— 8 min read
Rough-in Inspections: Key Steps and What to Expect
Last Updated Sep 24, 2024
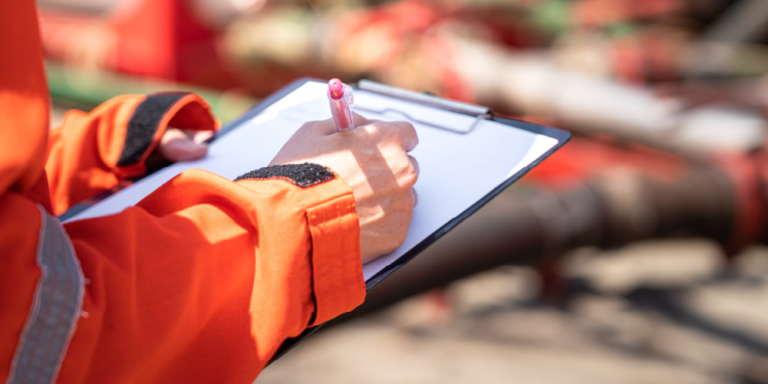
The commercial construction process includes a variety of routine and formal inspections to ensure every element is safe for use, up to code and constructed properly. However, some inspections are higher stakes than others, specifically those required for work permits or those that represent the end of a phase of construction.
Rough-in inspections are formal checks of important systems, such as MEP or fire safety, that occur after system installation but before the construction of finishing touches. Most rough-ins are conducted before the construction of walls or ceilings, so crucial system components, such as electrical boxes, water lines or air ducts, are easy to access for inspection and, if necessary, for addressing issues.
This article explores rough-in inspections, including how to prepare for them, what to expect and best practices.
Table of contents
The Basics of Rough-in Inspections
Rough-in inspections, or rough-ins, ensure components of important systems are up to code and safe to use, but they often also represent significant project milestones. Rough-ins are often required to close work permits and passing them is sometimes connected to contractors being able to receive payment. Rough-ins are usually conducted by the authority having jurisdiction (AHJ) or a third-party inspector.
In most cases, a municipality comes to conduct a rough-on after a room or area has been framed, important systems have been installed and numerous routine quality checks have been conducted. Some places, like Florence, Oregon, provide a list of required rough-in inspections with a description of when they should be conducted.
Rough-ins are meant to catch issues before they are closed in by a wall or ceiling and become more difficult and costly to address. Verifying systems have been installed correctly also helps to avoid potentially devastating issues, such as electrical fires, leaks or structural concerns.
Rough-ins are similar for most projects, regardless of the type of construction. Some projects have specialized systems that require rough-ins, such as medical gas hookups at a hospital or pipes storing hazardous chemicals at a power plant.
How to Prepare for Rough-in Inspections
It’s important to thoroughly prepare for rough-ins, as failing requires scheduling another inspection with the AHJ and can create additional costs and delays.
Thoroughly inspect before the rough-in.
Subcontractors and the general contractor (GC) should be checking work routinely and should both do formal checks and tests after installation and before the municipality is scheduled to come. Most trade partners formally evaluate their work after finishing, which is followed by another thorough check by the GC. By the time the rough-in actually happens, most issues should be identified and resolved and the AHJ should be mostly checking boxes as opposed to discovering new things. Some inspectors prefer to witness system tests, such as turning on electricity or running water to check for leaks. It’s still a good idea to run those tests before the rough-in to avoid surprises and catch any issues.
Include rough-ins in project planning.
Planning a rough-in can be complicated, as it often requires coordinating with numerous trades, must be completed before beginning dependent tasks and involves scheduling with an AHJ. Building rough-ins into the planning process as early as possible can help avoid delays or, if a delay does occur, help inform how it will impact a project’s critical path. Many planning methods, such as pull planning or work breakdown structure (WBS), use rough-ins as a milestone to help with planning and completing phases of a project.
Segment work.
Most projects require numerous subcontractors working on different tasks at the same time in order for a project to be completed on time. Projects might be segmented and numerous rough-ins might occur so that construction on the rest of the project can continue. For example, a hotel might be divided into floors or rooms and rough-ins might be done in each area. This ensures drywall work can begin in one area while systems are being installed in another. Effectively segmenting and sequencing is made possible with planning techniques, such as WBS, and by getting input from trade partners.
Get organized.
Many systems must be installed and inspected in each area, often around the same time. Many GCs gather all trade partners to create a plan for sequencing tasks in an area and then establish a clear procedure for marking what systems have been installed. This helps ensure nothing is missed and reduces miscommunication.
Many procedures start with sequencing. For example, a team might decide that the order of installation will be low voltage cabling followed by plumbing, electrical and HVAC controls. The GC might assign each trade a color and have them paint a stud their respective color each time they’ve finished work in an area. This signifies to the next trade that their work can begin.
For example, the subcontractor working on the low-voltage cabling might paint a stud pink when they’re done. This would cue the plumbing team that they can begin. Once plumbing is done, they might paint the stud green. This cues the HVAC team to begin, and so on.
Get better organized with this free Rough-in Inspection Checklist.
What to Expect During Rough-in Inspections
It’s important to have an understanding of what will be inspected at the rough-in. This helps to prepare, improves the quality of work and expedites the inspection process. Some places, like Merrimack, New Hampshire, will have a list on their website of everything that needs to be inspected.
Inspectors are usually responsible for evaluating whether things are up to code and comply with local regulations, so they often focus on ensuring elements are the correct size, are functioning and safely connect to the rest of the system. They usually don’t assess the specifics of the building plans, such as measuring an element’s placement. For example, they might check that the right wires are in the wall and that they’re safely installed, but not measure the placement of an outlet.
Commonly, rough-in inspections are required for the following elements:
- Electrical, including wiring, boxes, routing, mounts, service panels and meters
- Plumbing, including pipes, joints, routing, fasteners, venting and insulation
- Mechanical, including ductwork, HVAC equipment and HVAC controls
- Framing, including studs, fasteners, material quality, load paths, headers and egress
- Fire safety, including insulation, placement of components, fire blocking and running tests on emergency systems
Despite all the prep, inspectors still sometimes find issues that need to be addressed. If possible, minor issues will be addressed immediately so they can be checked while the inspector is still onsite. For major issues, the inspector will fail that room, area, or building — and another rough-in will need to be scheduled.
Best Practices for Rough-in Inspections
There are few things that can help make rough-in inspections more efficient and maximize their utility.
Collaborate.
Rough-ins are often important project milestones that require regular communication and collaboration between builders, contractors and owners. GCs should work to ensure everyone has a shared understanding of timelines, project requirements, safety measures and processes.
Trade partners have extraordinary expertise which can provide valuable insight into how long tasks should take, potential challenges and codes and regulations. Holding kickoff and OAC (owner, architect and contractor) meetings can help open lines of communication, keep the project on schedule and resolve issues as they occur.
Document everything.
The rough-in is often the last time some components will be accessible before being closed in by a wall or ceiling. GCs should thoroughly document all elements through photographs and videos. Documentation will be referenced during the final walk-through with the owner, the final inspection for the certificate of occupancy and will be included in closeout documents. Photographs can be quick ways to show work was completed effectively and safely without having to remove a section of a wall or ceiling, which would create delays and additional costs. Owners also often reference documentation in the future to locate important systems when doing maintenance or renovations.
Have trade partners on hand for the inspection.
Some GCs have trade partners attend the rough-in so they can be on hand to address minor issues. Minor issues can often be resolved while the inspector is still on site, which can help avoid failing the inspection and needing to schedule another.
Manage relationships with inspectors.
In many places, a few inspectors handle hundreds of requests, so it’s important to respect their time. Not every inspector wants to be buddies, but nothing good comes from a relationship that’s negative, contentious or distrustful. Positive relationships can help navigate uncertain issues that arise.
Technology and Tools to Help With Rough-ins
Rough-ins require an immense amount of planning, coordination and documentation. Many GCs use software to store and organize documents and photos, including those collected during and leading up to rough-ins. They also use project management tools to track inspections and to build and share plans, drawings and schedules. Finding tools to streamline those processes and create effective workflows can make rough-ins smoother, but also serve other parts of the project such as invoicing and closeout.
Was this article helpful?
Thank you for your submission.
100%
0%
You voted that this article was . Was this a mistake? If so, change your vote here.
Scroll less, learn more about construction.
Subscribe to The Blueprint, Procore’s construction newsletter, to get content from industry experts delivered straight to your inbox.
By clicking this button, you agree to our Privacy Notice and Terms of Service.
Categories:
Tags:
Written by
Ryan Nash
Ryan Nash is a Field Team Leader at RNGD, delivering safe, efficient, and quality commercial construction projects in greater Nashville. Since he joined the company as Superintendent, he has successfully delivered multiple $100M+ projects on schedule and within budget. Throughout his 10+ years in the industry, he has developed a cost-saving mindset, expertise in navigating complex challenges, and commitment to a safety-first construction site. Ryan holds a Bachelor of Science degree in construction management from Southeast Missouri State University. He lives in Nashville.
View profileJames Hamilton
71 articles
James Hamilton is a writer based in Brooklyn, New York with experience in television, documentaries, journalism, comedy, and podcasts. His work has been featured on VICE TV and on The Moth. James was a writer and narrator for the show, VICE News Tonight, where he won an Emmy Award and was nominated for a Peabody Award.
View profileExplore more helpful resources
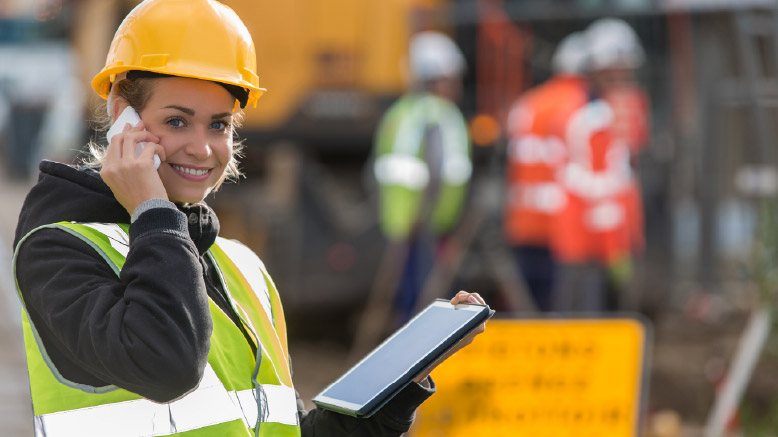
Construction Communication in the Digital Age: Pain Points and Opportunities for GCs
Construction professionals report that projects are moving faster than ever before. Demanding schedules aren’t the only thing that introduces speed, though. Information often changes quickly on projects. In fact, some...

A Fine Line: Balancing Standardized Construction Processes With Specific Project Needs
When it comes to the construction process, some general contractor (GC) firms formally adopt a mentality of continuous improvement. But even among those that don’t, construction teams know that getting...
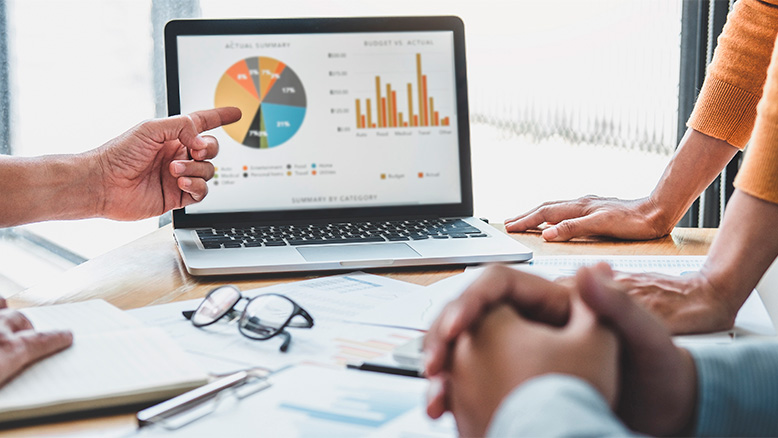
Construction Forecasting Beyond Financials: The Owner’s Guide
Just because a project is large in size, scope or social importance does not mean it will have infinite flexibility and budget. Projects can’t just change their offered service or...
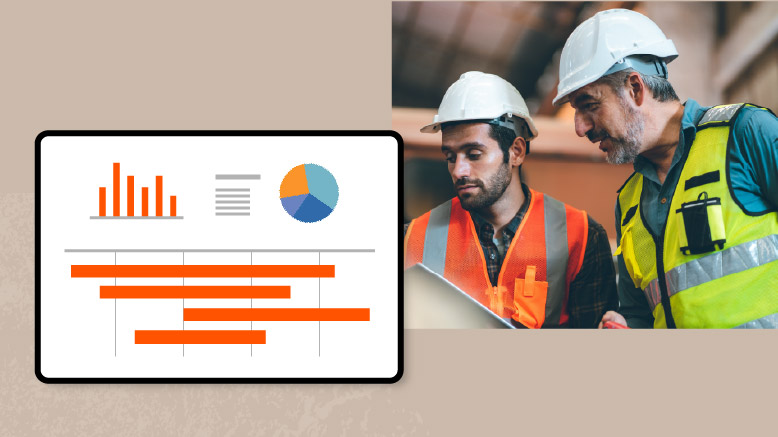
Using Data to Track Subcontractors’ Progress: 5 Keys to Success
Data gives general contractors powerful insights into the progress that subcontractors are — or aren’t —making toward project deadlines. However, the best data isn’t simply there for the taking. Optimizing...
Free Tools
Calculators
Use our calculators to estimate the cost of construction materials for your next project.
Templates
Find a template to help you with your construction project tasks.
Material Price Tracker
Get the latest U.S. retail prices and view historical trends for common building materials.
Glossary
Explore key terms and phrases used in the industry.