— 9 min read
Mastering MilCon: How to Tackle Military Construction Projects
Last Updated Nov 14, 2024
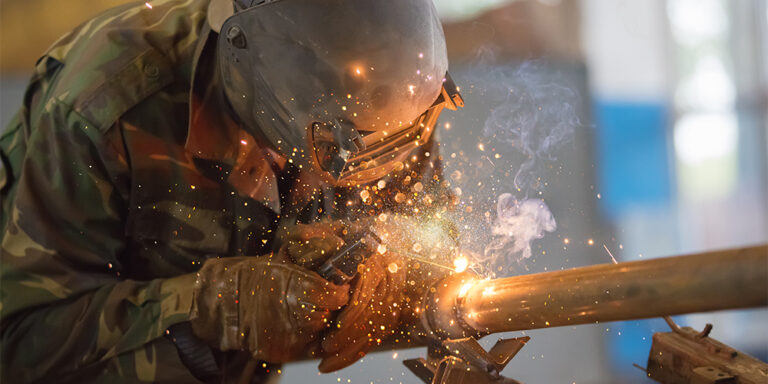
To succeed, construction companies need a consistent inflow of new projects. That can make working on military construction — or MilCon, for short — look particularly appealing.
The U.S. Department of Defense (DOD) gets multiple billions of dollars each year budgeted to allocate toward its MilCon projects. And because there’s such a steady stream of financing available, many contractors who get involved with MilCon report the consistent availability of new projects to bid. Plus, because the DOD is choosy about which companies it taps for its MilCon projects, becoming a known quantity to the DOD can mean less competition for these potentially high-dollar jobs.
That said, MilCon projects aren’t without their challenges. Specifically, contractors who get involved with the DOD have to manage stringent requirements. The DOD has its own master planning mechanisms, called installation master planning, along with its own security measures, processes, and project requirements.
As a result, MilCon construction is generally fairly complex and slow-moving. That shouldn’t scare construction professionals away, though. It just means that anyone interested in working with the DOD needs to know what to expect. This guide to MilCon can help.
Table of contents
MilCon Construction by the Numbers
Some facts and figures can help to frame up just how lucrative — and complicated — MilCon projects can be.
$16.67 billion
The amount requested in the Biden Administration’s Fiscal Year 2024 budget for DOD MilCon accounts (a decrease from the 2023 budget of $19 million)
5
The number of subchapters in the U.S. Code that govern military construction and military family housing.
150+
The number of MilCon projects that were reported as delayed in the DOD’s 2023 full-year report to Congress on military construction and military family housing.
In other words, there’s plenty of money allocated to this type of construction, but there’s also a lot of regulation that can add work and cause delays for contractors.
MilCon Acronyms and Abbreviations to Know
In addition to the bureaucratic processes that make MilCon projects complicated, the surrounding jargon can add another layer of complexity. Before getting further into this topic, then, it’s helpful to define some terminology.
Controlled Unclassified Information (CUI)
The information (e.g., drawings, specifications) provided to contractors may fall under the CUI umbrella, subjecting it to security measures with which the contractor may need to prove compliance.
Defense Biometric Identification System (DBIDS)
This is the database used to capture the identities of people with permission to enter military installations, then identify those individuals using barcodes on a badge or fingerprint scans. Some branches of the government also maintain their own identification systems, like the Navy Commercial Access Control System (NCACS).
Electronic Construction Management System (ECMS)
The ECMS is a construction project management software maintained by the Naval Facilities Engineering Command. Contractors may be required to use it on Navy projects.
Multi-Agency Contract (MAC)
Governed by the Economy Act, MACs are task-order or delivery-order contracts that allow government agencies to procure supplies and services from another agency. With MilCon, MACs allow the DOD to contract design, general contracting, and subcontracting companies to work on projects.
Resident Management System (RMS)
The RMS is the quality management and contract administration program the Army Corps of Engineers uses to oversee construction projects.
The Process of MilCon Projects
The DOD has laid out extensive documentation outlining requirements for MilCon projects. And the expansiveness of those regulations often extends project timelines. Per a Congressional Research Service report on MilCon, projects are routinely expected to take five years or longer to complete.
But within those strict parameters, there’s room for deviation. The DOD aims to standardize the MilCon process, but project execution depends heavily on the individual military personnel involved, particularly the project manager. Some are open to adopting technology to help move the project forward, for example, while others require hard copies of nearly everything.
How the project moves forward also depends on the level of security required. It’s generally easier to progress simple projects with lighter security needs, like the construction of barracks, than it is for builds with extensive specifications and security measures (e.g., armories, hangars for specialized military aircraft, etc).
While every project will have its own deviations from the standard due to its unique requirements, MilCon projects generally move through the main construction phases as follows.
Preconstruction
DOD construction projects have to begin with DD Form 1391, which captures the project’s purpose and cost. (See a completed Form 1391 here as an example.) Once that form is completed, the project is handed to the appropriate party based on the military branch spearheading it:
- Installation Management Command (IMCOM) for Army projects
- Air Force Installation and Mission Support Center (AFIMSC) for Air Force projects
- Naval Facilities Engineering Command (NAVFAC) for Navy projects
- Marine Corps Installations Command (MCICOM) Regional Command for Marine Corps projects
- The Adjutant General for National Guard projects
The military branch organizes the project — which often takes a year or longer — then passes it back to the Office of the Secretary of Defense, which reviews, prioritizes, and consolidates projects.
Consolidated projects are then handed to the Office of Management and Budget, which makes final revisions and factors those projects into the overarching DOD MilCon budget request submitted to the President. The Executive Office of the President then makes its budget request to Congress (like the $16.67 billion requested for 2024).
Once the full-year budget is authorized and approved by Congress, the funds get allocated back to the appropriate branch of the military.
Per the Congressional Research Service, all of that usually takes about three-and-a-half years to complete.
While they can work with a design firm to plan the project, military facility engineers aren’t allowed to enter into a contract for the actual construction of a DD Form 1391 project until the funds have been authorized and appropriated. As a result, they don’t start to solicit bids until all of the above happens.
When Construction Professionals Get Involved
The three-year+ process to get a MilCon project from ideation to contract doesn’t mean the construction company needs to sit idly by. In the meantime, they can take steps to prepare to bid government projects, like registering with the System for Award Management (SAM) database and ensuring they’re paying the prevailing wage, a requirement on many government jobs.
Once the DOD opens bidding, SAM-registered construction companies can come to the table in an attempt to get awarded the contract. As part of the bidding process, they will need to submit a comprehensive list of all personnel that will be involved in the project — including subcontractors — because all individuals on the jobsite will need security clearance. They also need to prove compliance with any security requirements, like the DOD’s Cybersecurity Maturity Model Certification (CMMC).
Learn more about the importance of cybersecurity in construction.
If they get the job, the construction company can’t begin work until the personnel is cleared. Generally, each individual needs to get a background check and a form of authorization to enter the jobsite, like a DBIDS card. This commonly takes months. The more stringent the security required on the project, the more involved this vetting process is and, consequently, the longer it takes.
As individuals get cleared to work on the job, the contractor can start submitting its documentation for approval. Each phase of the contract may get approved at a different time, so initiating submittals promptly helps the project move forward more as quickly as possible.
Construction
In some ways, once construction gets underway, MilCon projects aren’t very different from private construction projects: The contractors are expected to execute on the contract documents.
But DOD projects generally have an overarching security focus layered on top. If the contractor’s team is used to using their cell phones to take progress photos, for example, they will probably need to find a workaround. A lot of MilCon projects don’t allow personal phones onsite, and specifically ban taking photos. Generally, though, the project manager on the military side can issue a phone or camera for use. Be advised, though, that every action taken with that government-issued device will be reviewed to ensure its use complies with security requirements.
Similarly, contractors may use the same equipment they would on any other project, but that equipment will generally be subjected to a thorough search before it’s allowed on the jobsite. It may also need to stay on the jobsite for the duration of the project after passing inspection.
MilCon construction can also create coordination challenges because it’s extremely common for drawings and specifications to have sections redacted. Because these details are often considered CUI, each party will generally only know what they absolutely need to know to complete their scope of work. Even general contractors may work with redacted contract documents.
There is often a full set of drawings in the jobsite trailer. Who can access those drawings depends on their security clearance and the applicable CUI measures.
Because redacted information can create confusion, it can lead to delays as parties seek out the details they need to feel confident about the work they’re preparing to install. Theoretically, though, there should always be a designated military project manager or another stakeholder on-site tasked with overseeing the project and smoothing out wrinkles like this.
Closeouts
Once construction is complete, MilCon handover closely mirrors closeouts on traditional private projects a decade ago. That is to say, the DOD generally requires a physical — not cloud-based — copy of any closeout documentation.
In some cases, they may additionally require that the documents be uploaded to their chosen software, like the Navy’s ECMS or the Army’s RMS.
Stay updated on what’s happening in construction.
Subscribe to Blueprint, Procore’s free construction newsletter, to get content from industry experts delivered straight to your inbox.
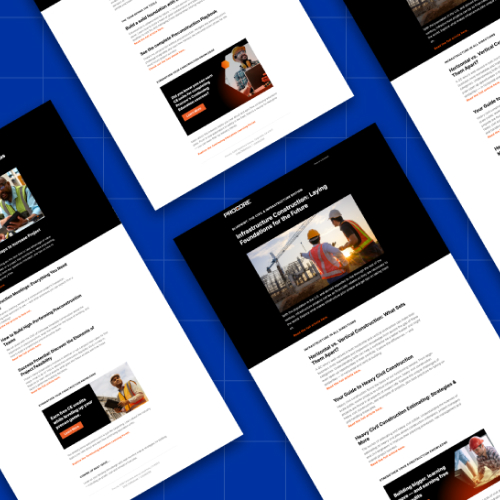
Looking Forward: MilCon and Technology
As the construction industry embraces new technology (albeit slowly), the way projects run is changing. 2-dimensional computer-aided design (CAD) has started to give way to 3D building information modeling (BIM). Project management software speeds submittals and enables the more accurate projection of schedules and costs. Drones and robots provide faster, more detailed assessment of site conditions and project progress.
At least, all of that is true on the private side. On public projects — and particularly DOD ones, with their extensive security needs — change is moving slowly. Everything is still almost exclusively handled in 2D, and often via hard-copy drawings and specs. Technology like drones are often strictly banned, and information exchange usually happens face-to-face, over the phone, and via email rather than in a streamlined software solution.
That said, branches of the military are making efforts to modernize their MilCon projects. Take, for example, Ignite, a communication software from AFWERX, the Air Force’s innovation arm.
Because of the deeply bureaucratic process and extensive security measures required for DOD projects, technological implementation will come slowly. But it does look like the DOD is working to adopt tools that can help to streamline and speed its notoriously slow MilCon projects.
Was this article helpful?
Thank you for your submission.
100%
0%
You voted that this article was . Was this a mistake? If so, change your vote here.
Scroll less, learn more about construction.
Subscribe to The Blueprint, Procore’s construction newsletter, to get content from industry experts delivered straight to your inbox.
By clicking this button, you agree to our Privacy Notice and Terms of Service.
Categories:
Tags:
Written by
Julie Colburn
View profileKacie Goff
66 articles
Kacie Goff is a construction writer who grew up in a construction family — her dad owned a concrete company. Over the last decade, she’s blended that experience with her writing expertise to create content for the Construction Progress Coalition, Newsweek, CNET, and others. She founded and runs her own agency, Jot Content, from her home in Ventura, California.
View profileExplore more helpful resources
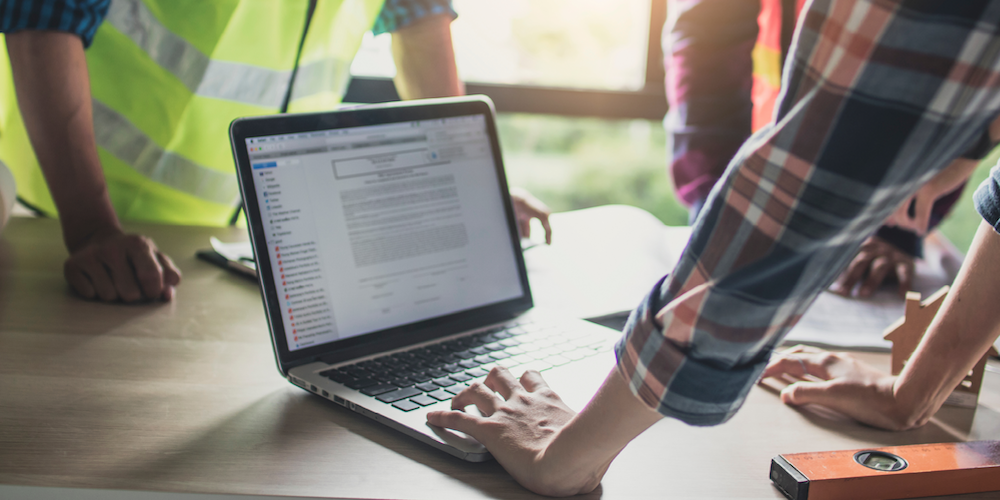
Sealed Bidding in Construction: The Ultimate Guide
For public construction in the United States, project owners typically use a sealed bidding process to promote transparency and cost-effectiveness. With this type of procurement, contractors submit sealed bids before...
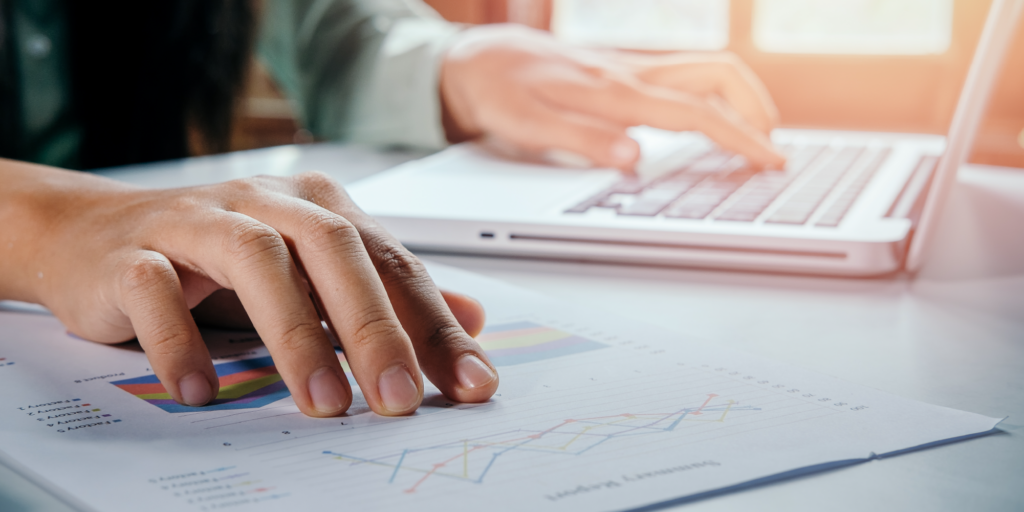
Bidding on Government Construction Contracts: A Contractor’s Guide
Winning a government construction contract can be lucrative for contractors. But contractors who want to win government construction projects must navigate a complex bidding process, increased regulation, and unique payment...
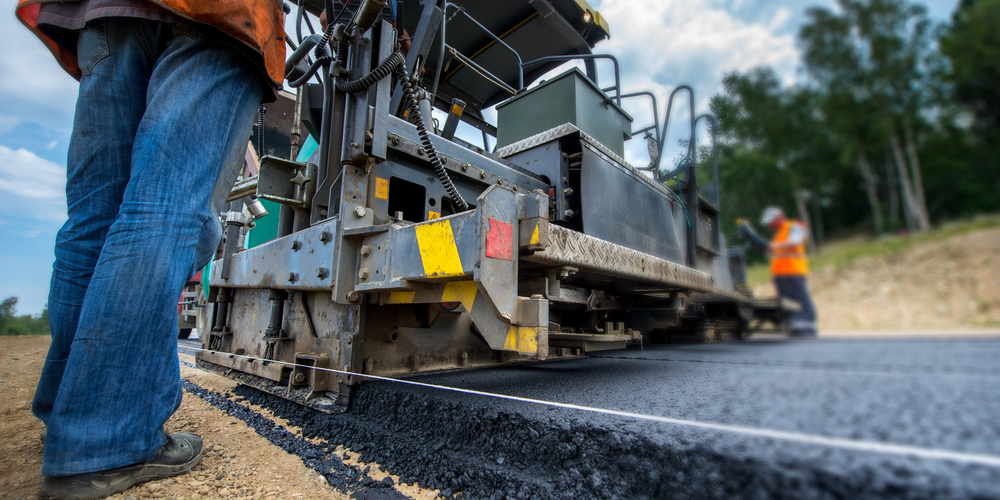
How to Qualify for Government Work as a Prime Contractor
Every year, the federal government awards billions of dollars to prime contractors to perform work. Since Congress passed the Infrastructure Investment and Jobs Act in 2022, billions more will be...
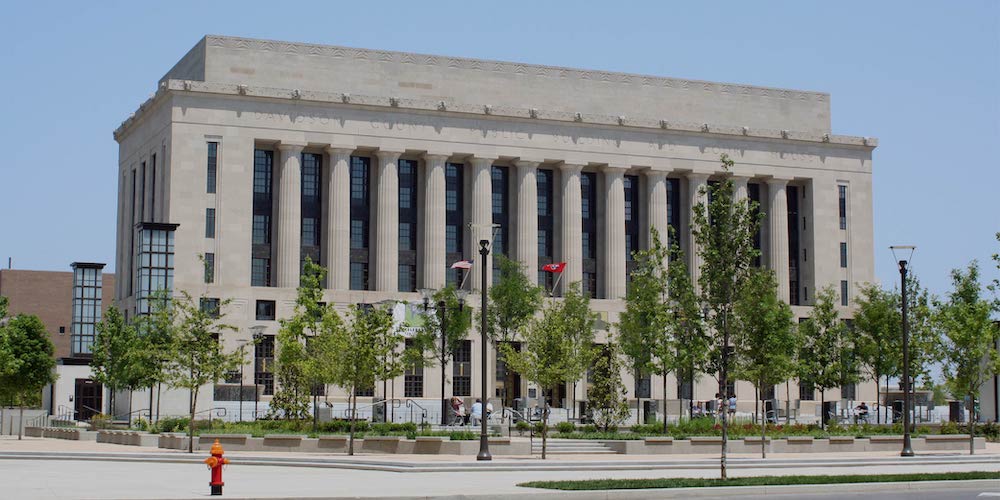
Little Miller Acts: Bond Requirements on State Construction Projects
For general contractors who commonly work on government projects, obtaining a surety bond should not be a new concept. Additionally, materials suppliers or specialty contractors may be familiar with the...
Free Tools
Calculators
Use our calculators to estimate the cost of construction materials for your next project.
Templates
Find a template to help you with your construction project tasks.
Material Price Tracker
Get the latest U.S. retail prices and view historical trends for common building materials.
Glossary
Explore key terms and phrases used in the industry.