— 12 min read
Construction Sites: The Ultimate Guide to Project Efficiency
Last Updated Sep 24, 2024
Last Updated Sep 24, 2024
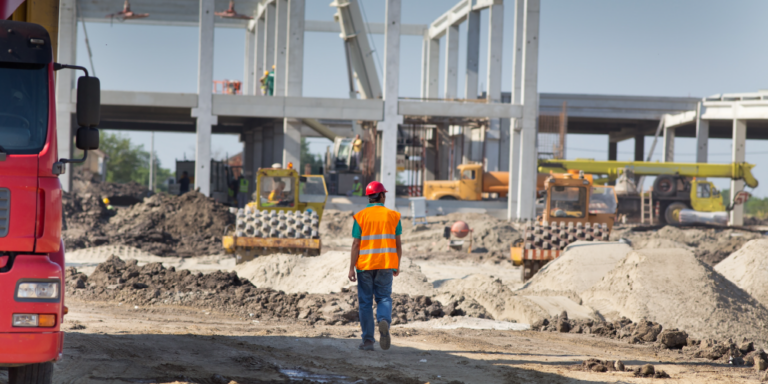
Well-built construction projects depend on well-run construction sites. Materials need to be delivered, plans need to be executed and issues need to be caught and fixed as early as possible. Effectively managing and monitoring a construction site improves the quality of the finished product, extends the life of equipment, and ensures the safety of everyone working on the project and living in surrounding areas.
This article explores the basics of construction sites, including day-to-day considerations, common roles and valuable resources.
Table of contents
The Basics of Construction Sites
Construction sites are as varied as the projects built on them: a lot for a single-family home, a hospital wing undergoing renovations, or the bottom of the ocean when installing fiber optic cables. The goal of managing a construction site is almost always the same: to facilitate the completion of the project as close to on budget, on time and at the highest quality as possible.
How to effectively manage each site depends on a range of factors, including the project type, whether it’s new construction or renovation, the site location, and the weather. A new office building in a crowded metropolitan area will require rigid plans around traffic control, deliveries, material staging, waste management and use hours. A single-family home being built as part of a new development might have work done in conjunction with other houses in the area and have an easier time storing material.
In many places, the authorities having jusridiction (AHJs) will have specific requirements for how to manage a site. This could pertain to safety, such as requiring maintained access by the fire department throughout the project, or environmental concerns, such as LEED building requirements, or California’s program to minimize pollutants from construction sites getting into stormwater runoff. In some cases, owners or funders have specific requests or requirements for how their site is managed, such as security clearance for site access or concealing the site behind scaffolding with screening until work is complete.
Learn how to successfully navigate working with AHJs on projects.
General contractors (GCs) are usually responsible for managing a construction site. Often, owners or GCs will assign a construction manager (CM) to manage the site from a macro level, while the project manager and superintendent manage at a micro level. All site leaders are responsible for making it safe, secure and efficient — but site managers are specifically charged with ensuring a site adheres to all mandates and regulations, prioritizes safety, keeps equipment and material secure, fosters positive relationships with the surrounding community and is conducive to the successful completion of construction.
Stay updated on what’s happening in construction.
Subscribe to Blueprint, Procore’s free construction newsletter, to get content from industry experts delivered straight to your inbox.
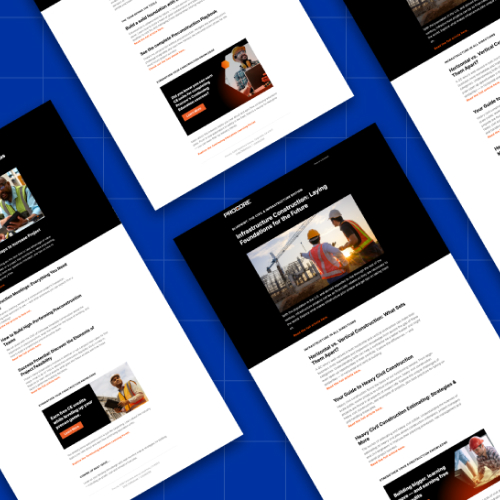
Common Roles on a Construction Site
Sites will often have different and rotating roles, but here are some common ones:
Superintendent | Also known as site managers or site supervisors. Site managers take care of daily operations on a construction site. This might include coordinating subcontractors, overseeing workers and enforcing safety regulations. |
Foreman | Foremen lead tradespeople and construction workers through day-to-day work. They relay instructions from the site’s superintendent and ensure tasks are completed correctly. |
Engineers | Engineers are often involved in planning and designing parts of a project before construction ever begins. However, engineers sometimes continue to play a role on site by ensuring the project complies with building codes and regulations, addressing structural concerns, ensuring work is done correctly, and supervising system installations. Common engineers include civil, structural and mechanical, electrical and plumbing (MEP). |
Architects | Like engineers, much of the architect’s work is done before construction begins, but they sometimes visit construction sites to ensure work is being done correctly, verify design feasibility, and approve changes. |
Equipment operators | Operators work heavy machinery like cranes, excavators, bulldozers, and forklifts. Some operators need specific training or licenses, such as crane operators in New York City. |
Laborers | Laborers carry out general tasks such as loading and unloading materials, operating equipment, cleaning the site or assisting tradespeople. |
Skilled tradespeople | Tradespeople complete specialized work on a project, such as carpentry, masonry, electrical, plumbing or ironwork. |
Project manager (PM) | PMs are responsible for the administrative oversight of a construction project. Much of their work happens in an office, such as budgeting or acquiring permits, but they are sometimes on site to track progress, manage resources, and coordinate inspections. |
Construction Manager (CM) | CMs usually supervise and coordinate the overall construction process to ensure successful project delivery. When working for an owner, a CM will provide input on design feasibility, coordinate construction activities, and manage the GC on the owner’s behalf. |
Subcontractors | Subcontractors perform specialized tasks and are often hired by the GC, CM, or PM. They operate as independent entities and may have their own team, workers and managers. |
Other common roles | Quality control inspectorEstimatorsHealth and safety advisorsEnvironment and sustainability consultants |
Construction Site Logistics
Construction site logistics refer to the coordination of operations to facilitate the work needed to complete a project. Logistics consider what happens on a site, when, and by whom. Logistical considerations are commonly divided into a few categories:
- Site layout and organization: A site needs certain things to be safe and effective, such as material and equipment storage, waste disposal, sanitation and bathrooms, signage and temporary structures such as offices. These things should be located in places that increase the site’s efficiency and don’t hinder the movement of people and equipment.
- Material and equipment management: Required materials and equipment need to be managed, stored, kept in good shape, and scheduled to be available when needed. For example, large cranes need to be placed strategically for safe and effective use, and their usage is often scheduled down to the minute.
- Transportation and access: Movement on the site, as well as entering and exiting, needs to be safe and efficient. This includes planning for and managing traffic, parking, loading and unloading zones, walkways, and coordinating with municipalities on any necessary road closures or traffic flow changes.
- Communication: Stakeholders need to be aware of plans, schedule changes, delays, and any other important information. This can include hosting meetings and briefings, managing signage or using project management tools to send messages to other parties.
A big part of managing site logistics is taking care of details so that people actively getting work done don’t have to worry about them. For example, some metropolitan areas don’t allow mud to be tracked out onto the road from a construction site. Logistics planning would manage this by putting a rumble strip on site that breaks off mud before vehicles leave.
Jobsite Safety and Security
Construction sites should be safe for everyone working there and anyone nearby who’s living, working or just passing through. Sites should also be secure so that equipment and materials aren't at risk of damage or loss and the project can continue without delay.
Safety and security are usually the responsibility of the superintendent, the PM, or, in some cases, a health and safety specialist. However, everyone on the job needs to be committed to following security protocols and creating a culture of safety.
Local municipalities, OHSA and unions often have mandates and requirements intended to make sites safe. Each project should have plans for safety and emergency preparedness. Safety and security considerations change depending on the type of project. For example, renovating the wing of a hospital while the rest of the building is in use would require strict rules around cleanliness and infection control, along with access, sound and signage.
Considerations also change over the life of a project. For example, during the early stages of building a new office building, the site might have an open hole in the ground during earthwork. Fall prevention measures and access will be tightly controlled to avoid injury. Once the building is vertical, equipment on the various floors will need to be secured and security cameras will need to be put in to ensure already installed materials aren’t taken or damaged.
Common safety and security considerations include:
- Personal protective equipment (PPE): Workers and visitors should have appropriate helmets, safety glasses, gloves, vests, and footwear.
- Access and secured perimeters: Only authorized people are able to enter, both during and after work hours. Some sites require workers to have keys, cards, or check in with a security guard in order to enter. Some public jobs require visitors to have an escort while on site.
- Fencing: The perimeter of the site should be secured and, oftentimes, covered with visual shields so the site remains inconspicuous.
- Equipment and material management: Resources should be placed and stored strategically to avoid damage and prevent unauthorized use. Many sites will have containers for workers to store materials. Heavy equipment, such as a cherry picker, might be placed away from the perimeter and stored so the bucket can’t be accessed.
- Security personnel and systems: Many places have security guards to monitor the site after hours. Other sites have security cameras installed, which has become easier to do and more affordable in recent years. Most sites should have lighting in areas where injury, theft or vandalism is a risk, such as in an office building that has been framed but not sealed.
- Training: All workers should receive safety training and, when applicable, be trained or licensed to operate heavy equipment.
- Signage: Hazardous areas and materials should be clearly marked or barricaded off to avoid injury or accident.
- Emergency preparedness: Trained first-aid personnel and first-aid stations should be available onsite. Sites need emergency and disaster plans, which should be practiced. This can include everything from transporting someone to a hospital all the way to a full site evacuation.
Stay updated on what’s happening in construction.
Subscribe to Blueprint, Procore’s free construction newsletter, to get content from industry experts delivered straight to your inbox.
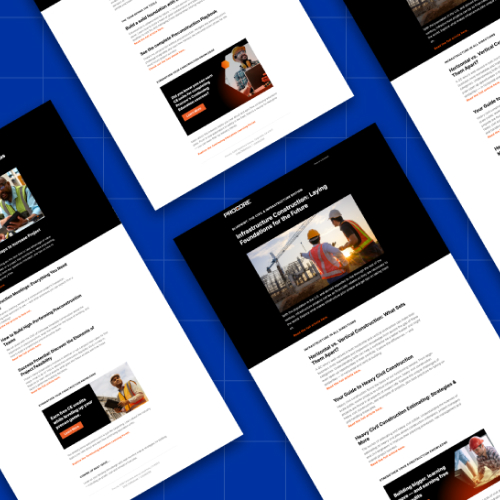
Site Access
Effectively coordinating site access is crucial for maintaining a safe and secure job site, managing resources and implementing a traffic control plan. The process of managing site access should explicitly define how the site is accessed by people, equipment and materials and who is able to be on the site.
Access generally depends on the nature of the project and its location. Many sites give stakeholders badges, ID cards, or keys that grant them access to the site or areas onsite that are relevant to their work. Most places require that the local fire department has a key and a clear path to the site in case of emergency. Some sites have specific requirements to receive access, such as a background check of proof of vaccination. On some government projects, contractors will be required to get facility security clearance (FCL), which is a determination made by the government that a contractor is able to access classified information.
For security and safety reasons, most site managers prefer guests to never be unaccompanied while on site, and will require visitors to have an escort. Digital tools can help manage who’s allowed on site and what documentation is required.
Sites need ways in and out that can be controlled and monitored. Sites are often designed by architects, who put access points in places that ensure workers, vehicles, equipment and deliveries are able to get in and out of the site.
For example, a job that requires a large amount of concrete should have a clear path for concrete trucks to get to the right place. Some projects, like airports, require each piece of equipment and machinery to be approved before being on site.
Construction Traffic Control Plan
Traffic control plans manage how site access impacts the area surrounding the site. Plans should ensure workers, vehicles, and equipment are able to enter and exit the site with minimal interference to public traffic and without putting anyone working, living or simply passing through in the area in danger. This might involve detouring traffic not related to the project, hiring flagging personnel to direct traffic, and placing signs, cones, and barriers to guide traffic.
Traffic considerations are often handled by the GC in partnership with the local municipality. Many places require permits when traffic is going to be altered, such as in Los Angeles. In many cases, traffic plans should also consider pedestrian safety by placing signage or creating safe pathways. Many places, such as New Orleans, also require permits to close sidewalks in order to establish a construction zone.
Material and Equipment Storage
Proper storage of materials and equipment prevents damage, injury and theft while also helping organize the job site. The plan for material storage depends on many factors, such as the size of the site, the nature of the project, and where it is in the construction process.
For example, the storage of resources looks different when a project is at the earthwork phase as opposed to in the finishing stages. Managing equipment during the earthwork phase of a project might look like securing equipment such as cranes and having containers on site for contractors to store materials. During the finishing stages, materials might be secured in the building or, if the site is in a crowded metropolitan area, stored in a different location.
One of the most important parts of managing the storage of resources is coordinating and receiving deliveries. Many GCs and CMs work to schedule deliveries of large equipment and materials to correspond to when they’ll be needed, as sites usually aren’t big enough to store all resources at the same time.
Effective material storage requires extensive documentation, such as recording delivery times or tracking inventory. A daily log tool allows users to track what is on the site, how it's used and any required maintenance.
The Many Considerations of Site Management
Many more things go into ensuring a construction site is effective and safe:
- Communication: Important information should be shared with the right people at the right point in the process to avoid conflicts, miscommunications, mistakes, or creating dangerous situations.
- Sustainability: GCs and CMs should have an understanding of how to run a site that is environmentally responsible, such as minimizing water usage, managing waste, and ensuring safe handling of chemicals.
- Technology: Tools such as Building Information Modeling (BIM), drones, and automated machinery can all help improve a site’s efficiency as well as create more accurate data.
- Quality control: Systems such as regular inspections and OAC meetings can help catch issues before they become bigger problems and ensure work is done correctly.
Construction sites are dynamic, busy places. Managing a site requires the ability to be adaptive, deliberate and organized. The countless details that go into site management are how projects get completed on time, on budget and meet or exceed all quality standards.
Was this article helpful?
Thank you for your submission.
0%
100%
You voted that this article was . Was this a mistake? If so, change your vote here.
Scroll less, learn more about construction.
Subscribe to The Blueprint, Procore’s construction newsletter, to get content from industry experts delivered straight to your inbox.
By clicking this button, you agree to our Privacy Notice and Terms of Service.
Categories:
Tags:
Written by
Bryan Magargee
Bryan Magargee is a Strategic Product Consultant for Procore with a decade of experience in construction project management where he managed achitects, contractors and engineers. Bryan is focused on implementing technology to streamline processes, production and efficiency.
View profileJames Hamilton
70 articles
James Hamilton is a writer based in Brooklyn, New York with experience in television, documentaries, journalism, comedy, and podcasts. His work has been featured on VICE TV and on The Moth. James was a writer and narrator for the show, VICE News Tonight, where he won an Emmy Award and was nominated for a Peabody Award.
View profileExplore more helpful resources
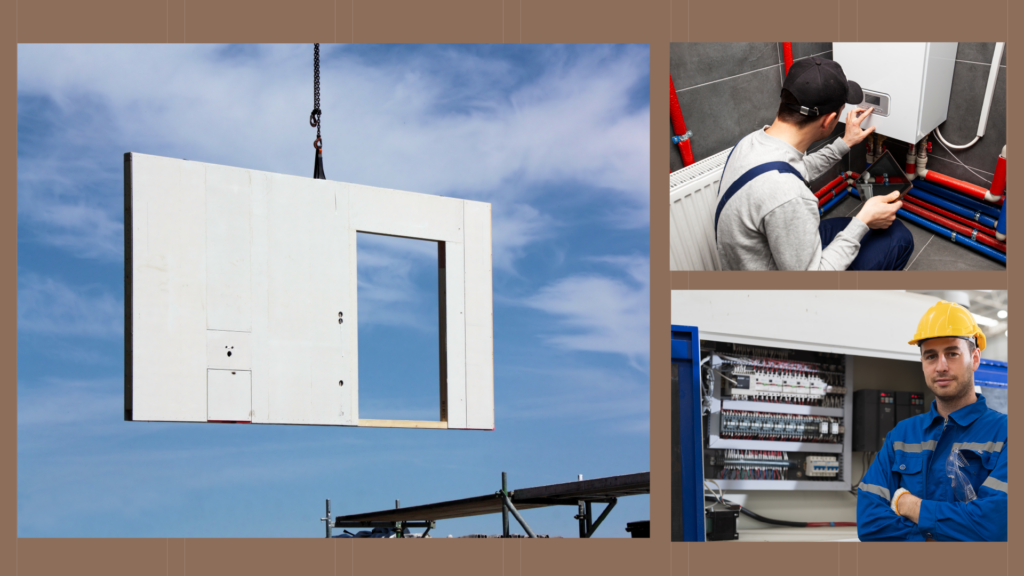
Modular Construction and MEP: A Collaborative Pairing
In an age of supply chain disruptions, workforce shortages, and rising material costs, off-site construction — including modular construction methods and prefabricated materials — is surfacing as a multipurpose solution....
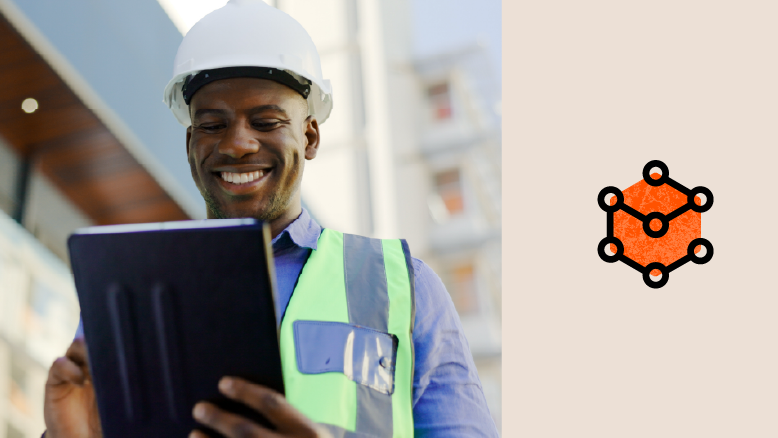
Connected Construction: Transforming the Industry Through Integration
Construction projects are becoming increasingly complex, so companies need to innovate to accurately and profitably complete these modern structures. Connected construction — using technology and data to improve communication, processes...
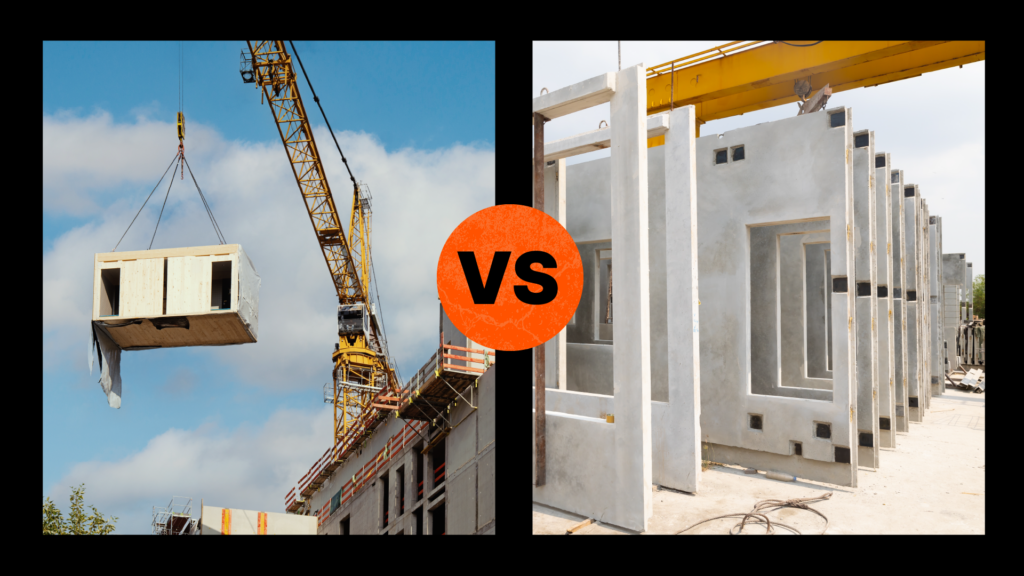
Off-Site Construction: Prefab vs. Modular
As the construction world becomes ever more competitive, deadlines get tighter and the margin for error gets slimmer, project owners around the world are always looking for an edge. Thanks...
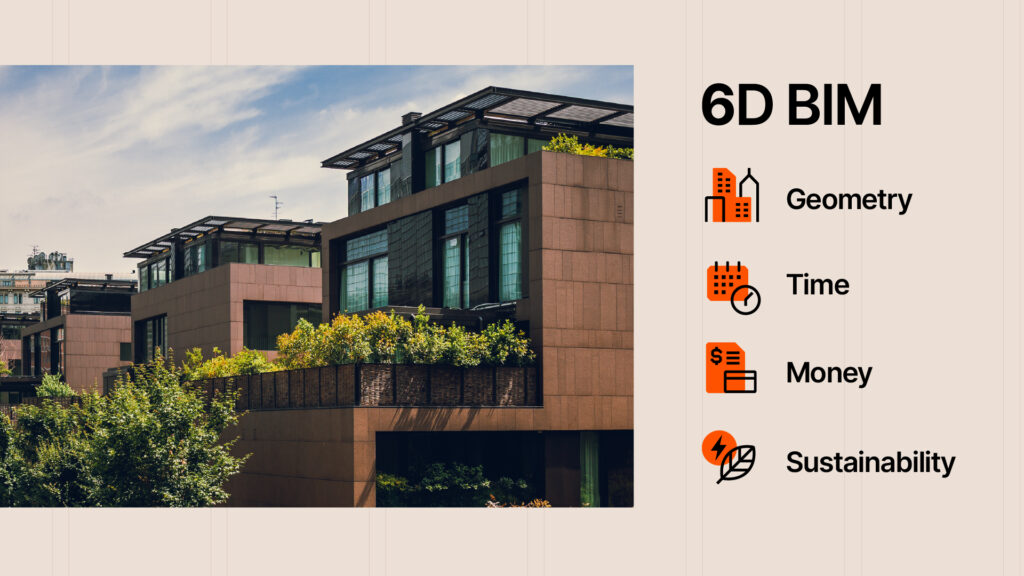
The Role of BIM in Sustainable Construction
Building information modeling (BIM) is transforming the architecture, engineering, and construction (AEC) industry. With this kind of sophisticated modeling, the industry has shifted from designing in 2D to 3D. This helps...