Case Study
Enhancing quality and safety processes in the field
KAST transformed project management using Procore's Action Plans and Inspections to improve construction operations
The Challenge
KAST Construction, a Florida-based GC specializing in multifamily housing and condominiums, felt that their workers in the field could benefit from clearer, more streamlined processes. Particularly for tasks that involved a lot of back-and-forth or searching for information and materials, KAST believed that alignment could help eliminate confusion and cut down on wasted time. Rather than micromanage, the goal was to provide support in situations where it was truly needed.
The Solution
KAST has been a Procore user since 2016. When Action Plans was released in 2021, they saw it as a prime opportunity to break down tasks into simple steps, send alerts for timely actions and provide everything needed to complete tasks in a single location. They also leveraged Action Plans’ ability to connect to several Procore tools, including Inspections, to make the centralized digital playbook more versatile.
The Results
- With the technology of Procore, team members have gone from feeling overwhelmed to empowered, significantly improving efficiency and clarity on every project
- Streamlined Action Plans saves valuable time and allows teams to efficiently close out projects
- With new processes in place, the pressure on team members is eased, creating a safer work environment
“Action Plans lays out the process and puts everything you need in one place. It reduces confusion, streamlines progress and leaves less room for error.”
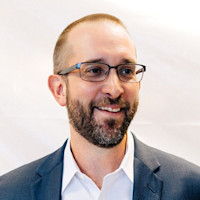
Rob Sloyer
Vice President, Innovation & Strategic Services
KAST Construction
Unclear expectations were a risk to quality and safety
With over 200 employees working on multifamily and hospitality projects in South Florida, KAST Construction doesn’t take chances when it comes to quality and safety. But like a lot of general contractors, KAST felt that its workers could benefit from clearer instructions for specific processes. Not knowing where to start, which steps to take next or frequently having to learn on the job was creating unnecessary risk and potential project slowdowns.
“Oftentimes there were a lot of unclear expectations, both in terms of what was required and the sequence in which tasks should be completed,” says Rob Sloyer, KAST’s VP of Innovation and Strategic Services. The same was true of finding the materials or supporting data to complete a specific assignment. “You might be given a task to get the job site safety signage, but then you have to go find those templates, or figure out where we provided a link to them.”
“A lot of the feedback from our project teams was that there was too much coming at them from too many sources.’” Sloyer says.
Luckily, as a longtime Procore customer, KAST already had the solution at their fingertips. By using a combination of Action Plans and Inspections, KAST has taken the guesswork out of their field work, putting clear instructions and expectations in the hands of their people and significantly improving efficiency and clarity on every project.
Bringing quality and safety to the field, one step at a time
Today, KAST team members have Action Plans to guide them through several critical processes, including safety project startup, VDC/MEP coordination project startup and pre-drywall inspection. They have even created an Action Plan for the overall quality control plan for every project, from meetings to mock ups to required inspections.
Particularly transformative is KAST’s use of Action Plans in combination with Inspections in the field. As a company that builds a lot of condominiums, KAST has a detailed and time-consuming pre-drywall inspection process that requires signing off on every single unit, floor by floor. Before the company created an Action Plan for the process, workers would often take notes in the field, then enter the data on their desktop computer in the office, leaving room for errors and oversights. By using the Action Plan, which links directly to the Inspection checklist, superintendents can now conduct the entire inspection on their mobile device, speeding up the process and minimizing the risk of missed steps.
And not only does Action Plans allow KAST to attach relevant documents and other materials to every task, it lets workers in the field upload evidence of their work. “In the job site safety signage example I used earlier, we can attach the template for the sign, but the user can also upload a picture of the sign once it’s up,” says Sloyer. “They’re not just telling you the sign is up, you can actually see it for yourself.“
With Inspections Scheduler, which allows users to schedule recurring or standalone inspections at a future date, KAST can avoid overwhelming its managers — who are typically working on three or four projects at a time — with inspections that don’t need to be performed for weeks or months to come. “The nice thing with the Scheduler is it doesn't actually create the inspection until it's time for the person to fill it out,” says Sloyer. “We have a scheduled inspection that goes out to each VDC manager for each of their projects, at which point they can go through and fill them out.”
Accelerating progress in surprising ways
Relying on Action Plans has come with some unexpected benefits. Previously, getting people to sign off on BIM plans was a struggle. “We've printed out full-size sheets and had people wet sign them in the trailer,” Sloyer says. “We've even tried sending them through DocuSign.” But with Action Plans, those struggles are practically eliminated. “We can put all of our documentation in there, including links to the final models, and the program keeps harassing you if you don't sign it. As a result, we've had a lot more completed sign offs than we have in the past.”
As a project moves along, the completed plans can be used as de facto progress reports. “You can filter through all the Action Plans for a job and see a little summary bar of the steps themselves,” says Sloyer. “For things like MEP coordination, the people who aren’t involved in the day-to-day can use that to see where we stand.”
With just a few new processes in place, KAST has eased the pressure on its team members and made everybody safer. “Action Plans lays out the process and puts everything you need in one place,” says Sloyer. “It reduces confusion, streamlines progress and leaves less room for error.”