— 8 min read
How to Coordinate MEP in Construction
Last Updated Sep 10, 2024
Last Updated Sep 10, 2024
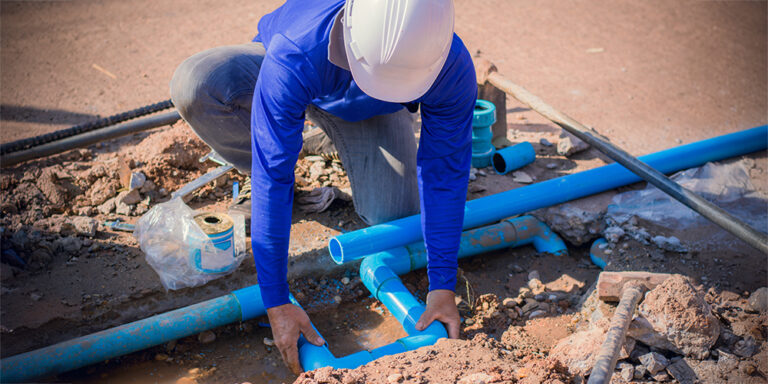
In a building, the mechanical, electrical and plumbing, or MEP system, is essentially the structure’s central nervous system. The MEP system integrates essential services — from lighting to air conditioning to sewage control — that help assure the building’s functionality, safety and comfort.
In essence, MEP in construction can be defined as the interconnected systems that make buildings suitable for human use. It’s also sometimes abbreviated as MEPFP, an expansive acronym which includes the fire protection system, as these are all interdependent components of a building’s design.
This article explores the coordination of MEP in construction, including its significance for building safety, the trials of maintaining adherence to ever-shifting codes, and best practices for dealing with trade workers who perform vital MEP services.
Table of contents
Importance of MEP Coordination
The various elements of mechanical, electrical and plumbing systems are all interconnected. Implementing this system sometimes requires working with MEP engineers, who are responsible for making sure the design of these systems is up to code, efficient and sustainable.
The mechanical component primarily involves heating, ventilation and air conditioning (HVAC) systems. These systems regulate the building’s internal environment, controlling temperature, humidity and air quality.
Plumbing systems are responsible for supplying water, removing wastewater and ensuring proper drainage and sanitation. Efficient plumbing systems provide potable water for drinking, cooking and cleaning, while also handling the safe removal of sewage and stormwater.
Electrical systems distribute power throughout the building, ensuring that all devices and amenities have the electricity they need to operate. This includes lighting, outlets, appliances and specialized equipment. Electrical systems are also necessary to power other MEP components, such as HVAC systems and plumbing pumps.
MEP coordination is about understanding all the sequence of activities needed to deliver a complete construction project. It is the overlaying of all the different systems and involves making sure that each system has all the necessary requirements. For instance, when installing an air conditioning unit, power, structural support and backing are needed.
Successful MEP coordination involves establishing a step-by-step process for pre-construction, construction, and close-out. During preconstruction, it’s necessary to set goals and milestones for engineering drawings, followed by milestones for the Business Information Modeling (BIM) system.
Stay updated on what’s happening in construction.
Subscribe to Blueprint, Procore’s free construction newsletter, to get content from industry experts delivered straight to your inbox.
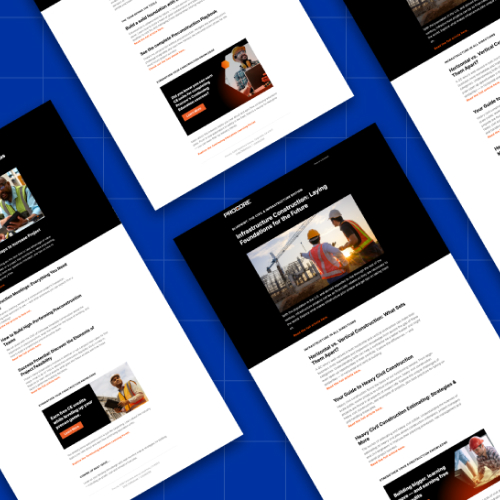
Common Challenges with MEP Construction
The general contractor (GC) should act as the anchor of all communications on the worksite when it comes to MEP coordination.
Being involved in coordination — especially when it comes to designing the building’s MEP system or managing code updates — can help a GC overcome a few common challenges with MEP construction.
Pro Tip
During the first pre-construction meeting, it's crucial to have a solid agenda and assign timelines and deadlines. Each system — like the fire alarm, HVAC or plumbing design — should have specific milestones. Establish a platform where all trades can make updates, ensuring everyone is looking at a live model. This constant communication helps identify and address issues before they escalate.
Gaps in Communication
The most challenging projects occur when the general contractor fails to manage the information between all trades. This can result in a disconnect between the mechanical and electrical teams especially, since proper functioning of HVAC systems requires electrical hookups.
A common challenge occurs with gaps in communication and update lapses in BIM models. Often, a trade — whether electrical, mechanical, or plumbing — may forget to update the model. When that happens, a project’s progress can quickly go south because construction may proceed based on outdated drawings.
Pro Tip
It's important to have someone within your team who communicates with the building and safety director. They can provide insights into future code changes, allowing you to make the necessary provisions.
Managing Code Changes and Updates
One of the significant challenges in MEP coordination is dealing with constantly evolving building codes. Changes in these codes can create complexities that require careful planning and adaptation.
For multi-year projects in particular, owners may request that projects follow the latest and most stringent codes, even if these codes are not yet officially in place. This requires the project team to make provisions for future code requirements, which can be challenging since the specifics of the new code may not be fully known.
If a project starts in 2024, the owner might ask for compliance with the 2025 code cycle, even though it’s not out yet. This requires making necessary provisions to ensure the system can meet those future codes.
On one project, we had an issue with electrical vehicle (EV) chargers. Initially, we followed the 2019 code, but the owner later wanted us to adhere to the 2022 cycle, which changed the definition of a charging station. We anticipated this change and ran extra conduits to meet the new requirements, preventing costly rework.
Gino Tomala
Project Manager
JRM Construction West
Complications with Design-Build
In a design-build project, the owner contracts with one entity, the design-builder, which manages both the design and construction services. This can result in a more streamlined process, but means that the responsibility for designing the complex MEP system falls upon the GC and their design-build team.
In traditional design-bid-build projects, MEP systems are designed in detail before construction begins, allowing for thorough planning and coordination. However, in design-build projects, the design phase overlaps with the construction phase, which can lead to challenges like code adherence and coordination issues.
I worked on a design-build hospital project on an existing campus. Each section had nearly 20 different subsections, and each had to follow the exact same code cycle. It was also difficult to find a happy medium and compromise between all of the different trades. Some of the changes to design were very big and substantial, and it was tough to find backing to cover the cost.
Gino Tomala
Project Manager
JRM Construction West
Effective Strategies for MEP Coordination
Meticulous planning and continuous communication is necessary to properly install these components — and following a few best practices can help a GC smoothly transition to handover.
Involve trade workers early.
Proper proactive planning necessitates early communication with the foremen and crews who are actually going to be performing the labor. Onboarding them early in the project’s life cycle — and taking time to explain their scope of work and the project’s vision — may allow for the identification and resolution of potential conflicts before construction begins.
Set the agenda during preconstruction.
From the very first preconstruction meeting, create a solid agenda from which the project leadership team can begin to assign timelines and deadlines for sections of the work. Generate milestones for mechanical, electrical and plumbing trades individually so each trade understands their own deadlines and how they align with the overall project goal.
Use a centralized digital platform.
Effective MEP coordination also relies on using a centralized platform where all trades can make real-time updates. In a fast-paced industry, working with the latest information is vital, and reduces the risk of errors and miscommunication.
Each trade should have permission to post and make updates to the centralized software program, and access to the same live models. Keeping communication inside of the software program—and not in text and email communications — can also help a GC manage their documents and stay organized for closeout.
Managing Union MEP Trade Workers
In most places, trade workers are part of long-standing unions, and the rules of these organizations add another layer of complexity to MEP coordination.
Union rules typically define the specific tasks that union members are allowed to perform, which can impact the scope of work and require careful coordination. Often, a contract that’s drawn at the start of a project doesn’t adequately address the entire scope of work for trade workers, and additional documentation might be needed.
A lot of times, elevators tend to be a gray area. As of today, I don't know if anyone can tell you which trade owns elevator installation—especially if they need extra conduits hooked up to the electrical system. Some might say that scope of work is for elevator trade workers. They might say, no, that’s for the electrical trade. If the electrical trade workers do it, they likely have to submit some sort of form letting their union know that they understand that they may be violating union contracts and may be infringing on another trade’s scope.
Gino Tomala
Project Manager
JRM Construction West
Harnessing Technology for MEP Coordination
The current state of technology adoption in the MEP field is filled with both opportunities and challenges.
While advancements in technology have the potential to revolutionize MEP coordination, the construction industry has been slow to adopt tools like artificial intelligence (AI) and machine learning. A significant barrier is the fear of job security among field workers and the perceived complexity of these tools.
Despite resistance, there are many potential benefits of integrating technology into MEP coordination. For example, BIM systems can greatly benefit from AI-driven clash detection. A significant advantage of AI is the ability to expedite the submittal process, since it can handle the heavy load of paperwork involved at high speeds, freeing up time for task coordination and problem-solving.
There’s a need across the field of construction for better data analytics, which can help pinpoint the root causes of recurring issues.
We need to start looking at our productivity rates to begin with, and also at the duration of each activity. And from there, we may start to see which trades, or what activities, are causing the most problems or slow-downs on the worksite.
Gino Tomala
Project Manager
JRM Construction West
The Bottom Line of MEP Coordination
In essence, the GC is the playmaking quarterback of all MEP operations — they manage the intricate web of communications necessary for responsible coordination, problem-solving and setting deadlines to ensure the structure is functional and safe for human occupancy.
By embracing best practices and leveraging opportunities to harness technology, construction projects can achieve better MEP coordination, leading to smoother operations and successful project outcomes.
Was this article helpful?
Thank you for your submission.
100%
0%
You voted that this article was . Was this a mistake? If so, change your vote here.
Scroll less, learn more about construction.
Subscribe to The Blueprint, Procore’s construction newsletter, to get content from industry experts delivered straight to your inbox.
By clicking this button, you agree to our Privacy Notice and Terms of Service.
Categories:
Tags:
Written by
Gino Tomala
Gino Tomala is a Project Manager at JRM Construction West. His decade of experience in the construction industry has enabled him to handle a variety of projects. His ability to set realistic goals and follow through in a timely manner creates a controlled atmosphere on all his job sites. In his role as Project Manager, Gino oversees and maintains all construction schedules, adhere to all milestone changes, meet with clients, architects and subcontractors to prevent and solve any problems that may arise during the construction process. He also processes and approves all subcontractor change orders and invoices, maintaining cost control. Gino works closely with the project team to ensure all schedules put forth are manageable and realistic. He handles the scheduling of trades and deliveries, and the coordination of all on-site activities, both as they relate to the construction of the project and as they affect or are affected by the rules of building management. Prior to joining JRM, Gino helped coordinate and manage high-budget projects including the $1.4 billion Harbor UCLA Medical Replacement Center. Prior to Rosendin, Gino worked as a Project Engineer at Skanska, where he managed the Franklin High School renovation and a $1.2 billion manufacturing project in Hillsboro, OR. Gino is based in Anaheim, California.
View profileTrey Strange
26 articles
Trey Strange is a Peabody and Emmy-Award winning writer and producer based in Brooklyn, NY. Throughout his career, Trey has worked for the Huffington Post, Houston Chronicle, Out Magazine, Brooklyn Eagle, CNBC, INTO, and New York Magazine's Bedford + Bowery. He received his Masters in Journalism and Middle East studies from New York University, and Bachelors in the same subjects from the University of Houston.
View profileExplore more helpful resources

Preconstruction Partnerships: How Safety Pros Can Collaborate with Estimating & Proposal Teams
Construction leaders and safety professionals are developing a strong understanding of how safety programs positively impact project outcomes. When safety is woven into every aspect of operations from pre-construction to...
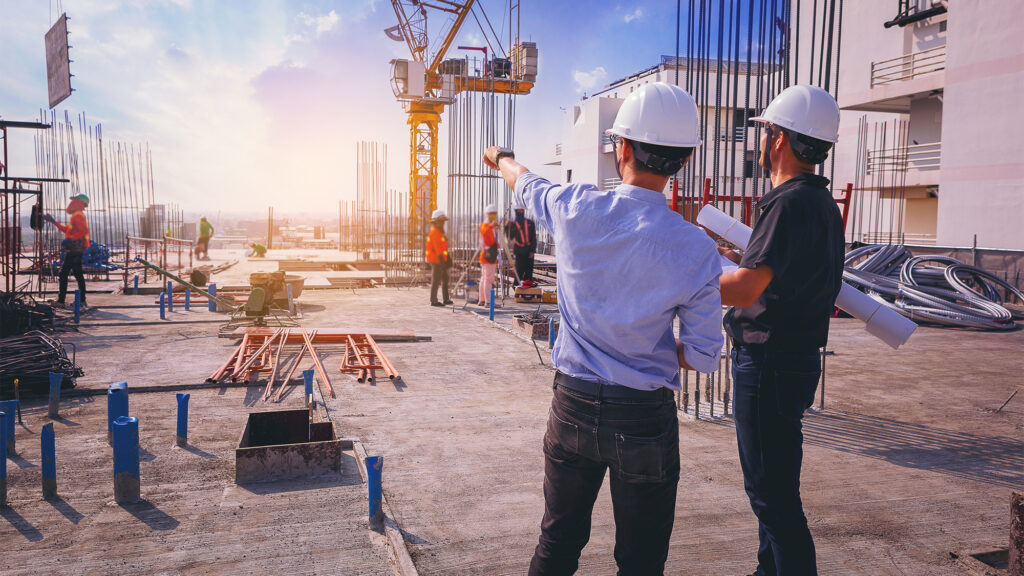
Construction Business Development: Tracking and Winning the Right Opportunities
Construction business development isn’t just a response to deadlines: It’s a long-term strategy rooted in focus, visibility and timing. Delays, funding gaps and market pressure have made it harder to...
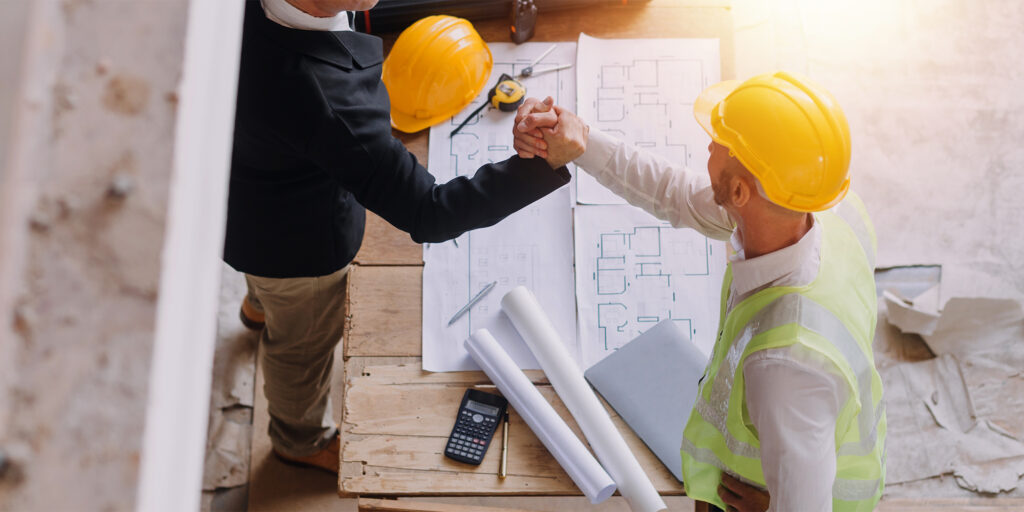
Qualifications-Based Selection: Prioritizing Expertise over Initial Cost
For large or complex construction projects, owners and public agencies often use qualifications-based selection (QBS) to prioritize experience and capability over merely selecting the lowest bid. QBS involves owners choosing...
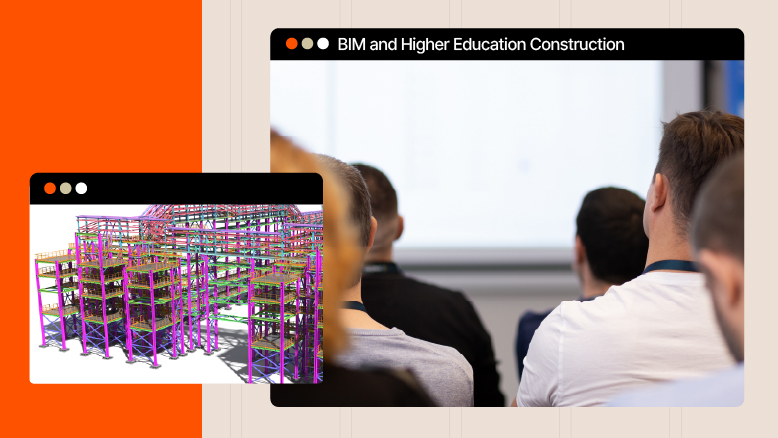
Using BIM in Higher Education Construction
As the construction industry changes, higher education institutions have started to implement building information modeling (BIM) at a rapid pace. If architecture, engineering and construction (AEC) companies want to work...