— 9 min read
The Importance of Construction Teamwork: Build a Solid Foundation With the Right Team
Last Updated May 14, 2025
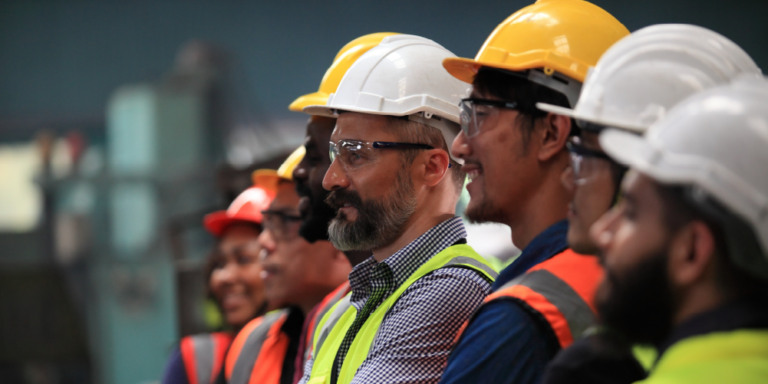
Construction is an industry of collaboration — no one person completes any job on their own. It could easily be argued that the most important skill for anyone in this field, besides being capable of doing the actual work, is the ability to work with others.
While fostering good relationships can be a valuable way to reduce risk and keep crew members motivated, allowing bad relationships to fester on the jobsite can have adverse effects that carry over to other projects — and can even ruin client relationships.
This article explores how to choose a successful team of collaborators, what to do when team relationships break down and how the atmosphere created by the general contractor (GC), project manager (PM), and other on- and off-site leadership can ultimately affect the consistency and quality of the completed project.
Table of contents
Assembling the Right Team
Forming the best crew for a job is the first step to making sure that all its members work well together. Of course, all employees on a construction site must be qualified and able to comprehend the basic functions of their jobs. But the most reliable teammates will also have an understanding of the full scope of the work, outside of their own tasks. Below are some qualities project leaders should look for when putting together a team.
Focused Leadership
A cohesive group starts with clear, focused leadership. The GC, PMs, and superintendents set the tone of their workplaces from day one. They can demand respect, or command it by communicating their vision to the larger workforce early on, letting everyone know they are on the same team.
Creating a culture of teamwork means having leaders who are set on building strong relationships between team members, subcontractors, designers, and the project owner. When the entire group understands the goal and shares the same values, it's easier to tackle challenges and make sure the project succeeds.
Varied Experience
It's beneficial to seek crew members who have worked across several trades or in different capacities across the jobsite. For example, a project manager who has also had experience as a tradesperson is will likely be able to understand more of the work’s scope than someone who’s only worked office-side.
Workers with experience in several areas can empathize with others who might be performing jobs they’ve had in the past. They know firsthand what their counterparts need and expect; they can more easily anticipate each others’ needs and share information. In this way, finding these types of crew members isn’t just a way to encourage compassion on the job site — it can also reduce the risk of rework.
Additionally, prequalifying subcontractors helps ensure high expectations and standards by the general contractor are met. Subcontractors should be skilled, reliable and responsible to reduce the possibility of any issues that may cause project delays.
Sets Others up for Success
It’s common for tradespeople to work in shifts and pick up where another construction crew left off, especially on larger projects.
Crew members should be considerate of their teammates on other shifts and help set them up for success. Keeping work areas clean and organized, and having clear communication channels to inform incoming crews of where the former shift wrapped up makes transitions much smoother. Personalities range, and construction sites can be places where people of vastly different backgrounds meet.
Solutions-driven
Finally, the most important aspect of a good team member is being solutions-oriented. Construction work is fast-paced and requires flexibility on every level. The best workers on the jobsite are not only those who can identify problems that will delay the project but also those who bring potential solutions to their supervisors so that the project can keep moving forward.
What Good Teamwork Looks Like
Teamwork is much like mitigating safety concerns — if it isn’t maintained, it’s hard to get it back. But strong teamwork almost always results in strong job performance. Most people genuinely want to do their jobs well and take pride in them — so creating a healthy environment for each crew member to thrive can be considered an unsung part of the quality control process.
Communication
When challenges arise on a construction site—for example, if a plumber finds an HVAC duct in their way when trying to install pipes to finish a space—communication plays a huge role in how quickly and effectively a problem gets solved.
In a jobsite with good teamwork, the plumber may call the superintendent to help figure out a rerouting solution. This also allows the superintendent to make any necessary adjustments to the master schedule if rerouting ductwork interferes with the work of other trades. But in a less-communicative workplace, the plumber may think the duct is unnecessary and break or remove it to get back to their task—and leaving the now-broken duct for someone else to fix.
Daily standup meetings with crews to lay out plans and expectations for the day ahead keep everyone on the same page about changes and expectations. It also gives teams a chance to chime in with any updates or information that came from the day before.
Collaboration
In addition to open communication, work environments that foster collaboration amongst teams helps build strong relationships and offer opportunities for better efficiency. Good teamwork often results from a strong company culture that promotes collaboration rather than competition.
Rotation programs, for example, help team members understand different roles within a company. Allowing workers to gain some experience in different roles fosters empathy and deeper understanding of how certain tasks are performed and allows teams to rely on one another to resolve issues that may arise.
Expert Insight
Let's look at the Second Avenue subway expansion project in Manhattan as an example of teamwork in action.
The subway construction team faced a challenge with the tunnel boring machine (TBM), which required freezing the soil to dig through it. Traditionally, this is achieved by inserting steel pipes and circulating a glycerin solution to keep the soil frozen.
However, project executives and engineers worked together on a more efficient approach. By assessing the materials needed along with other options, they found that using aluminum pipes instead of steel could greatly reduce both costs and complexity. Aluminum pipes allowed the TBM to cut through the aluminum, eliminating the need to remove the steel pipes from the ground later. This collaboration between the project managers, engineers and suppliers saved both time and millions of dollars.
Construction work has high premiums for missing deadlines. Collaborating across teams and trades, both laterally and vertically, is an integral part of making sure that the job is handed over on time.
Respect
Good teamwork also means respecting the chain of command. One of the most critical relationships on a construction site is that of the superintendent and foremen. Communication between these roles is necessary, especially if workmanship concerns arise. If there’s an issue with a crew member, superintendents should address the problem with their foreman, who has an established relationship with their crews, to manage the concern
Passing over this hierarchy to speak directly with the crew member could make a foreman feel disrespected — and nobody wants to do their best work at a job where they don’t feel valued. Having trust in appointed leaders and their relationships with their teams is key for both project efficiency and streamlined communication.
The Consequences of Bad Teamwork
Hiring the wrong crew member for a job can have negative consequences. It’s not unheard of for someone like this to become a foreman or other management role, and then a whole team suffers because of one person’s attitude toward the work.
One bad fit can tear down a workplace. For a team in decline, the construction site can begin to look messier — with crew members not picking up after themselves — and the communication between them beginning to erode. To prevent problems, it’s important for the site superintendent to monitor the emotional state of their employees as much as the work itself.
Establishing a culture of transparency encourages team members from the top down to share any work or personal concerns that may affect their performance, or the performance of others. Avoiding communication silos allows site leaders to have visibility into what’s happening with crews and vice versa.
When issues are neglected, they can lead to a boiling point: accidents or near-accidents, arguments and fights, equipment damage or worse. Stopping the work to address these matters is a proactive way for site leads to regain control over the environment.
Stay updated on what’s happening in construction.
Subscribe to Blueprint, Procore’s free construction newsletter, to get content from industry experts delivered straight to your inbox.
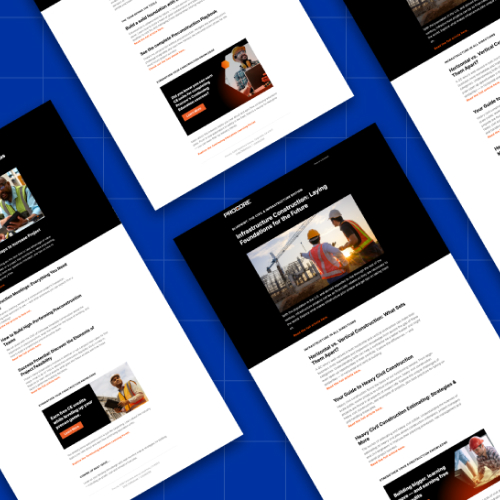
Navigating Conflict With Team Members
It can be very difficult to reverse the damaging effects of letting bad teamwork fester. In moments of conflict or discord, site leadership should try the following to get teams back on the same page.
Lead with empathy and understanding.
Site leaders should make time to know both their foremen and the crews they are working with. Prioritizing worker well being and relationship building from kickoff can help keep conflicts at bay.
Start with solutions.
Problems or issues come a dime a dozen. Encourage teams to present resolutions or suggestions for issues that they encounter to help keep tasks — and everyone involved — moving forward.
Take ownership.
Foster an environment where team members aren’t hesitant to take ownership for mistakes. The sooner people communicate any hiccups, the quicker resolutions can be discussed and implemented.
Remember the end goal.
It’s easy to get caught up in the stress surrounding jobsite work or administrative duties. This increases when timelines are truncated or delays begin piling up. Instead of adding to the pressure, leadership should remind workers of the bigger picture: completing a project that meets quality standards, and everyone working to get it done together.
When tensions are high, leadership should remain compassionate and understanding. Taking time to hear people out and lead by example when it comes to resolving conflicts can redirect crew members and other leaders to focus on the task at hand.
The Bottom Line on Teamwork
When a workplace has good teamwork, the energy is palpable. By setting a standard of empathy, care and rigor, the site leadership can help create a flywheel of positive reinforcement across the worksite — so that workers are helping each other solve problems instead of getting in each others' way.
In the best cases, these kinds of relationships become mentorships, with younger team members asking questions and learning from more experienced folks on the job. These are also the kind of relationships that can carry over into the next job. If a group of people can work well together on one job, they’re likely to be able to do so again.
So investing in these relationships, and fostering a mission of teamwork across a project, is an effort of foresight: a little conflict resolution and compassion in the short-term can have great benefits in the long run.
Was this article helpful?
Thank you for your submission.
100%
0%
You voted that this article was . Was this a mistake? If so, change your vote here.
Scroll less, learn more about construction.
Subscribe to The Blueprint, Procore’s construction newsletter, to get content from industry experts delivered straight to your inbox.
By clicking this button, you agree to our Privacy Notice and Terms of Service.
Categories:
Tags:
Written by
Jacob Kunken
24 articles
Jake Kunken currently works as Solutions Engineer for Procore's Heavy Civil division. He brings 14 years of experience working in various construction roles in New York and Colorado, including laborer, assistant carpenter, carpenter, assistant superintendent, superintendent, construction manager, safety manager, and project manager. Jake also spent time in EHS as an environmental engineer for Skanska. He’s worked on more than 40 commercial projects from ground-up, to heavy civil, hospital work, and tenant improvement. Jake studied Ecological Technology Design at the University of Maryland.
View profileTrey Strange
27 articles
Trey Strange is a Peabody and Emmy-Award winning writer and producer based in Brooklyn, NY. Throughout his career, Trey has worked for the Huffington Post, Houston Chronicle, Out Magazine, Brooklyn Eagle, CNBC, INTO, and New York Magazine's Bedford + Bowery. He received his Masters in Journalism and Middle East studies from New York University, and Bachelors in the same subjects from the University of Houston.
View profileExplore more helpful resources
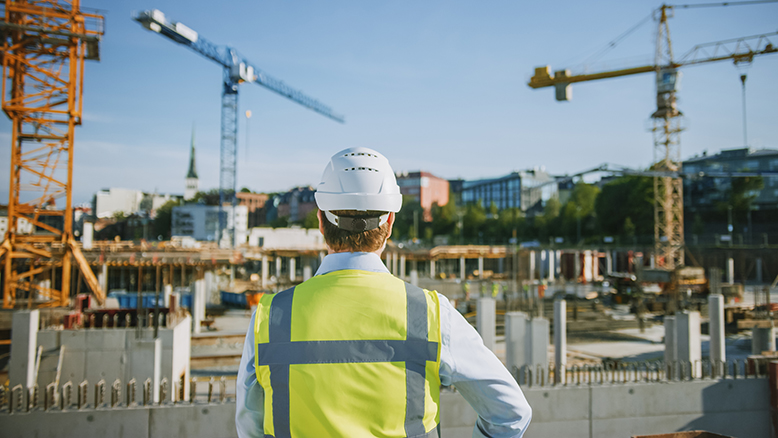
Commercial Construction Management: Mastering the Basics
Commercial construction management is no small feat: Commercial projects tend to be large and complex, and unlike residential construction, which involves repeatable tasks, can involve industry-specific and technical aspects. Commercial...
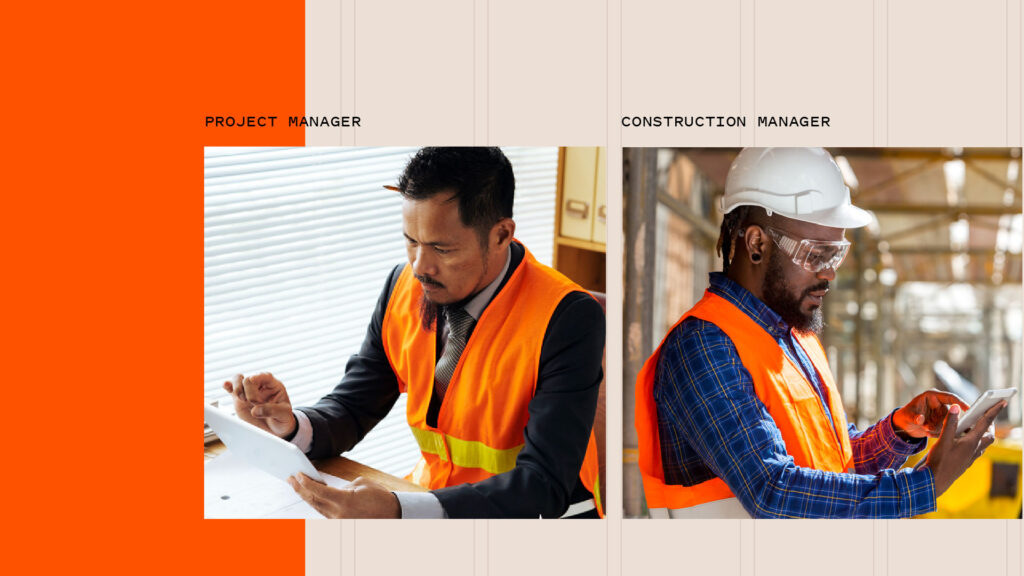
Construction Manager vs. Project Manager: Comparing Leadership Roles
Skillful oversight of construction projects allows companies to deliver to owners on time and within budget. Construction managers (CMs) and project managers (PMs) provide the necessary supervision to keep projects...
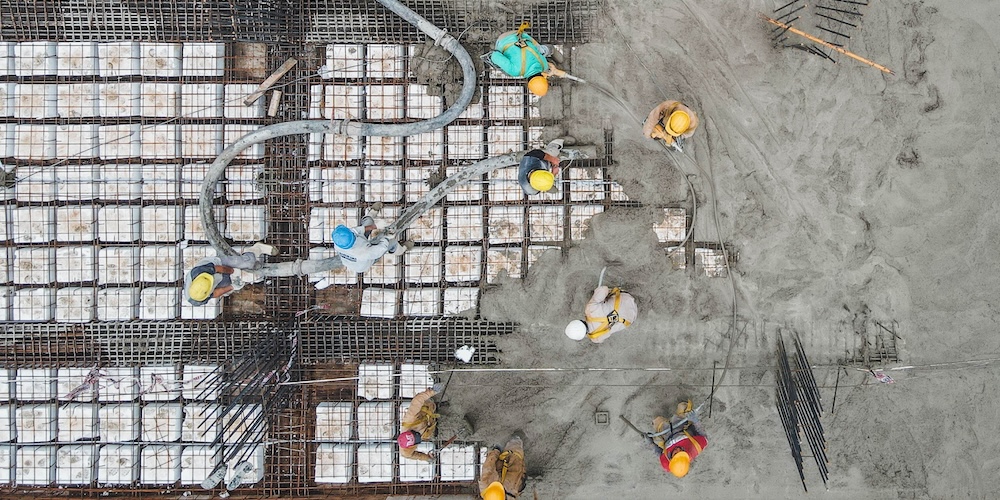
Mastering Construction Resource Management: Strategies for Success
Completing construction projects successfully requires the careful management of various resources: labor, materials, equipment, money, time and information. Since these resources are finite, allocating them wisely is crucial for minimizing...
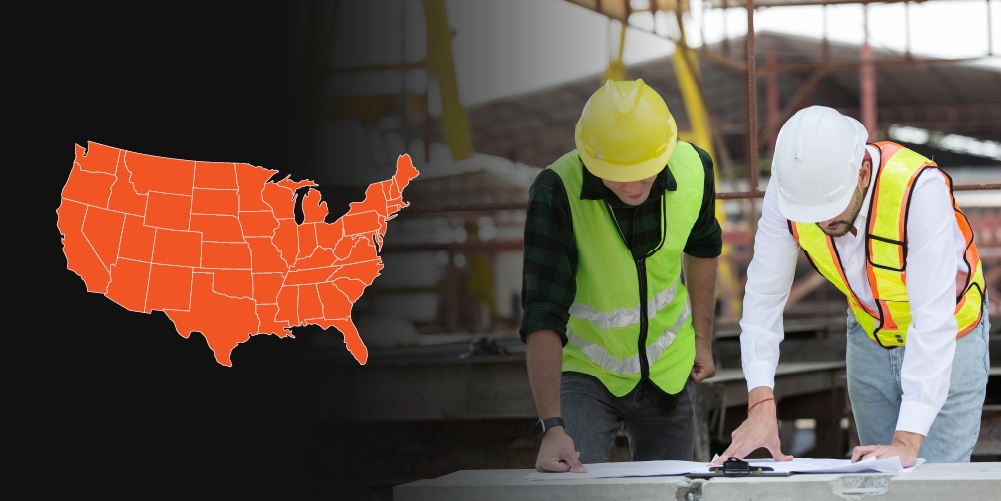
Managing Construction Projects in Different States: A Contractor’s Guide to Working Across State Lines
For many general contractors, taking on work in a new state or region can offer transformative opportunities for building a thriving business and a respected reputation. But managing projects is...
Free Tools
Calculators
Use our calculators to estimate the cost of construction materials for your next project.
Templates
Find a template to help you with your construction project tasks.
Material Price Tracker
Get the latest U.S. retail prices and view historical trends for common building materials.
Glossary
Explore key terms and phrases used in the industry.