— 7 min read
The Importance of Minimizing Construction Rework
Last Updated Aug 12, 2024
Last Updated Aug 12, 2024

Construction rework can be costly and cause delays, and it can be frustrating to coordinate crews to return to redo portions of a job. With the multiple trades required for most construction jobs, almost all projects have some rework due to client changes, workmanship problems or material flaws. Minimizing rework on a construction project is in the best interests of general contractors, owners and trade partners, as the schedule and financial costs of rework can seriously impact the whole project.
Being alert to the most likely causes of rework and implementing strategies to reduce the need for rework can help construction companies keep projects on schedule and on budget. This article will cover how project team leaders can use thorough project planning, communication and collaboration across teams to minimize construction rework, improve quality control and avoid or decrease errors and cost overruns.
Table of contents
What is Construction Rework?
Construction rework refers to the process of revising or redoing work that was initially completed incorrectly or did not meet the required specifications. Various possible reasons for rework include design errors, poor workmanship, material defects or changes in project scope.
The size of each occurrence of rework can also vary. With minor issues caught early, the cost and time to perform the work can be minimal. An issue discovered later in the process, after many other trades have worked in the area, can be a much costlier fix in terms of time and money. Similarly, change orders due to changes in design or scope can involve more significant rework.
Any time there is a need for rework, it could involve more than one trade returning to redo their work. Rework can be much more involved with the intersection of multiple MEP and structural elements that can require many teams to tear out and redo their work.
Even when caught relatively early in the process, rework can throw off the construction schedule. Imagine an underfloor installation like electrical that needs to be reworked for some reason. Time for rework means the carpeting is delayed, and installing desks and computers is also pushed back. All the work scheduled to come after is delayed, complicating the process for managers and teams trying to deliver the project on time.
We worked on one project where large glass windows in the atrium were installed during the autumn. The team delivered the building to the owner and was subsequently hired to fit out office building floors for tenants. The work was proceeding during the following summer when the vast glass windows in the atrium started shattering — it turned out, during the glass production process, oil droplets seeped into the glass. When exposed to the heat of the summer sun, the oil expanded, causing the glass to spontaneously shatter.
As the glass contractor brought in cranes to replace the windows, it was too dangerous to have work proceed on the office floor areas looking out onto the lobby. The teams fitting out the floors had to rearrange their schedules to work on the far side of the office to leave the parts overlooking the lobby clear.
This required nimble scheduling, nighttime work and extra costs passed to the owners. Due to material flaws, this rework impacted multiple trades working on a completely different project within the building. With a whole team effort, the office floors were delivered on time despite the atrium glass replacement upending scheduling.
Daniel Kavanagh
Solution Specialist, Industry Compliance
Procore Technologies
The Impacts of Rework
Rework can substantially impact a project in many ways. Delays can cause serious scheduling headaches, and deciding who is responsible for the cost of the rework can get complicated, making the task an often dreaded part of any job. Here are the most common consequences of the need for rework.
Increased Costs
Rework typically incurs additional labor, materials and equipment costs. It can also lead to penalties for project delays.
Project Delays
Rework can cause significant delays in the project timeline, affecting subsequent tasks and the overall completion date.
Reduced Productivity
The need for rework can disrupt workflow and reduce the overall efficiency of the project team.
Diminished Quality
Frequent rework can impact the quality of the final product, as continuous changes and corrections can lead to inconsistencies and defects.
Client Dissatisfaction
Rework can lead to frustration and dissatisfaction for clients, potentially damaging the reputation of the construction firm.
Damage to Team Morale
Each trade takes pride in their work, and having to come in and redo the job, quite possibly through no fault of that trade, can be demoralizing.
Common Causes of Construction Rework
Each project is unique, so there can be many challenges faced by rework contractors. Experienced team members may be able to spot issues quickly due to similar problems they have previously encountered, but unexpected issues can arise too. Here are the most oft-encountered causes for the need to perform rework.
Design Errors and Omissions
Mistakes or incomplete information in the design phase can lead to rework. This includes inaccurate drawings, incorrect specifications or conflicting information.
Pro Tip
Providing a mock-up room or samples of the proposed design for sign-off by the design and owner teams can prevent rework by giving a concrete rendering of the quality standard and design vision in advance.
Poor Workmanship
Substandard work by contractors or laborers, often due to inadequate skills, lack of training, or insufficient supervision, can necessitate rework.
Material Defects
Using faulty or substandard materials can result in rework when the materials fail to meet quality standards or performance criteria.
Changes in Scope
Modifications to the project scope after work has commenced can lead to rework. These changes might be due to client requests, regulatory requirements or unforeseen site conditions.
Communication Breakdown
Ineffective communication among project stakeholders, such as designers, contractors and clients, can lead to misunderstandings and errors that require rework. Language barriers can often be a source of miscommunication among crews. Site leads should confirm that everyone on the jobsite is clear on any directives or instruction about their scope of work before getting started.
We ended up asking our site teams to provide a translator if they had non-English speaking workers. So, if I was carrying out a toolbox talk or a presentation on site, I would always ask, 'Does anybody not understand me? If so, what language do you speak?'
I would then find a translator, have them translate the information, and sign a document confirming that the translation was done. This ensured that the communication was effectively conveyed to the team.
Daniel Kavanagh
Solution Specialist, Industry Compliance
Procore Technologies
Inadequate Planning and Scheduling
Poor planning and scheduling can result in rushed work, errors and the need for rework to correct mistakes made due to time pressure.
Damage by Other Trades
Equipment and workers moving through the site can accidentally hit a wall or scratch a piece of ironwork already installed and require rework to eventually deliver a quality product to the owner.
Strategies to Minimize Construction Rework
Pre-planning is one key element of all construction projects, and careful planning helps to reduce the need for rework. Planning ahead can detect design flaws, allow proper time for each stage of work to avoid rushing, and put quality assurance practices in place that will detect problems early. Here are tips to help reduce the need for rework.
Improve design accuracy.
Ensuring thorough and accurate designs can help minimize errors and omissions. This includes using advanced design tools and conducting detailed reviews.
Enhance communication.
Establishing clear communication channels among all project stakeholders can help prevent misunderstandings and ensure everyone is on the same page.
Implement quality control.
Implementing robust quality control and assurance practices can help identify and rectify issues before they require rework.
Pro Tip
A good practice is to “punch as you go,” checking quality and fixing problems while they’re still small.
Train and develop skills.
Investing in the training and development of the workforce can improve workmanship and reduce the likelihood of errors.
Plan comprehensively.
Detailed planning and scheduling can help anticipate potential issues and ensure work is carried out methodically and correctly.
Structure change management.
Implementing a structured change management process can help manage scope changes effectively and minimize their impact on the project.
Good communication and tracking can facilitate all of these strategies, and construction management platforms allow for transparency and collaboration that can help decrease the need for rework. Clash detection technology like BIM helps uncover design flaws before a project starts, eliminating a lot of possible rework.
Explore data and trends for building materials prices.
Get the latest U.S. retail prices and view historical trends for common building materials.
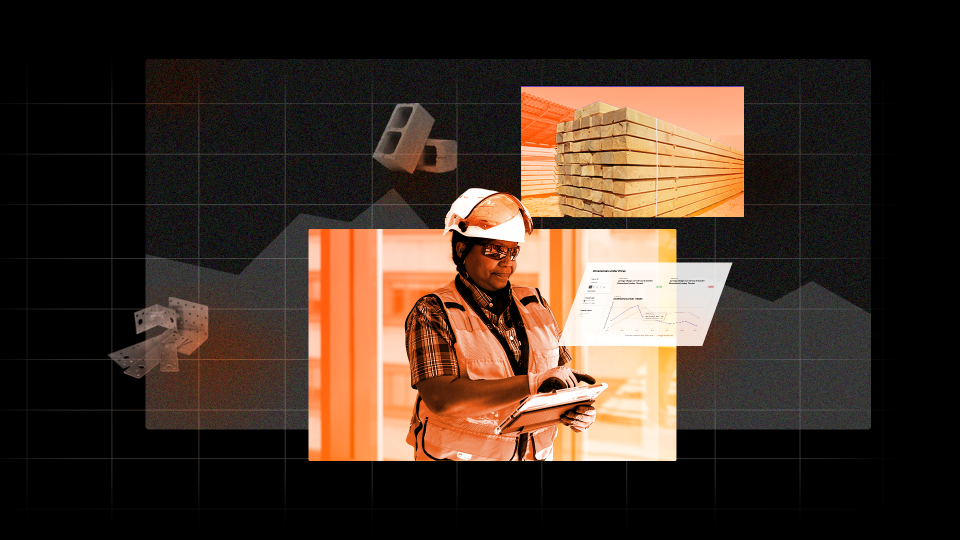
Understanding rework can help avoid it.
Construction rework is an issue that can significantly affect project success. By understanding rework’s causes and implementing strategies to prevent it, construction firms can enhance efficiency, reduce costs and improve project outcomes.
Was this article helpful?
Thank you for your submission.
100%
0%
You voted that this article was . Was this a mistake? If so, change your vote here.
Scroll less, learn more about construction.
Subscribe to The Blueprint, Procore’s construction newsletter, to get content from industry experts delivered straight to your inbox.
By clicking this button, you agree to our Privacy Notice and Terms of Service.
Categories:
Tags:
Written by
Daniel Kavanagh
15 articles
Daniel Kavanagh is a Senior Strategic Product Consultant at Procore, based in Dublin, Ireland. Daniel is a results-oriented project manager with a passion for building relationships and exceeding client and management expectations, with career experience in project management, systems implementation, technical design and architectural finishes. Daniel has been a member of the construction industry since 2014, and graduated from the Carlow Institute of technology.
View profileJulia Tell
43 articles
Julia Tell is a freelance writer covering education, construction, healthcare, and digital transformation. She holds a Ph.D. in Media & Communications and has written for publications including Business Insider, GoodRx, and EdSurge, as well as nonprofits, international businesses, and educational institutions.
View profileExplore more helpful resources
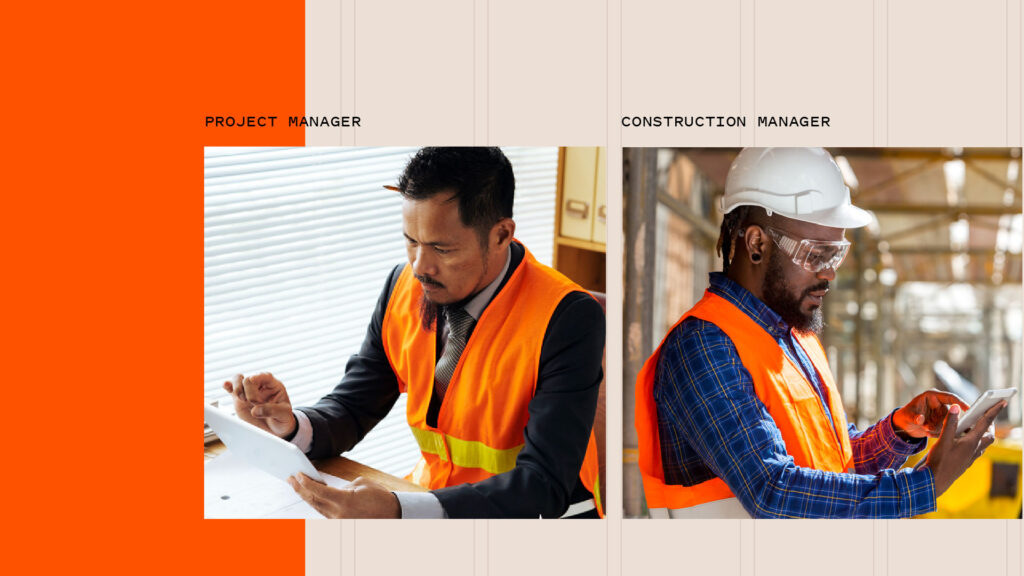
Construction Manager vs. Project Manager: Comparing Leadership Roles
Skillful oversight of construction projects allows companies to deliver to owners on time and within budget. Construction managers (CMs) and project managers (PMs) provide the necessary supervision to keep projects...
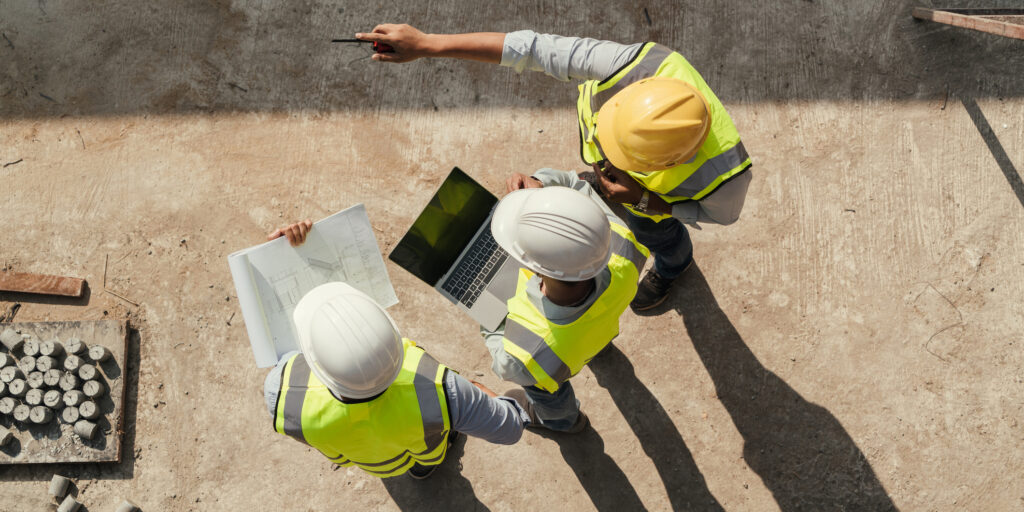
Holistic Construction Project Oversight: Aligning Relationships & Processes
All parts of a construction project are connected. A delayed approval for a change order can impact a project’s timeline, required overtime and, ultimately, the budget. Communication with an owner...
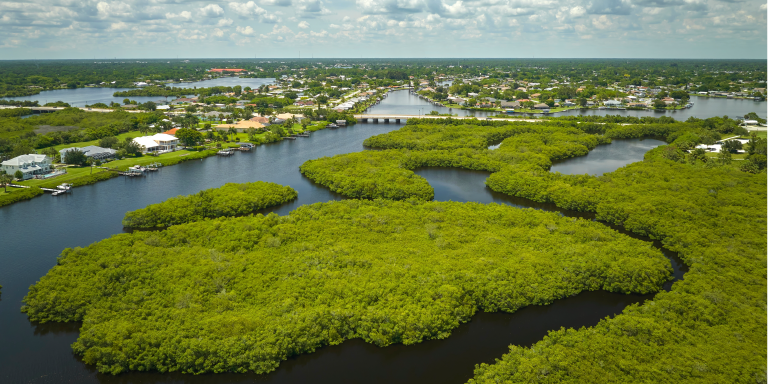
Navigating the Challenges of Industrial Construction in Wetland Areas
Industrial construction in Florida presents unique challenges and opportunities for construction companies, especially because over 31% of the state is wetlands. As the demand for logistics and distribution facilities grows,...
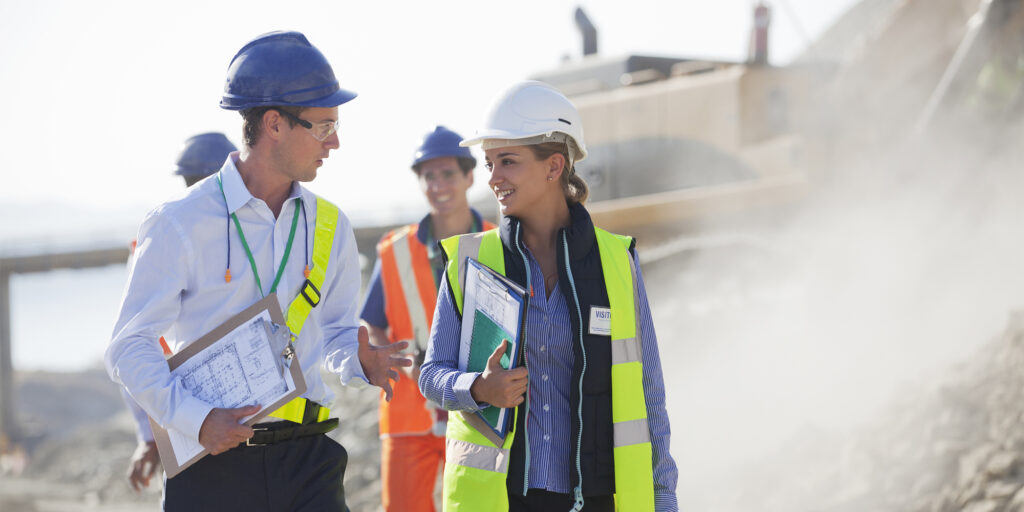
Building Together: How Integrated Project Delivery Creates Shared Value
As technology and innovative processes continue to evolve the construction industry, the need for openness and collaboration among teams and stakeholders has increased significantly. Traditional project delivery methods, such as...