— 6 min read
Modular Construction: Assembling the Future of Construction
Last Updated Oct 30, 2024
Last Updated Oct 30, 2024
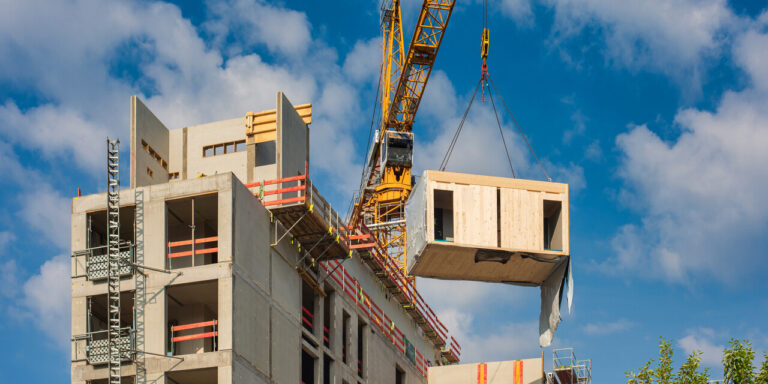
As the construction industry deals with a number of converging challenges, modular construction is emerging as a forward-thinking and highly technical solution to streamline the building process.
Modular construction is the process of building modules in a manufacturing facility, which are then shipped to job sites and constructed. Although the construction industry has used modular construction for many years, modern technological advancements like BIM have broadened its use cases.
Modular construction puts an intense focus on early planning, putting more risk on the preconstruction and design teams, in hopes to make construction faster, smoother and safer. Since manufacturers create and ship all modules before construction, any incorrect or damaged designs can lead to longer and more costly delays.
Table of contents
The benefits of Modular Construction
Modular construction has been popular at different times in US history, and is currently enjoying favor in other parts of the world, like China, but has yet to find its stride in modern North America. Builders aren’t accustomed to working with prefabrication – after all, it’s an entirely different way of building. If given a chance, and with the right set of circumstances, modular construction can offer a lot of benefits for both owners and contractors.
Reduced Timelines
Modular construction offers contracting teams the ability to work on two fronts at once: while ground preparation and foundation work is happening on site, the rest of the building can be in-process in a manufacturing facility. This dual approach can lead to drastically reduced timelines – some estimates claim a time savings of 20-50 percent – for a project’s construction phase and ensures that the two phases don’t depend heavily on one another.
Risk Management
Owners and contractors can control many of the variables that introduce risk into construction projects. Constructing modules in controlled settings significantly reduces the impact of weather, materials delays, and worker shortages. This approach enhances predictability and consistency, minimizing the variability often encountered in on-site projects.
Modular construction reduces risk by hyper-focusing on pre-planning, allowing you to build a part, piece, or entire entity off-site. These components are then shipped to the construction site, where they can either be assembled on-site or arrive fully completed and ready to be installed immediately
Ken Fuhrman
Senior Solutions Engineer
Procore Technologies
Heavy preconstruction planning allows for more efficient use of materials and workforce. Manufacturing teams can plan out which cuts of materials to use so that there’s less waste. Factory assembly makes efficient use of employee skill sets and time on the floor, while fitting together premade modules on site is often quicker and simpler than traditional on-site construction, requiring fewer labor hours.
Safer Working Conditions
Manufacturing facilities offer the benefits of carefully controlled workspaces, saving laborers from changing conditions like heat, wind, and rain. Indoor settings present the opportunity to use robotics elements to help complete some of the most dangerous tasks, and there’s significantly less risk for falls within factory walls. Work in this setting also prevents workers from having to work on top of one another or fighting for space to work on their trades.
Integrating modular construction into existing project frameworks
Some projects use modular elements into a traditional on-site build. The integration of modular construction into existing project frameworks requires careful planning and coordination.
Take for example a hospital construction, where space constraints necessitated the use of a prefabricated mechanical penthouse built off-site and later assembled on location. This approach not only addressed spatial limitations but also ensured that the project adhered to tight schedules without compromising quality.
However, fitting modular units into traditional job sites can come with its own unique challenges. For instance, storing modular units may require a significant amount of safe storage space. Without a storage area for the units, the manufacturer and project managers may find it daunting to coordinate the delivery of the right units at the right time.
Stay updated on what’s happening in construction.
Subscribe to Blueprint, Procore’s free construction newsletter, to get content from industry experts delivered straight to your inbox.
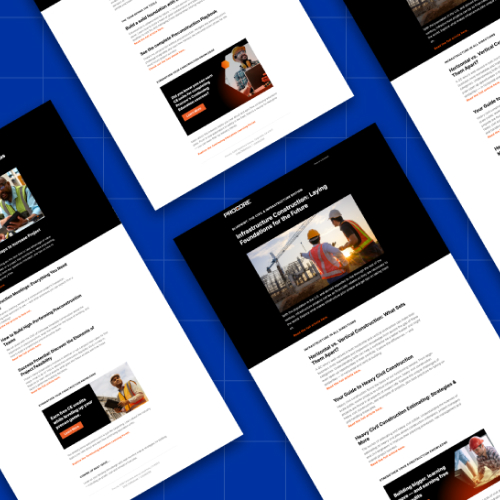
The challenges of modular construction
Despite its benefits, modular construction presents certain logistical and operational challenges. Some of the hurdles occur because modular construction isn’t all that familiar or popular in the US, so developers and contractors haven’t learned how to optimize the method just yet.
Planning and Logistics
Shipping and transporting prefabricated components can be complex. Inaccurate labels can make it difficult to determine where each piece belongs, especially if transportation becomes jumbled and modules arrive out of order. If this occurs, teams must ensure there is adequate landing space on or near the site to store the modules while awaiting installation.
Finally, although the manufacturing team avoids weather complications, the transportation team does not have the same advantage. Even bad weather can complicate the movement of large modules and make installation more difficult, especially when the modular unit must be placed on top of another finished piece without a roof.
Shipping was unpredictable because we were installing the structure on a finished roof with the occupied hospital directly beneath, which was very risky. We had to ensure everything was as precise as possible while executing the plan we developed over six to twelve months. The actual pick and shipping process went relatively quickly. We likely spent six to twelve months on pre-planning, with the build being the easier part. The construction was very focused, safe, and took place off-site in a controlled environment. This involved assembling everything, shipping it, and then reassembling it on site.
Ken Fuhrman
Senior Solutions Engineer
Procore Technologies
Dealing With Two Building “Sites”
Modular construction creates two separate building "sites": one where the structure will be erected and another at the manufacturing facility where the modules are built. Teams permitted to work at one site may not have access to the other, and the distance between the two sites might make travel inconvenient.
Moreover, regulatory considerations and union stipulations can affect the scope of off-site work, requiring construction managers to be adaptable and well-informed. In the hospital construction project mentioned previously, the regulations prevented manufacturing teams from installing any safety or fire alarm or suppression components in advance; instead, local technicians installed those elements on-site.
The future of Modular Construction
The success of modular construction largely depends on designers, but technology also plays a crucial role in addressing its challenges and increasing industry acceptance. Software solutions provide essential tools for intricate planning, coordination, and real-time tracking, which are vital for successful prefabrication and improved project management.
Building Information Modeling (BIM), in particular, enables detailed 3D modeling of projects. This capability allows architects and engineers to visualize designs and make necessary adjustments before construction begins, enhancing accuracy and reducing the risk of costly errors. Additionally, BIM's ability to detect design clashes early on helps resolve issues before they escalate, minimizing expensive changes and delays.
These technological advancements ensure that prefabricated components fit together seamlessly during on-site assembly, making the construction process more efficient and streamlined. As technology continues to evolve, it will further support the growth and acceptance of modular construction methods, potentially reshaping the future of the industry.
Was this article helpful?
Thank you for your submission.
0%
0%
You voted that this article was . Was this a mistake? If so, change your vote here.
Scroll less, learn more about construction.
Subscribe to The Blueprint, Procore’s construction newsletter, to get content from industry experts delivered straight to your inbox.
By clicking this button, you agree to our Privacy Notice and Terms of Service.
Categories:
Tags:
Written by
Ken Fuhrman
Ken Fuhrman is an experienced Senior Solutions Engineer at Procore Technologies, specializing in providing enterprise solutions for general contractors. With over a decade of experience in the construction and technology sectors, Ken has developed expertise in engineering and project management, contributing significantly to complex projects across the Greater New York and Philadelphia areas. He is a proud alumnus of Penn State University, where he earned a Bachelor of Science degree in Civil Engineering.
View profileKristen Frisa
67 articles
Kristen Frisa is a contributing writer for Procore. She also contributes to a variety of industry publications as a freelance writer focused on finance and construction technology. Kristen holds a Bachelor of Arts in Philosophy and History from Western University, with a post-graduate certificate in journalism from Sheridan College. She lives in Ontario, Canada.
View profileExplore more helpful resources
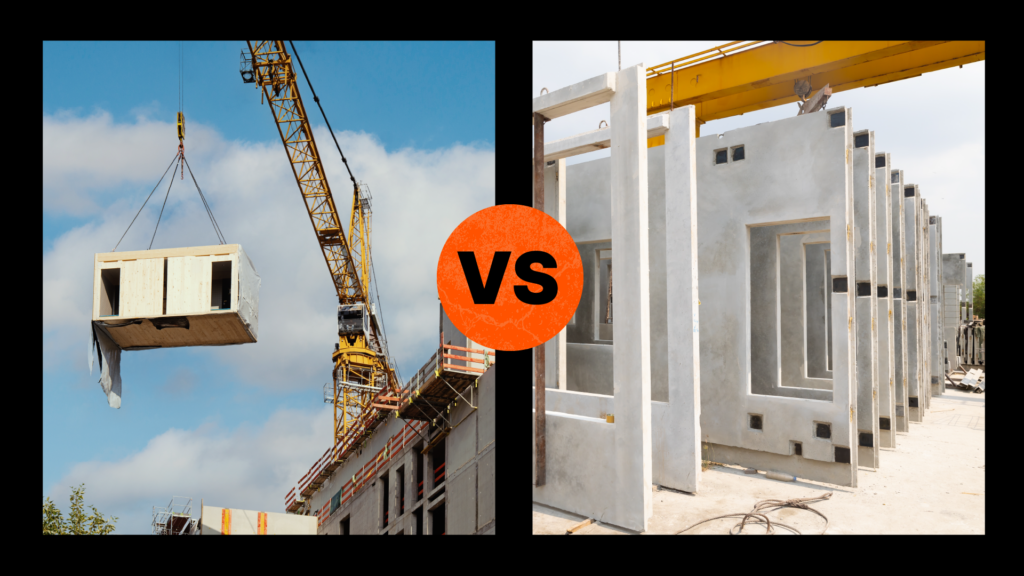
Off-Site Construction: Prefab vs. Modular
As the construction world becomes ever more competitive, deadlines get tighter and the margin for error gets slimmer, project owners around the world are always looking for an edge. Thanks...
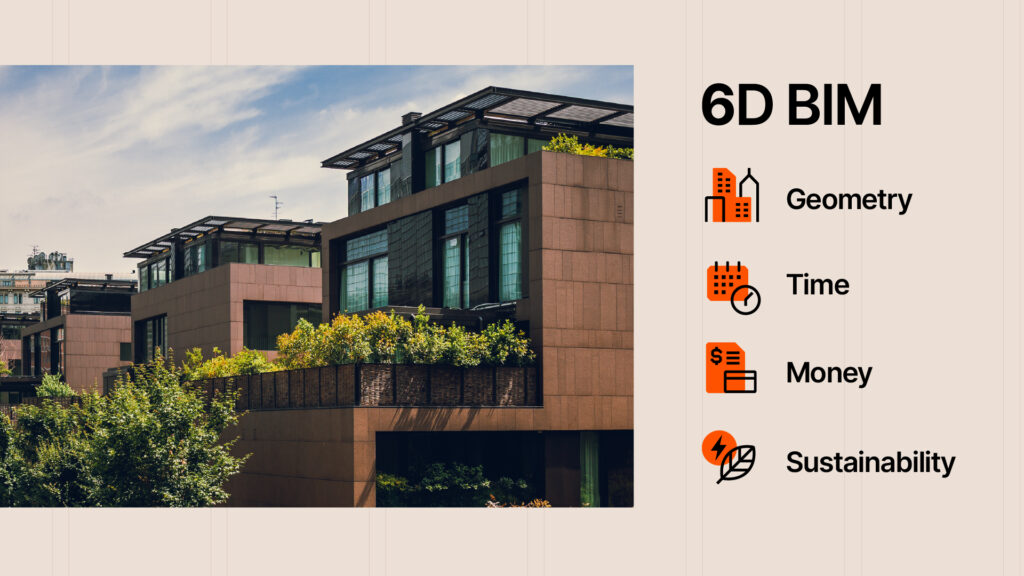
The Role of BIM in Sustainable Construction
Building information modeling (BIM) is transforming the architecture, engineering, and construction (AEC) industry. With this kind of sophisticated modeling, the industry has shifted from designing in 2D to 3D. This helps...
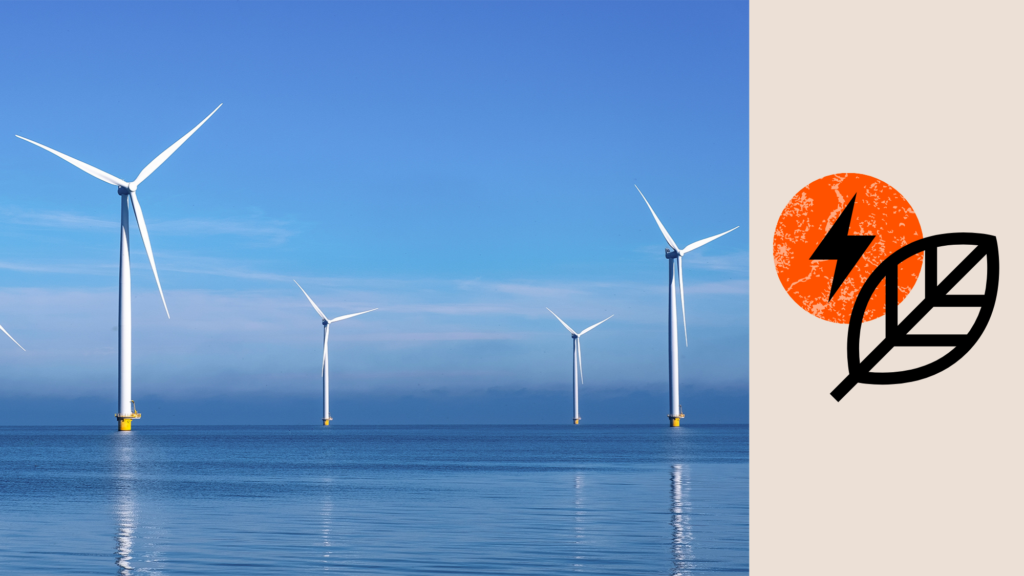
Harnessing Energy: Advancements in Offshore Wind Farm Construction
Offshore wind farms harness the potential of oceanic wind resources, providing a reliable and eco-friendly power source. As energy demand continues to escalate worldwide, these vast installations offer construction professionals...
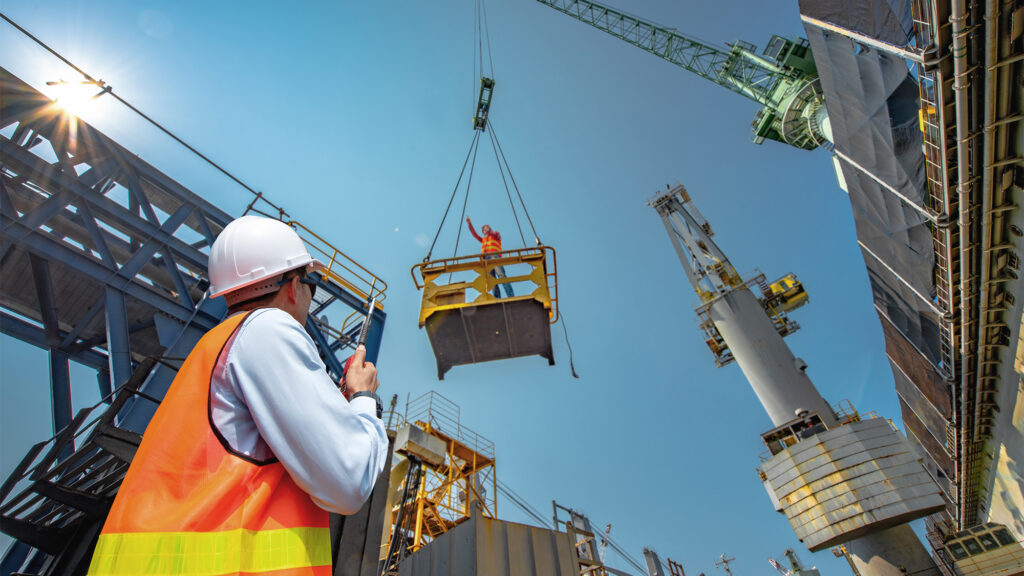
Using AI to Manage Risk in Construction
Since the day construction became an industry, many people have been trying to manage the risks of building things — to identify and mitigate potential conditions that might impact a project’s...