
Article
Managing Risk in Construction Materials Supply Chain
For head contractors in Australia and New Zealand, mastering supply chain management is pivotal to ensuring successful and profitable construction outcomes in an ever-evolving global landscape.
Want to learn more? We’re here to help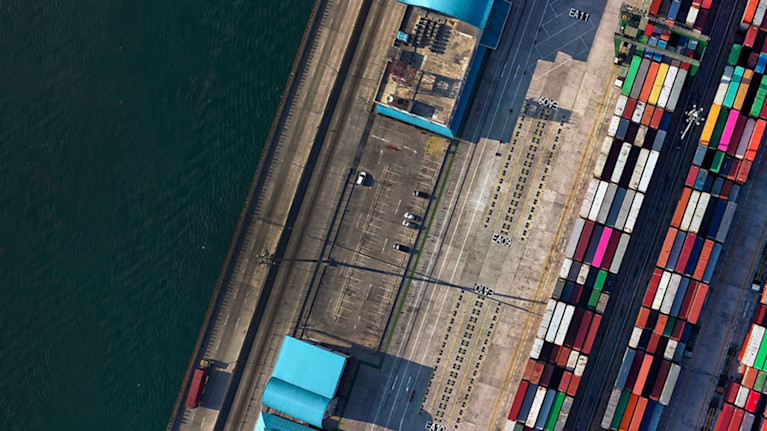
Every successful construction project hinges on effective supply chain management. It’s a balancing act—you need to source high-quality materials, find the right price, and partner with a reliable supplier. Doing it right increases the chance of finishing your project on time and budget.
Unfortunately, global events can throw even the most meticulous plans off schedule. In the last three years alone, we’ve seen global pandemics, international conflicts, labour shortages, and environmental changes impact the delivery and cost of critical building materials.
McKinsey expects costly supply chain disruptions from extreme weather, financial crises, pandemics, and other significant events to occur every three or four years. In light of this, head contractors handle long-term, capital-heavy construction projects and stay prepared for any supply chain disruption.
This piece will discuss major supply chain issues and the strategies they can implement to overcome them.
Chapter 1
Challenges in the Construction Materials Supply Chain
The construction industry is a vast and intricate web of processes and dependencies, with the supply chain being a pivotal component. Ensuring the smooth flow of materials from suppliers to sites is essential for timely project completion. Unfortunately, this is rarely the reality.
The flow of construction materials is impacted by global and regional events, from pandemics to labour shortages to war. For head contractors in Australia and New Zealand, here are the most pressing challenges to the supply chain:
Materials Sourcing and Procurement Issues
One of the primary challenges lies in the sourcing and procurement of materials. The global supply chain for construction materials is diverse, encompassing a range of categories. From foundational elements like aggregates and steel to intricate components like wiring, the availability and stability of these materials can vary significantly.
For instance, while aluminium, lumber, roofing materials, and semiconductors have a relatively stable supply chain, there are noticeable shortages in mechanical and electrical products, as well as copper. Such disparities can lead to project delays and increased costs, emphasising the need for meticulous planning and foresight.
Quality Control and Assurance
Quality is non-negotiable in construction. The materials used, whether steel, wiring, or aggregates, literally form the foundation of a project's success. It's not just about sourcing materials; head contractors authenticate that these materials meet the highest quality standards.
That means verifying their quality, assessing their cost-effectiveness, and determining their delivery speed.
Striking the right balance between these factors is a challenging feat. Real-time quality assurance becomes crucial here, allowing contractors to make informed decisions that ensure both the integrity of the project and its timely completion.
Navigating Complex Vendor Relationships
Beyond the tangible materials, the relationships that head contractors nurture play a significant role in the supply chain. Managing a construction project isn't just about bricks and mortar—it's about fostering strong ties with all stakeholders involved, including subcontractors, inspectors, funders, and, most importantly, vendors.
A robust vendor relationship can expedite material delivery and cost savings. However, the opposite is also true. A strained relationship caused by slow payment or poor supplier communication can lead to project stagnation. Head contractors must prioritise these relationships, ensuring clear communication, adherence to payment schedules, and a shared vision for project success.
Australia and New Zealand face regional and global challenges to the construction materials supply chain—materials sourcing, quality control, and vendor relationships—that threaten timelines, budgets, and even the strength of strategic partnerships.
Chapter 2
Head Contractors’ Approach to Supply Chain Management
The construction industry requires rigorous supply chain management with its complex processes and diverse stakeholders. Head contractors must ensure that materials move smoothly from vendors to construction sites.
Try this three-step proactive strategy:
Step 1) Identify and Assess Potential Risks
Identifying potential risks in the material supply chain is merely the tip of the iceberg. It sets the stage for a more comprehensive supply chain management process. Head contractors and project managers must investigate their current vendor network. This involves gauging the amount of risk they're willing to shoulder.
For instance, allocating additional time to evaluate the vendor network meticulously is prudent during the construction material takeoff phase. This can help spotlight potential problem areas, such as a lack of alternative suppliers or regional supply constraints.
Step 2) Implement Risk Mitigation Strategies
Given the inherent complexities and stringent timelines associated with construction projects, having robust risk mitigation strategies is non-negotiable. It's about ensuring the project remains on course, even when unforeseen challenges arise. This demands a business approach characterised by resilience, agility, and sustainability.
Practical strategies include opting for substitute materials when primary choices are unavailable, placing orders well in advance to circumvent potential delays, and optimising inventory management to ensure materials are available when needed.
Step 3) Consistent Risk Monitoring
Don't treat supply chain management as a one-and-done deal. Stay vigilant at every project stage, catching potential disruptions early to avoid those expensive hiccups.
Integrating advanced tools and procedures is a game-changer in today's digital age. By leveraging construction management systems, head contractors can harness the power of financial forecasting and analytics tools. This provides real-time insights into the state of the material supply chain and aids in proactive decision-making.
Chapter 3
Benefits of Effective Supply Chain Risk Management
In the intricate world of construction, the supply chain stands as a linchpin, determining the success or failure of projects. Effective risk management within this chain isn't just a precautionary measure; it's a strategic move with many benefits. Let's delve into the advantages that a well-managed supply chain brings to the table.
Improved Project Outcomes
A strong strategy for managing supply chain risks is essential for the success of construction projects. When carried out skillfully, it promotes stakeholder teamwork, prepares for unexpected challenges with backup plans, and sets up systems to monitor real-time progress. These components help builders tackle significant disruptions and ensure projects conclude successfully.
Cost Savings
Financial prudence is a cornerstone of any construction project. Delays and fluctuating material costs can wreak havoc on budgets, leading to financial strain and potential project stagnation. By integrating quality assurance and risk management processes into the supply chain, head contractors can significantly reduce the direct costs associated with procuring materials and the indirect costs stemming from unforeseen delays. It's about optimising every dollar spent, leading to overall cost efficiency.
Insider Tip for ANZ Contractors Want to secure your market edge and stakeholder trust in the ANZ region? Stay ahead of supply chain disruptions. It's not just about financial stability; it's about maintaining that invaluable reputation that opens doors to premier opportunities. Sidestep the financial pitfalls of disruptions and keep that competitive momentum rolling. Check out the Procore software solution for Project Financials |
Enhanced Reputation
A business's reputation is its most valuable asset in the construction industry. Past successes (or failures) are pivotal in shaping a company's image, influencing its ability to attract new projects. Word of mouth and referrals remain powerful tools, and a company's track record is often the deciding factor for potential clients.
By prioritising supply chain risk management, head contractors ensure that projects are completed on time and within budget and foster stronger, more collaborative relationships with suppliers. This dual benefit bolsters the project's success rate and enhances the business's standing in the industry.
Chapter 4
Best Practices for Supply Chain Risk Management
In the dynamic realm of construction, the supply chain is a critical pillar. This effective management system can differentiate between a project's success and failure. As the industry evolves, so do the challenges and risks associated with the supply chain. Here, we explore some best practices that can guide head contractors in navigating these complexities.
Diversify Across Materials and Suppliers
Putting all your eggs in one basket, especially in the construction industry, can be perilous. Sole reliance on a single supplier or material category can spell disaster when unforeseen disruptions strike, be it a global pandemic, geopolitical tensions, or blockages like the infamous Suez Canal incident. The solution? Diversification.
By establishing a comprehensive roster of potential vendors for crucial materials, contractors can bolster their supply chain's resilience. This acts as a buffer against disruptions and can lead to competitive pricing. To achieve this:
Determine your risk tolerance and threshold.
Pinpoint critical materials and partners.
Address vulnerabilities by expanding the vendor pool, especially in areas deemed high-risk.
Work Collaboratively with Suppliers
A shift in perspective can lead to transformative results. Instead of viewing suppliers merely as vendors, consider them strategic business partners. This approach fosters a more collaborative and cost-effective relationship. Head contractors can solidify trust by negotiating mutually beneficial agreements and setting sights on long-term partnerships, ensuring a smoother supply chain process.
Analyse Data to Improve Decision-Making
In today's data-driven age, construction management tools offer a goldmine of insights. With powerful analytics, these tools can process historical and current project data to forecast costs and potential challenges. For instance, predictive analytics in construction forecasting tools can spotlight impending supply chain issues, allowing contractors to make proactive decisions, such as early material ordering, to circumvent delays.
Leverage Emerging Technologies
The wave of technological disruption reshapes industries, and construction is no exception. Embracing this change can give contractors a competitive edge, especially concerning supply chain optimisation and risk mitigation. Innovations like construction analytics software, building information management, and AI are revolutionising the construction process with predictive capabilities and enhanced visibility and efficiency.
Construction Analytics Software
Construction analytics software is a digital solution that helps head contractors and stakeholders collect, analyse, and interpret project-related data. These tools offer insights into performance metrics, enabling managers to pinpoint inefficiencies and areas for improvement. Powered by artificial intelligence and machine learning, construction analytics provides a clear view of a project's financial health, tracks expenses, and forecasts future costs.
It’s easy to see how these features benefit head contractors who struggle with managing the construction materials supply chain. The software facilitates optimal resource allocation, ensuring efficient workforce, machinery, and material usage. Additionally, it plays a crucial role in risk management by identifying patterns, predicting potential risks, and suggesting mitigation strategies. Over time, it can even detect industry trends, helping businesses adapt to evolving market conditions.
Building Information Management (BIM)
Building Information Management (BIM) tools are advanced software solutions designed to help head contractors plan, design, construct, and manage buildings and infrastructure projects. Unlike traditional blueprints, BIM tools create a 3D digital representation of a structure, providing a complete view of its characteristics down to the materials. This dynamic model allows multiple stakeholders, from architects and engineers to contractors and facility managers, to collaborate in real-time, helping ensure accuracy and efficiency.
BIM goes beyond just geometry—it incorporates data about the different construction materials used, enabling lifecycle management from inception to demolition. This holistic approach aids in optimising designs, simulating performance, detecting clashes, and streamlining construction processes. Plus, BIM tools can integrate with other software, like construction analytics, providing comprehensive cost estimation, scheduling, and sustainability analysis solutions.
While the health of the construction materials supply chain in the ANZ region remains in flux, head contractors who take proactive measures to diversify vendors, invest in partnerships, and leverage new technology are in a great position to finish projects on time and within budget.
Chapter 5
How to Reduce Construction Material Supply Chain Disruption
Vulnerabilities of the global supply chain mean these products—aggregates, metals, and mechanical components—can be tough to get.
Procore, a leading construction management platform in ANZ, offers solutions customised to regional challenges, empowering contractors to strengthen their supply chain by:
Analysing previous project data to determine the efficacy of the current supply chain
Forecasting project financials to identify the best time to order materials
Communicating more efficiently with front-line contractors about stock
Searching the Procore Network to identify top vendors in a specific region
Leveraging BIM to reduce materials waste and increase savings
Despite the global economic uncertainties, there’s still demand for commercial and industrial construction across Australia and New Zealand. With governments pumping funds into the sector—it's the perfect moment for visionary construction firms to take the reins.
Try Procore’s construction management platform and see how a strengthened construction materials supply chain improves outcomes for all stakeholders.