— 11 min read
9 Tips for Effective Subcontractor Management
Last Updated Sep 1, 2024
Last Updated Sep 1, 2024

Subcontractor management, the overseeing, supervision and coordination of subcontractors, profoundly impacts the overall success of a construction project. This integral piece is usually shouldered by the general contractor, constituting a substantial component of their responsibilities throughout the construction process.
Effective subcontractor management aligns efforts of various disciplines on a construction project and ensures all trades work cohesively, meet project goals and contribute positively to the overall success of the project.
In this article, we will explore nine key practices for managing subcontractors efficiently in order to achieve the best possible results.
Table of contents
1. Choose subcontractor partners that are the best fit.
Subcontractors assume a critical role in executing specialized scopes of work, and their performance ripples through project quality, timelines and overall outcomes. Ensuring that the right subcontractor partner is selected lays the groundwork for a well-executed project.
GCs commonly curate a list of pre-qualified specialty contractors to choose from. In the prequalification stage, the general contractor evaluates the specialty contractors, considering criteria such as their past performance, safety ratings, experience, references and financial stability.
When selecting subcontractors, it’s important for GCs to align their choices with the goals of the project.
For example, the specifications for a healthcare project will set stringent requirements for infection control, air quality and patient safety. The general contractor should prioritize hiring HVAC subcontractors with a proven track record of successfully delivering work within healthcare facilities.
These subcontractors should have experience installing mechanical building systems that adhere to these required high-quality air standards. Dedicating time and effort to choosing subcontractor partners known for their reliability, capabilities, and compatibility can result in more efficient project execution. This helps decrease the possibility of rework, improve project results, and increase the project owner's satisfaction.
Another key piece of the tendering process is soliciting a minimum of three bids per trade. Obtaining multiple bids fosters a competitive environment among potential subcontractors, encourages bidders to submit their most competitive and cost-effective proposals – and ensures that the GC has a comprehensive view of all of the available options.
Competitive bidding also gives the GC the opportunity to evaluate and compare different approaches, costs and timelines proposed by various subcontractors. This is essential for selecting the most qualified and cost-effective subcontractors that align with the overall goals and requirements of the project. Having multiple bids aids the general contractor to make informed decisions, mitigate risks and negotiate favorable contract terms.
2. Set clear expectations.
Contract negotiation is the first step in setting expectations. The terms set in the contract define the expectations, responsibilities and deliverables for both the general contractor and subcontractors.
During contract negotiations, clear outlines regarding payment terms, project milestones, scope adjustments and dispute resolution mechanisms are established. This helps avoid future misunderstandings and potential conflicts during the project execution phase. Contract negotiation also helps establish the foundation for a productive and successful collaboration between GCs and subcontractors.
Subcontractors must have a precise understanding of how their role fits into achieving the project's scope and goals. Clear definitions help prevent misunderstandings, reduce the likelihood of scope creep and ensure that subcontractors contribute effectively to the project's success.
Establishing clear communication channels between the general contractor and the subcontractor ensures that information flows seamlessly. It is imperative for general contractors to keep subcontractors in the loop, providing timely updates on any project developments, changes and expectations. This proactive approach enhances responsiveness, facilitates prompt issue resolution and nurtures a cohesive working relationship.
While establishing clear expectations typically takes place at the beginning of the project, in subcontractor management, there may be instances where it becomes necessary to revisit and reaffirm these expectations as the project progresses.
Establish a positive jobsite culture.
A crucial facet of this process involves cultivating a positive jobsite culture and a strong safety culture, both of which are fundamentally driven by effective leadership. Because jobsite safety and relations can erode quickly and difficult to restore, implementing a positive work culture right away is critical. Creating a positive jobsite environment involves a culture of collaboration and mutual respect. By embracing a "one-team philosophy," the focus shifts from individual roles and responsibilities to a collective commitment to project success.
This approach involves breaking down silos between different subcontractors and between subcontractors and the GC. When everyone on the jobsite feels valued and recognized as an integral part of the larger team, ideas are shared, problems are addressed collectively and successes are celebrated together.
The synergy between the GC and subcontractors is crucial for maintaining a collaborative and productive working relationship. Effective communication, shared goals and a mutual understanding of project objectives foster an environment where challenges are addressed promptly, and solutions are implemented.
3. Identify, assess and manage potential risks.
In subcontractor management, identifying potential risks and challenges is a proactive step in ensuring project success. Risks may include delays, quality issues, safety concerns or unforeseen obstacles related to subcontractor performance.
The initial phase of risk management in subcontractor management occurs during the bidding process, emphasizing the importance of selecting the correct partner. While a single bid might stand out as notably lower than others, it’s important to delve into the underlying factors behind the discrepancy. This may help minimize the risk of unforeseen costs and challenges that may surface later in the project lifecycle.
When creating the contract it is important for both GCs and subcontractors to establish clear contractual agreements and operational protocols. By addressing these aspects collaboratively, the likelihood of legal disputes, financial discrepancies and operational disruptions is minimized.
The clarity provided by well-defined contractual terms and site procedures fosters a shared understanding, promotes accountability and establishes a foundation for a cooperative working relationship. Developing contingency plans that outline alternative strategies and actions to be taken in the event of identified risks materializing is another crucial aspect of risk management.
This ensures that the project team can adapt to any unforeseen conditions that arise. GCs should also ensure contingency funds are allocated to further safeguard the project against unknown risks that could affect the budget or project timeline.
4. Anticipate schedule conflicts.
Effective scheduling involves aligning multiple contractors’ schedules within the project timeline, and being able to foresee and navigate potential scheduling conflicts.
Creating a comprehensive project timeline that delineates critical milestones and deadlines is important. GCs should work closely with each subcontractor to incorporate their schedules and scopes into the overarching project plan. Conducting routine reviews and communicating schedule updates to project stakeholders helps keep everyone on the same page.
When assessing the time required for each trade to execute their tasks, GCs frequently incorporate schedule float. Float represents the duration by which a task can be delayed without affecting the start of subsequent dependent tasks.
For example, a GC might inform a subcontractor that their scope of work must be completed within three days, but in the project schedule, they allocate a window of five days to allow for potential delays without impacting the overall project timeline. This ensures that the delay of one trade does not have cascading effects on the other trades. This also provides the GC with a window to ensure quality standards are met, and prescribe any corrective actions if they are substandard.
The general contractor can foster a collaborative environment by organizing regular meetings, or daily jobsite huddles, that bring together all relevant subcontractors. These sessions should provide a platform for discussing project progress and updates, addressing concerns and promoting collaboration.
5. Prioritize jobsite safety.
Safety is of utmost importance on a jobsite — and a safety culture is instilled by leadership. The site superintendent is typically responsible for making sure safety procedures are enforced. While every onsite employee is responsible for the safety of their team and the secure completion of their tasks, the superintendent drives overall site safety and coordination, as well as proper site ingress and egress.
GCs should also consider a subcontractor's safety track record when choosing trade partners. During the selection process, it’s good practice to check the subcontractor's insurance coverage, safety practices and procedures and commitment to compliance.
Subcontractors should be informed and involved in the project’s site-specific safety plan to ensure their scopes of work are incorporated.
Stay updated on what’s happening in construction.
Subscribe to Blueprint, Procore’s free construction newsletter, to get content from industry experts delivered straight to your inbox.
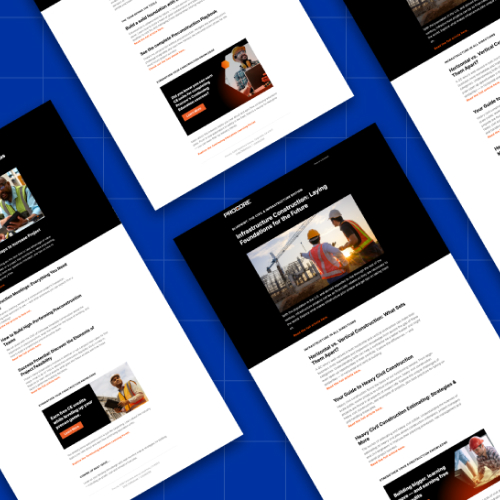
6. Proactively manage budgets.
To help avoid busting the budget, it’s important to examine subcontractor bids with an eagle eye. This ensures that every bid is not only competitively priced, but also aligns with project requirements.
Developing comprehensive contracts that explicitly delineate the project's scope, deliverables, timelines, payment terms and other pertinent details can help keep the budget on track. This minimizes the chances of scope gaps arising and mitigates the risk of increased costs to account for overlooked project aspects.
By continuously monitoring subcontractor costs and expenses throughout the project lifecycle, general contractors can regularly assess budgeted vs. actual costs, and promptly address any discrepancies or potential overruns. This safeguards against unwarranted financial surprises and prevents these problems from escalating later on in the project.
Fostering a collaborative environment with subcontractors to identify and implement cost-efficiency measures also helps with cost control. Subcontractors are often able to bring trade-specific creative solutions and potential value engineering options to deliver cost-effective outcomes without compromising quality.
Additionally, establishing a systematic approach for managing variations and change orders enables GCs to address modifications with subcontractors promptly, preventing potential disruptions to the overall project budget and timeline.
7. Maintain quality control standards.
For a general contractor, the pivotal factor in achieving an excellent final project lies in the high-quality work delivered by subcontractors. During the planning and contract negotiation phases, it’s important to set quality standards and benchmarks. This process ensures alignment with both the overarching project objectives and the client's vision. By establishing these clear benchmarks, GCs lay a solid foundation for systematically evaluating subcontractor performance throughout the course of the project.
Additionally, it’s important for GCs to implement a system that includes regular inspections and continuous monitoring of subcontractor performance throughout the project's lifecycle. This ongoing oversight serves as a proactive measure to guarantee the consistent delivery of high-quality work to the client.
By adopting the philosophy of trust but verify, the general contractor maintains a trusting relationship with their subcontractor partners while simultaneously confirming the quality of their work through inspections. This approach guarantees a quality product is delivered that aligns with and fulfills the client's expectations.
8. Leverage technology to improve communication.
Technological integration plays a significant role in streamlining subcontractor management for GCs as well as establishing efficient pathways and workflows that foster collaboration between various specialty contractors.
Project management software tools provide a unified source of accurate information for planning, executing and overseeing all facets of a construction project. Additionally, these platforms are accessible to every member of the project team, ensuring everyone stays informed about the latest project updates, changes, documentation and communication.
The seamless collaboration facilitated by these tools ensures that subcontractors are efficiently incorporated into the project workflow. Through digitized communication channels, project managers, superintendents and subcontractors alike can access real-time updates. This helps foster transparency and coherence throughout the project's lifecycle.
This streamlined communication not only expedites decision-making processes but also ensures that all stakeholders, including subcontractors, are synchronized with the project's evolving requirements. Moreover, the integration of these tools fosters an environment where information flows seamlessly, breaking down silos and creating a more interconnected and efficient construction delivery team.
9. Embrace collaboration with subcontractors.
The success of any construction project hinges largely on how effectively all project stakeholders work together. As each subcontractor specializes in a specific aspect of construction or scope, acknowledging their expertise sets a tone of mutual respect and enhances the overall quality of work.
On a construction site, specialty trade feedback can be the difference between a job done right the first time and costly rework. When managing subcontractors, it’s essential to remain open to their insights, which can offer invaluable onsite and trade-specific perspectives. If problems arise, the focus should be on collective problem-solving rather than finger-pointing.
GCs can incorporate pull planning into their project management approach to further develop this partnership. Pull planning, a collaborative scheduling technique, engages all stakeholders and trade partners in the planning process. By doing so, GCs are able to harness subcontractors’ expertise and insights, leading to a more comprehensive and realistic project plan and schedule.
Viewing subcontractors as partners creates a foundation for mutual respect and understanding. This not only facilitates a more seamless project execution but also ensures that project stakeholders are united towards achieving a common shared goal.
Effective subcontractor management is the linchpin of success on any construction project. As the project team navigates the intricate web of tasks and responsibilities, fostering collaboration, transparency and open communication should be top priority.
By embracing a one-team philosophy and implementing robust project management systems, GCs can streamline operations and cultivate an environment where each individual feels valued and accountable. In the realm of construction, success is truly a collective effort, and mastering subcontractor management ensures that each unique skillset converges seamlessly toward a shared vision of successful project delivery.
Was this article helpful?
Thank you for your submission.
92%
8%
You voted that this article was . Was this a mistake? If so, change your vote here.
Scroll less, learn more about construction.
Subscribe to The Blueprint, Procore’s construction newsletter, to get content from industry experts delivered straight to your inbox.
By clicking this button, you agree to our Privacy Notice and Terms of Service.
Categories:
Written by
Jacob Kunken
21 articles
Jake Kunken currently works as Solutions Engineer for Procore's Heavy Civil division. He brings 14 years of experience working in various construction roles in New York and Colorado, including laborer, assistant carpenter, carpenter, assistant superintendent, superintendent, construction manager, safety manager, and project manager. Jake also spent time in EHS as an environmental engineer for Skanska. He’s worked on more than 40 commercial projects from ground-up, to heavy civil, hospital work, and tenant improvement. Jake studied Ecological Technology Design at the University of Maryland.
View profileTaylor Riso
73 articles
Taylor Riso is a marketing professional with more than 10 years of experience in the construction industry. Skilled in content development and marketing strategies, she leverages her diverse experience to help professionals in the built environment. She currently resides in Portland, Oregon.
View profileExplore more helpful resources
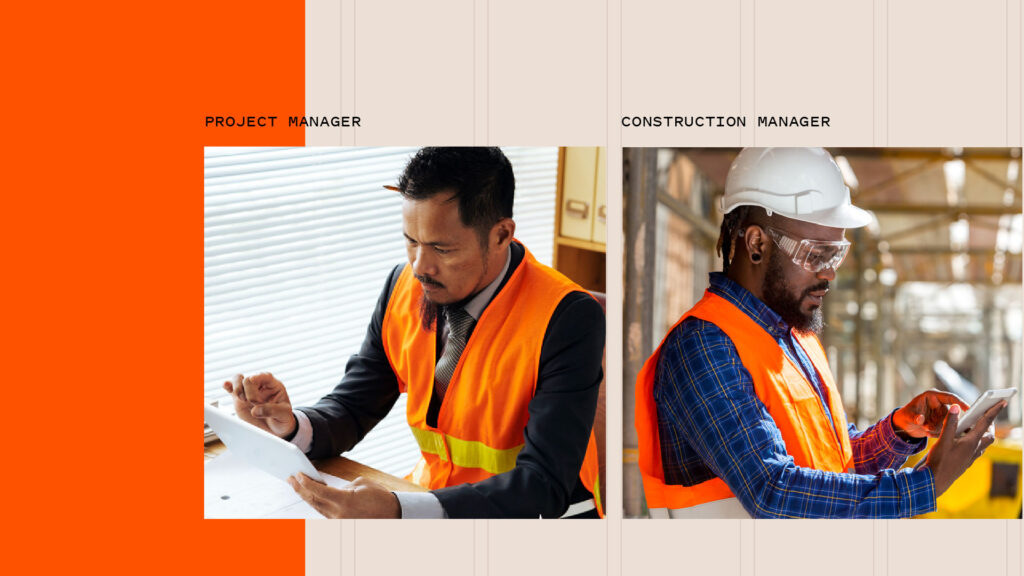
Construction Manager vs. Project Manager: Comparing Leadership Roles
Skillful oversight of construction projects allows companies to deliver to owners on time and within budget. Construction managers (CMs) and project managers (PMs) provide the necessary supervision to keep projects...
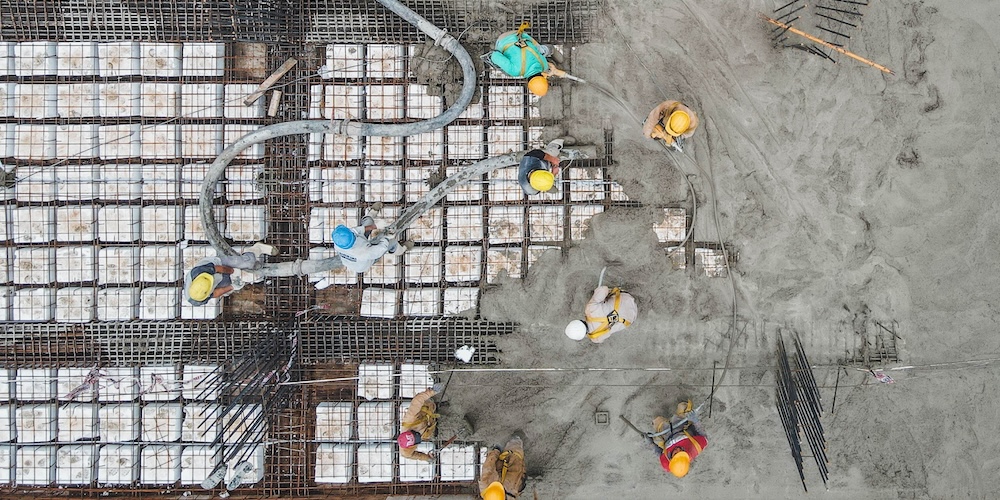
Mastering Construction Resource Management: Strategies for Success
Completing construction projects successfully requires the careful management of various resources: labor, materials, equipment, money, time and information. Since these resources are finite, allocating them wisely is crucial for minimizing...
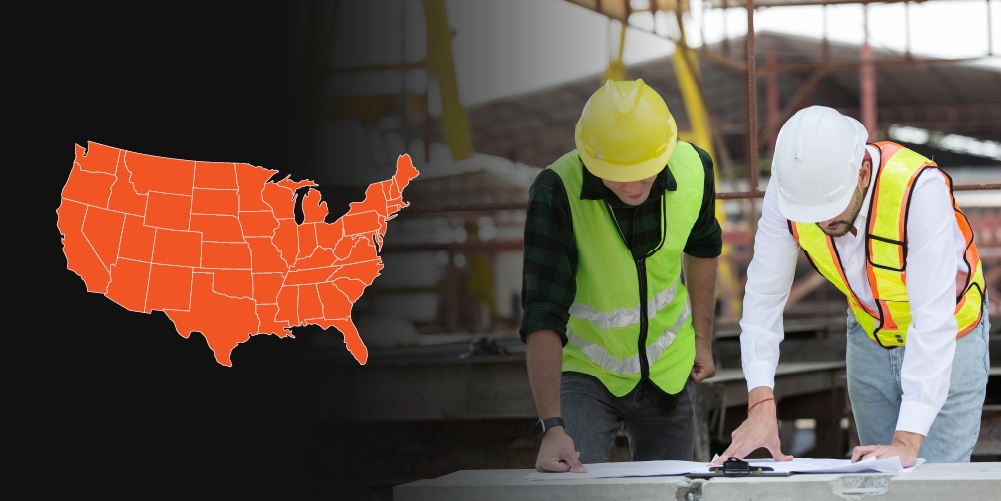
Managing Construction Projects in Different States: A Contractor’s Guide to Working Across State Lines
For many general contractors, taking on work in a new state or region can offer transformative opportunities for building a thriving business and a respected reputation. But managing projects is...
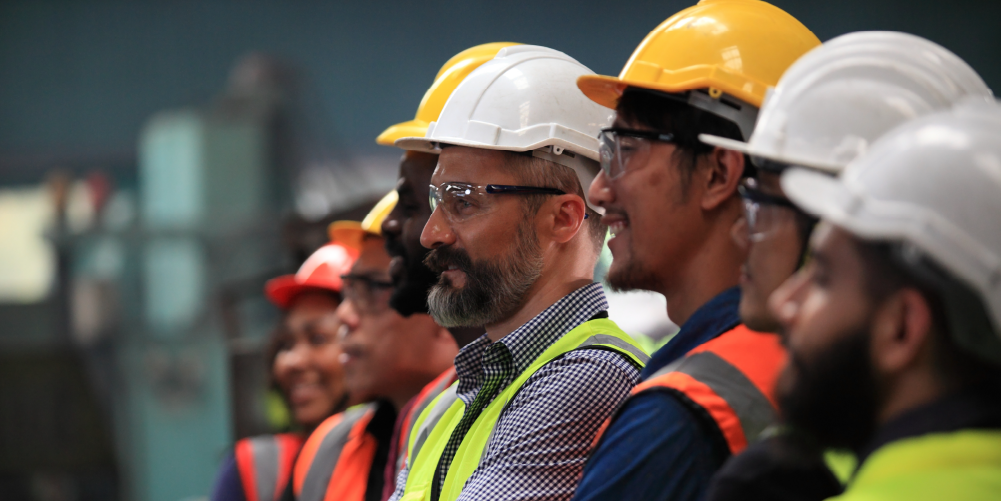
Construction Teamwork: Build a Solid Foundation With the Right Team
Construction is an industry of collaboration — no one person completes any job on their own. It could easily be argued that the most important skill for anyone in this...