— 4 min read
Using a Rough-in Inspection Checklist (Guide & Free Download)
Last Updated Sep 24, 2024
Last Updated Sep 24, 2024
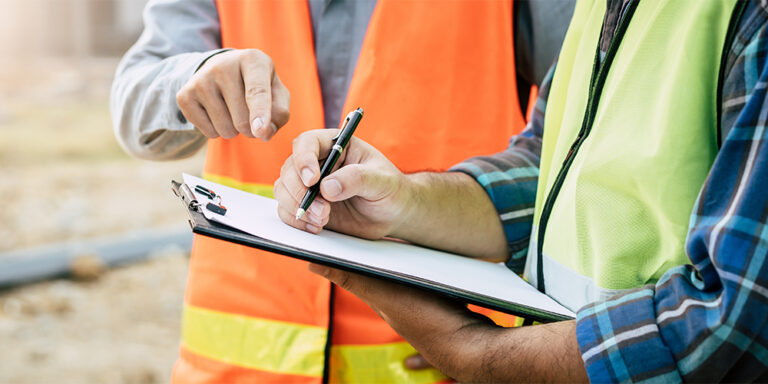
One of the most common significant milestones in a construction project is the rough-in inspection. Rough-ins are the formal checks of important systems — such as electrical, plumbing and HVAC — that occur after they have been installed but before they have been enclosed by walls and ceilings. Preparing for rough-in inspections requires consistency, organization and attention to detail, which is why a reliable checklist is such a valuable tool.
This article focuses on rough-in inspections — their value, what they should include, best practices and a free downloadable checklist.
Table of contents
The Importance of a Rough-in Inspection Checklist
Rough-in inspections are meant to catch issues before they are closed in by a wall or ceiling and become more difficult and costly to address. Rough-ins are commonly required to close work permits and passing them is sometimes connected to contractors receiving payment. An inspector that discovers a major issue can fail that room, area or building and another rough-in will need to be scheduled.
A checklist can serve as a comprehensive, standardized guide to quality control across different projects, areas and teams. Checklists provide clear criteria for each component to ensure it meets regulatory standards and project specifications. They further save time by having the ability to be reused or slightly altered for different projects, rooms or areas.
Checklists transform the process of preparing for rough-ins from a potentially chaotic, research-heavy and error-prone task into a controlled, efficient and replicable procedure. This helps avoid costly rework or delays, while also improving communication, collaboration and accountability between stakeholders.
Free Download
Rough-in Inspection Checklist
This checklist comes with several of the most common fields in a construction rough-in inspection, and can be downloaded and customized to suit any project.
- Free customizable checklist
- Ready-to-use — make a copy in Google or download as a PDF
- Trusted by construction professionals
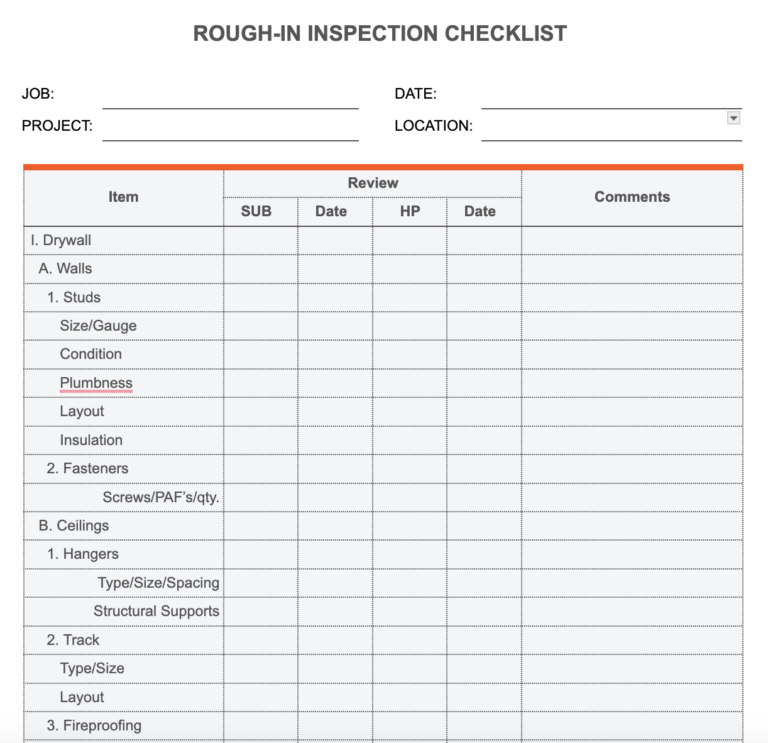
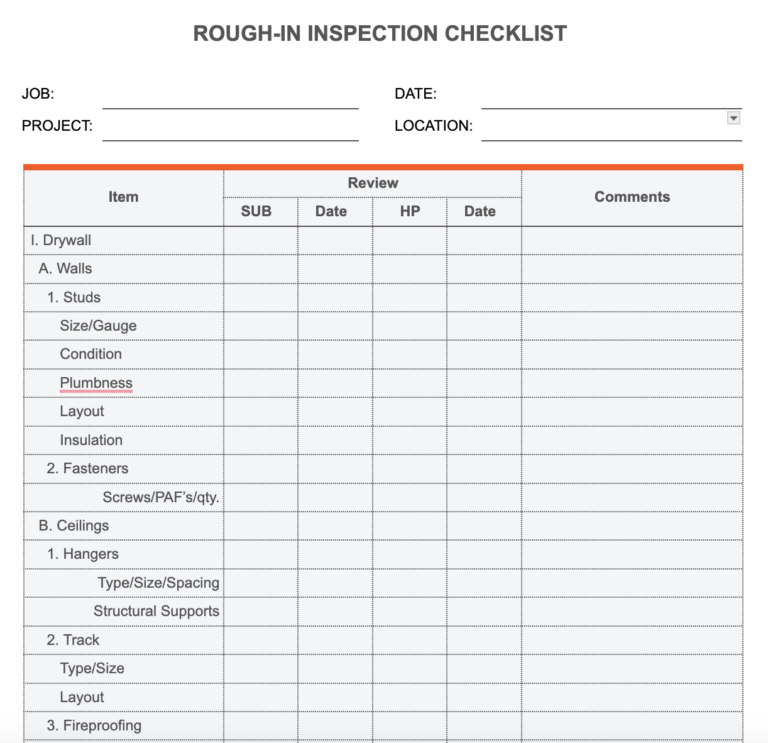
Information to Capture on a Rough-in Inspection Checklist
While rough-in checklists can vary depending on the type of project and local building and safety requirements, they tend to include checks of the following components:
Electrical
- Wiring, including type and gauge
- Boxes and panels, including configuration, securing methods and placement
- Conduits, including sleeves, penetrations, mounting and routing
- Code compliance
Plumbing
- Pipes and joints, including location, elevation, pitch and sizes, as well as sealing to prevent leaks and the placement and stability of sleeves, penetrations and anchors.
- Venting, including installation methods and locations
- Testing for leaks and functionality
- Code compliance
Mechanical
- Ductwork, including placement and sealing
- HVAC equipment, specifically placement, installation and testing to ensure functionality
Insulation
- Placement, quality and efficacy for insulation of piping and ductwork
Fire safety
- Sprinkler systems, including head location
- Adherence of all systems to fire safety regulations
- Testing to ensure systems are leak-free and operational
How to Implement a Rough-in Inspection Checklist
To make sure a checklist will be helpful and improve project outcome, there are a few steps to follow before, during and after the inspection.
Before the Inspection
- Sharing the checklist: Ensure trade partners understand how their work will be inspected and evaluated before they ever begin.
- Numerous quality control checks: Include a space for the trade partner to check and sign off their work, as well as a space for the general contractor (GC) to conduct a final check.
- Documentation: Include detailed documentation, including photos and labels. This helps if the inspector has questions, but can also be included as part of the closeout documents.
During the Inspection
- Trade partners attendance: Have trade partners present at the inspection to address any minor issues immediately.
- Communication: Maintain clear and open lines of communication with the inspector to clarify and resolve any issues as quickly and as thoroughly as possible
After the Inspection
- Documentation: Document all inspection results, any corrections and unexpected questions or concerns that popped up.
- Addressing issues: Handle minor issues on the spot; for significant issues, address and schedule a re-inspection.
- Improving the checklist: Add, edit or clarify any steps that might’ve helped better prepare for the inspection, so they can be included in the future.
Courses about construction.
For construction.
Unlock your career potential with our free educational courses on Health & Safety, Data in Construction, and more.
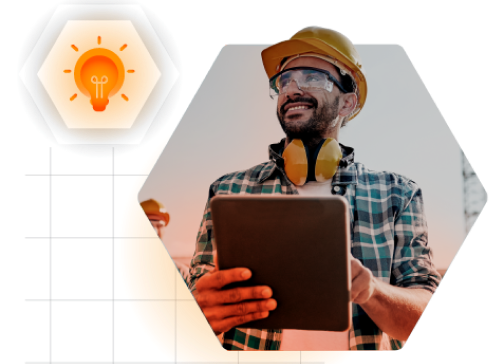
Maximizing a Rough-in Inspection Checklist
Checklists should help mitigate risks and ensure compliance while also maintaining project timelines and improving communication. However, reaping these benefits requires some deliberate effort from the GC overseeing the process.
First, there is the question of consistency. Checklists require the buy-in and diligent adherence to a process over time to ensure no critical steps are missed. This also helps improve the components over time. Without consistency, checklists become just another document floating around.
Checklists also require extensive documentation, which can be made easier by adopting digital and mobile tools, such as Procore, that can help make submittals and closeout documents easier to share, store and access.
However, perhaps the biggest key to implementing an effective checklist is collaboration. Involving trade partners early in the process, welcoming input on how to improve the list’s procedure and comprehensiveness and providing clear expectations can go a long way to improve project outcomes.
Was this article helpful?
Thank you for your submission.
0%
0%
You voted that this article was . Was this a mistake? If so, change your vote here.
Scroll less, learn more about construction.
Subscribe to The Blueprint, Procore’s construction newsletter, to get content from industry experts delivered straight to your inbox.
By clicking this button, you agree to our Privacy Notice and Terms of Service.
Categories:
Tags:
Written by
Ryan Nash
Ryan Nash is a Field Team Leader at RNGD, delivering safe, efficient, and quality commercial construction projects in greater Nashville. Since he joined the company as Superintendent, he has successfully delivered multiple $100M+ projects on schedule and within budget. Throughout his 10+ years in the industry, he has developed a cost-saving mindset, expertise in navigating complex challenges, and commitment to a safety-first construction site. Ryan holds a Bachelor of Science degree in construction management from Southeast Missouri State University. He lives in Nashville.
View profileJames Hamilton
70 articles
James Hamilton is a writer based in Brooklyn, New York with experience in television, documentaries, journalism, comedy, and podcasts. His work has been featured on VICE TV and on The Moth. James was a writer and narrator for the show, VICE News Tonight, where he won an Emmy Award and was nominated for a Peabody Award.
View profileExplore more helpful resources
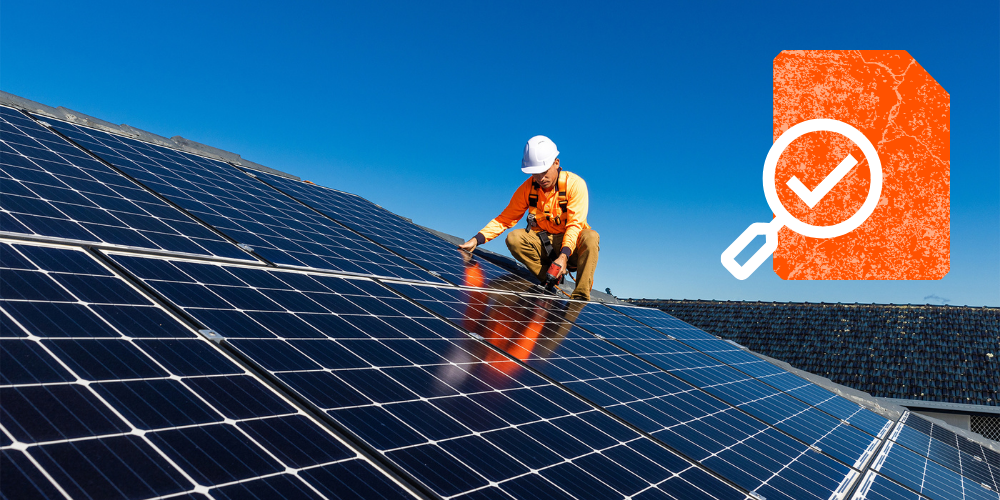
Optimizing Solar Inspections: A Construction Pro’s Guide
As solar power becomes more prevalent in both residential and commercial projects, construction contractors and project owners will need to become more familiar with solar installation projects. Solar inspections —...

The Ultimate Guide to Managing Commercial Construction Inspections
Commercial construction projects require ongoing inspections at almost every point of the building process, from checking the site before construction to the final inspection with a local building authority. Understanding...

The Contractor’s Guide to Concrete Inspections
Concrete: It’s the key building block of nearly every structure’s foundation — and it’s the world’s most widely used building material. For most general contractors, understanding how to assess concrete...
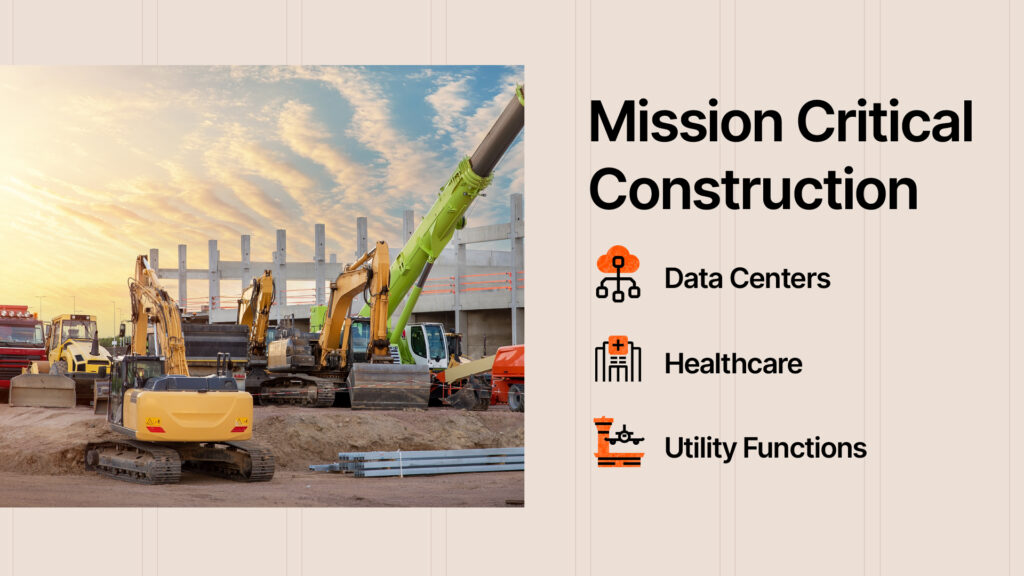
Mission Critical Construction: Strategies for Success
Mission critical construction involves building structures whose functions cannot afford to fail, as any disruptions can lead to significant consequences for society. Keeping data centers, hospitals, power plants and other...