— 6 min read
Mechanical Rough-In Inspections: Preparing & Responding
Last Updated Jun 6, 2025
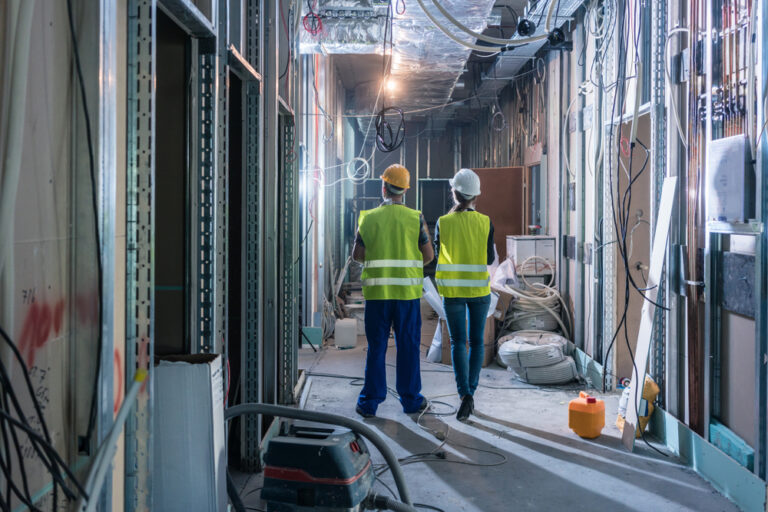
A mechanical rough-in inspection is a key step in delivering a successful construction project: It helps make sure the mechanical system meets all required specifications and regulations and — most importantly — performs as required.
Mechanical rough-ins are parts of the mechanical system that are installed before walls are completed. They usually include things like ducting, pipes and electrical wiring related to the HVAC system in the building but are not yet completed or commissioned for use.
This article will discuss what happens during a mechanical rough-in inspection, how to prepare and next steps for construction after passing or failing.
Table of contents
What is a mechanical rough-in inspection?
A mechanical rough-in inspection is an on-site inspection of all mechanical work done to date, usually conducted by a licensed building inspector. This inspector could be a building inspector who works for the city or, on larger commercial construction projects, a third-party building inspector hired by the project team.
The building inspector will visually inspect, measure, photograph and record details of all ducting, insulation, dampers and controls and other parts of the system to make sure that they meet all local building code requirements.
When does a mechanical rough-in inspection happen?
A project team will usually schedule a mechanical rough-in inspection after all the system components mentioned earlier are installed and in place but before the walls are completed.
Mechanical rough-ins are usually also completed and inspected before other services — like the building’s plumbing and electrical — are completed because ducting and related elements of the mechanical system are often installed behind those.
This way, if something needs to change after the inspection is completed, builders won’t have to work around or remove those other services. However, it also means that while contractors don’t want to schedule this inspection before everything is completed as required, they shouldn’t wait too long — because some work may be on hold until it is completed.
A Typical Mechanical Rough-in Inspection Checklist
Since the specification and design of a mechanical system varies dramatically from one building to another, there may be some unique features that need to be inspected in some buildings, but usually, the mechanical rough-in checklist will include the following items:
- Pipe and ductwork locations
- Pipe and ductwork sizes
- Pipe pitch to confirm that the pipes are at the correct angle to ensure proper drainage where necessary
- Pipe joints and ductwork connections and joints
- Pipe and ductwork supports
- Vent pipe placement
- Vent locations, sizes and installation
- Furnace and air handler locations
- Wiring runs for electrical associated with the mechanical system
- Location, size and type of electrical outlets and switches related to the mechanical system
- Grounding of the electrical associated with the mechanical system
- Access panels and circuit boards
- Leak checks
During each step of the inspection, the building inspector will refer to the project plans, specifications and the local building codes governing the project. They will check that everything is properly sized and designed to meet or exceed regulatory requirements and that everything has been installed in the correct locations, to the correct dimensions, etc.
As the building inspector completes their checklist, they will document any issues or noncompliances in writing and with photographs, which will all form part of the inspection report.
What happens if a contractor fails a mechanical rough-in inspection?
If a contractor fails an inspection, they will need to make all the changes required by the building inspector and then schedule another inspection to check that all the problems noted have been corrected satisfactorily.
Most building inspectors will pass or fail mechanical rough-ins by room, floor or location, so when they return for a follow-up inspection, they will only inspect the areas that did not pass the previous time.
This means that in the areas that did pass, other work can commence or continue, which helps minimize project delays.
Sometimes, if issues are very minor and there’s enough time while the inspector is still on-site, a crew might be able to make the necessary changes on the same day, have that area re-inspected before they leave and pass on the second try.
Also, remember that unless contractors are working on a design-build project, design responsibility for mechanical systems usually rests with the client’s architecture and engineering team.
So, if a contractor follows all the specifications and drawings for the project and a building inspector fails a portion of the work for code noncompliance, they may be able to request a change order to cover the cost of remedial work.
How to Prepare for a Mechanical Rough-In Inspection
Even if the building inspector handling a mechanical rough-in inspection passes some areas, it’s always best to pass in every work area during the first inspection.
There are several ways to create the best chance of passing a mechanical rough-in inspection.
- Make sure the crew is always working from the latest revisions of all drawings and specifications.
- Refer any discrepancies in the design to the project team as soon as possible — and document every request for information (RFI) response.
- Conduct in-house inspections of all mechanical rough-ins as they are completed and remediate any problems as they arise.
- Create in-house inspection test plans (ITPs) and inspection checklists and use hold points so work is compliant at every step before moving on.
- Purchase materials from reputable suppliers and approach manufacturers for input about optimal installation processes where applicable.
- Consider phased installation on larger projects, which will allow for the inspection of smaller areas at a time while work continues on other parts of the project.
- Include inspections in planning by accounting for downtime while they’re conducted — and make sure the team is ready for every inspection well before the date arrives.
The more frequently builders conduct their own checks during the mechanical system installation, the less likely the inspector will find any serious problems during the official inspection.
Inspection Record-Keeping Tips
Construction projects run on paperwork. While it might take boots on the ground and skilled artisans to get the work done, if they don’t have meticulous documentation, there can be big, expensive problems.
All reports and other documentation from every mechanical rough-in inspection should be added to the project records.
Not only will the client probably expect all inspection and other reports to be submitted with the closeout package, but they can be useful in the event that there are any disputes about the work, warranties or other issues at a later date.
It’s always a good idea to keep multiple copies of these types of reports in digital and hardcopy format, so they're easy to access when needed. Using a digital project management solution that includes a document archive is a good place to store a copy for easy access and collaboration as needed.
Stay updated on what’s happening in construction.
Subscribe to Blueprint, Procore’s free construction newsletter, to get content from industry experts delivered straight to your inbox.
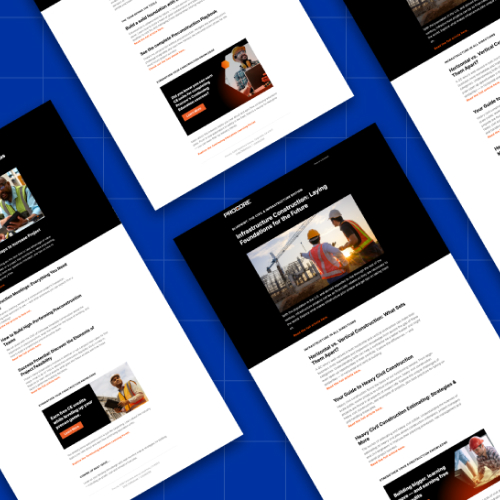
A Valuable Step In the Construction Process
It’s easy to think of mechanical and other rough-in inspections as an unnecessary delay in the schedule, but the truth is that these kinds of inspections are important to delivering quality construction projects that are safe and will stand the test of time.
Human error, design flaws and similar issues do arise on construction projects from time to time, and inspections are intended to catch those mistakes before they cause real problems so that they can be properly corrected before proceeding to the next phase of work.
So, when it comes to mechanical rough-in inspections, treat them as a tool and focus on maintaining high-quality standards, following specifications and drawings to the letter and taking a little extra time to plan and prepare.
Was this article helpful?
Thank you for your submission.
0%
0%
You voted that this article was . Was this a mistake? If so, change your vote here.
Scroll less, learn more about construction.
Subscribe to The Blueprint, Procore’s construction newsletter, to get content from industry experts delivered straight to your inbox.
By clicking this button, you agree to our Privacy Notice and Terms of Service.
Categories:
Tags:
Written by
Tamara Aspeling
Tamara Aspeling is a trained construction estimator and project manager with 25 years of industry experience. She started writing professionally in 2008 and has since written extensively for the construction industry, including publications like Modular Advantage magazine. She is also a traditionally published nonfiction author and the owner of The Construction Writer Inc. Tamara studied at Western Province Technical College in South Africa and completed her national certificate in 1999. She also holds an SEO Certification from Google and a Content Marketing Certification from HubSpot.
View profileExplore more helpful resources
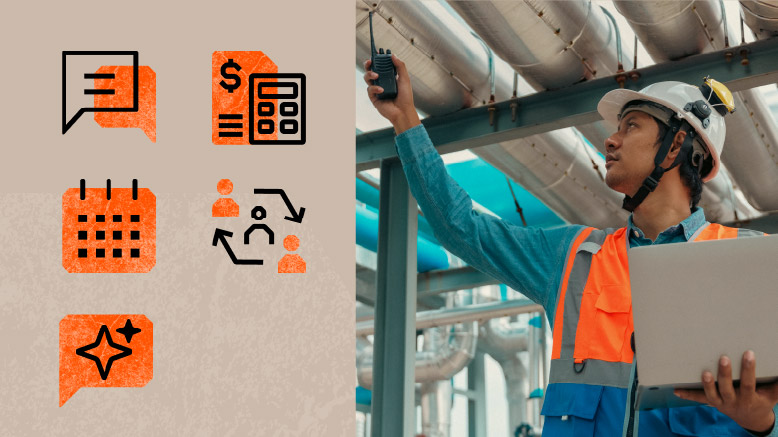
The Top 5 Skills of High-Performing MEP Professionals
Compared to standard MEP professionals, high-performing MEP pros don’t just get the job done. They also combine five key skills around technology, scheduling, finances, communications and flexibility into a proactive approach...
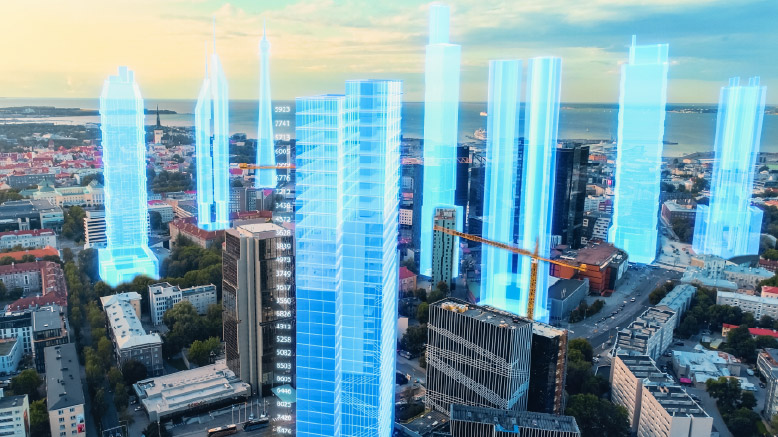
How AI is Reshaping Decision-Making and Project Resilience in Civil Construction
In construction, the ability to make informed, timely decisions is paramount. No longer is it sufficient to rely solely on historical data or reactive problem-solving. Enter artificial intelligence (AI), a...
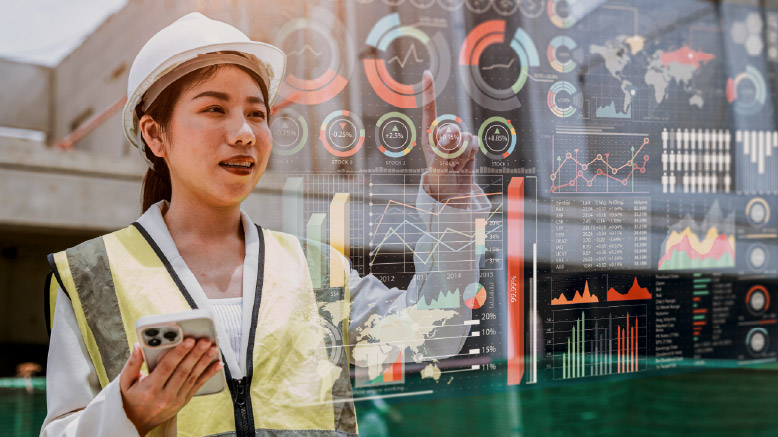
How AI is Redefining Efficiency & Safety in Civil Construction
As demand for new and modernized infrastructure surges, the civil construction industry faces an imperative to deliver projects with unprecedented speed, precision and safety. Emerging at the forefront of this...
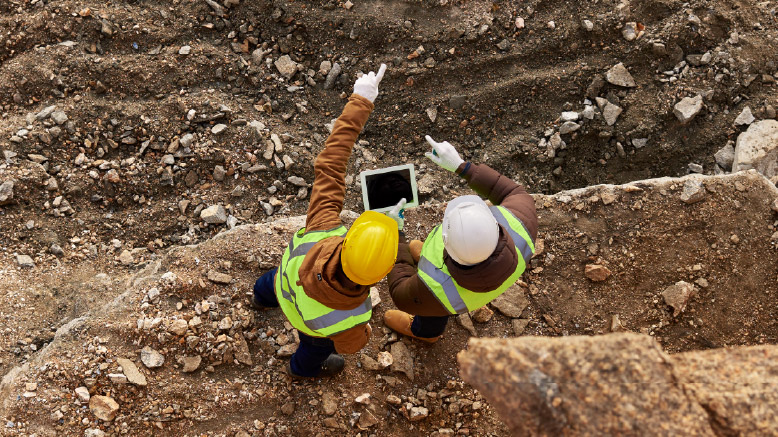
Building a Culture of True Tech Readiness in Civil Construction
While significant investments are pouring into revitalizing the nation’s infrastructure, the true capacity to capitalize on this opportunity hinges on more than just funding — it relies on a fundamental...
Free Tools
Calculators
Use our calculators to estimate the cost of construction materials for your next project.
Templates
Find a template to help you with your construction project tasks.
Material Price Tracker
Get the latest U.S. retail prices and view historical trends for common building materials.
Glossary
Explore key terms and phrases used in the industry.