— 10 min read
Solar Construction: Insights From Preconstruction to Activation
Last Updated Jun 11, 2024

Sustainable energy is the future, with technologies like electric vehicles, wind farms and biofuels revolutionizing the market. Among these, solar energy emerges as a particularly lucrative and innovative field — one that stands apart from other construction opportunities.
Solar construction stands out for its labor dynamics: It demands skilled labor for preparation and maintenance, yet the actual installation process is far less specialized. Crews could be working screwing in the same bolt 44,000 times, needing much less specialization and training than typical vertical construction.
Additionally, even the most minimal efficiency gains in these tasks can lead to significant time and cost savings, positively impacting a general contractor's profit margins — and the environment.
This article will break down the costs, benefits and common challenges of solar plant construction.
Table of contents
Basics of Solar Energy
There are two main types of solar plants: thermal and photovoltaic. Thermal plants use heat from the sun’s rays to create electricity — on some, mirrors are directed at a single point that collects the heat energy and then transforms it into electricity. On others, panels focus the light down into vats of water which heat up and create power like a boiler.
The other more common type of solar plants use photovoltaic (PV) technologies, and those are the ones you’re most likely to see along the side of the road. Panels take in the UV rays and convert them into an electrical current that can be transformed into DC power.
On solar plants, jobs are quantified by the megawatts of energy they’re going to produce. For scale: a medium-sized project might be about two miles of solar panels, generating around 30 megawatts of electricity; a large-scale project could be 15 miles of panels generating 180 megawatts.
Benefits of Solar Construction
Solar construction varies from traditional vertical construction in many different ways, but for general contractors, one of the main differences is in contracts. Typically working on a vertical build, GCs will be agreeing to a guaranteed maximum price or a cost plus model. However, on solar construction projects, general contractors sometimes opt for lump sum contracts.
A contractor may say that they'll build a 180-megawatt plant for $180 million. But anything they don’t use of that $180 million, they can keep. The lump sum contract already has a fee built-in and allows contractors to make a substantial profit by increasing efficiency during the actual project.
While the higher fee could give some owners sticker shock, the work of a general contractor on a solar plant site is highly specialized. Workers are dealing with highly technical panels, building transformers and dealing with electricity.
On the back end, companies building solar farms typically agree to manage operation and maintenance for anywhere from 10 to 15 years. This means monitoring solar panels to ensure continued functionality and making sure plants produce the correct amount of power for their entire lifespan. If anything does happen to go wrong, the company will send their own workers to replace or fix problems.
All of these factors make solar construction an extremely lucrative opportunity for general contractors.
Learn more about other types of construction infrastructure projects.
Preconstruction
Interconnect Agreement
Before starting a project, owners will need to have an interconnect agreement. This document is put together in conjunction with local utility companies, promising the plant can produce an average amount of power and that the area’s infrastructure is capable of accepting the energy.
Sometimes during this process, it becomes clear that state and local power grids are not going to be able to handle the wattage of the plant, typically because the location is so remote that there simply isn’t enough existing infrastructure.
In these cases, owners can opt to build entire substations on the property — including high-voltage transformers running high-voltage transmission lines — to handle the newfound electrical demands. Or they can build batteries that contain excess energy which grids can draw off during cloudy or dark days when the panels aren’t producing as much power. This work can be incredibly lucrative to a general contractor, but the big price tag might wave off some owners. Because of this, some people decide to have an interconnect agreement in the works before even finalizing the purchase of land.
Along with ensuring the power grid is able to handle energy from a new solar plant, an interconnect agreement will also lay out the amount of energy a plant is expected to produce and the price the utility company is willing to pay for it.
An agreement may lay out that a 180-megawatt plant is guaranteed to produce 170 megawatts per day — building in some wiggle room for the inevitable broken panel or day-to-day inefficiencies. The utility company will then use this information to make their own internal plans: knowing a plant is going to be able to provide a certain amount of power allows them to ramp down their own production so the grid doesn’t become overloaded.
Once the plant is running, any massive shutdowns or major problems are going to have ripple effects for real people counting on that power for their homes and businesses.
Location Scouting and Preparation
Finding the proper location to build solar plants is critical. An ideal location provides the solar panels with full days of unobstructed exposure to the sky — the sun is obviously the largest power generator, but PV panels can also create energy from lunar light. This means avoiding hills that hide the sun in the morning or evening, and locations with vegetation that will grow quickly and shade the panels.
As much as it might be counterintuitive, it’s also important to avoid locations that become too hot during periods of the year. Solar panels can overheat and start to malfunction. This is why states like California – bountifully sunny but not overwhelmingly hot — host most solar plants.
After owners procure the land, many computer programs can map plots, determine the shape and create layouts of how to fit the most solar panels on that plot. They can take into account things like angle of the sun and potential tree cover to optimize the layout in just a few minutes.
Monitoring & Safety on Solar Plants
While solar plant construction isn’t as technically complicated as some vertical construction projects, it does involve some extremely heavy civil engineering. Workers are grading a lot of land, scraping the surface and putting posts into the ground for tracking systems — which can have substantial environmental impacts.
Contractors and owners have to coordinate with state and local officials to make sure that workers are not causing any substantial damage or running afoul of environmental protection. These can be as obvious as checking for the nests of endangered animals or as finicky as not being able to build during conditions that draw out protected micro-organisms.
Additionally, you’ll most likely need to coordinate with local Native communities. Testing needs to be done to ensure you’re not inadvertently disturbing burial grounds and local monitors can ensure that you stay away from any protected or sacred land. Make sure that in any budget you factor in the cost of both Native and biological monitors onsite, especially in the earliest stages of construction.
Working with electricity is always risky if not handled correctly, and can be an even bigger problem when you're dealing with wide open areas where any problem may not be fixed fast enough to avoid a catastrophe. PV panels produce DC power, which is much more unstable than the AC power used in homes and businesses. Electricians obviously know about DC power, but they don’t typically touch it. Because of this, you’ll need to ensure there are robust lockout/tagout procedures in place on the plant.
Finally, unlike vertical construction in a more urban area, solar plant sites typically lack any kind of shelter for workers to rest. GCs will want to erect tents or build temporary shelters to allow workers to get out of the sun and wind during breaks. Failing to do this could lead to health problems for workers.
Stay updated on what’s happening in construction.
Subscribe to Blueprint, Procore’s free construction newsletter, to get content from industry experts delivered straight to your inbox.
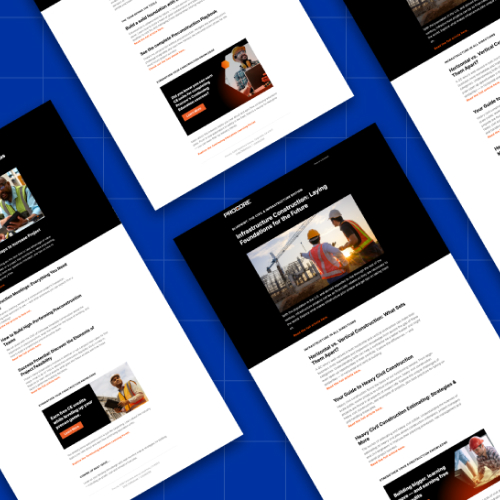
Construction
The beginning of your construction is going to require the most skilled labor of the whole project. If the land you’re building on has a substantial amount of rolling or undulating, you’ll need to be prepared to grade the land to make it more suitable for the panels.
Installing Electrical Wire
Once this process is started, electrical experts will start installing wire. These not only send the power from the panels to transformers, they’ll power the plant’s tracker systems — computers that track the sun and pivot the panels towards the light. While some owners may opt not to have trackers, it can dramatically increase plant productivity.
Panel Installation
After wiring is in place, the panels are installed. Racks hold the panels up off the ground and are held in by steel I-beams. That means using pile drivers to pound hundreds of thousands, if not millions, of beams into the ground. This is where a smart general contractor can save time and make money.
For example, say a contractor sets budget and estimates it will take about 90 seconds of labor to put a million piles in the ground. If you can get those piles in the ground in 75 seconds, you’re saving 15 seconds per pile times a million. That’s a lot of labor and equipment hours that you’re saving, which all goes back into your pocket.
The installation of the actual panels then is sort of like putting together furniture. It’s not hard, but can be tedious. Thousands of panels require tens of thousands of parts that need to be installed one at a time. Large jobs might employ a maximum crew of between 800 and 1,000 people, many of whom are not skilled construction workers.
Because of this, though, there can be a high risk for injury. Most workers aren’t people who have spent a ton of time on job sites and are familiar with construction best practices. Larger general contractors may choose to have a core team of skilled managers who travel from job site to job site, monitoring and making sure everyone is safe.
The panels themselves are fragile and require care when transporting and installing. Owners may want to purchase the panels directly from manufacturers and pay the cost of shipping them to the job site themselves.
However, this is another area for a skilled GC to take over and be able to make a profit. Agreeing to incur the price of any panel broken during transit allows the GC to make a profit in the end (if they’re careful).
Permission to Operate
Once the panels are in, the tracking system is up and running and every screw and bolt are securely installed, you have to return to your interconnect agreement.
Each interconnect agreement includes a section called “permission to operate.” This stipulates that before you can flip the switch on the new plant, workers from the electrical utility company must make one final inspection. They’ll ensure that everything has been safely installed, is producing the amount of energy you have guaranteed and won’t either overload the grid or leave it lacking.
Successfully Completing Solar Construction
The key to building solar plants is to take care throughout the process. Because of its repetitive nature, solar construction can seem monotonous. But every piece requires attention — delicate panels need to be handled with care, screws need to be tightened so high winds don’t blow the plant apart and wiring needs to be checked and triple-checked to avoid catastrophe. Keeping these factors in mind, smart, detail-oriented general contractors can take massive advantage of this booming industry.
Was this article helpful?
Thank you for your submission.
50%
50%
You voted that this article was . Was this a mistake? If so, change your vote here.
Scroll less, learn more about construction.
Subscribe to The Blueprint, Procore’s construction newsletter, to get content from industry experts delivered straight to your inbox.
By clicking this button, you agree to our Privacy Notice and Terms of Service.
Categories:
Tags:
Written by
Rachael Ceciliani
Rachael is a Strategic Product Consultant for Procore who has been in the construction industry since 2013, spending 8+ years with McCarthy Building Companies and growing her expertise as a construction project manager.
View profileCait Bladt
13 articles
Cait Bladt is a multi-award winning freelance writer and producer. Her work has appeared at Vice, ABC News and Rolling Stone among others. She currently lives in Brooklyn with her cat Patricia.
View profileExplore more helpful resources
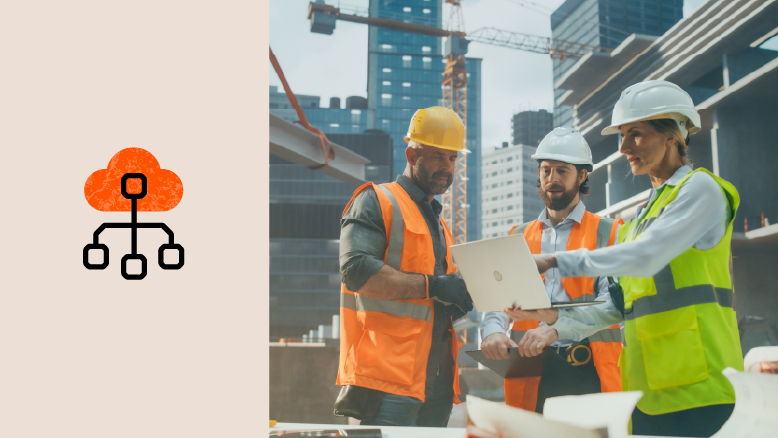
Guide to the Common Data Environment (CDE) & BIM
BIM isn’t just a 3D model. As its full name — building information modeling — suggests, BIM encompasses processes, too. It’s a wide-ranging digital effort designed to drive wins on the...
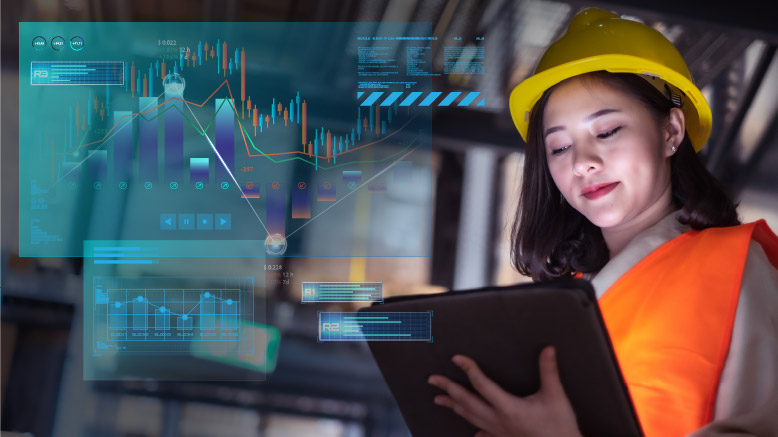
The Human-AI Partnership: Cultivating a Future-Ready Workforce in Civil Construction
The civil construction industry is at a crossroads, poised between traditional methodologies and a technologically advanced future. As projects grow in scale and complexity, the integration of artificial intelligence (AI)...
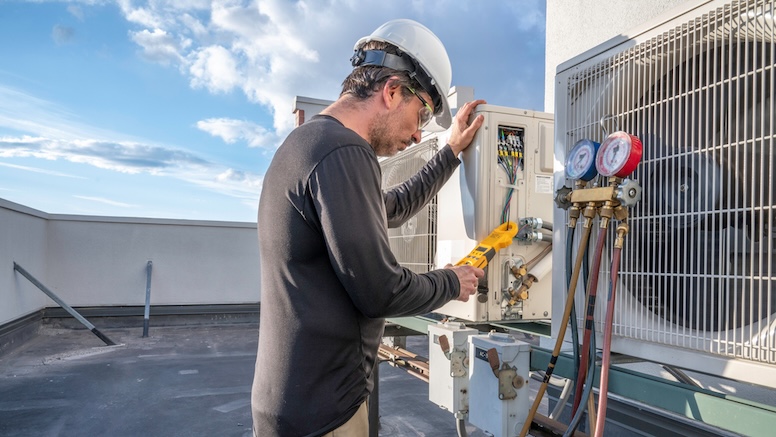
Inside Ductless HVAC Systems
As construction projects grow in size and complexity, ductless HVAC systems are gaining traction. In a world demanding customizable solutions and sustainability, ductless HVAC is flexible and energy efficient. HVAC...
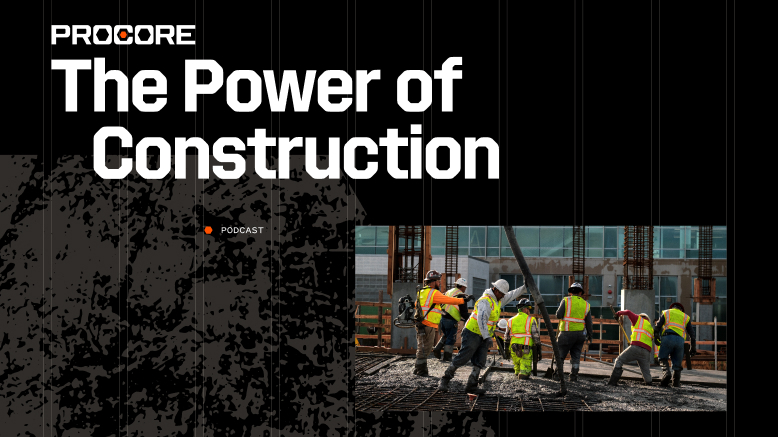
How Can We Bridge the Data Gap in Construction?
In Episode 3 of The Power of Construction, Eric Whobrey, ARCO Murray’s VP of Innovation and Managing Partner joins hosts Sasha Reed and Kris Lengieza to explore the data gap...
Free Tools
Calculators
Use our calculators to estimate the cost of construction materials for your next project.
Templates
Find a template to help you with your construction project tasks.
Material Price Tracker
Get the latest U.S. retail prices and view historical trends for common building materials.
Glossary
Explore key terms and phrases used in the industry.