— 24 min read
Ultimate Guide to Submittals in Construction
Last Updated Mar 13, 2025
Last Updated Mar 13, 2025

Construction designers, architects and engineers design projects to a very high degree of detail. The design team produces drawings and specifications that prescribe the materials, equipment, and even building methods required to ensure quality. However, this level of detail means even minor deviations from the plans can have enormous consequences. Because the actual work and materials are typically provided by a variety of specialty contractors and suppliers, it is crucial that designers and contractors are on the same page.
A submittal is any written or physical information sent by contractors for approval by the design team, confirming that the materials, products, and equipment planned for construction meet the contract requirements. In this article, we’ll explore the role they play in a construction project, including common types of submittals and the information they contain. We’ll also review common submittal challenges — and what construction professionals can do to solve them.
Table of contents
The Basics of Construction Submittals
Submittals are an essential tool in the quality control process of any construction project, ensuring that contractors install materials, products, and equipment according to the project drawings and specifications.
Submittals can include product data sheets, samples, mockups, manuals, and more. Before work can proceed, the specialty contractors on the project are typically required to submit specific documentation for approval by an architect or engineer.
Many submittals are sent in before work is started, but the submittals process is ongoing throughout the project and up to closeout. Submittals provide specific detail about the materials, equipment, and systems being installed by each contractor, and sometimes the methods they are using to install them.
RFIs in the Submittal Process
While subcontractors are preparing submittals to send for design review, questions frequently arise about the drawings or specifications that need answers before they can proceed. Contractors often send a request for information, or RFI, to the design team to ask questions and request clarification to ensure they prepare the correct items.
Both submittals and RFIs are similar in that they are covered in the General Requirements of the prime contract, where the communication process between the GC and the architect is defined.
In a perfect world, all RFIs are resolved before any submittals are produced for a scope of work. But in reality, submittals might reveal new questions that need to be taken up with the design team. The submittal process and RFI process can start to intertwine and work concurrently as the subcontractors, GC and architect work through constructability issues or possibly scope gaps.
For example, if the specifications call for a hallway to be painted “gray,” the painting contractor may issue an RFI to ask for the specific color mix or product name. They could choose any shade of gray, but there’s a risk that the owner or designer will object to the shade the sub chose and require them to repaint.
However, if the specs call for “PPG PPG0994-1 Afraid of the Dark,” the contractor already knows the exact shade required. They can proceed with submittals of the paint color for the designer’s approval/confirmation. They may prepare brushouts (paint samples) or even a mock-up onsite so the designer can have a better idea of how their idea looks and performs in reality.
Types of Submittals
The most common types of submittals prior to construction include shop drawings, material samples, engineering calculations, product cutsheets, mockups, and vendor information. Other submittals are prepared during project closeout, and include items like product warranties and as-built drawings. This is by no means an exhaustive list, and it will be different for each contractor or vendor that contributes to a project.
Depending on the preferences of the design team and the GC, a specialty contractor may be asked to send individual submittals or a submittal package. A submittal package is a group of closely-related submittals. For example, an electrical contractor may submit a light fixture package containing product sheets for the 25 different fixture types used on the interior of the building.
Shop Drawings
Shop drawings are detailed plans, drawings, and illustrations that illustrate how specific elements of the project will be fabricated and/or installed. Shop drawings are commonly required for specially fabricated materials or custom-built equipment to ensure the product’s fit and function matches the design. For example, HVAC contractors often submit shop drawings of custom ductwork to ensure it complies with design requirements and provides adequate airflow, and to show the routing of the ductwork throughout the building.
Product Data
The design team often requires contractors to submit product information provided by the manufacturer. These documents, known as data sheets or “cut sheets,” contain standard details about products like sizes, performance data, preparation and installation instructions.
Material certificates or test reports may also be required to verify that an item meets or exceeds the specified standards.
Samples
Samples are physical examples of materials to be installed. The design team wants to verify that the materials match the intended quality, color, texture, or structural requirements. Common examples of samples required as a submittal include flooring, tile, and paint.
Mockups
Mockups are essentially models of a constructed element, either produced at scale or life-size using the same materials and methods to be used in the project. These are produced to verify the aesthetics and/or workmanship of the product.
Sometimes, especially when mockups are too large or unwieldy to transport, photos of the mockups may be submitted to document an in-person review of the mock-up. Mock-ups can also be a portion of the work performed onsite (in situ), which is then put on pause for a submittal review. Again, this would be documented with photos and processed like all other submittals.
Engineering Calculations
Calculations may be required to demonstrate that the work a contractor provides is sufficient for the intended application. For example, electrical contractors are often required to submit voltage drop calculations, short-circuit analysis, and load calculations to ensure the electrical system is designed appropriately and can handle the expected demands. This is especially important on institutional projects, like hospitals, where power interruptions could result in lost lives.
Vendor Information
Particularly on large commercial or public projects, the project owner often has limited visibility into the parties that the general contractor or their subs hire to perform specialized portions of the work. At times, the owner may request a list of all subs and suppliers providing work and materials on a project, along with contact information and a description of their scope of work.
Warranties & Manuals
Contractors and suppliers are often required to provide documentation about the terms of warranty coverage for products, materials, or equipment used in the project. Operation or maintenance manuals provide detailed instructions on how to operate and maintain various components or systems in the building. If these are reviewed during the construction submittal process, they might also be asked to provide actual executed warranties for the project during the closeout submittal process.
As-Built Drawings
As-built drawings, simply called “as-builts,” are the final diagrams submitted by a contractor upon completion of their work. Where shop drawings are submitted before installation, as-built drawings reflect the final product, including any approved changes to the specifications and locations of products, components, and assemblies. These and other similar record documentation is considered a closeout submittal and provided at the end of the project.
Free Class: Basics of Submittals
Master the basics of submittals with industry expert Janine Trinidad, and earn continuing education credits from AIA.

Information to Include in a Submittal
Submittal documents provide important information about the document itself, the preparer, the review process, and dates that items were sent and received. When sending a submittal package, contractors typically use a transmittal, or cover sheet, that lists all of the submittals included so the recipient can verify that nothing is missing.
- Project Name
- Spec Section: The specification number that the submittal or package corresponds to (e.g. 087100 Door Hardware)
- Submittal Number: A unique identifier for the submittal being sent
- Revision or Version Number: For use when versions of a submittal are created in response to a revision request
- Package Number: If the submittal is part of a package, include the number of the package
- Submittal Manager: Name and contact information for the person who is responsible for document management, typically a General Contractor project manager or project engineer
- Submission date: The date the submittal was sent
- Received date: The date the submittal was received
- Approver(s): Name and contact information for the people responsible for review and approval
- Response: Typically preset fields for Approved, Approved as Noted, Revise and Resubmit, and Rejected
- Notes/Remarks: Blank space for the reviewer to provide details about changes or revisions requested
One of the big advantages of using submittal software is the automated collection and tracking of most of this information. Software automatically records submission and receipt dates, commenter names, and contact information, helping to prevent errors or miscommunication that are common with a manual process.
The Submittals Process Explained
There is no one-size-fits-all approval process for submittals. A well-designed submittals process strikes an appropriate balance between quality control and speed. If the approvals process takes too long, it could delay a subcontractor’s procurement process and disrupt the project schedule down the line. If it happens too quickly, details can be missed or items approved without adequate review.
In general, there are four primary steps in the submittals process on any construction project.
1. The general contractor creates a submittal schedule.
The first phase of the process involves creating a submittal schedule that outlines expected timelines for all project submittals. It also identifies who is responsible for each submittal and includes projecting approval timelines.
The general contractor on a project is typically responsible for making this schedule in a sequence that minimizes potential delays. For example, they will schedule submittals for materials with long lead times before submittals for final trim work.
2. Contractors prepare submittal documents.
Once the schedule has been created, contractors and subcontractors are given the green light to begin preparing their submittals documents. During this time, the specialty contractor reviews the project specifications and plans related to their scope of work, including any performance criteria, applicable codes and standards, as well as any specific brands or models that have been specified by the design team in the contract.
Then, the specialty contractor compiles the relevant documents and information (such as shop drawings, project data, materials samples, etc.) that they’ll need to include in their submittal. Depending on the submittals schedule, or requests from the hiring party, a specialty contractor may send single submittals on a single part of the design — like the concrete mix specifications — to get it approved earlier than other activities of the project that are built or performed later.
Other times, they compile everything into a single submittal package to be sent up the chain. Once they have all the required information, the contractor sends the single submittal or submittal package to the GC for review.
3. The design team reviews the submittals.
Upon receipt, the GC reviews each submittal to confirm the information in the submittal aligns with the project specifications detailed in the contract. The GC may also review the submittals to catch any discrepancies or errors before sending the submittals to the design team for review. The best GCs have a keen eye on how submittals from each specialty contractor fit together. For example, execution schedules, and compatible materials between two specialty contractors can save time and money avoiding change orders in the future.
The design team (which could include the architect, engineers, and a construction manager or owner's rep) also reviews the submittals after the general contractor’s initial review to ensure that the information in the submittals aligns with the design requirements.
4. The design team responds to the submittals.
If the submittal documents match what’s specified in the contract and design documents, then the design team will mark the submittals as approved and send back to the GC for distribution to the subcontractor to begin working on the project.
If a submittal is approved, the contractor can begin work.
There are instances where the design team may approve a submittal, but only after certain conditions are met. They may respond with approved with conditions, approved as noted, or approved with corrections. In this case, the design team may note any corrections or changes that need to be made to the submittals for the subcontractor to address, but the subcontractor isn’t required to resubmit the documents before getting started.
If the submittal is rejected, the contractor must resubmit.
Submittals may be rejected if the materials or information submitted by the subcontractor differ from what’s been outlined in the contract documents. Submittals that lack detail about materials or the scope of work to be performed could also result in a denial.
If a submittal is denied, the contractor must create a new submittal that sufficiently addresses the reason for the denial in the initial submission.
In order to help mitigate prolonged wait times or additional steps in the process, it’s important for contractors to make sure their submittals are in line with the information specified in the contract documents, along with any additional information shared by the design team.
The best construction companies continually evolve and update the process to get submittals approved and materials on the jobsite as efficiently as possible.
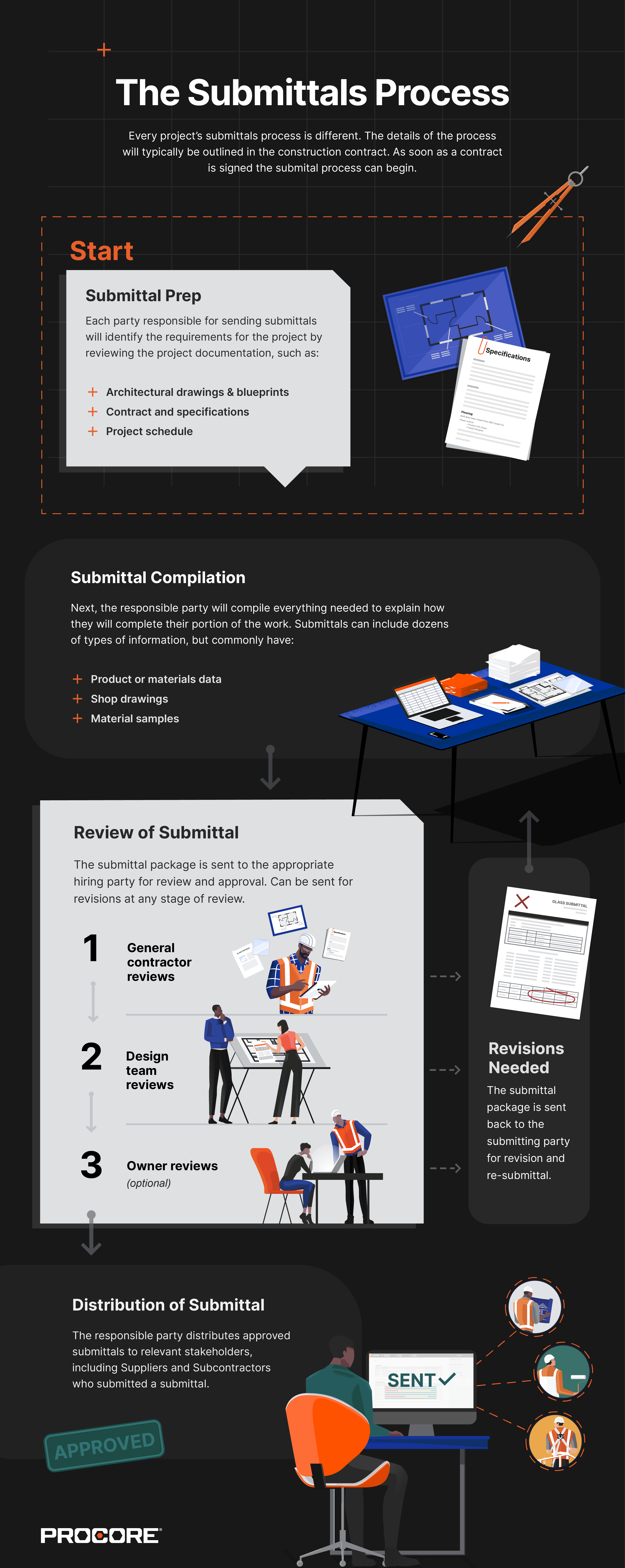
Process Roles & Responsibilities
While specialty contractors are responsible for putting together the actual submittals for the work they will complete, everyone on a project plays a part in the submittals process. Let’s take a look at each party involved in the submittals process, from the top to the bottom, and review who does what, and when, to make sure things go as smoothly as possible.
The Project Owner
Owners are rarely directly involved in the submittals process. They hire construction managers, architects and engineers for a reason. A smart owner knows that each step in the submittal process can slow down the project.
The Design Team
The design team – typically architects and engineers – are generally the main decision-makers in the submittal approval process. They review submittals and compare them to the specifications to confirm they meet the project requirements.
Construction Manager or Owner's Rep
If the owner hired a Construction Manager or Owner’s Rep to oversee the project, they will likely be a key decision maker in the submittals process. The CM typically represents the owner or design/architect teams and thus has similar responsibilities (depending on the structure of the project). They are hired to ensure the successful completion of the project and as a result have a big stake in the outcome of the project.
General Contractor
The general contractor plays several roles in the submittals process. First, they are responsible for document management – scheduling and organizing submittals from their subcontractors. Once they receive the required submittals, they typically perform a high-level review, verifying their conformance to both the prime contract and subcontract.
After review, the GC forwards submittals to the Construction Manager or design team for approval. The GC is also typically responsible for managing the communication process between their subcontractors and the design team to ensure that all required submittals are approved on time.
Subcontractor
Subcontractors perform much of the heavy lifting in the submittals process. They are tasked with understanding the project requirements from the architect and design team, and explaining in detail how they will do the work. They package up information from their suppliers and fabricators, detail what they will install, how they will install it, and when they will do the work.
Suppliers And Fabricators
While suppliers are typically not directly involved in the process, they are working closely with the subcontractor responsible for sending the submittal up the chain. For example, a supplier may put together a quote with lead times, product spec sheets, and other relevant information that the subcontractor will use as part of the submittals package.
Common Variations in the Submittals Process
The process for submittals review is typically set by the design team and outlined in the construction contracts. The general contractor will be collecting submittals from all the subcontractors, and packaging them to deliver to the design team. However, the flow of this process may see some significant variation depending on the project type and wishes of the owner and design team.
The process for submittals can vary for different stages of a project. For example, the owner may want to be heavily involved in the interior design submittals and approve every page of information. That same owner may also trust that the GC will make sure the electrical aspects are completed correctly, and won’t want to look at the electrical submittals.
The GC’s role in this process is to make sure the submittals from various specialty contractors interlock like a massive jigsaw puzzle. That jigsaw puzzle needs to be presented to the design team at various stages and match the initial vision for the project. Depending on the scale of the project, (i.e. the number of parties involved) and the involvement of the top-of-the-chain parties like the owner or developer, the process itself can vary widely.
The Goal: Streamline Communication
The submittals process can vary greatly. Even construction on the same type of building with the same GC and design team as previous projects can result in changes in the process. Always read contract documents carefully and prepare submittals to be approved, or approved with conditions on the first go around. The submittals process is an exercise in communication, and communication is hard.
Some processes are relatively straightforward, and progress in a straight line to the architect and back to the subcontractor.
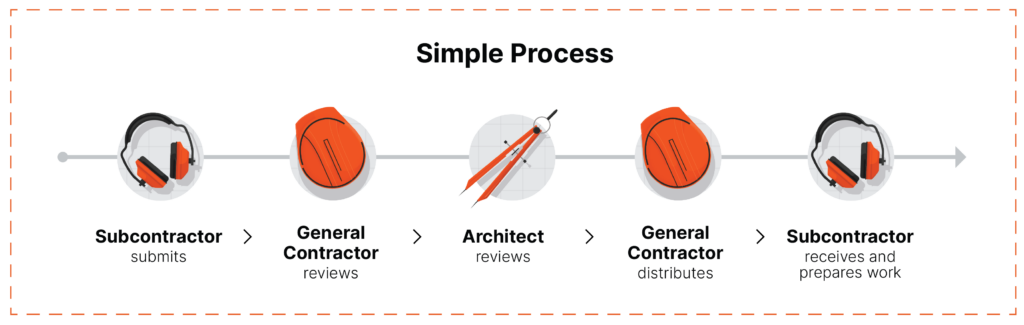
On some projects, the submittals process can be much more complex, with approvals required from additional parties, like the Construction Manager, Engineer, and/or Owner's Rep.

Even when the process is "simple," a reviewer may return submittals to the subcontractor for revision several times before they make it to the designer or Owner's Rep whose issues the final approval required for work to commence. The more parties involved in approvals, the longer the submittals process is likely to take.
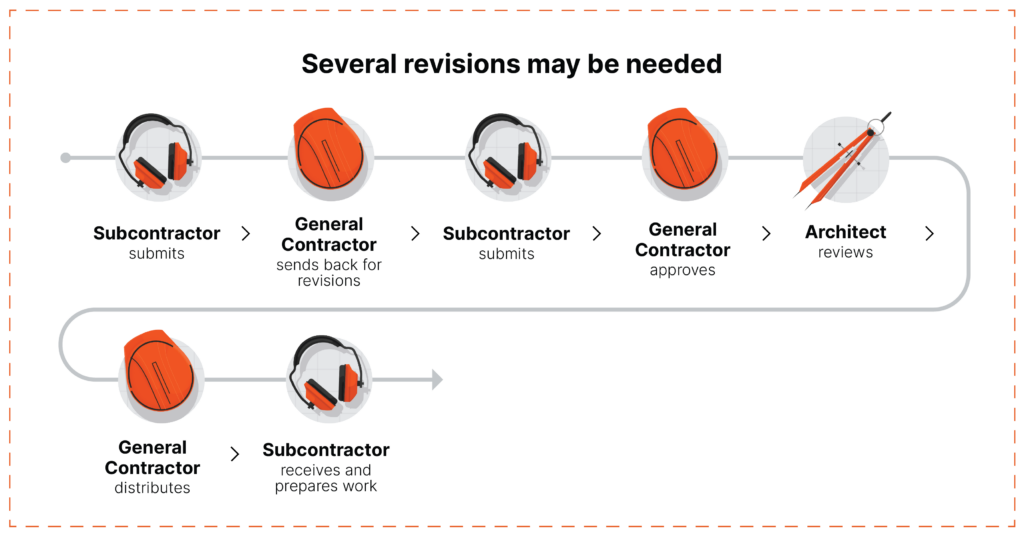
Design teams, GCs, and specialty contractors should always be looking for ways to improve the submittals process. The use of technology and cloud-based software to track and organize submittals can greatly reduce review time and errors in the process. Because it makes all communication contained in a single place, it is easy to see the status of all submittals on a project -- and who needs to take action.
Key Factors That Affect Submittals
There are certain conditions that may affect the timing and speed of the submittals process. After the design phase is over and the contract is finalized, there are several factors that will influence when submittals start rolling for each stakeholder. Project size, lead times for materials, and the construction schedule can factor into how quickly submittals should be processed. Below are six factors that impact the timing of the submittals process:
Project scope and complexity
Larger and more complex projects may require more submittals than smaller projects, and an earlier start to the submittal process. This could be due to the amount of components, scope of work, and amount and types of materials needed to complete the project.
Contract documents
The terms stated within a contract may dictate when the submittal process should begin. More importantly, the contract will state expectations for review durations and response times among the parties. Some contracts may specify a particular timeline for submittals, especially for projects with strict deadlines or complex coordination requirements.
Specifications
The spec book provides all of the details subcontractors need to identify the correct materials and collect documentation from their suppliers or fabricators. Clearly detailed specifications make it easy for specialty contractors to identify the submittals needed. If the specifications are unclear or ambiguous, subcontractors will need to submit RFIs to clarify the requirements and ensure they are submitting the appropriate documentation. Reviewing and responding to RFIs will add more time to the entire process.
Stay updated on what’s happening in construction.
Subscribe to Blueprint, Procore’s free construction newsletter, to get content from industry experts delivered straight to your inbox.
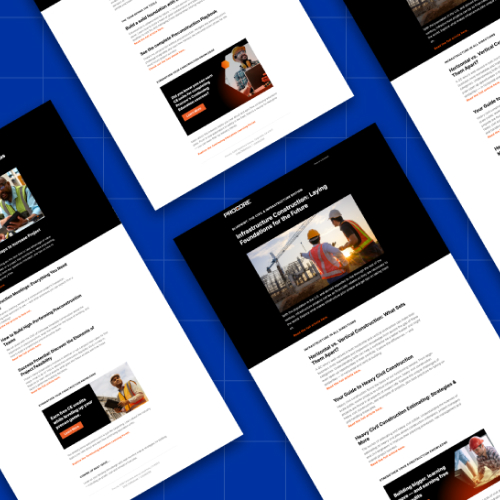
Submittal Preparation & Testing
Contractors can prepare some submittals, like cut sheets, in as little as one day. Others, like mockups, off-site testing, or shop drawings for custom fabricated items take time to prepare.
For example, a concrete contractor may need to mix, pour and cure a sample cylinder for compression testing to ensure it meets the engineering requirements. This can take anywhere from 48 hours to several weeks – if the test results are rejected, they may need to perform the test again, adding additional weeks to the process.
Lead times
Materials or equipment with longer lead times (such as window systems, electrical transformers, custom flooring, precast concrete elements, or elevators) typically require submittals to be turned in earlier to prevent project delays.
Submittals need to be reviewed and approved before these items can be ordered, so starting the process sooner may help ensure they arrive on site when needed. Specialty contractors should monitor changes to their supply chains closely and communicate potential disruptions or material shortages to the GC and design team. They may need to expedite submittals to ensure materials and equipment arrive on time.
Stakeholder availability
The availability of key project stakeholders such as architects, engineers, and the client can influence the submittal workflow – especially for down the specialty contractors. If the review and approval process of submittals is expected to be time-consuming, or the reviewers have other projects on their plate, it is important to get submittals sent to them by a certain date so that they don’t delay the project’s progression.
Regulatory requirements
Some regulatory or certification requirements may determine if the submittals process should begin earlier on a project. For example, projects aiming for specific green building certifications might need to start submittals early to ensure compliance with the certification requirements.
Construction schedule
The overall construction schedule plays a crucial role in determining the start of the submittal process. An accelerated construction schedule may require an expedited submittal process with either a reduced number of reviewers or faster turnaround times for each stage of approvals. Generally, submittals for work items that fall on the critical path need to be prioritized to avoid delays to the project schedule overall.
Solving Common Submittal Challenges
The success of a project relies on a submittals process that requests, collects, reviews, and distributes submittals with a large number of stakeholders. A lot can go wrong with timing, accuracy, communication and more. Let's take a look at some of the most common challenges — and how to improve them.
Submittal Tracking & Accountability
With hundreds or thousands of submittals and dozens of people involved in the review process, tracking the status of each document is one of the biggest challenges in the submittals process. Knowing where each submittal is in the process — and who is responsible for the status of each one — is critical. This is a particular challenge for contractors or owners following a manual process with physical paper submittals. If multiple reviewers leave comments on a submittal, it isn’t always clear who wrote each one — or which response was created first.
It is important that everyone in the submittal process can clearly identify the source and date of each comment. In the past, when everything was done with pen and paper, reviewers often used a unique ink color. Software has greatly streamlined the review process, making it easy to see whose court the ball is in at any moment.
Version Control
Version control is a particularly difficult challenge when a project is using a manual or paper process for sending and tracking submittals, especially when multiple reviewers are involved. Contractors and designers can end up referencing different document versions. If an architect or engineer marks up a document, those notes may be lost in subsequent versions, making it difficult for them to track whether or not the contractor adequately addressed them.
Submittal software helps ensure that everyone can easily identify the most current version of a submittal and view the history of comments and revisions.
Subcontractor Coordination
Subcontractors typically have limited visibility into the overall plan for submittals, which can cause confusion up and down the submittal chain. The general contractor needs to create a submittal schedule based on more than just procurement lead times, and coordinate work closely between subcontractors.
Architects and engineers often want to review submittals for adjacent systems simultaneously to ensure they will work together. When those submittals are coming from two different subcontractors, the GC needs to communicate timing needs to both. Sharing 2D overlays or BIM files with specialty contractors can help them understand how they fit into the overall plan — and identify potential causes for submittal revisions in advance.
Some submittals require even closer subcontractor coordination. For example, a mockup for an advanced waterproofing system may require contributions from multiple subs in advance and requires scheduling the work on the mockup around other site activities.
GCs should take a holistic approach to communicating submittal needs to their subcontractor teams. A regularly scheduled submittal meeting with reps for each trade keeps everyone on the same page, and using BIM or other 3D models in conjunction with standard submittals can help subs see the bigger picture. For complex systems, 2D overlays are often not sufficient to show building constraints.
Approval Delays
A smooth submittal review and approval process is critical to keeping the overall project on schedule. The approval workflow needs to be clearly communicated to all contractors and reviewers. But it also needs to be flexible enough to accommodate changes.
Approval delays can have a waterfall effect on a project, causing further delays down the line. Submittals for materials with long lead times or jobsite work in the early parts of a project are the most important to get compiled and approved quickly. The cascading effect of delayed submittals in any point of the process can derail the overall schedule.
Logically, submittal managers also prioritize review for materials with long or unknown lead times. In some cases, they may need to arrange concurrent reviews to expedite time-sensitive submittals.
Communicating the priorities of construction activities with the submittal reviewers is key to expediting the process. Making weekly status updates on what submittals are in progress and in the pipeline is recommended.
Once approved, submittals should be sent to all appropriate parties so everyone in the field is working from the same page. Any delays in passing the approved documentation along, even if just a day or two, can impact the material ordering process and place a project low in the manufacturing shop’s queue.
Miscommunication
The submittal process is complicated by the hierarchy of contracts: The architects and engineers rarely have a direct line of communication with the specialty contractors who bring their designs to life. Contractors are siloed from the design team and from each other. Poor communication is the cause of most construction challenges, and submittals are no exception. The entire submittals process is a complex exercise in cross-party transfer of highly detailed information.
Submittals should be a standing agenda item at project meetings to communicate status updates and hold responsible parties accountable. In many cases, rather than pushing comments between an architect and subcontractor, it’s easier to schedule a submittal review meeting to get them in the same room (or at least in the same Zoom). Crucial conversations avoid potential delays and financial disputes.
The responsibility doesn’t lie exclusively with the general contractor. Each specialty contractor is contractually obligated to comply with the specifications — which include the listed submittals. Contractors should issue RFIs early and often to resolve questions about material requirements or submittal workflows. Ask for access to 3D drawings or overlays that show how systems interact and review them during the submittal process to avoid clashes when installing in the field. These communication practices all help to reduce rework, costs and interruptions to the flow of work on site.
Bridging the Gap Between Design & Build
Submittals are a critical piece of the construction project puzzle, an essential lifeline between the teams designing the project and those actually building it. Submittals require careful scheduling, communication and attention to detail in order to prevent costly mistakes or delays. Despite the challenges, when handled correctly, a streamlined submittals process is a powerful tool to execute construction projects of any level of complexity.
Was this article helpful?
Thank you for your submission.
100%
0%
You voted that this article was . Was this a mistake? If so, change your vote here.
Scroll less, learn more about construction.
Subscribe to The Blueprint, Procore’s construction newsletter, to get content from industry experts delivered straight to your inbox.
By clicking this button, you agree to our Privacy Notice and Terms of Service.
Categories:
Written by
Janine Trinidad
21 articles
Janine Trinidad is a Construction Educational professional for Procore Technologies. In previous roles, Janine managed all phases of construction on hotel, mixed-use, and institutional projects in the San Francisco Bay area. She was responsible for negotiating contract budgets and change orders, managing RFIs and submittals, and overseeing quality control, among other duties. She is also a certified transformational coach with a focus on women-centered and trauma-informed methods. She is passionate about transforming the construction industry to be a healthier, more successful and welcoming place to work and believes technology and education are allies in doing so.
View profileAnthresia McWashington
19 articles
Anthresia McWashington is a Content Manager at Procore. She previously worked as an editor and reporter for Gulf Energy Information and Houston Media Group. She earned her BA in Communications and Journalism from the University of Houston. Anthresia loves track & field and practicing her French. She lives in Houston.
View profileExplore more helpful resources
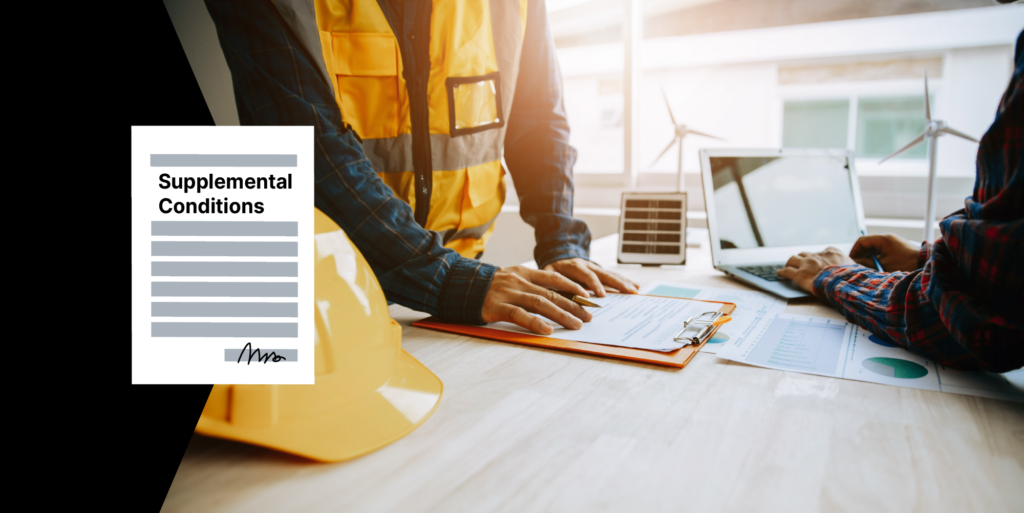
Understanding Supplementary Conditions on Construction Contracts
No two construction projects are exactly alike — and the same goes for construction contracts. Even when using a standard contract form, owners and contractors sometimes use supplementary conditions to...
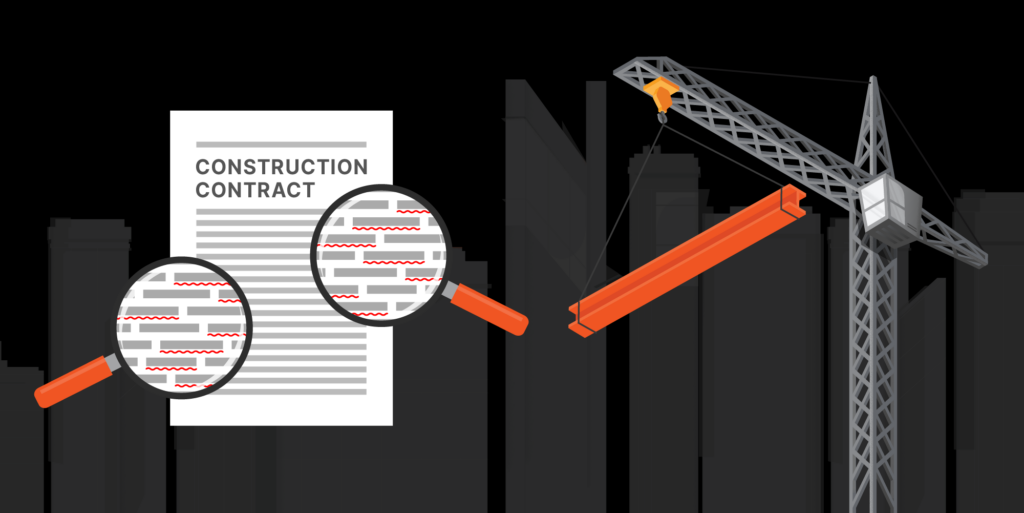
A Straightforward Guide to Construction Contract Review
Construction contracts are like the glue for the project team. They’re the ties that bind the working relationships and goals for the project, containing information about responsibilities, liabilities and processes...
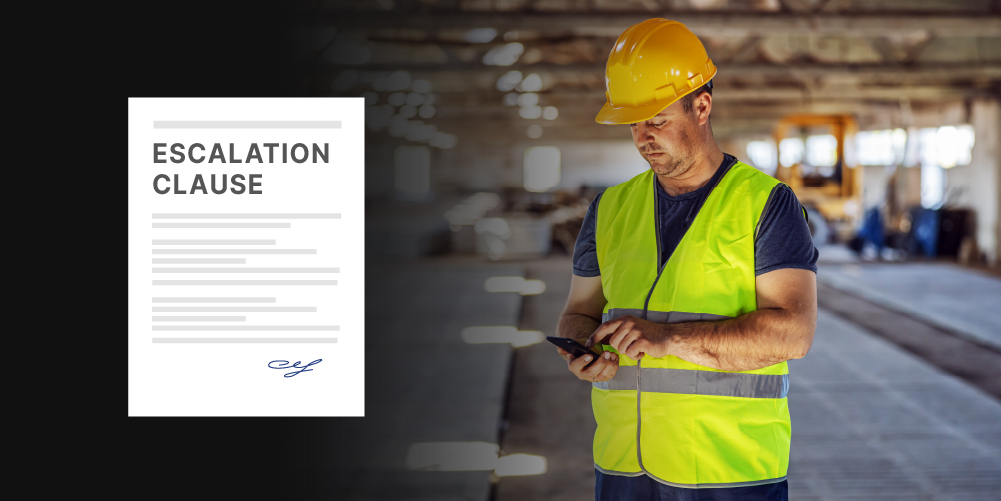
Escalation Clauses in Construction Contracts: When and How They Apply
In construction contracts, an escalation clause allows for the escalation of a certain price for labor or materials to be used in a construction project. This type of clause is most...
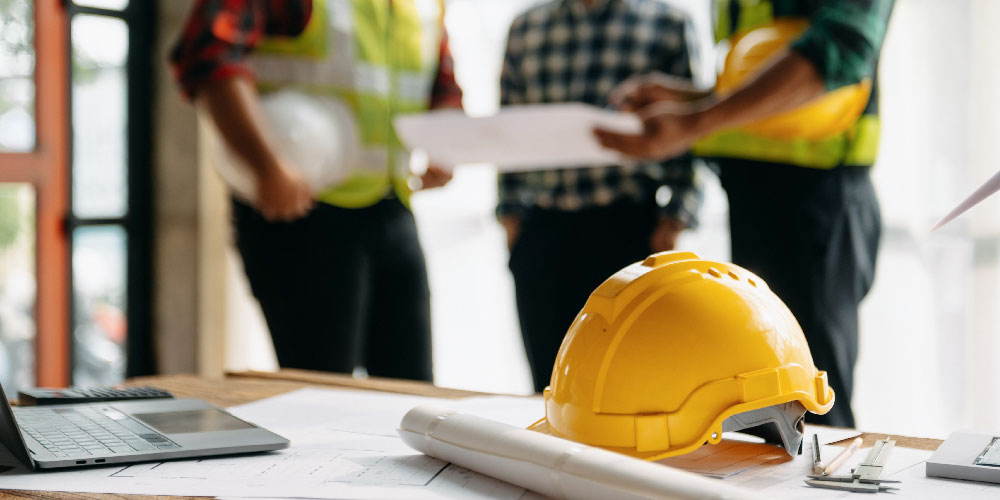
Scope Gap: Addressing Ambiguous Project Requirements
To turn contract documents into an actual building, every construction project requires stakeholders to complete certain items of work. Ideally, the scope of work outlines those items and clarifies who’s...