excel in covering large, horizontal, or remote project areas such as highways and oil refineries. Equipped with technologies like LiDAR, drones can not only capture images but also measure grades and quantities, providing precise metrics that are invaluable for progress tracking.
“Drones can be a slam dunk for the construction industry. You spend a couple thousand bucks investing in them to have fly over, and they can do some really cool things. If you’re remote, out in the middle of nowhere with a pipeline or at an oil refinery, they can get to places you can’t.”
Dave Brown
Senior Strategic Product Consultant, General Contractors
Procore
AI and Robotics
The construction industry is still considering the possibilities and costs of automation, which can be useful even in small, unexpected ways for a GC or construction company.
In terms of progress tracking, robots can be deployed to autonomously document the site, reducing the need for manual site walks and allowing for continuous data collection.
Artificial intelligence can further amplify this capability by interpreting the collected data, turning images into actionable insights.
The combination of artificial intelligence and cameras offers a wealth of information processing. It's not just about taking a picture; it's about interpreting what the picture is showing. It can tell if a material is drywall.
It can configure whether a road is 10 or 11 miles complete. Innovating how to collect photos and parse through them at scale is crucial. It can turn qualitative information into numbers, like being 72% done with drywall installation.
Dave Brown
Senior Strategic Product Consultant, General Contractors
Procore
Gantt Charts, BIM, and Project Management Software
Gantt charts, provided by tools like Oracle Primavera and Microsoft Project, can allow GCs to visualize the project schedule, track percent completion and manage timelines efficiently.
Using Building Information Management software (BIM) can add another layer of utility by offering a digital representation of the physical and functional aspects of a project, enabling teams to collaborate and share updates.
Finally, project management software can integrate these tools, creating a unified platform for scheduling, resource allocation, and timekeeping that allows a GC to monitor all aspects of the iron triangle at every project they’re involved in.
Strategies for Addressing Project Delays
One of the easiest ways to spot a delay is when the schedule does not align with the budget— essentially, this means the project is burning more money than forecasted.
When a GC notices this happening in one of their projects, they can employ a few key strategies to address the delay.
Identify the root cause.
The most important part of addressing a delay is finding its cause.
When a GC notices work slipping on a particular metric, the first thing to do is hit pause—this keeps the problem from growing any further. Then, look at where money is being spent, and where the schedule seems to be slower than usual, and try to find the reason behind it.
Blame the process, not the people.
Ultimately, the responsibility for all delays rests on a GC’s shoulders, since it is their duty to get the job done.
For this reason, focus on identifying and addressing the root causes without blaming individuals. If blame is necessary, assign fault to the process, not a person. Contracts often make it easy to blame people, but focusing on process issues is more productive, and keeps crew members focused on returning to the work as soon as possible.
Reallocate resources efficiently.
Identify actionable steps within the project's capacity to address the delay. After taking any necessary corrective actions to get the project back on track, communicate changes and new plans clearly to all stakeholders.
Create a contingency plan.
Early input and communication with the people doing the work can identify potential issues before they escalate.
When something goes wrong, make sure the team members onsite know how to solve the problem if it arises again. Flipping problems and obstacles into teaching moments can create trust and respect with workers — and can also make them better at their jobs in the long run.
Monitor and prevent future delays.
Follow up regularly with stakeholders to ensure that the project remains on track and to address any new issues promptly. Communicate with trade contractors to continue to set realistic deadlines and schedules.
Finally, continue to monitor the schedule after the problem is fixed, as it drives many aspects like budget impact and jobsite safety.
Courses about construction.
For construction.
Unlock your career potential with our free educational courses on Health & Safety, Data in Construction, and more.
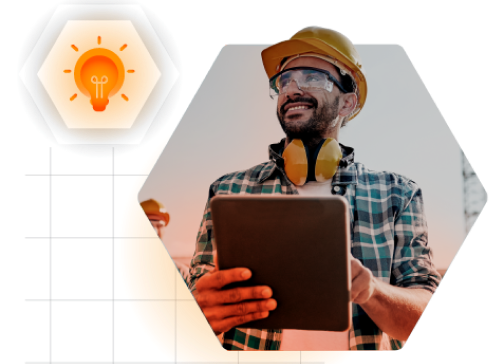
The Importance of Integrated Project Management
Effective progress tracking in construction projects is not just a matter of using the right tools; it also requires strong collaboration, open communication, and visibility among all project leaders and team members. By getting everyone on the same page, potential delays can be addressed as early as possible.
A centralized construction management software platform can seamlessly integrate the task of project management with everyday work onsite.
Progress tracking often involves handing off information from one person to the next, and sometimes there's a long process. Using a consolidated system can just help with that handoff. It's less copy and pasting, less emailing, and fewer opportunities for human error.
When dealing with work at scale, having data systems that can handle that kind of sharing, and also have both codified and customizable features, can really help.
Dave Brown
Senior Strategic Product Consultant, General Contractors
Procore
Efficient Progress Tracking Requires Communication and Collaboration
Creating a highly efficient workflow is possible by harnessing the power of technology and construction software — as well as fostering a collaborative and communicative project environment.
By employing these strategies, a GC can manage even the most complex project with confidence, maintaining client trust and getting a step closer to securing the next job.
Was this article helpful?
Thank you for your submission.
100%
0%
You voted that this article was . Was this a mistake? If so, change your vote here.
Scroll less, learn more about construction.
Subscribe to The Blueprint, Procore’s construction newsletter, to get content from industry experts delivered straight to your inbox.
By clicking this button, you agree to our Privacy Notice and Terms of Service.
Categories:
Tags:
Written by
Dave Brown
Dave is a Senior Strategic Product Consultant for Procore, specializing in General Contractors. Previously, he worked for Consigli Construction Co in Boston and Washington, DC as a Project Engineer and Assistant Project Manager, responsible for a variety of activities including bidding and procurement, contracts, and cost control. Dave holds a Bachelor's Degree in Structural Civil Engineering from Bucknell University.
View profileTrey Strange
26 articles
Trey Strange is a Peabody and Emmy-Award winning writer and producer based in Brooklyn, NY. Throughout his career, Trey has worked for the Huffington Post, Houston Chronicle, Out Magazine, Brooklyn Eagle, CNBC, INTO, and New York Magazine's Bedford + Bowery. He received his Masters in Journalism and Middle East studies from New York University, and Bachelors in the same subjects from the University of Houston.
View profileExplore more helpful resources
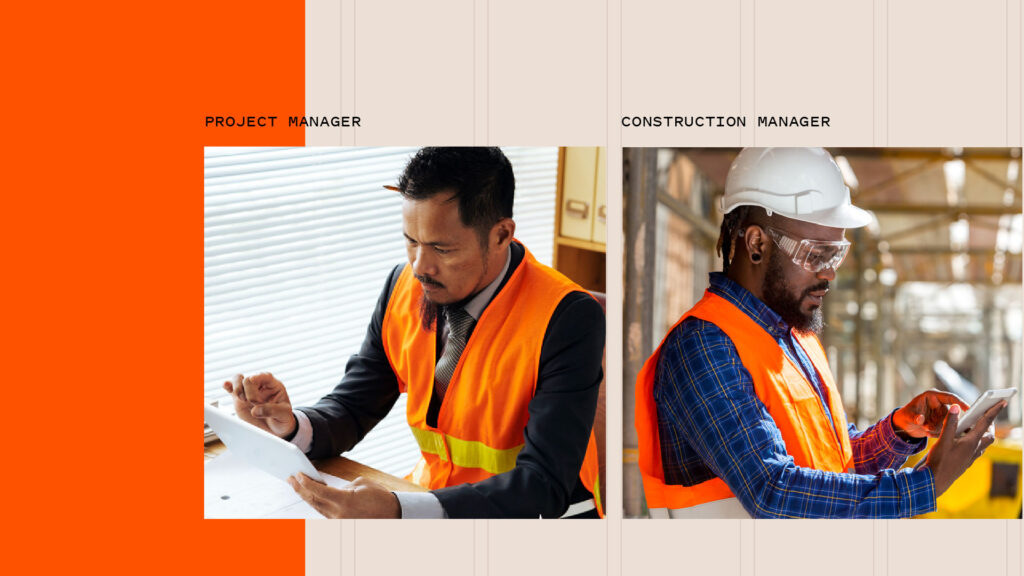
Construction Manager vs. Project Manager: Comparing Leadership Roles
Skillful oversight of construction projects allows companies to deliver to owners on time and within budget. Construction managers (CMs) and project managers (PMs) provide the necessary supervision to keep projects...
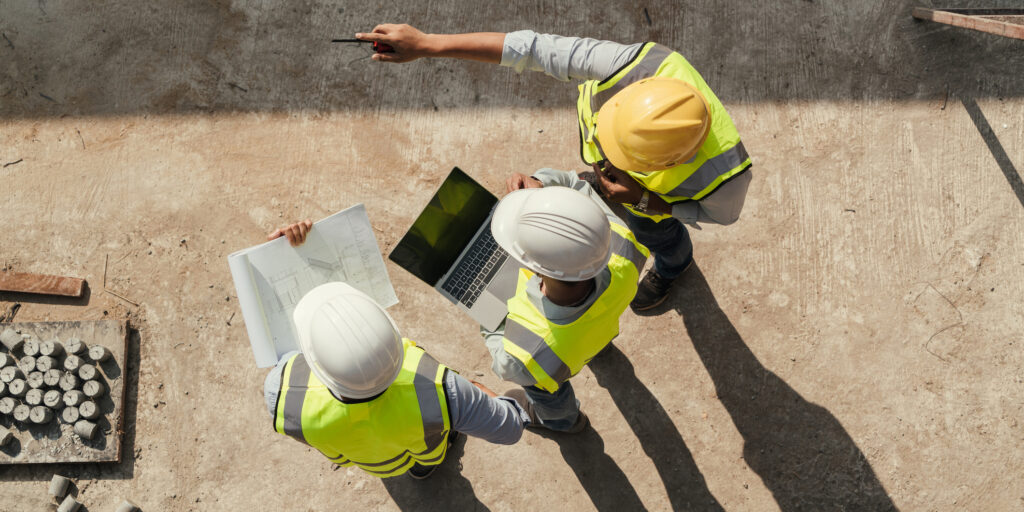
Holistic Construction Project Oversight: Aligning Relationships & Processes
All parts of a construction project are connected. A delayed approval for a change order can impact a project’s timeline, required overtime and, ultimately, the budget. Communication with an owner...
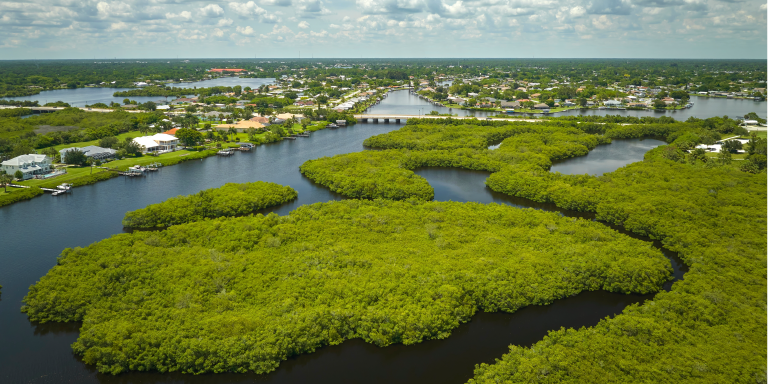
Navigating the Challenges of Industrial Construction in Wetland Areas
Industrial construction in Florida presents unique challenges and opportunities for construction companies, especially because over 31% of the state is wetlands. As the demand for logistics and distribution facilities grows,...
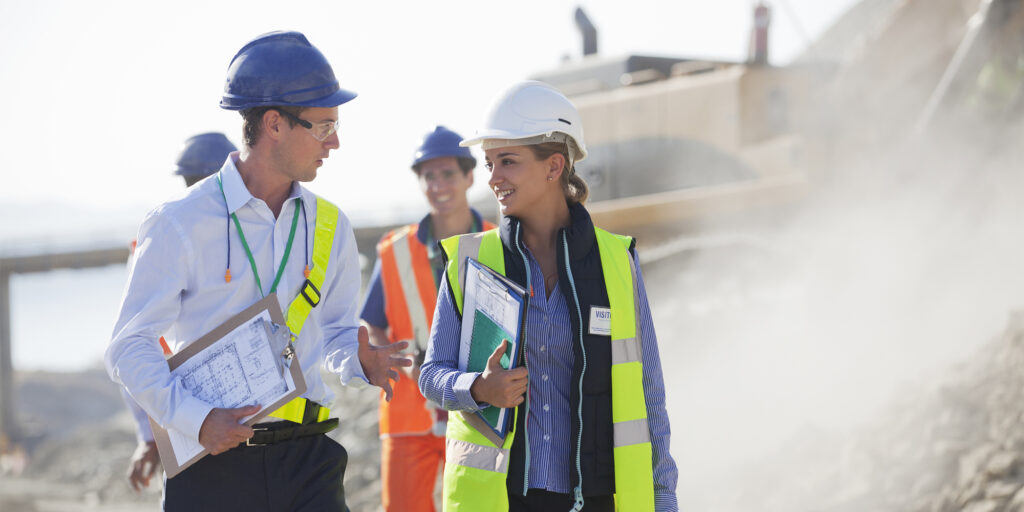
Building Together: How Integrated Project Delivery Creates Shared Value
As technology and innovative processes continue to evolve the construction industry, the need for openness and collaboration among teams and stakeholders has increased significantly. Traditional project delivery methods, such as...