— 10 min read
Construction Site Logistics: Best Practices for Building Smarter
Last Updated Mar 20, 2025
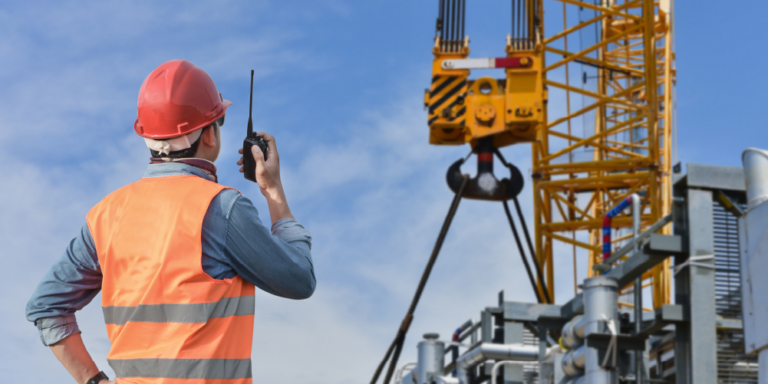
The effective management of construction site logistics can separate a timely, on-budget and high-quality construction project from one that falls short.
Construction site logistics refer to the operations that need to happen in order to facilitate construction work. Effective logistics create systems and plans to coordinate what happens on a site, when and by whom in order to ensure the completion of a project.
This article explores construction site logistics, including main categories, common examples and best practices.
Table of contents
The Basics of Site Logistics
Managing logistics is about identifying and taking care of anything and everything needed to keep work moving forward as smoothly as possible. A lot needs to happen for work to get done: Schedules need to be coordinated, materials need to be procured and systems need to be created.
Logistics range from big-picture considerations — such as sequencing tasks most effectively — to minutiae, such as installing a rumble strip so vehicles leaving the site don’t track mud.
The construction process requires logistics throughout its lifespan. Common categories include mitigating risk on a jobsite, procuring and allocating resources, managing equipment and materials and communicating important information to stakeholders.
For example, a hospital undergoing renovations would require securing work permits, procuring materials, hiring contractors and subcontractors, creating plans to get equipment into the building, coordinating work hours with hospital staff, hanging signage and managing access to ensure the work site remains safe and separate from the parts of the hospital that are in use.
Most logistics are coordinated by people in a leadership or administrative role on a job site. Construction managers (CMs) coordinate much of the construction process, including coordinating and sequencing activities, laying out and managing the construction site and receiving deliveries.
Superintendents take care of daily operations such as coordinating subcontractors, supervising workers and enforcing safety regulations. Project managers (PMs) handle many of the administrative logistics, including acquiring permits, managing resources, tracking expenditures and coordinating inspections.
Key Factors of Construction Site Logistics
There are seemingly endless things to consider when managing logistics. However, there are common categories that logistics often fall into.
Site Layout and Organization
Sites need to be set up and organized to ensure work can happen effectively and safely. Common site layout and organization logistics include the placement of and systems for:
- Material storage and staging
- Equipment placement and storage
- Waste disposal
- Sanitation and bathrooms
- Signage
- Temporary structures (such as offices)
- Ingress and egress
- Break areas
- Site access points
Each site has its own limitations and constraints that need to be considered. For example, a building on a busy street being repurposed to become a restaurant might have limited space for storage and material staging. In the case of a horizontal project, such as a water pipeline, CMs need to plan to move the site as work progresses and account for changing conditions.
Permits often determine what can and needs to be done on a site. Many municipalities or other Authorities Having Jurisdiction (AHJs) provide instructions and applications to get permits on their website, such as in Orlando, Florida. Permits often state when work can happen, how to establish a construction zone around the site perimeter, what inspections will be required and any specific constraints, such as noise limitations.
PMs and CMs sometimes use preconstruction meetings to gather information that will inform the site layout. This might include information about staging of materials, equipment needs and how many people will be on site at a time. Site managers must coordinate storage for subcontractors’ equipment, often done in large steel containers on site. In some cases, sites require the construction of temporary structures, such as site trailers or mobile offices.
Material and Equipment Management
Required materials and equipment need to be managed, stored, kept in good shape and scheduled to be available when needed. Proper resource management prevents damage, injury and theft, while also helping organize the jobsite. The plan for resource management should account for many things, including:
- Storage
- Deliveries
- Inventory management
- Waste management
- Resource scheduling
- Maintenance plans and areas
- Fueling stations
- Temporary utilities (such as water, electricity and internet)
The plan for material and equipment storage depends on many factors, such as the size of the site, the nature of the project and the current stage of the construction process.
For example, resource management during the earthwork phase might include coordinating storage space for contractor equipment and securing heavy equipment such as cranes. During the finishing stages, logistical concerns change and might include deliveries and securing equipment in the building or at a different location.
In hotel construction, subcontractors might be coordinating the delivery of furniture, features and equipment (FF&E), such as beds, dressers or chairs.
Coordinating and receiving deliveries are some of the most important parts of managing resources. GCs and CMs should communicate with teams to understand when resources are needed, while also communicating with vendors to understand when resources will be available. Many GCs and CMs will use a method called just-in-time (JIT) deliveries, which aligns plans for deliveries to correspond with when they’ll be needed. This can save on costs related to storage and transportation while also reducing waste.
Effective material management requires extensive documentation, such as recording delivery times, verifying deliveries are correct, and tracking inventory. Daily logs and records are helpful tools for tracking what is on the site, how it's used, and any required maintenance.
Transportation and Access
Site managers need to have plans for how people, equipment and materials get on and around the site, and who is able to access the site. Considerations for this include defining and managing entrances and exits, security, movement on the site, traffic, parking, loading and unloading zones, walkways, and coordinating with municipalities on any road closures or traffic flow changes.
In all transportation plans, the goal is to ensure workers, vehicles, and equipment are able to enter and exit the site with minimal danger to the team and anyone working, living or simply passing through the area. For many projects, getting into the site will connect directly to a road.
In some cases, traffic might need to be detoured or slowed, which can require site managers to place signs, cones, barriers, and to hire flagging personnel to direct traffic. Many places require permits to alter traffic, such as “Blocking Right Of Way Permits” in St. Louis, MO.
Some sites are not directly accessible from a road. This is common in renovation projects, where part of a building is under construction while the rest of the building is in use. In these cases, site managers need to establish paths to access the site that are minimally invasive to the surrounding areas, buildings and neighbors. This might require coordinating with the owners of a surrounding property and establishing systems that minimize wear and tear on these routes.
Accessing the Site
Determining who is able to access the site generally depends on the nature of the project and its location. Many sites give stakeholders badges, ID cards, or keys that grant them access to the site or areas onsite that are relevant to their work. Some sites have specific requirements to receive access, such as a background check or proof of vaccination.
Some government projects require contractors to get facility security clearance (FCL), which is a determination made by the government that a contractor is able to access classified information. For security and safety reasons, most site managers prefer guests to never be unaccompanied while on site, and require visitors to have an escort. Digital tools can help manage who’s allowed on site and what documentation is required.
Communication
Systems need to be established to ensure stakeholders are aware of plans, schedule changes, delays and any other important information. This might include a construction kickoff meeting, routine briefings, OAC meetings, signage, displays with schedules and digital tools that manage and organize communication between stakeholders.
Some GCs use pull planning, which is a collaborative form of backwards planning that invites key stakeholders into the planning process and can increase communication and buy-in.
Many jobs establish numerous mediums for communication. For example, a chain of command is often helpful. Workers might share their needs, concerns and plans with a foreman, who will serve as the go-between for workers and the superintendent. However, certain systems are more efficient and effective when more people can submit questions and access documents on their own.
Construction management software allows authorized team members to submit a request for information (RFI) — and makes it easier to share responses with everyone who might be impacted.
GCs or CMs will usually manage and monitor communication systems to ensure they are functioning and fostering collaboration. However, nearly everyone on the job site must buy-in to participating and adhering to the systems in order for them to work.
Stay updated on what’s happening in construction.
Subscribe to Blueprint, Procore’s free construction newsletter, to get content from industry experts delivered straight to your inbox.
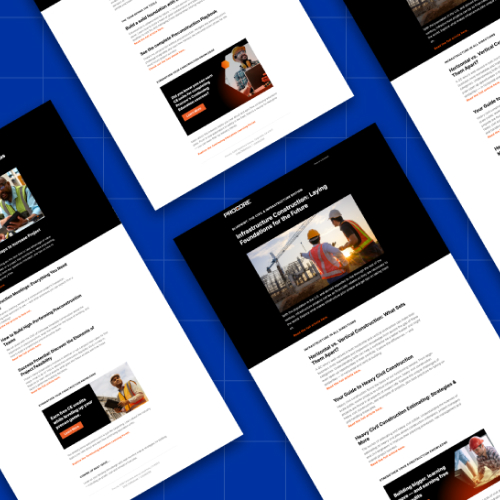
Site Logistics for Different Types of Projects
Logistical plans and concerns vary depending on the type of project, the physical nature of the site, zoning laws, construction regulations, budget, and weather.
For large projects, such as housing developments or some commercial buildings, the movement of vehicles and workers is often relatively easy because of the large amount of space available. In small sites, such as a hotel in a crowded downtown, logistical plans often need to minimize the number of people and vehicles on site. Public projects often involve more stakeholders, which can make coordinating logistics and establishing systems more complicated.
Road and highway projects, have the additional complication of having a moving work site. In Texas, for example, one mile of a roadway project might require excavating dirt, the next might require pulling clay, and the one after might require a bridge to get past a river. GCs use extensive analysis to determine what equipment, material and traffic plans are needed to navigate these changing conditions.
3 Best Practices for Managing Site Logistics
Construction site logistics requires an immense amount of adaptability, as new variables and challenges constantly emerge. However, there are a few things that usually help make coordinating logistics go as smoothly as possible:
1. Have a complete and up-to-date set of drawings and specifications.
Scheduling, budgeting and material and equipment procurement are tough to do without a full understanding of the project’s end goal. Making plans without having complete and updated drawings can lead to delays, miscommunication and having to revise plans. Construction management software allows anyone to access certain drawings and for drawings to be updated immediately.
2. Create and monitor workflows.
Construction workflows are processes for completing common sets of tasks, actions or project phases. Workflows standardize sequences of operational tasks so they can be reviewed, streamlined and repeated from project to project. This can increase a team’s adaptability, making planning easier and saving money and time. Common workflows include estimating and bidding, invoicing, RFIs, submittals, change orders and inspections.
3. Build relationships.
Logistics require extensive collaboration and communication with people beyond the job site, such as the municipality or neighbors in the surrounding area. Making an intentional effort to have open lines of communication, transparently convey information and deliberately build positive relationships can help improve the management of common logistics, such as coordinating inspections or rerouting traffic.
Site Logistics: Complex Yet Simple
Managing logistics is often extremely complex. Considering a concrete pour, which is often a finite part of a larger job, there are many variables that need to be sorted and taken care of, including the need for and availability of workers, the need for and availability of materials and equipment, receiving concrete from numerous providers, concrete inspections and the weather. However, coordinating logistics is also quite straightforward.
The goal is always to identify what a project needs to continue moving forward and find a way to make that happen.
Was this article helpful?
Thank you for your submission.
100%
0%
You voted that this article was . Was this a mistake? If so, change your vote here.
Scroll less, learn more about construction.
Subscribe to The Blueprint, Procore’s construction newsletter, to get content from industry experts delivered straight to your inbox.
By clicking this button, you agree to our Privacy Notice and Terms of Service.
Categories:
Tags:
Written by
Bryan Magargee
Bryan Magargee is a Strategic Product Consultant for Procore with a decade of experience in construction project management where he managed achitects, contractors and engineers. Bryan is focused on implementing technology to streamline processes, production and efficiency.
View profileJames Hamilton
70 articles
James Hamilton is a writer based in Brooklyn, New York with experience in television, documentaries, journalism, comedy, and podcasts. His work has been featured on VICE TV and on The Moth. James was a writer and narrator for the show, VICE News Tonight, where he won an Emmy Award and was nominated for a Peabody Award.
View profileExplore more helpful resources
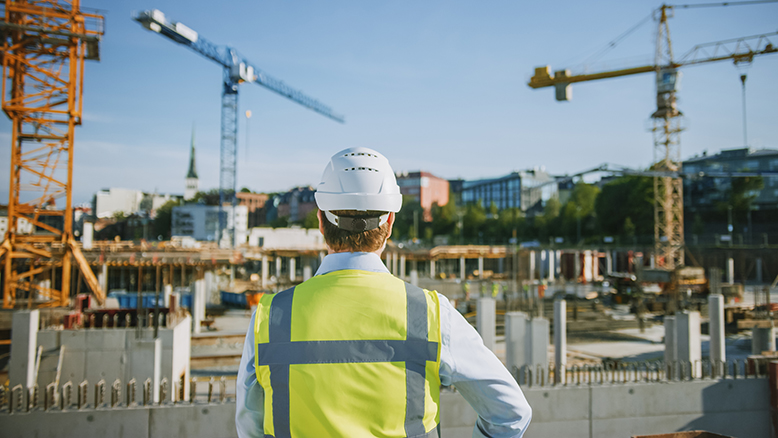
Commercial Construction Management: Mastering the Basics
Commercial construction management is no small feat: Commercial projects tend to be large and complex, and unlike residential construction, which involves repeatable tasks, can involve industry-specific and technical aspects. Commercial...
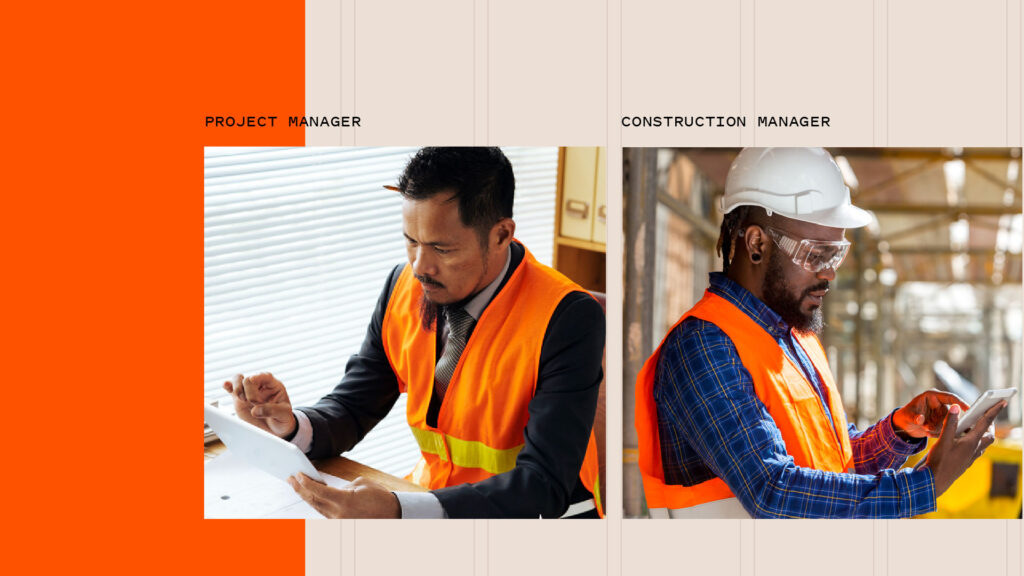
Construction Manager vs. Project Manager: Comparing Leadership Roles
Skillful oversight of construction projects allows companies to deliver to owners on time and within budget. Construction managers (CMs) and project managers (PMs) provide the necessary supervision to keep projects...
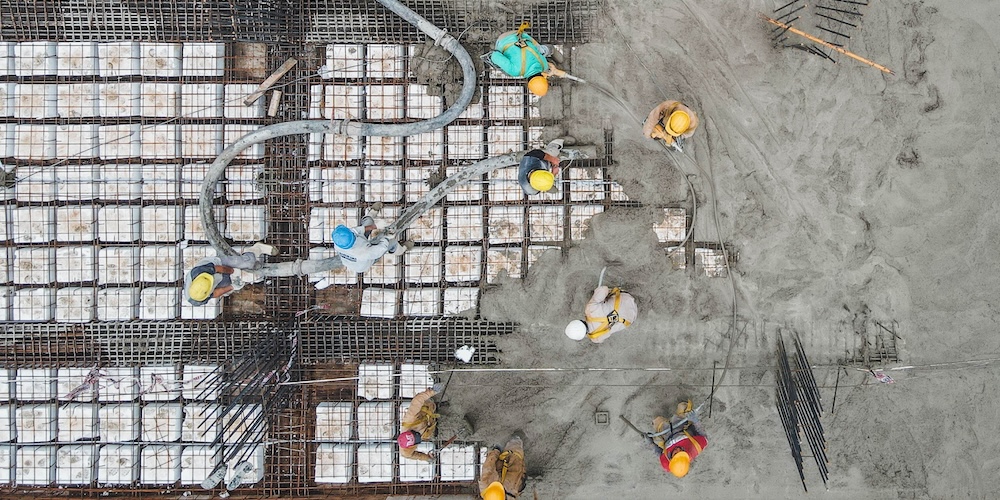
Mastering Construction Resource Management: Strategies for Success
Completing construction projects successfully requires the careful management of various resources: labor, materials, equipment, money, time and information. Since these resources are finite, allocating them wisely is crucial for minimizing...
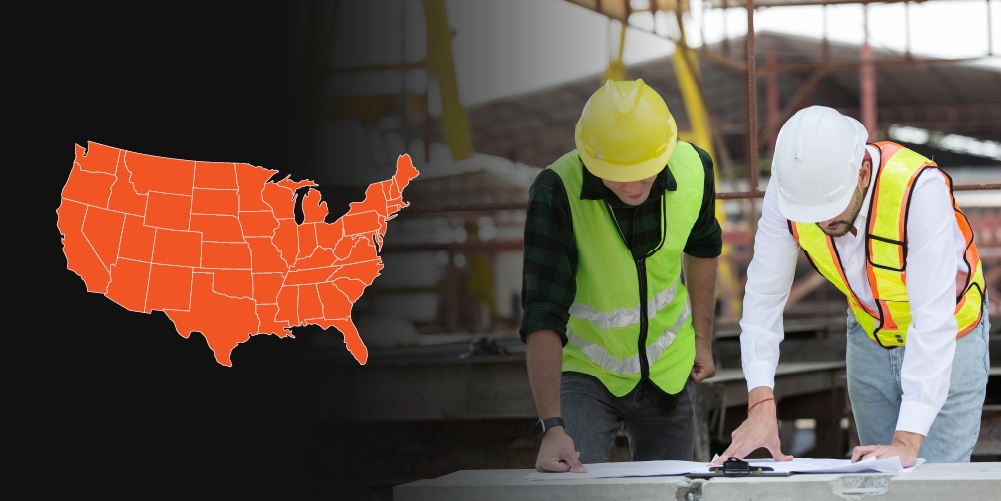
Managing Construction Projects in Different States: A Contractor’s Guide to Working Across State Lines
For many general contractors, taking on work in a new state or region can offer transformative opportunities for building a thriving business and a respected reputation. But managing projects is...
Free Tools
Calculators
Use our calculators to estimate the cost of construction materials for your next project.
Templates
Find a template to help you with your construction project tasks.
Material Price Tracker
Get the latest U.S. retail prices and view historical trends for common building materials.
Glossary
Explore key terms and phrases used in the industry.