— 14 min read
How Project Phasing Keeps Construction Projects on Time and on Budget
Last Updated Jun 26, 2025
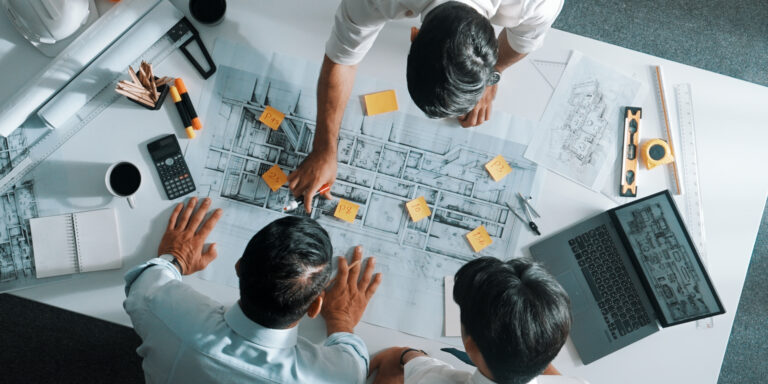
Managing a construction project involves balancing countless tasks, coordinating multiple trades and meeting strict deadlines. Without a structured approach, it’s easy for projects to fall behind schedule or exceed budget. For general contractors, one of the most effective strategies for handling this complexity is project phasing.
Project phasing divides a construction project into clear, sequential stages, creating a roadmap that guides the project from start to finish. This method helps general contractors (GCs) set measurable milestones, streamline coordination among subcontractors and address potential issues before they escalate.
In this article, we explore what project phasing is, why it’s essential for successful project delivery and how it helps contractors mitigate risks, manage subcontractors and stay on schedule.
Table of contents
Understanding Project Phasing
Project phasing involves the sequential breakdown of a construction project into a series of defined stages or phases. Each phase encompasses a set of tasks that must be completed before moving on to the next, creating a logical flow of activities. From preconstruction and site preparation to structural work, interior finishes and turnover, phasing helps map out the entire project lifecycle. By establishing these phases, contractors can better track progress, allocate resources efficiently and communicate expectations clearly to all stakeholders.
Why phasing matters to general contractors
For GCs, project phasing is a key tool that helps guarantee successful project delivery. By segmenting the project into defined stages, GCs can:
Track progress
Phasing establishes measurable milestones that make it easier to monitor productivity and keep the project on schedule.
Manage subcontractors effectively
With clear phases in place, GCs can coordinate the work of multiple trades, reducing conflicts and improving site efficiency.
Mitigate risks
Phasing allows GCs to identify potential issues early and implement risk management strategies tailored to each stage of the build.
Project phasing offers a clear framework that helps general contractors manage the complexity of construction, respond to changes efficiently and maintain steady progress, minimizing the risk of costly delays and disruptions.
Typical Phases of a Construction Project
While the overall structure of project phasing remains similar across most commercial construction projects, the specific phases, tasks and terminology can differ based on project type, region and construction methods.
1. Preconstruction Phase
Preconstruction is where foundational planning takes place, setting the project up for success before any major onsite work begins and a smooth transition into active construction. Key activities in this phase include:
Clearing the site, grading and addressing any necessary environmental considerations.
Obtaining the required building permits to comply with local regulations.
Stormwater management: Implementing erosion control measures to protect the site and surrounding areas.Setting up temporary power, water and sewer connections and coordinating with utility providers so that these services are available when construction begins.
Stormwater management
Implementing erosion control measures to protect the site and surrounding areas.
Mobilization
Bringing equipment and crews onsite to prepare for the start of construction.
Effective preconstruction planning is important, as it lays the groundwork for all subsequent phases and helps prevent delays later in the project.
2. Structural Phase
The structural phase involves constructing the building’s framework, using materials such as concrete, steel and timber. The choice of materials often varies based on project type and regional preferences.
For example, concrete pours and metal stud framing are common in urban commercial builds, while mass timber is gaining popularity for its sustainability and aesthetic qualities, particularly in the Pacific Northwest where heavy timber construction is a regional staple. This phase is typically the longest and most complex, forming the core of the building and setting the stage for all future work.
3. Interior Rough-In and MEP Installation
The interior rough-in phase is dedicated to the installation of mechanical, electrical and plumbing (MEP) systems, which provide the building’s essential functions. This stage requires close coordination among trades, as plumbing, electrical and HVAC work often overlap and must be synchronized to avoid conflicts and allows for efficient installation.
Learn more – Rough-in Inspections: Key Steps and What to Expect
On many projects, interior rough-in begins before the structural phase is fully complete, leading to a practice known as phase stacking. Phase stacking involves starting later phases before the previous ones are fully completed. While this overlap can accelerate the timeline, it also demands precise planning to keep the project on track and prevent delays or costly rework.
4. Exterior Envelope and Weatherproofing
The exterior envelope phase is essential for sealing the building against the elements. Achieving a weather-tight seal at this stage safeguards the project from potential setbacks, such as water infiltration, mold growth, or temperature fluctuations, all of which can disrupt subsequent phases and may result in cost overruns.
Drying in the building
The primary objective is to “dry in” the structure as quickly as possible. This involves closing up the exterior to prevent water intrusion, which can lead to costly rework, mold issues and delays in interior work.
Facade installation
The installation of the building’s facade (e.g., cladding, siding, or curtain walls) is often a complex process that requires coordination with structural components and ongoing interior work.
Waterproofing and insulation
Proper waterproofing protects the building from moisture infiltration. This includes applying membranes, sealants and drainage systems. Adding insulation at this stage helps regulate interior temperatures and improves energy efficiency.
Coordination with interior rough-in
Exterior envelope work often overlaps with interior rough-in, requiring careful synchronization. If the exterior isn’t sealed in time, it can disrupt interior construction activities and lead to scheduling conflicts, increased risk and potential damage to installed systems.
5. Interior Finishes
Pro Tip
Expect a time crunch in the finishing phases, no matter how well you’ve managed the earlier parts of the project. Unlike structural work, where productivity can often be ramped up, finish work like installing cabinets or tile has physical limitations. Plan ahead and communicate realistic expectations with the owner.
The interior finishes phase marks the final push to complete the interior spaces and prepare the building for occupancy. This stage involves installing drywall, cabinetry, light fixtures and completing tasks like painting and trim work that give the project its finished look. Many of these tasks require a high level of craftsmanship and attention to detail, as they are among the most visible elements of the build.
While this phase signals that the end of the project is near, it often comes with its own set of challenges. Compressed timelines are common, especially when ownership groups push for early move-in dates. The increased schedule pressure can place heavy demands on these trades, making it difficult to maintain quality while meeting tight deadlines.
6. Turnover and Closeout
The final phase of the project, known as closeout, involves handing over the building to the client and completing any remaining tasks before formal closure. The general contractor transitions the project to the building management team, guaranteeing that all systems are fully operational and that the client is satisfied with the completed work.
This stage typically includes obtaining the certificate of occupancy, confirming that the building meets all safety and regulatory requirements for use. Final inspections and walkthroughs are conducted to help identify and resolve punch list items, allowing the project to be officially closed out. The general contractor also provides ongoing support through warranty work, handling any defects or concerns that may arise after the building is occupied.
The Role of Scheduling and Phase Stacking
Effective scheduling is essential for managing project phasing, enabling general contractors to optimize workflows, streamline coordination and adapt to changes. Two key strategies — phase stacking and lean scheduling techniques — are particularly valuable for maintaining control over complex projects.
Phase Stacking for Efficiency
Pro Tip
Don’t be afraid to stack phases, but be strategic about it. Overlapping tasks like rough-in and exterior work can help speed up the timeline, but only if you have strong on-site coordination. Weekly planning meetings with subcontractors are essential to avoid scheduling conflicts and keep everything on track.
On fast-track projects, this approach allows trades to work concurrently. By overlapping activities, general contractors can maximize resource utilization and accelerate completion. However, phase stacking requires precise planning and coordination, as it increases the complexity of onsite operations.
With multiple trades working simultaneously, there is a greater risk of scheduling conflicts, site congestion and potential rework if tasks are not aligned properly. Successful phase stacking depends on detailed daily planning and real-time adjustments to keep the project moving forward smoothly.
Evolving from CPM to lean scheduling
Traditional scheduling methods, such as the Critical Path Method (CPM), provide a detailed, top-down view of the project timeline by outlining tasks in a fixed sequence based on dependencies. While CPM is effective for establishing a baseline schedule, its linear approach often struggles to accommodate the dynamic nature of active job sites. When unexpected changes occur, rigid schedules can quickly become outdated, leading to misalignment among trades and an increased risk of delays.
In contrast, lean construction scheduling techniques like the Last Planner System offer a more adaptive and collaborative approach. Last Planner System focuses on short-term planning and involves all stakeholders in the scheduling process. Rather than strictly following a high-level timeline, this method emphasizes working backwards from critical milestones, engaging trade partners in the decision-making process to determine the most efficient sequence of tasks.
This helps identify potential issues early, allowing the team to address them proactively and adjust plans in real-time. The flexibility of lean scheduling makes it particularly effective for managing the fast-paced, ever-changing environment of modern construction projects.
Advantages of adaptive scheduling
By adopting strategies like phase stacking and lean scheduling, general contractors can improve trade coordination, reduce risks and enhance project efficiency. The focus on real-time updates and stakeholder collaboration enables a more responsive approach, better suited to the dynamic demands of complex construction projects. These methods help GCs maintain control, avoid costly disruptions and deliver projects on time.
Risk Management and Project Phasing
Construction projects are inherently complex, and effective risk management is a key component of successful project phasing. Without a strong risk management strategy, issues like coordination failures, scheduling conflicts and last-minute changes can lead to costly delays and disruptions. By anticipating common risks and employing proactive mitigation techniques, general contractors can handle these challenges more effectively.
Identifying common risks in phasing
The process of dividing a project into sequential phases introduces several potential risks that can disrupt the flow of work. One of the most common issues is coordination failure, where misalignment between trades leads to delays, rework or even safety hazards.
Pro Tip
Don’t underestimate the importance of ownership involvement in decision-making. Delays in approvals or last-minute design changes can derail even the best-laid plans. Establish a clear line of communication with the ownership group from the start to avoid costly disruptions.
Scheduling conflicts are another frequent problem, particularly in fast-track projects where multiple trades are working simultaneously. When tasks overlap without clear communication and planning, it can result in site congestion and conflicts over shared resources or areas.
Changes from the owner or design team during construction can also negatively impact the project timeline. For example, decisions to alter high-end finishes or modify design elements midway through a phase often lead to extended lead times, rework and increased costs. These changes ripple through the entire schedule, affecting subsequent phases and complicating trade coordination.
Mitigating risks with Lean Construction techniques
Real-time schedule updates are also essential for managing risks effectively. Unlike traditional static schedules, dynamic updates reflect the current status of the project, enabling contractors to respond quickly to disruptions. Regular coordination meetings with subcontractors help keep everyone informed and aligned with their responsibilities. Consistent communication creates a collaborative environment where issues are quickly identified and resolved, reducing the risk of delays.
Effective implementation of lean construction techniques requires more than just planning—it demands consistent communication, flexibility and a commitment to real-time adjustments. By integrating methods like the Last Planner System and prioritizing dynamic scheduling, general contractors can transform potential risks into manageable challenges.
Impact of Technology on Project Phasing
Technology plays a significant role in limiting risk for managers, leading to less errors, which leads to statistically faster schedules. While tools like digital scheduling software, reality capture and data analytics have improved phase management, emerging trends such as prefabrication and modular construction hold the most promise for transforming project phasing in the future.
Key digital strategies to enhance project phasing
Implementation of technology helps make managing project phases more efficient and precise. Several key tools have had a notable impact on phase planning and execution:
Digital work plans and scheduling software
Traditional scheduling practices, like sticky-note planning, have evolved into digital platforms that offer a more streamlined and collaborative approach. Construction software now enables general contractors to digitize their work plans, allowing for real-time updates, better visibility across teams and more effective coordination of overlapping tasks. These tools help keep the project on track by providing an up-to-date view of the schedule and enabling quick adjustments when changes occur.
Drones and robotics for inspections
Reality capture technology has become essential for gathering accurate, high-resolution data on construction sites. Drones provide a bird’s-eye view of the site, allowing project teams to quickly assess progress and spot potential issues without disrupting on-site activities. Robotics further enhance jobsite inspections with tasks like automated drywall installation and precision scanning, improving data accuracy and reducing human error. Together, these tools strengthen quality control and provide valuable insights throughout the project.
Data-driven decision-making
The ability to collect and analyze historical project data has become a game-changer for general contractors. By leveraging data from previous builds, GCs can make more informed decisions about phase planning, identify potential risks earlier and adjust strategies based on proven outcomes. Predictive analytics can highlight patterns that may not be immediately obvious, allowing teams to anticipate delays or challenges before they impact the project timeline.
Automation
Digital tools greatly improve the management and execution of project phasing in construction by simplifying design, scheduling and resource allocation into a single, cohesive process, which reduces the need for manual data entry and lowers the risk of human error. With automation, project managers can quickly adapt to changes, allocate resources more efficiently and make sure tasks are completed on time, making construction projects more efficient, on schedule and on budget.
While technology continues to enhance phase management, the hands-on nature of construction remains a limiting factor in significantly reducing phase durations. Until more advanced automation and robotics become commonplace, phase durations are unlikely to see substantial reductions. However, by embracing digital tools, drones,and data-driven approaches, general contractors can better manage the complexities of each phase, mitigate risks and optimize project delivery.
Advancing Project Phasing through Prefabrication and Modular Construction
Prefabrication and modular construction offer a way to streamline project phasing by shifting significant portions of the build offsite. By fabricating elements such as wall panels, mechanical systems and even entire room modules in controlled environments, contractors can achieve higher quality and consistency while accelerating the overall timeline. Offsite production also helps to alleviate site congestion and reduce the risks posed by weather delays, making it a compelling strategy for fast-track projects.
Despite these advantages, prefabrication and modular construction present unique challenges. Transporting large prefabricated components to the jobsite requires detailed logistical planning and can be hindered by regulatory constraints. Once onsite, these elements often need adjustments to fit specific site conditions, which can limit the time savings gained from off-site work. Integrating prefabricated components into traditional construction workflows demands precise coordination across all trades, as any misalignment can disrupt the flow of the project.
As the industry continues to adopt and refine these techniques, the potential for prefabrication and modular construction to shorten phase durations and enhance project efficiency is becoming more apparent. For now, general contractors should focus on effective planning and coordination, while leveraging existing technologies to optimize each phase.
Adapting Project Phasing for the Future of Construction
By dividing the project into clearly defined stages, GCs can enhance visibility, streamline coordination among trades and address potential issues early. The adoption of lean scheduling techniques and phase stacking reflects a shift towards more adaptive, real-time planning that meets the dynamic demands of today’s job sites.
Looking ahead, the integration of new technologies, such as advanced scheduling software and prefabrication methods, will continue to refine how project phases are executed. With a strong phasing plan in place, GCs can confidently handle complex builds, mitigate risks and deliver high-quality results that meet or exceed client expectations.
Was this article helpful?
Thank you for your submission.
100%
0%
You voted that this article was . Was this a mistake? If so, change your vote here.
Scroll less, learn more about construction.
Subscribe to The Blueprint, Procore’s construction newsletter, to get content from industry experts delivered straight to your inbox.
By clicking this button, you agree to our Privacy Notice and Terms of Service.
Categories:
Tags:
Written by
Britt Jordan
Britt Jordan is an experienced construction professional with over a decade in the industry, specializing in management and technology solutions. He spent more than seven years at ANDRES Construction Services, where he advanced from Office Engineer to Operations Technology Specialist. Known for integrating technology with construction, Britt is committed to innovation in the field and now works as a Solutions Engineer at Procore Technologies.
View profileTaylor Riso
80 articles
Taylor Riso is a marketing professional with more than 10 years of experience in the construction industry. Skilled in content development and marketing strategies, she leverages her diverse experience to help professionals in the built environment. She currently resides in Portland, Oregon.
View profileExplore more helpful resources
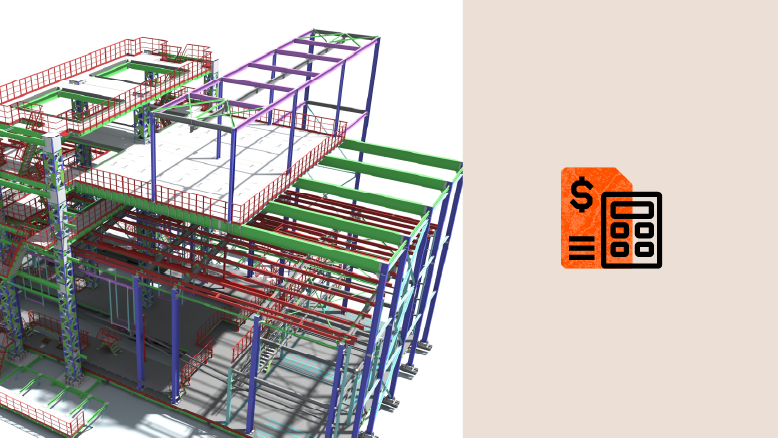
BIM for Construction Cost Control & Budget Management
As the construction industry advances in its digital transformation journey, building information modeling (BIM) is becoming increasingly common. Teams and individuals who push back against using the 3D model and...
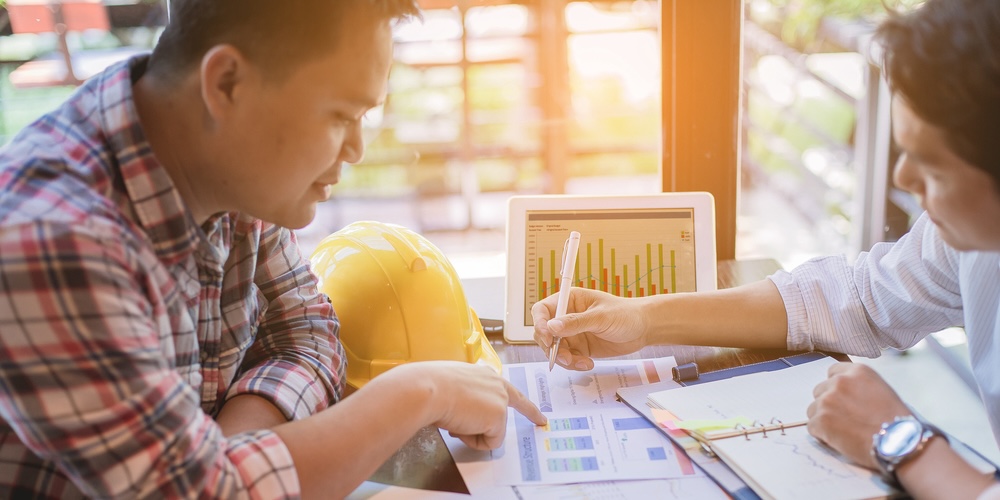
Estimate vs. Budget: Tools to Guide Construction Financial Planning
Whether building a residential home, a commercial complex or a large-scale infrastructure development, understanding and managing costs is key to completing a project on time and within financial limits. Effective...
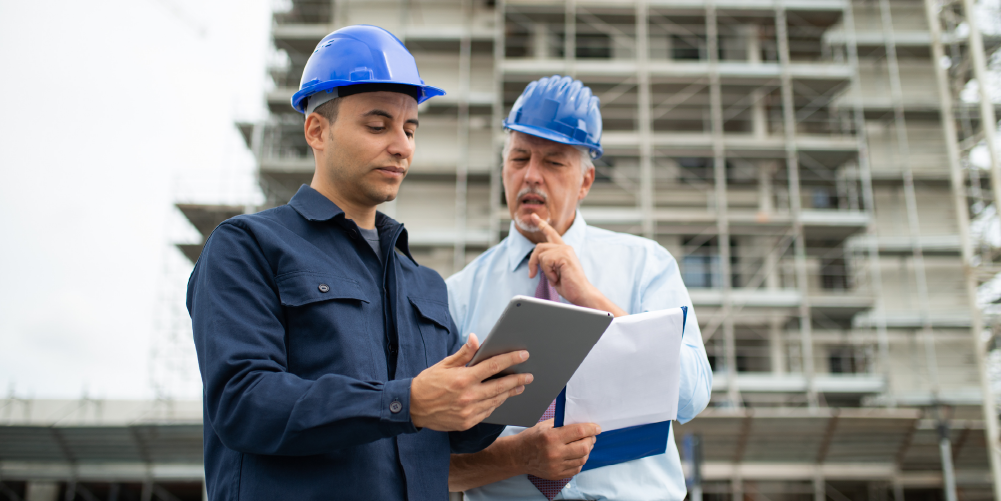
Construction Project Over Budget? Common Causes & Solutions
On construction projects, going over budget is an all-too-common scenario. This situation is more than a mere miscalculation: It can fundamentally alter the trajectory and outcome of a construction project...
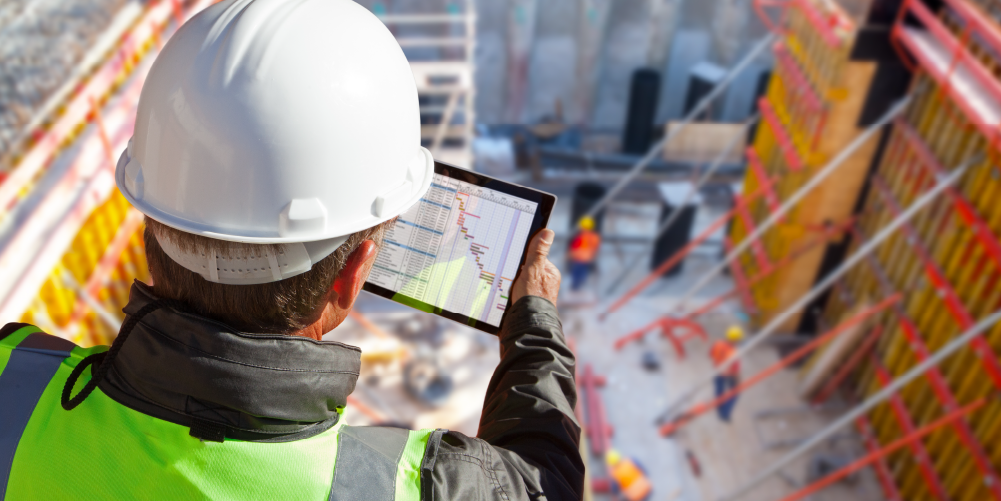
Managing Direct Costs in Construction — and Their Impact on the Budget
Direct costs in construction are expenses directly linked to the construction of a specific project, such as materials, labor and equipment. These costs are key components in project planning and...
Free Tools
Calculators
Use our calculators to estimate the cost of construction materials for your next project.
Templates
Find a template to help you with your construction project tasks.
Material Price Tracker
Get the latest U.S. retail prices and view historical trends for common building materials.
Glossary
Explore key terms and phrases used in the industry.