— 7 min read
Understanding the Last Planner System in Construction
Last Updated Nov 6, 2024
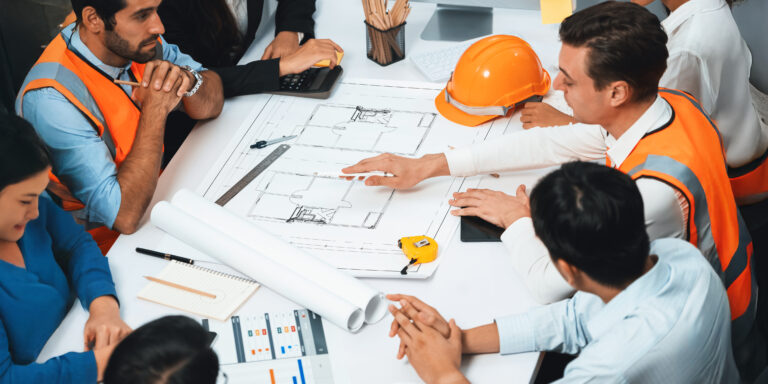
Construction scheduling is a complex process affecting multiple stakeholders. Increasing accuracy and collaboration with trade partners when scheduling construction work can positively impact on-site workflow and efficiency.
The last planner system (LPS) is a collaborative planning and project management strategy used to enhance efficiency and communication. It involves engaging the individuals who are closest to the actual work— often referred to as the "last planners"— such as foremen and field supervisors, in the planning process.
This system emphasizes breaking down the project into manageable tasks and continuously improving the workflow through regular meetings and reviews. It is a core component of lean construction practices, designed to improve project outcomes by fostering teamwork and reducing waste.
Last planner sytem can be used in many project delivery methods, but is commonly part of integrated project delivery It can be a game changer for companies that want to make their planning more accurate and realistic, improve on-time project delivery, and increase transparency for all project stakeholders.
This article will explore the main components of the last planner system, including key strategies and best practices for executing this planning methodology.
Table of contents
The Last Planner Process
The last planner system embodies the principle of respect for people and their expertise, which helps companies maximize the effectiveness of collaboration.
LPS shifts the planning and the input to the person they call the last planner, who will ultimately be out there installing the work in the field. Who better to ask for input on the schedule than the people who will be performing the work?
Ben Ashburn
Staff Trainer & Program Manager
Procore Technologies
Implementing the last planner system involves multiple steps, the most well-known being pull planning. However, the last planner system consists of a lot of detail, going from an overview of the master schedule to a gradual breakdown of more detailed scheduling.
Master Scheduling
The master schedule is the overall plan of work and sets out big-picture milestones, such as “foundation begins” and “foundation ends.” During this step, design and construction teams, including the last planners, establish completion dates for major project components.
Phase Scheduling
Phase scheduling takes the activities between the large milestones and breaks them down into more manageable work segments. This step involves pull planning techniques, with teams looking at project milestones and working backward to determine how to complete the work on time and most efficiently.
For instance, between the concrete start and finish, the team needs to build and finish the form, create the steel reinforcement or have it delivered, schedule inspections and pour the concrete. This can be broken down even further into areas of the project, such as the northwest portion of the building or the addition.
During phase scheduling, teams can identify what needs to be in place for each trade to begin their scope of work. This level of detail includes determining the handoffs, where each trade can hand off the job to the next team.
Respect and Teamwork
Using the last planner system leverages and respects the expertise of the people responsible for varied trades and components of the work. Project team members and trade partner contributes ideas to the scheduling with knowledge of the specialty work their crews will perform. Many problems that might otherwise arise can be avoided through collaborative planning and teamwork involving experts tasked with completing each part of the build.
Lookahead Planning
During lookahead planning, the teams involved in the work planned for the next few weeks — typically about six weeks — will get together to determine more detailed plans to prepare the site for each trade’s work. These plans are the “where and when” of what each team will do during the weeks ahead.
The discussion includes details on what each team needs to do to make the site ready for the next trade. Each trade can describe the conditions required to start work immediately, which can include cleaning the site, rebar being tied off and inspected or any other preparation for the hand-off to the trade coming in next, commonly called a make-ready.
Weekly Work Planning
Teams usually meet each Monday to examine the six-week plan and the week ahead and make promises of work to complete. Reviewing the work plan weekly allows each team to determine exactly what tasks must be completed to stay on pace with the plan.
You're working with the people who can and will promise to make tasks happen. You have everyone who needs to talk with each other right there, and the team can get on the same page before they leave the meeting.
Ben Ashburn
Staff Trainer & Program Manager
Procore Technologies
During the weekly meetings, teams report on Percent Plan Complete (PPC) and discuss lessons learned and reasons for any delays in completing portions of the plan. Sometimes, reasons for not staying on schedule are out of the team member’s control, and the superintendent may need to call project managers or architects to resolve the issue. However, most of the planning and adjustments occur in the on-site meeting.
Daily Huddles
Every morning, the last planners — the crew leaders for each trade— meet briefly with the GCs site superintendent on site to check progress on the weekly promises. Crew leaders can identify constraints— obstacles or hurdles to the work for the day or week — so the team and superintendent can make adjustments to minimize or remove the constraints for work to proceed.
Constraints can include things such as a delayed delivery, running behind in some aspect of work or waiting on approval or inspection. One team might need to work on a Saturday to get back on schedule, and other team members may be able to help find ways to deal with constraints.
Best Practices for Implementing the Last Planner System
The construction industry is beginning to see the value of the collaborative work style involved in the LPS. Yet, as it is a change from previous workflows, it takes time and effort to start incorporating the method.
Hire a consultant.
Hiring a consultant or trainer with experience in the LPS can be beneficial to run the first few meetings. Shifting the way of working with the assistance of someone who has completed numerous projects using this method makes it easier for team members to adapt to the process.
Include last planner system in contracts.
All team members and crew leaders need to invest time in participating in the last planner system. Attending meetings should be part of the contractual obligation of all contractors involved in the project.
Be accountable, not confrontational.
Getting buy-in from team members unfamiliar with the last planner system can be challenging, especially if they are not used to being held accountable in frequent meetings. Setting the tone that everyone is in this together and will work through it together can help. Team members depend on each other, and changing the culture to value accountability rather than blame can be a radical shift for some team members.
The team is just reviewing the facts. not pointing fingers at anybody. We're just saying, ‘Here's what's holding us back,’ and figuring out why. If it's done in a non-confrontational manner, it creates a real sense of collaboration and teamwork. And people generally like it.
Ben Ashburn
Staff Trainer & Program Manager
Procore Technologies
Have visual aids onsite.
A large whiteboard or other visual chart in the trailer for daily and weekly meetings keeps the details accessible to the last planners. Columns for prerequisites, constraints and other information are used, with color-coding or distinct shapes representing each element type. Often, the board uses large sticky notes so elements can be easily moved as needed by the last planners themselves.
Planning for the Future of Scheduling
The logic of having people who will perform the work involved in scheduling seems obvious, but it is a substantial change for construction companies that are used to imposing schedules created by the GC.
However, as more contractors shift to using the Last Planner System in scheduling construction work, more workers will be familiar with it, and implementation will be more straightforward. Investing in the work required to use the Last Planner System can improve problem-solving, reduce delays, and create a more cooperative and less stressful work environment.
Was this article helpful?
Thank you for your submission.
100%
0%
You voted that this article was . Was this a mistake? If so, change your vote here.
Scroll less, learn more about construction.
Subscribe to The Blueprint, Procore’s construction newsletter, to get content from industry experts delivered straight to your inbox.
By clicking this button, you agree to our Privacy Notice and Terms of Service.
Categories:
Tags:
Written by
Ben Ashburn
21 articles
Ben Ashburn is a Senior Construction Education Trainer at Procore. After a successful career as a construction estimator — working his way up from estimating manager to senior estimator — Ben has spent the most recent part of his career in construction sharing his skills with other as a construction educator. Ben has an extensive background in construction education: He has been an assistant professor in the Department of Construction Science at Texas A&M, and lectured about estimating, scheduling, management, and other related construction topics at Murray State University. He has been a construction training and learning development partner with Procore since 2019.
View profileJulia Tell
50 articles
Julia Tell is a freelance writer covering education, construction, healthcare, and digital transformation. She holds a Ph.D. in Media & Communications and has written for publications including Business Insider, GoodRx, and EdSurge, as well as nonprofits, international businesses, and educational institutions.
View profileExplore more helpful resources
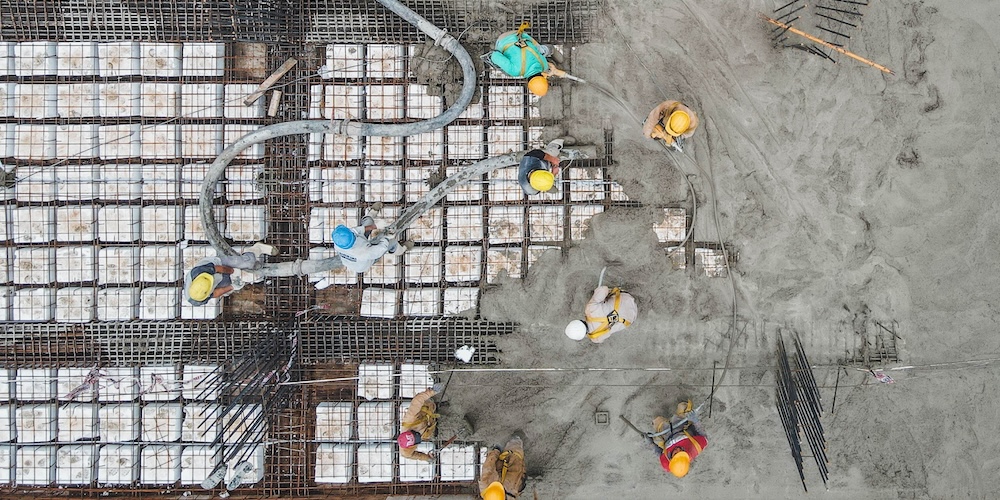
Mastering Construction Resource Management: Strategies for Success
Completing construction projects successfully requires the careful management of various resources: labor, materials, equipment, money, time and information. Since these resources are finite, allocating them wisely is crucial for minimizing...
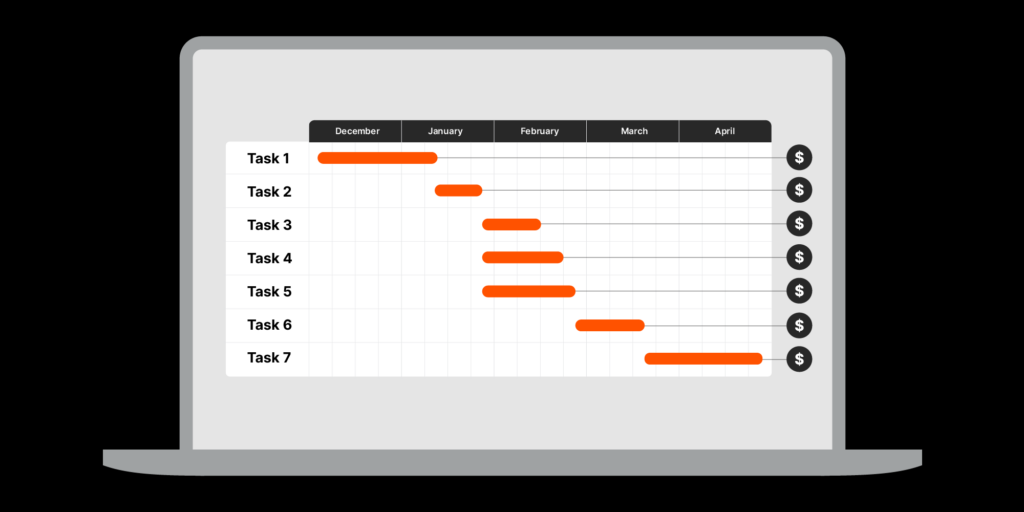
Cost-Loaded Construction Schedule: Analysis, Risks & Benefits
Both scheduling and cost control are make-or-break aspects of construction projects, but in many cases the two areas are kept very separate from one another — the project scheduler and...
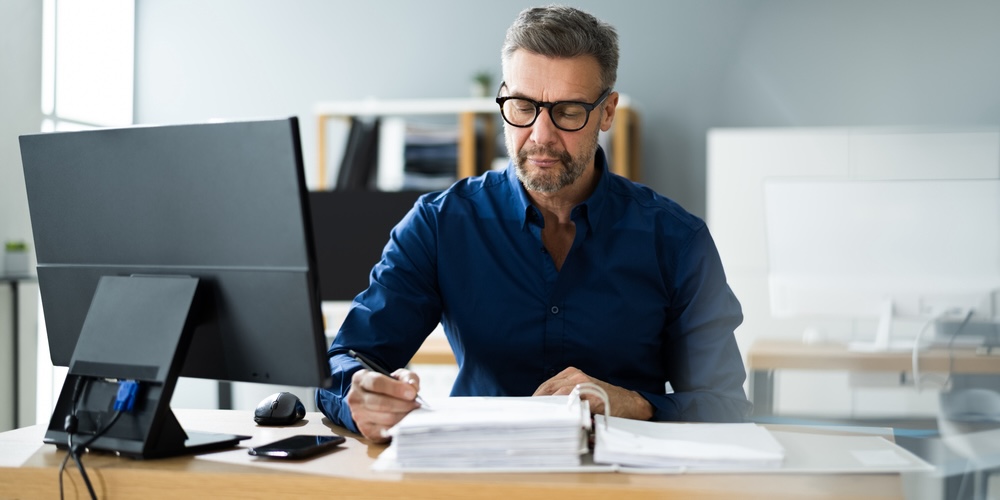
Forensic Schedule Analysis: Unlocking Insight Into Project Delays
Though construction sites may sometimes look like a large collection of machines, ultimately, it’s people who get things built. However, people aren’t perfect, and delays happen all the time —...
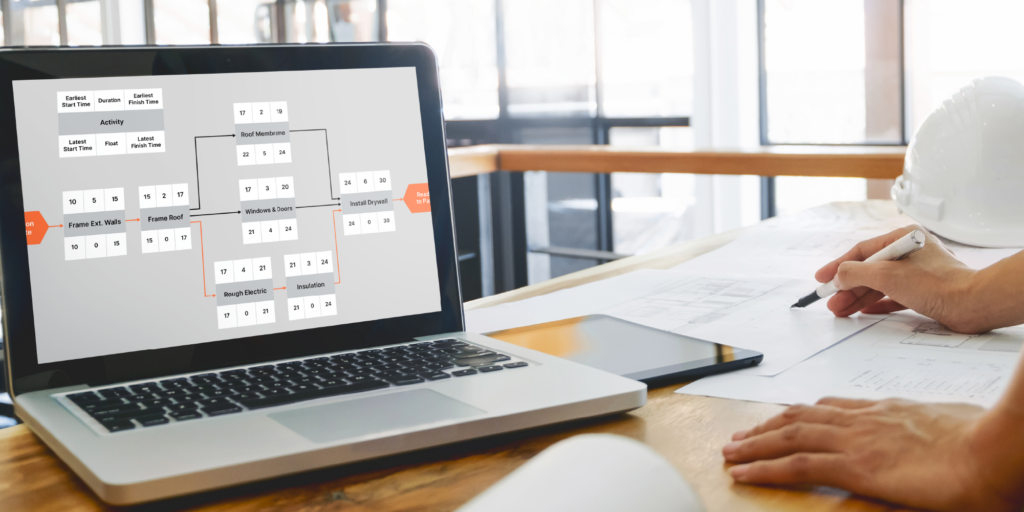
Mastering the Critical Path: A Guide to CPM in Construction
While every task must be completed to complete a construction project, some tasks are more critical than others. It’s crucial to be able to identify which activities must be finished...
Free Tools
Calculators
Use our calculators to estimate the cost of construction materials for your next project.
Templates
Find a template to help you with your construction project tasks.
Material Price Tracker
Get the latest U.S. retail prices and view historical trends for common building materials.
Glossary
Explore key terms and phrases used in the industry.