— 38 min read
The Ultimate Guide to Construction Scheduling
Last Updated Nov 15, 2024
Last Updated Nov 15, 2024
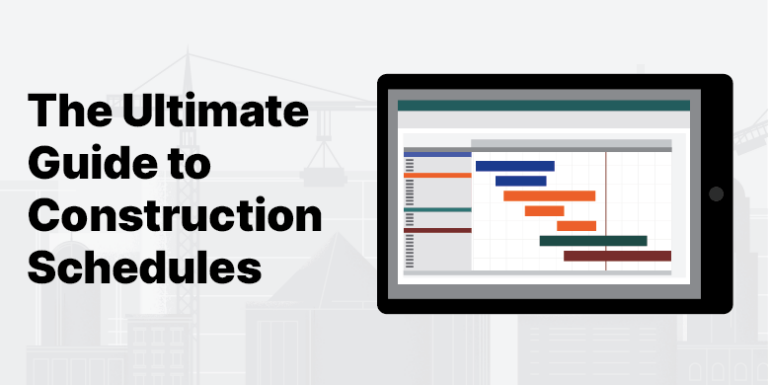
A successful construction project requires careful project management, and one tool stands out as the cornerstone: the construction schedule. Think of it as a roadmap detailing who needs to do what, where, when, and in what order. It’s all about coordination, planning, and a lot of careful decisions.
A well-structured construction schedule enables construction professionals to manage resources more efficiently, saving both time and money. It helps anticipate potential hiccups before they become major issues, ensuring that the work stays on track. Finally, a solid construction schedule makes it clear to everyone involved — from contractors and suppliers to clients — what needs to happen and when.
Below, we'll walk you through the basics of construction scheduling as well as the principles that lead to a solid schedule, different methodologies and approaches to scheduling, and common challenges that construction schedules face — as well as ways to approach those challenges and improve construction scheduling.
Table of contents
Construction Scheduling Basics
At its core, a construction schedule is a strategic tool — a meticulously crafted timeline of activities, milestones, and deliverables that make up a construction project. Once construction begins, the schedule is a living document that represents the best path to completion for a project that is up against real obstacles like weather, differing site conditions, supply chain constraints, and labor availability.
Regardless of how the schedule is represented — a Gantt chart, a network diagram, or a 3D model — it ultimately shows information about the timing and sequencing of every action that takes the project from beginning to end. In developing and managing the schedule, construction professionals have a variety of vocabulary they use to represent the project as a whole.
Term | Definition |
---|---|
Project Milestones | Specific points in time within the project schedule that indicate important stages of the project |
Duration | The time to complete a task, usually measured in work days or calendar days |
Dependencies | Relationships between different tasks, where one task relies on another to start or finish |
Lead time | The amount of time an activity starts prior to another activity starting or completing |
Lag time | A delay or waiting period following an activity required for reasons such as drying, curing, or settling |
Float | The amount of time that a task can be delayed without delaying the project completion date (also called “slack”) |
Resource Allocation | The process of assigning and managing assets (like labor, materials, and equipment) to complete specific tasks |
Baseline Schedule | The approved version of a schedule that can typically be changed only through formal procedures |
When creating a construction schedule, construction project managers typically begin by breaking down the work into discrete units (called "activities" or "tasks"), estimate durations, and arrange all project tasks — taking into account dependencies as well as lead and lag associated with various tasks to overlap and buffer as necessary.
In addition to these basic terms, developing a robust and useful construction schedule also depends on a number of key principles — like how work is divided up, how activities are sequenced, and how resources are allocated.
Stay updated on what’s happening in construction.
Subscribe to Blueprint, Procore’s free construction newsletter, to get content from industry experts delivered straight to your inbox.
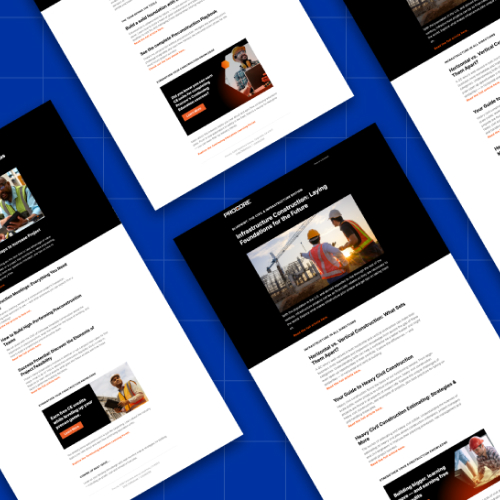
Principles of Construction Scheduling
Construction schedules depend on a series of nearly universal principles that guide their creation and management. These fundamental principles include ideas like Work Breakdown Structure (WBS), which helps take the overall project and identify small, manageable, concrete tasks to place on the schedule. Other concepts like the critical path and resource allocation are also essential to the scheduling process.
Concept | Definition | Example |
---|---|---|
Work Breakdown Structure (WBS) | A detailed breakdown of the total scope of a project into smaller, manageable tasks | In constructing a commercial office building, a WBS might include tasks like "Excavate site," "Pour concrete for foundation," "Install structural steel frame," and "Install HVAC system" |
Critical path | The longest series of sequential tasks, which determines the minimum time needed for project completion (any delay in critical path tasks will affect the project's end date) | In the same office building project, the critical path could include sequential tasks like "Excavate site," "Pour concrete for foundation," "Install structural steel frame," "Complete exterior walls," and "Install roofing" |
Resource allocation | The process of assigning and managing the necessary resources (labor, materials, equipment, etc.) for each task | The task "Install HVAC system" might involve allocating a specialty contractor's crew and ordering specific equipment |
Risk assessment | The process of identifying, evaluating, and mitigating potential risks in a project | Risks like weather delays, labor shortages, and supply constraints affect many project schedules |
Continuous monitoring | Regularly tracking the progress of the project against the schedule to identify any deviations and take corrective actions | Weekly reviews of the schedule might reveal that pouring concrete for the foundation is taking longer than expected due to unforeseen site conditions, and the schedule needs to be adjusted accordingly |
We'll take a deeper look at each of these concepts and how they contribute to the overall functioning of an excellent construction schedule.
Work Breakdown Structure (WBS)
Construction projects are extremely complex, so breaking down the overall project into smaller parts is essential. Work Breakdown Structure is used to identify the components that make up the entire project, which is helpful for estimating, bidding out portions of a job to specialty contractors, and scheduling tasks.
In essence, WBS creates a project hierarchy from big (the entire project) to very small (a single task). In practice, it looks like this:
WBS Level | Definition | Example |
---|---|---|
Project | The overall goal of the construction project | "Construct a new office building" |
Phase | Key stages in the project, typically organized chronologically | "Site Preparation," "Foundation Construction," "Superstructure Construction," "Building Envelope Construction," "Internal Works," "Finishes," "Commissioning and Testing," and "Landscaping" |
Deliverable | A tangible item that is produced as a part of a phase. Each phase has one or more deliverables | For the "Superstructure Construction" phase, a deliverable could be "Erected steel frame of the building" |
Task | Individual activities that need to be completed to produce a deliverable | Within the "Erected steel frame of the building" deliverable, tasks could include "Deliver steel beams to site," "Position and align steel beams," or "Weld/bolt beams into place" |
In order to use Work Breakdown Structure effectively, construction professionals rely on several key rules:
- 100% rule: The next level down in the WBS is a complete description of the level above. It means that the lower-level WBS elements should fully and completely define the scope of the higher-level elements. This ensures that no part of the project’s work is left out of the WBS.
- Mutually exclusive elements: Each element in the WBS is mutually exclusive, or distinct, from all other elements. There should be no overlap in scope between different elements. This prevents duplication of work.
- Measurable work packages: A group of related tasks at the lowest level of the WBS is called a work package. These packages should be defined such that their completion can be measured and monitored.
By creating measurable, mutually exclusive elements that all account for 100% of the project, construction professionals ensure that their schedules are a complete reflection of the entire project.
The Critical Path
In construction scheduling, the critical path is the sequence of project tasks that adds up to the longest overall duration, dictating the shortest time possible to complete the project. That's why project managers are often most concerned about tasks that are "on the critical path" — any delay on these tasks directly impacts the project completion date.
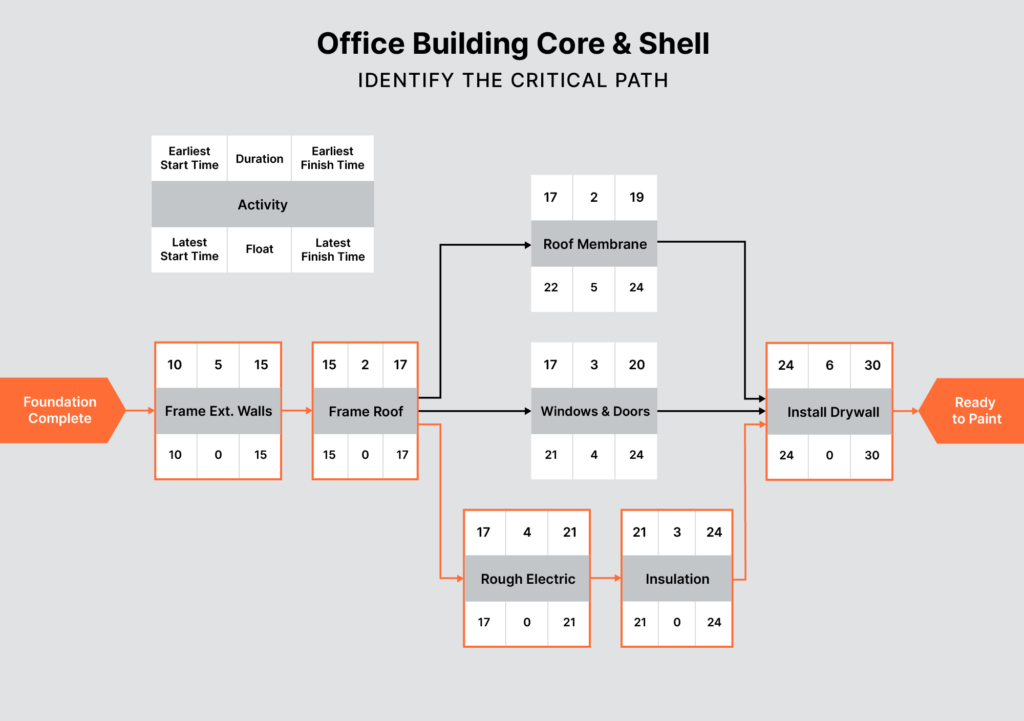
Determining the critical path requires the following steps:
List tasks.
Construction project managers start by listing all tasks needed to complete the project, usually derived from the Work Breakdown Structure (WBS)
Sequence tasks.
Next, they determine the order in which these tasks must be performed, including dependencies. Some tasks can't start until others finish, while others can happen simultaneously.
Estimate task durations.
For each task, an estimated duration is established. These estimates are typically based on past experience, industry standards, and input from specialists or subcontractors.
Draw a network diagram.
Tasks, dependencies, and durations are then plotted on a network diagram that visually represents the order of operations.
Identify the critical path.
The critical path is the sequence of tasks that has the longest total duration. If any task on this path gets delayed, it will push out the project's finish date.
The identification of the critical path affects the following:
- Scheduling: Understanding the critical path allows project managers to schedule activities for the most efficient use of time and resources. It helps them to see where there is flexibility in the schedule (tasks not on the critical path may be able to be delayed or rescheduled without affecting the overall project timeline) and where there is not (delays to critical path tasks directly impact the project end date).
- Contract: Often, construction contracts include clauses related to the project timeline, with penalties for late completion and sometimes bonuses for early completion. Identifying the critical path is crucial for making realistic commitments in the contract and for understanding the implications if delays occur.
- Finances: The critical path affects cash flow, as money is often paid out upon the completion of different stages of work. Delays in the critical path can lead to delays in payment, affecting the financial health of the project. Furthermore, delays can lead to increased costs, for example, through longer equipment rental periods, extra labor costs, and penalty clauses.
In other words, the critical path is more than just a scheduling tool — it's a major factor in the financial health of general contractors and specialty contractors.
Resource Allocation
Resource allocation involves assigning available resources in the most effective manner to complete project tasks. In construction, resources primarily include labor, equipment, and materials.
Here's the general process:
Identify necessary resources.
For each task in the Work Breakdown Structure (WBS), project managers identify the necessary resources. This could involve specific trades, specialized equipment, or certain materials.
Determine availability and constraints.
Next, the availability of these resources and any constraints (like budgetary limits or time restrictions) are determined.
Assign resources.
Based on the requirements and constraints, resources are then assigned to tasks in the project schedule. This involves deciding how many resources are needed for each task and when they will be required.
Resource allocation plays an important role in construction scheduling, since it influences many other aspects of the project:
Overall timeline
The availability of resources can directly affect the project schedule. If a resource is not available when required, a task may need to be delayed, which could impact the overall project timeline.
Budget management
Effective resource allocation is key to managing the project budget. Over-allocation of resources can lead to unnecessary costs, while under-allocation can cause delays, leading to potential cost overruns.
Efficiency
Proper resource allocation can also increase project efficiency. By ensuring that resources are used effectively and not sitting idle, project managers can save time and money, and increase overall project productivity.
Allocating resources carefully can help mitigate risks before a project even breaks ground. Of course, project managers also have to carefully reallocate resources as the project unfolds and conditions change. Staying mindful of the critical path and the budget helps project managers wisely use resources while maintaining profitability and an on-time finish.
Risk Assessment
When creating and managing a construction schedule, risk assessment is a systematic approach to identify, evaluate, and address potential hazards that could impact the project's timeline, cost, or quality. It allows for proactive planning and better decision-making, helping projects stay on track and within budget.
The process of risk assessment generally involves the following steps:
- Risk Identification: The first step involves identifying potential risks. These could be anything from supplier issues, inclement weather, labor shortages, or regulatory changes that could potentially delay the project.
- Risk Analysis: Once risks are identified, their potential impact on the project is analyzed. This could involve determining how the risk could affect the project schedule, the costs involved, and what would be required to mitigate the risk.
- Risk Response Planning: After analyzing the risks, appropriate response strategies are developed. This could involve contingency plans, allocating extra resources, or adjusting the project schedule to accommodate potential delays.
- Risk Monitoring: The last step involves continuous monitoring of identified risks and the effectiveness of the response strategies. This ensures that the project can adapt to changing circumstances and new risks that may arise.
With a proper risk assessment strategy built into the scheduling process, the project manager can provide a more realistic schedule, insights into resource allocation, and a more quality deliverable.
Learn more:5 Steps to Reduce & Mitigate Risk
Continuous Monitoring
Continuous monitoring in construction enables managers to track progress, identify deviations, and make necessary adjustments in a timely manner. Crucially, it involves regular communication with all project stakeholders to ensure everyone stays aligned with the evolving project plan.
Here's a look at the typical continuous monitoring process:
- Tracking Project Progress: This involves regularly assessing the completion of tasks against the project schedule, then understanding what's been accomplished and what remains to be done.
- Comparing Actual vs. Planned Performance: The project's actual progress is compared against the planned schedule. Any discrepancies can signal potential issues that need attention.
- Regular Meetings: Regular meetings with all key construction personnel are a crucial part of the monitoring process. These meetings serve to discuss progress, create and share look-ahead schedules, address issues, and update the project plan as necessary.
- Making Necessary Adjustments: If discrepancies or issues are identified, necessary changes are made to the project schedule. This could involve rescheduling tasks, reallocating resources, or activating contingency plans.
- Updating Stakeholders: Whenever there are changes to the project plan, it's essential to communicate these updates to all relevant stakeholders, including the project owner. This ensures everyone is aware of the current project status and any changes in expectations.
Continually monitoring the project schedule helps keep a project on track — both in terms of timeline and budget. The on-the-ground reality of a construction project is always different than the ideal plan that was laid out beforehand, but savvy construction project managers are able to respond to changing circumstances to keep projects on track.
Courses about construction.
For construction.
Unlock your career potential with our free educational courses on Health & Safety, Data in Construction, and more.
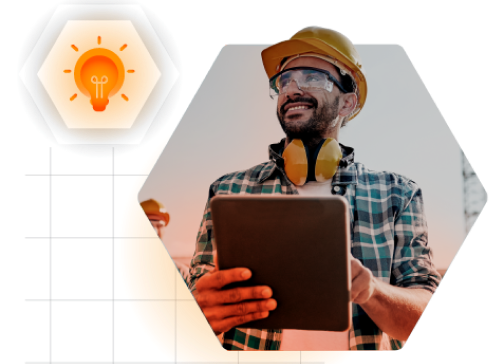
Visualizing Construction Schedules
Representing the construction schedule visually enables all stakeholders to understand the plan clearly, facilitates coordination, and aids in tracking project progress. While the construction process is complex, representing it visually can make it more comprehensible and manageable. Three popular visualization tools are commonly used in the construction industry today: Gantt charts, network diagrams, and 3D BIM models with scheduling data (also called BIM 4D). Each offers a unique perspective on the project timeline, tasks, and dependencies, empowering project teams to manage the construction process more effectively.
Visualization Method | Description |
---|---|
Gantt Charts | Gantt charts present the project schedule as a bar chart, with each task depicted as a horizontal bar. The length of the bar corresponds to the task duration. Task dependencies can also be displayed as connecting arrows between bars. |
Network Diagrams | Network diagrams (also known as PERT charts or CPM diagrams) illustrate task dependencies. They consist of nodes (tasks) and arrows (dependencies), forming a network that demonstrates the sequential relationship of tasks. |
3D Models (BIM 4D) | 4D Building Information Modeling (BIM) links a 3D digital model of a building with time or schedule-related information. It provides a dynamic representation of the construction process over time. |
In the following sections, we'll delve into each of these tools and their unique benefits to the construction scheduling process.
Gantt Charts
Gantt charts are likely the most common representation of a construction schedule used in the industry today. They provide a graphical representation of the construction schedule, displaying all tasks and activities against a timeline. Each task is represented as a horizontal bar, the length of which represents the planned task duration. The positioning of the bar on the timeline indicates the task's start and end dates. Arrows between bars represent dependencies among tasks.
Gantt charts are dynamic planning tools that are updated and revised as construction progresses. As work is completed, or if delays occur, the Gantt chart can be updated to reflect these changes, allowing project stakeholders to see the current project status at a glance.
Because Gantt charts show dependencies between tasks, they can improve the coordination of the various tasks and resources required for a complex construction project. This visualization can assist in sequencing activities, ensuring that necessary prerequisite tasks are completed before subsequent work begins.
Here are some advantages of Gantt charts in construction scheduling:
- Visual clarity: Gantt charts offer a clear, visual representation of the schedule that is easily understood by all stakeholders.
- Task dependencies: Arrows show the interdependencies between various tasks, which can help in preventing scheduling conflicts.
- Progress tracking: Gantt charts can be updated to reflect the actual progress of tasks, making it easier to compare planned progress with actual progress.
- Resource planning: They can provide a snapshot of when certain resources will be needed for specific tasks, helping in resource allocation and planning.
Using Gantt charts, construction project managers can visually manage, track, and update their project schedules, leading to improved project execution and coordination.
Network Diagrams
Network diagrams, another key tool in construction scheduling, are graphic representations of the project tasks and their sequential relationships.
Unlike Gantt charts which primarily emphasize the timeline, network diagrams emphasize the logical sequence of the tasks and the dependencies between them. They can present a clear sequence of events and how each task links to others, effectively showing the flow of the project. Nodes in the network diagram represent tasks, and arrows represent dependencies, showing the sequence in which tasks must occur.
As with Gantt charts, network diagrams are also dynamic. As the project progresses and circumstances change, the diagram can be updated to reflect these changes, giving a real-time representation of the project's progress and any alterations to the sequence of work.
Network diagrams can play a crucial role in coordinating tasks. By showing dependencies, they indicate which tasks need to be completed before others can begin, thereby aiding in effective workflow planning.
Here are some advantages of network diagrams in construction scheduling:
- Task sequencing: Network diagrams highlight the dependencies and sequence of tasks, providing a clear picture of the task flow.
- Critical Path identification: They can help in identifying the critical path – the sequence of tasks that must be completed on time for the project to finish on schedule.
- Sensitivity analysis: Network diagrams can indicate which sequences of tasks have some scheduling flexibility (float) and which don't, providing an understanding of how sensitive the schedule is to delays in specific tasks.
- Effective coordination: By providing a visual flow of tasks, network diagrams can assist in coordinating the sequence of work, helping to prevent scheduling conflicts and bottlenecks.
Network diagrams can be used in coordination with Gantt charts. Some project managers use a network diagram to lay out the logical sequence of dependencies for a project, then lay them out a timeline with durations using a Gantt chart.
3D Models With Scheduling Data (BIM 4D)
In Building Information Modeling 4D (BIM 4D), construction sequences and activities are linked to the 3D model of the project, providing a visual representation of the construction process over time. This allows project stakeholders to visualize the project as it will be built, helping them understand how the project will progress and how the construction site will look at different stages.
Like Gantt charts and network diagrams, 4D BIM models are updated as construction progresses. As actual construction takes place, the 4D model can be updated to reflect the current project status. This allows stakeholders to see the progress in a highly visual and intuitive format, enhancing understanding and communication.
Using 4D BIM can significantly improve coordination among project stakeholders. By visualizing the construction process, it becomes easier to identify potential issues, such as clashes between different components or sequencing issues, before they occur on site.
Here are some advantages of 4D BIM in construction scheduling:
- Visualizing construction progress: BIM 4D provides a dynamic view of the project's progress over time, allowing stakeholders to better visualize and understand the construction process.
- Improved coordination: Using a model paired with scheduling data can enhance coordination among stakeholders by highlighting potential conflicts or issues, aiding in their early resolution.
- Efficient resource management: Modeling can assist in planning the use of resources, ensuring that they are available when needed and minimizing idle time.
BIM 4D is a powerful tool for visualizing the construction schedule, promoting effective coordination, and enhancing communication among project stakeholders. It represents the future of construction scheduling, combining the power of 3D modeling with the time-related data of the construction schedule.
Types of Construction Schedules: Common Methodologies
The approach to scheduling can significantly vary depending on the type of scheduling method a project manager employs. Different methodologies offer unique perspectives, tools, and strategies for planning, managing, and controlling the project schedule. Some may prioritize collaboration and flexibility, while others might emphasize strict task sequencing or the management of repetitive work.
To understand the range of approaches, let's explore several established construction scheduling methodologies and their distinguishing features:
Methodology | Definition |
---|---|
Critical Path Method (CPM) | A construction scheduling technique that identifies the sequence of tasks that has the longest duration, thereby determining the shortest possible project duration |
Last Planner System (LPS) | A collaborative, commitment-based planning system that involves the project's frontline workers (the "Last Planners") in the scheduling process. In LPS, these workers make commitments to each other about what work will be completed in the next week, improving predictability and efficiency. It promotes a bottom-up approach, where the ones executing the work have a major say in the planning |
Program Evaluation and Review Technique (PERT) | A statistical tool that uses a weighted average of three times (optimistic, most likely, and pessimistic) to estimate each task duration, thereby handling uncertainty in the project schedule |
Line of Balance (LOB) | A method for products that require repetitive work, such as high-rise buildings. It illustrates the rate at which units must be completed per time period to avoid disruption and shows where multiple crews are needed |
It's worth noting that these methodologies are not mutually exclusive, and a construction project may utilize more than one method concurrently. For instance, a project might apply the Critical Path Method for overall schedule development and the Last Planner System to enhance frontline worker engagement. Each methodology offers its unique advantages and can contribute to the robustness and resilience of the construction schedule. The choice depends on various factors, including the project's complexity, the team's expertise, and the project owner's preferences and requirements.
Critical Path Method (CPM)
The Critical Path Method (CPM) is a staple in the world of construction scheduling, often adopted for its ability to effectively visualize and manage project timelines. CPM is a type of "push planning," where project managers establish the work schedule and "push" tasks forward based on the project's needs and deadlines.
In practice, CPM begins with the identification of all the individual tasks or activities required to complete the project. These tasks are then sequenced according to their dependencies, and the duration of each task is estimated. The result is a network diagram that clearly shows the "critical path" – the sequence of tasks that determines the minimum duration of the project. Tasks on the critical path have zero "float", meaning any delay in these tasks will directly impact the project completion date. By identifying the critical path, CPM allows project managers to prioritize tasks and focus resources where they are most needed.
However, like any other methodology, CPM comes with its own set of strengths and weaknesses. Here's some examples:
Advantages | Drawbacks | Strategies to Address Drawbacks |
---|---|---|
Offers a clear visualization of the project timeline, enabling easy tracking and management | Assumes fixed and certain task durations, which often doesn't reflect real-world conditions | Use historical data and expert judgment to provide more accurate task duration estimates |
Identifies critical tasks, allowing for prioritization and efficient resource allocation | Overemphasizes task sequences and may overlook resource constraints | Combine CPM with other methodologies that focus on resource allocation, such as the Last Planner System |
Simplicity and straightforwardness make it user-friendly and easy to understand | Doesn't fully account for uncertainties and unexpected changes in the project | Implement risk management practices and continuously update the schedule to reflect real-time changes |
Although CPM is widely used, it's rarely the only planning tool in a construction project's toolbox. It's commonly integrated with other methodologies, each selected to complement the others and to address the unique complexities and requirements of the project. This balanced, multi-method approach can mitigate the drawbacks of each individual method and leverage their advantages, leading to more resilient and effective project scheduling.
Last Planner System (LPS)
The Last Planner System (LPS) is a collaborative, commitment-based planning system that integrates pull planning with constraint analysis, lookahead scheduling, and weekly work planning. Originating from the principles of Lean Construction, it puts the decision-making process into the hands of the people carrying out the tasks — the last planners.
In practice, LPS employs a series of collaborative meetings involving key project stakeholders, where tasks are backward scheduled from a milestone or project completion date. This "pull" approach ensures that work is planned based on the readiness and the capacity of the workforce — not pushed onto them without consideration of existing conditions.
Here are the advantages and drawbacks of the Last Planner System, as well as possible ways to handle these drawbacks:
Advantages | Drawbacks | Handling Drawbacks |
---|---|---|
Greater control and commitment from the people executing the tasks | Requires a high level of collaboration and trust among team members | Foster a collaborative environment and build trust among team members |
Improved team communication and coordination | Can be time-consuming to implement and manage | Invest time in training and implementing the system |
Better risk management and reduced uncertainty | Success highly depends on the active participation of all team members | Encourage and incentivize active participation |
The Last Planner System works best when team members are willing to commit to their responsibilities and are proactive in discussing constraints and changes. This is particularly true in complex projects with multiple interdependent tasks and overlapping trades, such as commercial construction projects or large infrastructure projects, where coordinating schedules between multiple stakeholders is necessary.
Program Evaluation and Review Technique (PERT)
The Program Evaluation and Review Technique (PERT) is a statistical tool that was designed to analyze the duration of tasks involved in completing a project. It's particularly useful in projects where the duration of tasks is uncertain. In construction, PERT can be a valuable tool to manage the inherent uncertainty of construction processes.
PERT begins with three estimates for each construction task:
- Optimistic Time (O): The minimum possible time required to accomplish a task, assuming everything proceeds better than is normally expected.
- Pessimistic Time (P): The maximum possible time required to accomplish a task, assuming everything goes wrong (but excluding major catastrophes).
- Most Likely Time (M): The best estimate of the time required to accomplish a task, assuming everything proceeds as normal.
Using those estimates, a project manager can use a formula — (O + 4M +P) / 6 — to determine the expected time and variance for each task, helping them create a more realistic schedule and account for potential shifts in task durations.
PERT helps with risk mitigation in construction scheduling by assigning a time range to each activity rather than a fixed duration, allowing for more realistic scheduling. Furthermore, the variance calculation gives project managers insight into which activities have the most risk associated with their completion times, enabling targeted risk management efforts.
This approach has both advantages and drawbacks, detailed below:
Advantages of PERT | Drawbacks of PERT | Strategies to Handle Drawbacks |
---|---|---|
Provides a structured framework for estimating task durations and identifying critical activities | Assumes a probability distribution for task durations that may not be accurate for all tasks | Complement PERT with other scheduling methods to validate estimates and address uncertainties |
Helps to mitigate risk by identifying the activities that carry the highest risk associated with their completion times | Requires three estimates for each activity, which can be time-consuming to gather | Ensure a clear communication channel with all involved parties to make the estimation process efficient |
Offers a statistical approach to schedule estimation, which can be more accurate and realistic than deterministic methods | Relies heavily on the accuracy of estimates, as inaccurate estimates can lead to unrealistic schedules | Invest in regular training for project estimators and use past project data to improve the accuracy of estimates |
Like other scheduling methodologies, PERT can be used in tandem with other techniques to take advantage of its strengths while compensating for its weaknesses. For instance, combining PERT with the Critical Path Method (CPM) allows for a more rigorous analysis of the project schedule, blending PERT's probabilistic approach with CPM's deterministic model.
Moreover, PERT's focus on risk assessment aligns well with the proactive approach of methodologies like Lean Construction or the Last Planner System. These methodologies promote a collaborative planning process and emphasize continuous learning.
Line of Balance (LOB)
For projects involving repetitive tasks that span multiple units or locations, such as the construction of identical units in a high-rise building or a housing development, a unique methodology called the Line of Balance (LOB) can be effective.
Line of Balance, also known as flowline or repetitive scheduling method, is a graphical tool used to optimize the scheduling and management of these repetitive tasks. It displays the rate at which these tasks need to be performed to maintain a continuous flow of work, thereby balancing resources and ensuring steady progress.
LOB scheduling presents a visual depiction of scheduled work and actual work done. The schedule is represented on a chart with two axes:
- The vertical axis typically represents the sequence of tasks or activities. These tasks are listed in the order they should be completed.
- The horizontal axis represents the time, often with a specific scale like days, weeks, or months.
The basic LOB chart contains diagonal lines for each task. Each line starts at the point that represents when a task should start for the first unit (or location), and ends at the point representing when the task should finish for the last unit. The slope of the line signifies the speed of the work. A steeper line indicates a faster pace of work, while a less steep line indicates slower work.
The goal of LOB is to create a steady and continuous flow of work, with no idle time between tasks. This is represented on the chart as a series of parallel lines, with no gaps between the end of one task and the start of the next.
When actual work progress is plotted on the chart, deviations from the planned schedule can be easily spotted. If actual work is lagging behind the planned schedule, the line representing the actual work would fall below the planned line. Conversely, if work is ahead of schedule, the actual work line would be above the planned line.
This method has a number of advantages as well as some key drawbacks, including:
Advantages | Drawbacks | Strategies to Address Drawbacks |
---|---|---|
Optimizes resource use and reduces idle time by ensuring a steady flow of work | Not suitable for projects with non-repetitive tasks, or tasks that have varying durations across different units | Combine LOB with other scheduling methodologies for projects with a mix of repetitive and non-repetitive tasks. |
Use historical data, expert judgment, and PERT or other estimation techniques to improve the accuracy of task duration estimates. | Requires accurate estimates of task durations and clear definitions of task sequences | Use historical data, expert judgment, and PERT or other estimation techniques to improve the accuracy of task duration estimates |
Can be easily adjusted to accommodate changes in project scope or schedule | May require frequent updates and adjustments to maintain accuracy | Incorporate regular schedule review and update processes, especially by using software tools |
Line of Balance can be particularly beneficial when used in conjunction with other scheduling methods. For instance, Critical Path Method can be used to schedule non-repetitive tasks in the project, while LOB can be used for repetitive tasks. This combination ensures the overall efficiency and effectiveness of the project schedule. As with any methodology, it's important to understand when and where LOB is most applicable, and to adjust your approach based on the specific needs of your project.
Scheduling Challenges
Every construction project, no matter how well-planned, can encounter scheduling challenges. These may arise due to various factors such as unforeseen site conditions, changes in project scope, adverse weather, resource availability issues, and more. Understanding these challenges and being aware of them can help project managers better prepare for and mitigate potential project delays and overruns.
Challenges | Examples |
---|---|
Resource availability | Limited availability of skilled labor, machinery, or materials |
Weather conditions | Adverse weather causing delays in outdoor construction activities. |
Change orders | Design changes or unforeseen issues requiring adjustments to the original plan |
Project Complexity | Complex projects with numerous interdependencies can make scheduling more difficult |
Regulatory approvals | Delays in obtaining necessary permits or inspections can halt work |
Unforeseen site conditions | Discovery of hazardous materials or unstable ground conditions requiring remediation |
Equipment failures | Breakdown of essential construction machinery causing work stoppage |
Supplier delays | Delays in material delivery due to supplier issues |
Labor Disputes | Strikes or other labor issues can halt work |
Communication Breakdown | Miscommunication or lack of communication can lead to scheduling misunderstandings or conflicts |
Decision paralysis | Stakeholders fail to provide key decisions in timely manner or request additional time to review |
Many of these challenges can be proactively managed during the creation of the schedule by incorporating contingencies and flexibilities that account for potential issues. Of course, even with the most thorough planning, some problems will inevitably arise once construction has begun. Fortunately, there are strategies to respond effectively, which we'll cover in the next section.
Strategies to mitigate scheduling problems
Construction project managers are equipped with an arsenal of strategies to overcome potential scheduling obstacles. These strategies range from proactive measures to reactive approaches applied once a problem has already arisen. The choice of strategy depends on the specific situation, the resources at hand, and the potential impacts on the project’s timeline and budget.
Here are a few common strategies used in the industry:
Strategy | Definition | Type |
---|---|---|
Look-ahead schedules | Detailed schedules created for a specified period ahead (like 2–6 weeks) can foresee upcoming work and manage resources effectively. | Proactive |
Resource leveling | Adjusting the project schedule to minimize resource usage fluctuations helps in the optimal utilization of resources. | Proactive |
Schedule compression | Reducing the project schedule without reducing the project scope. It involves techniques like fast-tracking and crashing. | Reactive |
Fast-tracking | Overlapping activities that were originally scheduled to occur sequentially. This increases risk and may result in rework. | Reactive |
Crashing | Adding additional resources to activities on the critical path to complete them sooner. This usually increases cost. | Reactive |
Forensic schedule analysis | Detailed investigation of the project schedule to identify issues that have caused delays and to suggest mitigations for future projects | Both |
Look-ahead schedules
Look-ahead schedules are a proactive planning tool that offers a detailed view of what’s expected to happen in the immediate future of a construction project. They are typically short-term, covering two to six weeks, and are updated on a regular basis — usually weekly. The focus of a look-ahead schedule is managing upcoming tasks that are prepared, fully resourced, and ready to go.
The process of creating and maintaining look-ahead schedules involves the following steps:
- Identify upcoming tasks: These are the tasks that are scheduled to occur within the next few weeks. The time frame can vary, but it's generally short-term.
- Break down the tasks: For each identified task, break it down into sub-tasks or activities that need to be completed. This provides a more granular view of what needs to be done.
- Assign resources: Determine which resources (materials, labor, equipment) are needed for each task and ensure that they will be available when needed. This step also involves assigning responsibility for each task to a specific team or individual.
- Update regularly: Update the look-ahead schedule at regular intervals, such as every week. This allows for any necessary adjustments to be made based on the actual progress of the project.
Collaboration is a key factor in the success of look-ahead schedules. Project team members need to coordinate and communicate regularly to ensure that everyone is on the same page about what tasks are coming up and what needs to be done to prepare for them. This can involve regular meetings or check-ins to discuss the look-ahead schedule and any potential issues.
Look-ahead schedules can play a pivotal role in mitigating potential delays. By providing a short-term view of the project, they allow the project team to anticipate potential issues before they become problems.
In essence, look-ahead schedules are a proactive tool for project management that focuses on preparation and forward planning. They help to ensure that tasks are not just planned, but also ready to be executed, with all the necessary resources in place.
Resource leveling
Resource leveling is a proactive technique used in construction project management to resolve resource allocation problems and manage resource usage efficiently. Using this strategy, the project schedule is adjusted based on resource constraints with the goal of balancing the demand for resources with the available supply.
Here's how it typically works:
- Identify resource constraints: The first step in resource leveling is identifying resource constraints. Resources are most often people, equipment, or materials.
- Review the project schedule: With constraints in mind, project managers review the project schedule. Examine the sequence of tasks and the resources allocated to each of these tasks. Note any instances where a resource is overallocated — for example, a tradesperson scheduled to work more hours in a time period than is feasible.
- Adjust the schedule: Next, adjust the schedule to address the overallocation. This can be done by delaying tasks or splitting them over longer durations. The objective is to ensure that no resource is overused at any point in the schedule.
- Review and repeat: Finally, review the modified schedule, and repeat the process as necessary until you achieve a balanced distribution of resources throughout the project timeline. This might also involve reassessing task dependencies and constraints to find more efficient scheduling options.
For example, on a project, you might find that your team of electricians is scheduled to work on wiring in multiple parts of a building simultaneously. In this case, you would reschedule these tasks so that they occur consecutively rather than concurrently, thereby preventing the overallocation of your electricians.
Resource leveling offers several significant benefits. By avoiding overallocation, it helps prevent burnout in your team, ensuring that productivity and morale remain high. It can also result in cost savings by avoiding the need for overtime or the hiring of additional staff.
However, resource leveling is not without its drawbacks. While ensuring that resources are efficiently used, there may be a trade-off in terms of project duration. Resource leveling can extend the project timeline as tasks are rescheduled to avoid the overallocation of resources. This means that projects might take longer to complete than initially planned.
Furthermore, while resource leveling might prevent over-exertion of resources, it could also inadvertently create periods of inactivity for resources. There might be waiting times or idle times when resources are not fully utilized, which can lead to inefficiencies.
Despite these challenges, resource leveling offers a proactive approach to ensuring that resources are used efficiently and effectively throughout the project's lifespan. This prevents burnout among team members and can lead to significant cost savings.
Schedule compression
Schedule compression is a strategy used in construction project management to shorten the project schedule without changing the project scope. This is typically done in response to project delays — or when the project needs to be completed earlier than initially planned. In the world of construction, this technique is paramount especially in large-scale projects where meeting deadlines is often tied to significant financial implications like liquidated damages.
Two primary techniques are generally used for schedule compression: crashing and fast-tracking.
- Crashing involves adding more resources to critical path tasks to complete them faster. For example, if a construction project is falling behind, crashing could involve hiring additional labor or working overtime to speed up the process and complete tasks in a shorter period.
- Fast-tracking is a technique where activities that were initially planned to be performed sequentially are executed in parallel or overlap. In order to actually shorten the schedule, this means that the tasks performed in parallel must be on the critical path.
Here is how schedule compression is generally applied:
- Identify the critical path: First, you need to understand which tasks directly impact the project’s finish date. These are the tasks on the critical path. Delays in these tasks will cause your entire project to be delayed.
- Explore alternatives: Look for tasks within the critical path that can be sped up without affecting the project's scope. This could be done by adding extra shifts, increasing manpower, or employing more efficient equipment.
- Decide on a strategy: Based on your analysis, decide whether crashing, fast tracking, or a combination of both is suitable for your situation.
- Implement the changes: Implement the decided schedule compression techniques. This could involve hiring additional workers, working overtime, or executing tasks in parallel that were originally planned sequentially.
- Monitor the results: After implementing schedule compression techniques, closely monitor the results to ensure they are effective. This includes managing any potential risks or drawbacks that may arise, such as increased costs (from crashing) or increased risk and rework (from fast-tracking).
Remember, schedule compression is a reactive strategy that can help bring a delayed construction project back on track. However, it's not without risks, so it's crucial to carefully consider the potential implications before making changes to your project schedule.
Crashing, for instance, can increase the overall project cost. The additional resources, be it more labor or equipment, will inflate the budget. This strategy may also cause resource fatigue or over-allocation of resources, leading to decreased productivity. Not to mention, the quality of work may be compromised due to the rush to complete tasks, which can lead to costly and time-consuming rework.
On the other hand, fast-tracking can increase project risks as activities are performed concurrently that should have been done sequentially. This could potentially result in rework if the tasks that were done simultaneously did not consider the output of preceding tasks as expected. For instance, if interior design work begins before the building structure is fully approved, any changes in the structure's design could mean that the already-started interior work needs to be redone. This can also lead to increased miscommunication and lack of coordination among different teams.
However, it's important to keep in mind that while these risks exist, they can be effectively managed. Proper planning, clear communication, and meticulous management can go a long way in mitigating these risks. Moreover, the benefits of schedule compression often outweigh these risks, especially when it's crucial to meet project deadlines. This strategy allows construction projects to adapt to changes and unforeseen delays, making it a valuable tool in the project manager's arsenal.
Forensic schedule analysis
A forensic review of a construction schedule, also known as forensic schedule analysis, is a process that involves examining and analyzing the construction schedule after a project has concluded to identify what actually happened during the project, particularly when and why deviations from the planned schedule occurred.
The goal of forensic review is to determine the causes of the delays, their impacts on the project, and who is responsible for them. Ultimately, contractors and owners can use the findings to inform future projects and avoid similar delays in the future.
This can involve:
- Reviewing the original schedule: The analyst begins by reviewing the original planned schedule, including the planned start and end dates for each activity, the sequencing of activities, and the identified dependencies between them.
- Reviewing the actual progress: The analyst then compares the planned schedule to what actually happened. This involves reviewing progress reports, meeting minutes, daily logs, change orders, and any other documentation that provides information about when activities started and finished and when resources were allocated.
- Identifying delays: The analyst identifies any activities that were delayed or disrupted, noting when these delays occurred and how long they lasted.
- Analyzing causes of delays: The analyst tries to determine the causes of the identified delays. This could include factors like changes in scope, adverse weather, errors in the original schedule, resource shortages, or other unforeseen issues.
- Determining impact analysis: Finally, the analyst determines the impact of the identified delays on the overall project. This involves calculating how much the project was delayed overall and identifying any knock-on effects on subsequent activities.
The results of a forensic schedule analysis can be used to resolve disputes about delays, determine liability for increased costs, or provide lessons for future projects.
The future of construction scheduling
Emerging technological advancements such as advanced analytics, machine learning, and artificial intelligence offer the potential to revolutionize construction scheduling. These innovations can enhance accuracy in predictions, enable timely adjustments, and increase the overall efficiency of the process.
Artificial intelligence, for instance, holds the promise of analyzing past projects to forecast realistic timelines and resource requirements for new ones, offering real-time schedule adjustments based on changes on the ground. This proactive potential will not only provide a reactive capability but also further augment the ability to mitigate risk in construction projects.
The integration of Building Information Modeling (BIM) and other 3D visualization tools with scheduling software is expected to further gain momentum. The creation of more detailed and accurate 4D schedules through this integration will enhance planning, communication, and risk mitigation in construction projects.
Regardless of what future technologies promise, the essence of construction scheduling lies in its ability to significantly mitigate the risk of complex construction projects, ensuring they are delivered on time and on budget while maintaining the highest standards of quality and safety. As methodologies and tools evolve, the goal of making the construction process more predictable and manageable is becoming increasingly attainable. The ideal for construction scheduling is a landscape where projects run smoother, unexpected events become anticipated, and the process becomes more streamlined and efficient.
Was this article helpful?
Thank you for your submission.
100%
0%
You voted that this article was . Was this a mistake? If so, change your vote here.
Scroll less, learn more about construction.
Subscribe to The Blueprint, Procore’s construction newsletter, to get content from industry experts delivered straight to your inbox.
By clicking this button, you agree to our Privacy Notice and Terms of Service.
Categories:
Tags:
Written by
Daniel Gray
28 articles
Daniel is an educator and writer with a speciality in construction. He has been writing construction content for Procore since 2022, and previously served as a Procore Content Manager before continuing to pursue an education career as an Assistant Headmaster for Valor Education in Austin. Daniel's experience writing for construction — as well as several clients under an agency — has broadened his knowledge and expertise across multiple subjects.
View profileReviewed by
Justin Vogel
Justin is a Senior Strategic Product Consultant for Procore. Justin has an extensive background in real estate development, construction engineering, and project management professional entrusted with high profile structures, and is involved in over $3.5 billion worth of construction representing developers, CEO's, GC's, equity partners, consultants, and attorneys in unique and complex pursuits.
View profileAlex Six
10 articles
Alex Six is an Enterprise & Strategic Civil & Infrastructure Overlay Account Executive for Procore. Alex has a long background in the construction industry beginning with an internship with one of the biggest contractors in the world, and expanding across projects with teams as small as 4 people and as large as multi-billion dollar budgets with large teams and disciplines. His resume includes Caltrans highways & bridges, Metro light rail & underground, as well as airport runways and utilities.
View profileExplore more helpful resources
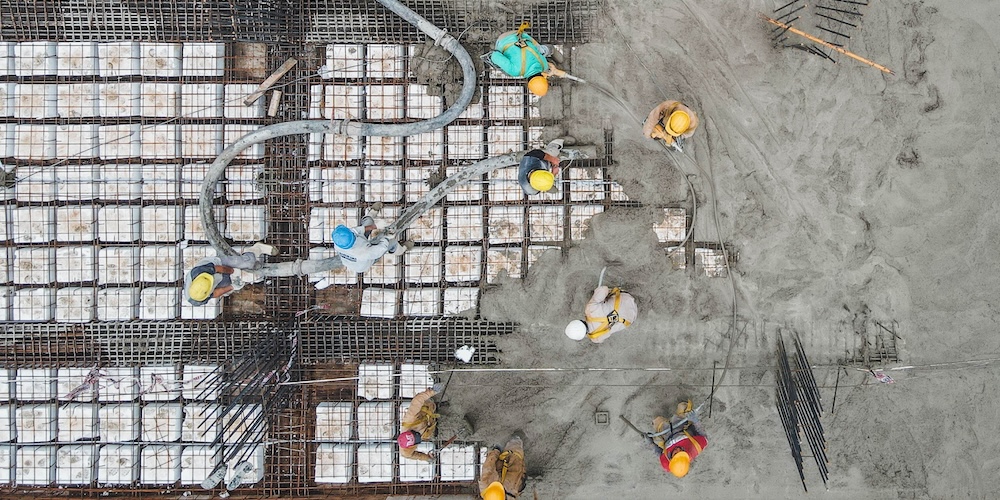
Mastering Construction Resource Management: Strategies for Success
Completing construction projects successfully requires the careful management of various resources: labor, materials, equipment, money, time and information. Since these resources are finite, allocating them wisely is crucial for minimizing...
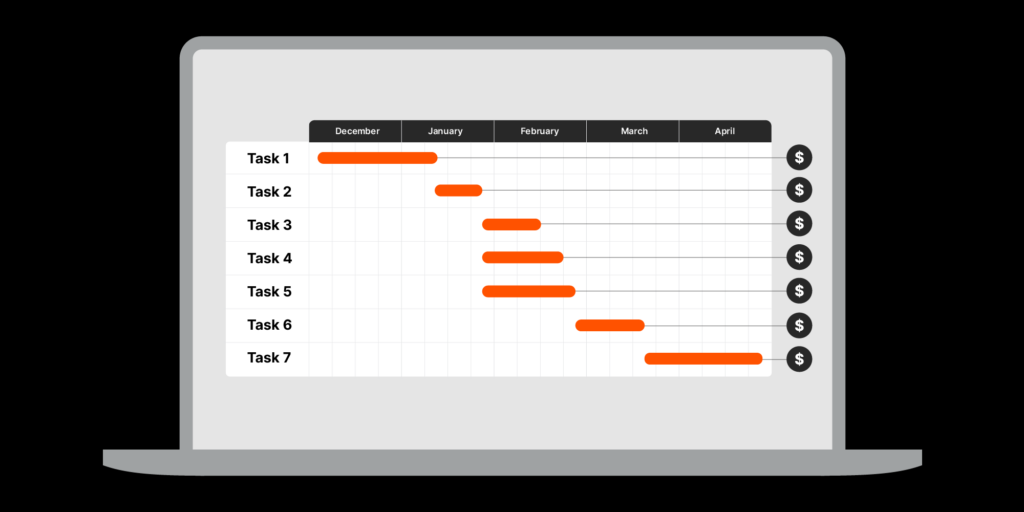
Cost-Loaded Construction Schedule: Analysis, Risks & Benefits
Both scheduling and cost control are make-or-break aspects of construction projects, but in many cases the two areas are kept very separate from one another — the project scheduler and...
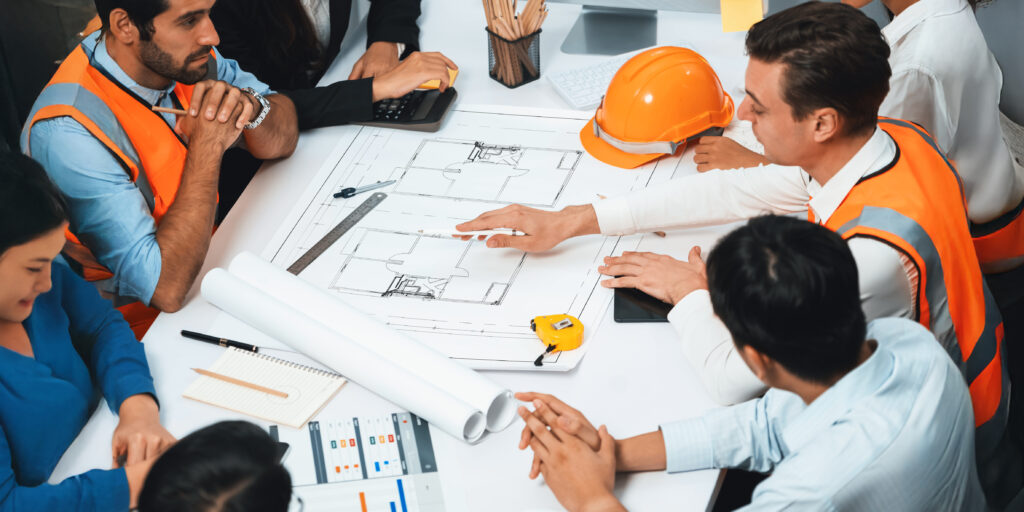
Understanding the Last Planner System in Construction
Construction scheduling is a complex process affecting multiple stakeholders. Increasing accuracy and collaboration with trade partners when scheduling construction work can positively impact on-site workflow and efficiency. The last planner...
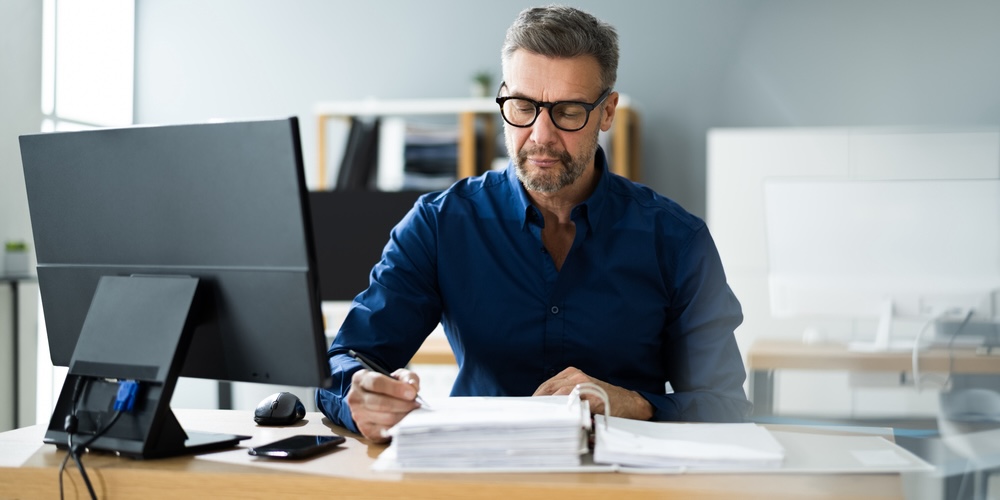
Forensic Schedule Analysis: Unlocking Insight Into Project Delays
Though construction sites may sometimes look like a large collection of machines, ultimately, it’s people who get things built. However, people aren’t perfect, and delays happen all the time —...