— 8 min read
A Contractor’s Guide to Supply Chain Management
Last Updated Mar 13, 2025
Last Updated Mar 13, 2025
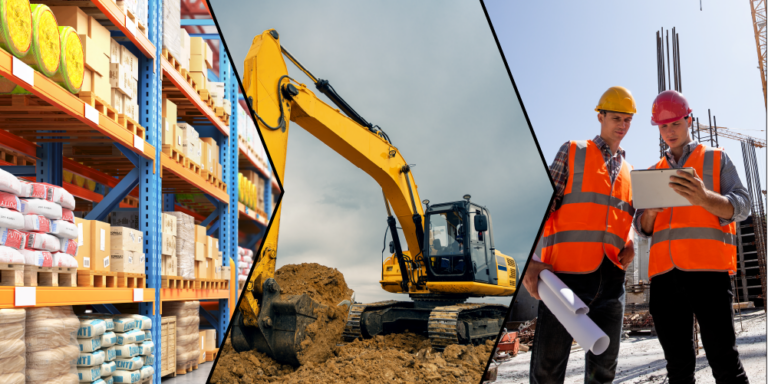
The construction supply chain refers to the steps involved in getting tools, building materials, and other necessities to the jobsite. Effective supply chain management is critical to the fluid momentum on any construction jobsite – employees can't build without the necessary tools and materials. However, long lead times, shortages, and regulations regarding materials procurement have made it difficult to smooth the flow of supplies to construction job sites.
This article will discuss the steps involved in a construction supply chain, challenges to supply chain management, and best practices for maintaining a consistent and cost-effective supply chain.
Table of contents
Links in the Construction Supply Chain
The construction supply chain starts with initial designs and ends with materials used at their destinations. Several links in the chain must be managed effectively to keep the project running smoothly. Below are the major components generally associated with supply chain management in construction.
Planning
When the design team, made up of the owner, architect, and engineer, draws up plans for a new build, they include the materials and the specifications they envision for the new project. Providing specific details — such as a particular brand or paint color for bathroom walls — is helpful for the general contractor when ordering materials.
Submittals
The GC that wins the bid for the project will refer to the materials and specifications the design team has created. The general contractor and subcontractors create submittal documents that detail the materials they intend to order for the project. The submittals may include product samples or data sheets passed to the owner and architect for approval before contractors order any materials. It’s essential for the design team and GC to iron out the details during this part of the process to prevent delays later if materials are incorrect.
Free Class: Basics of Submittals
Master the basics of submittals with industry expert Janine Trinidad, and earn continuing education credits from AIA.

Sourcing
Once approved, the contractor finds a place to procure the necessary materials. Some materials must be ordered from a fabricator or manufacturer, while others will come from a warehouse or third-party supplier. The contractor sources the materials and places the order.
When possible, ordering materials early on can help offset project hang-ups. Specialty materials — such as custom tiles that must be imported from a small designer in another country — may need to be ordered months in advance for a timely delivery.
Production
Materials produced to order may begin in a manufacturing facility and then move to a fabricator for completion before delivery to the job site. It’s important to keep lead times for these at top-of-mind to keep things moving onsite.
Delivery
Contractors and subcontractors need open communication about what materials are needed and when they're needed to ensure budget adherence and uninterrupted workflows.
Installation
Supply chain management reaches even as far as product installation. Materials must be on-site on time and located strategically to the installation area to avoid inefficiency onsite.
Challenges to the Construction Supply Chain
Fast and fluid supply chains are critical to construction timelines. Any delay in material delivery can disrupt the construction schedule, wasting time and money and chipping away at owner goodwill. Here are some of the challenges affecting efficient construction supply chain management.
Slow approval process
After the owner and design team have completed the design, it's up to the general contractor to build the project according to those specifications. The GC looks at the design and produces submittals to confirm the design team's choices before ordering any materials. Communication time for these approvals varies, so procurement might be on the back foot from the start.
Long lead times
Some construction materials take a long time from when a construction procurement professional orders them to when they arrive on the jobsite. Some long lead times are related to the distance materials have to travel. Other materials must be fabricated specifically for the building job at hand. Manufacturing disruptions, labor shortages, and delivery delays further lengthen lead times for some products.
Long lead times can disrupt construction schedules and create delays and lost labor time if not managed well. Further, products that are hard to get also often increase in price.
Price fluctuations
Price increases are always a concern for an industry that requires so many inputs and maintains slim profit margins. Over the past three years, severe and sometimes sudden price fluctuations have meant builders have had to be particularly strategic about purchasing construction materials.
According to Linesight’s Q2 2023 commodity report, the cost of bricks was 53% higher in Q2 2023 than in Q2 2021, but the cost of lumber dropped by 51%. This after a wild ride with lumber that peaked in May 2021, when the price per 1,000 board feet had increased 530%.
Changes in construction costs make it very difficult to bid accurately and stay competitive.
Ineffective communication and data management
Each link in the construction supply chain has its own systems in place. The challenge comes when the systems don't integrate or interact effectively, resulting in lost communications, confusion, and delays. Procurement professionals can get around these challenges by becoming familiar with supply chain partners, understanding their systems, and discussing solutions to ensure speedy materials ordering and delivery.
8 Tips for Streamlining the Supply Chain
While many of the challenges to a construction supply chain are out of builders' control, a few strategies and some forward thinking can help remove uncertainty and inefficiencies to smooth the materials procurement process. Below are eight ways management teams can tackle the challenges associated with supply chain management.
Manage inventory.
Precisely track and control materials and equipment already on hand. This helps prevent loss and misuse of commonly used materials, reduces the risk of wasted stock, and ensures nobody is sitting around waiting for supplies.
Track orders closely and communicate often.
Watch for a bill of materials or bill of lading paperwork and inspect it early for errors or omissions. Problems caught early on can travel back through the same stops as when they came and avoid further confusion.
Insist on a transparent supply chain.
To understand and mitigate risks in a supply chain, builders need to be familiar with each link. When sourcing materials, ensure supply partners are open about their products, delivery partners, and storage solutions.
Remove links in the chain.
Each step in the supply chain introduces new risks and lengthens the lead time to access materials. Removing unnecessary steps could save time and money. A builder could take delivery time and costs out of the equation by using a local manufacturer. Bigger companies may have the resources to purchase a manufacturing facility for some of their more critical materials to shorten the supply chain significantly.
Watch for trends
Watch forecasts to understand when demand might increase, prices may go up, delivery may be slow, or lead times may get out of hand for the materials needed for upcoming and current jobs. Do a cost analysis to determine if buying early and in bulk and then storing the surplus may help control costs. Alternatively, consider adding a price escalation clause into contracts that will allow additional costs to be shared between contractors and owners.
Implement Supply Chain Risk Management
Supply Chain Risk Management (SCRM) involves understanding the challenges impacting the supply chain and building protections for as many possibilities as possible. A comprehensive SCRM starts by monitoring events and markets in real-time. It then strategizes using if-then scenarios and creates backup plans, including secondary materials sources, acquiring some links in the supply chain, and partnering with suppliers with a robust SCRM.
Strategize for better on-site materials management.
Materials management doesn't end when inventory arrives on site. Store materials strategically so that they're easily accessible to installation crews or subcontractors. Laborers wandering around looking for materials, moving other items to find what they need, or traveling across the site with their materials create inefficiencies and possible safety hazards. Careful tracking prevents other teams from using materials that weren't intended for their jobs.
Get everybody on the same page.
As much as possible, get everyone on a single system or platform. Shared communications portals allow all communications to stay in one place and visible to each company in the chain. Along each step, everyone can see and track materials with ease, estimate arrival times, and make changes easily, streamlining the process for the shortest possible arrival times.
Shared technology enables better materials tracking, as collaborators can upload documents and receipts, make notes, and invoice all through a single platform. Architects and engineers can approve submittals through a single system to make the whole process faster. Contracts can be shared, altered, and eventually signed in a single place, where all stakeholders know they're viewing the most recent version.
Better supply chain management is about planning.
Construction supply chains are sometimes long and complex, making them seem impossible to manage. However, since supply chain interruptions can disrupt construction projects, it is critical to manage materials procurement closely to improve efficiency and avoid risks.
Maintaining transparent supply chains, understanding trends and forecasts for your most critical materials, and planning ahead can help dodge risks and keep projects running smoothly while controlling costs and maintaining some predictability for owners.
The best supply chain management plans involve shortening the chain wherever possible. By taking advantage of bulk buying or bulk pricing, tracking materials progress from order to delivery, and working together through robust common technology platforms to maintain peak communication and data sharing inventory management teams can help keep project delivery on schedule.
Was this article helpful?
Thank you for your submission.
100%
0%
You voted that this article was . Was this a mistake? If so, change your vote here.
Scroll less, learn more about construction.
Subscribe to The Blueprint, Procore’s construction newsletter, to get content from industry experts delivered straight to your inbox.
By clicking this button, you agree to our Privacy Notice and Terms of Service.
Categories:
Tags:
Written by
Kristen Frisa
67 articles
Kristen Frisa is a contributing writer for Procore. She also contributes to a variety of industry publications as a freelance writer focused on finance and construction technology. Kristen holds a Bachelor of Arts in Philosophy and History from Western University, with a post-graduate certificate in journalism from Sheridan College. She lives in Ontario, Canada.
View profileBen Ashburn
20 articles
Ben Ashburn is a Senior Construction Education Trainer at Procore. After a successful career as a construction estimator — working his way up from estimating manager to senior estimator — Ben has spent the most recent part of his career in construction sharing his skills with other as a construction educator. Ben has an extensive background in construction education: He has been an assistant professor in the Department of Construction Science at Texas A&M, and lectured about estimating, scheduling, management, and other related construction topics at Murray State University. He has been a construction training and learning development partner with Procore since 2019.
View profileExplore more helpful resources
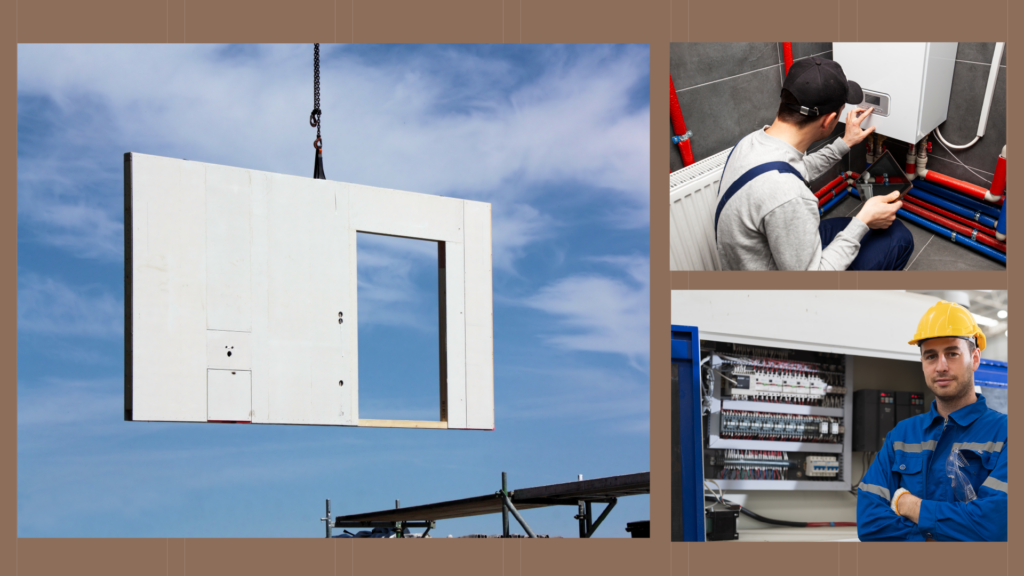
Modular Construction and MEP: A Collaborative Pairing
In an age of supply chain disruptions, workforce shortages, and rising material costs, off-site construction — including modular construction methods and prefabricated materials — is surfacing as a multipurpose solution....
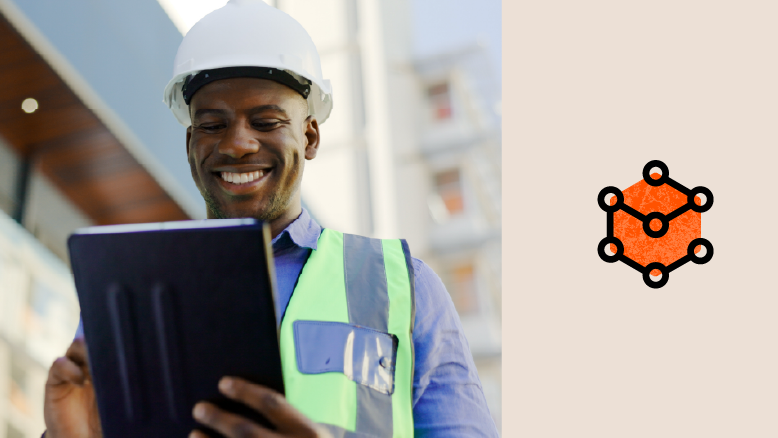
Connected Construction: Transforming the Industry Through Integration
Construction projects are becoming increasingly complex, so companies need to innovate to accurately and profitably complete these modern structures. Connected construction — using technology and data to improve communication, processes...
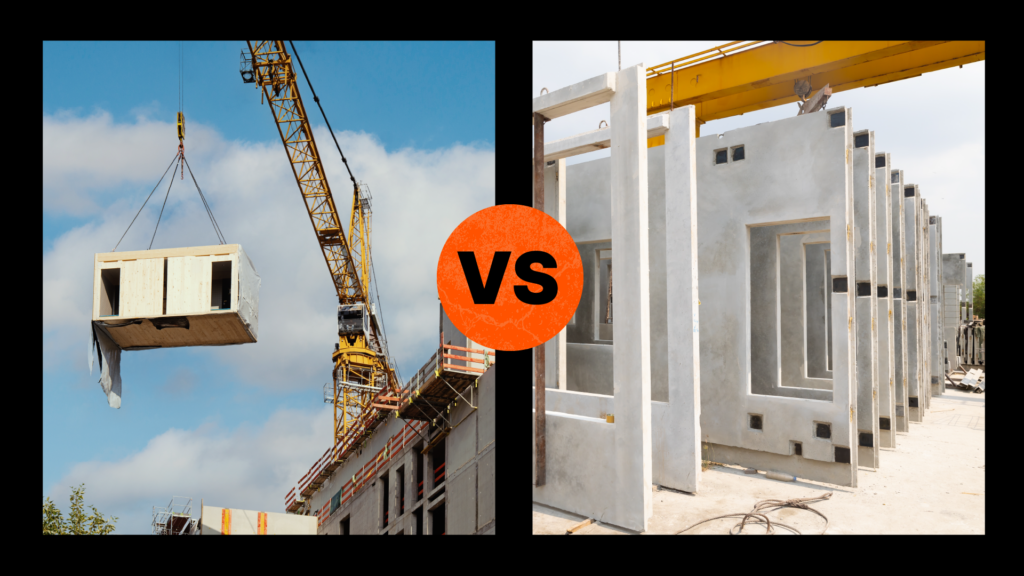
Off-Site Construction: Prefab vs. Modular
As the construction world becomes ever more competitive, deadlines get tighter and the margin for error gets slimmer, project owners around the world are always looking for an edge. Thanks...
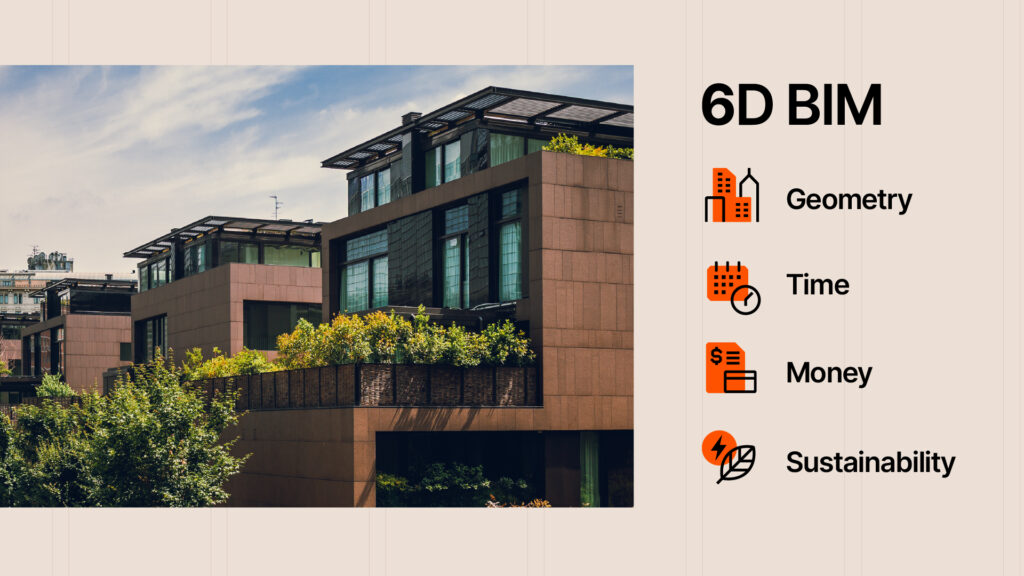
The Role of BIM in Sustainable Construction
Building information modeling (BIM) is transforming the architecture, engineering, and construction (AEC) industry. With this kind of sophisticated modeling, the industry has shifted from designing in 2D to 3D. This helps...